Fabbricazione additiva accessibile per componenti in ABS
La diffusione dei materiali ingegneristici ha rappresentato un fattore chiave per la crescita della fabbricazione additiva e questo è particolarmente vero per l’ABS, il materiale più comunemente usato oggi nella produzione manifatturiera. Purtroppo, questa capacità è stata limitata dalla necessità di ricorrere a stampanti industriali tradizionali dai prezzi e dalle dimensioni non accessibili a molti. Dave Veisz, Vicepresidente del reparto di ingegneria di MakerBot, esamina la questione e parla dei recenti sviluppi di una fabbricazione additiva a prezzi accessibili che consente di superare questi limiti, contribuendo a colmare il divario tra la fabbricazione additiva di tipo industriale di alta qualità e la stampa 3D desktop.
di Giovanni Sensini
Se per caso avete avuto la sfortuna di calpestare un Lego, saprete quanto possano essere incredibilmente dolorosi – per non dire indistruttibili – quei piccoli mattoncini. Questa sorprendente combinazione di durata e di impressionante resistenza alla trazione, insieme alla finitura lucida, è dovuta alla loro realizzazione in ABS, un polimero termoplastico molto apprezzato per i beni di consumo stampati ad iniezione.
Oltre alla resistenza alla trazione, la straordinaria quantità di proprietà dei materiali ABS comprende la resistenza alle alte temperature, la riciclabilità, l’elevata resistenza chimica e la bassa conduttività elettrica. È per questo motivo che l’ABS viene utilizzato per produrre molti degli oggetti di uso quotidiano che ci circondano, dai cruscotti delle auto e dagli alloggiamenti elettrici alle tastiere dei computer e, naturalmente, ai giocattoli per bambini.
“Sebbene una gran parte dei componenti in ABS venga ancora fabbricata con metodi di produzione tradizionali come lo stampaggio ad iniezione, si sta diffondendo sempre di più l’uso della fabbricazione additiva di livello industriale in quanto opzione economicamente vantaggiosa per la produzione rapida di prototipi in ABS e di parti finali in serie limitate”, spiega Dave Veisz, Vicepresidente del reparto di ingegneria di MakerBot. “Mentre la capacità di produrre parti in autentico ABS di livello ingegneristico è diventata comune per le stampanti 3D di fascia alta, la fabbricazione additiva desktop per molto tempo ha avuto difficoltà a produrre queste parti con un livello di affidabilità e ripetibilità capace di soddisfare le aspettative di ingegneri e designer industriali”.
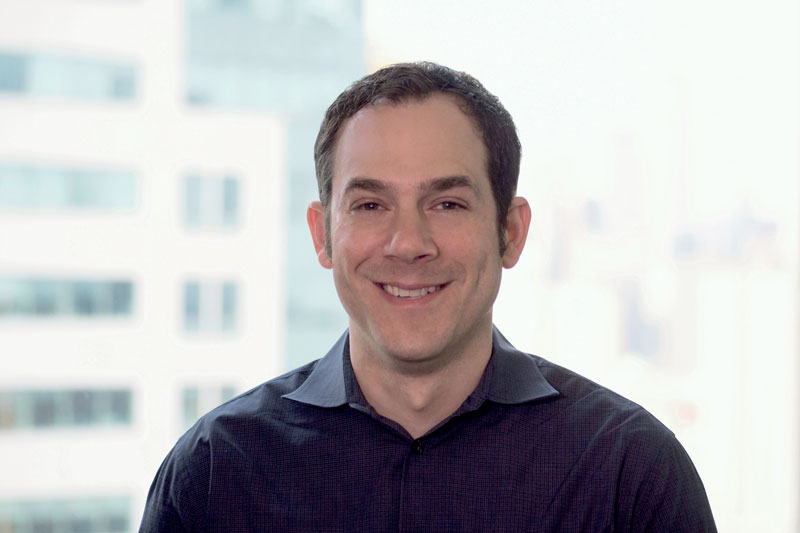
La sfida
Il problema risiede nella resistenza alle alte temperature e nel punto di fusione dell’ABS. “Il raffreddamento provoca una delaminazione che porta a un grave indebolimento della struttura del pezzo e alla fine crea deformazioni e crepe, vanificando in sostanza la ragione della scelta dell’ABS”, sostiene Veisz. “Se un pezzo viene raffreddato rapidamente mediante tempra, può anche essere soggetto a fenomeni di contrazione dovuti all’esposizione all’aria. Pertanto, quando si producono pezzi in ABS utilizzando una stampante 3D desktop, sono fortemente indicati un processo di raffreddamento controllato e una camera chiusa. Quanto più grande è il pezzo, tanto più è probabile che le forze di contrazione entrino in gioco, provocando deformazioni o sollevamento dei bordi.
Alcuni ingegneri possono abbandonare del tutto l’ABS e rivolgersi a materiali alternativi come il PLA, che in genere richiede una temperatura di stampa inferiore (190-230 °C a fronte dei 210-250 °C raccomandati per l’ABS), oltre a comportare un rischio di deformazione ridotto. Tuttavia, il basso punto di fusione del PLA ha lo svantaggio di un’importante perdita di resistenza alla trazione se riscaldato a più di 50 °C, rendendo fragile il pezzo prodotto. Da buoni ingegneri, non ci sottraiamo mai a un problema di natura chimica e a quanti sono determinati a perseverare con l’ABS si possono suggerire diversi “trucchi” o approcci alternativi per migliorare la qualità del pezzo. La maggior parte delle soluzioni si riduce a due tattiche fondamentali: modificare il materiale o modificare la stampante 3D”.
Cercando su Internet è possibile trovare una serie di materiali ABS modificati, da quelli termocromatici e traslucidi a quelli ritardanti di fiamma e persino luminosi (fosforescenti). “Questi adattamenti chimici – afferma Veisz – offrono agli ingegneri la libertà di scegliere la formula ideale specifica per l’applicazione richiesta.
Tuttavia, queste formule modificate tendono ad avere un costo e l’ABS etichettato come “ottimizzato per la stampa 3D” non fa eccezione. Se per un verso l’ABS può essere modificato chimicamente attraverso l’integrazione di un additivo o aumentando il rapporto di polibutadiene (la B dell’ABS), per potenziarne la resistenza al calore tale vantaggio è controbilanciato da una serie di effetti negativi: temperature di deformazione termica più basse, modulo di tensione ridotto e minore resistenza alla trazione. Questo può tradursi in un prodotto di qualità inferiore, totalmente inadatto a molte delle applicazioni ad alte prestazioni per le quali viene utilizzato l’ABS, come la fabbricazione di componenti per l’industria automobilistica e aerospaziale.
L’evoluzione di una fabbricazione AM per l’impiego di ABS non modificato
Se la modifica del materiale non sortisce l’effetto desiderato, allora la naturale conseguenza è il tentativo di modificare la stampante 3D stessa. Molte stampanti 3D desktop presenti oggi sul mercato permettono all’utente di controllare la temperatura della piastra di costruzione. “La presenza di una base riscaldata a temperatura controllata permette di trasferire una certa quantità di calore sul fondo della parte stampata in 3D, riducendo il rischio di separazione degli strati”, sottolinea Veisz. “MakerBot ha adottato questo approccio con le sue prime stampanti 3D, tuttavia si è visto che l’effetto era limitato. Con questa tecnica non è possibile controllare in modo uniforme la temperatura di tutti gli strati di un pezzo contemporaneamente, esponendolo così al rischio di deformazioni e crepe.
Quando abbiamo progettato la recente piattaforma METHOD, abbiamo deciso di controllare la temperatura di tutto il piano di costruzione e non solo della piastra. Invece di riscaldare semplicemente dal basso, la camera chiusa permette di far circolare il calore al suo interno spingendo l’aria su entrambi i lati. Questo assicura un controllo migliore in quanto ogni strato viene stampato nello stesso ambiente termico senza dover “armeggiare” con le impostazioni della stampante. Questa tecnologia è stata progettata per aiutare gli ingegneri a ottenere parti in ABS dimensionalmente accurate e di qualità industriale a un costo significativamente inferiore rispetto ai processi di fabbricazione tradizionali”.
Ma anche con un nuovo approccio al controllo della temperatura del piano di costruzione, le difficoltà non sono finite. “Poiché l’estrusore si trova in un ambiente più caldo, c’è il rischio di espansione”, continua Veisz. “Sorge allora spontanea una domanda: se esiste un problema termico fondamentale nell’utilizzo dell’ABS su una stampante 3D desktop, perché ci ostiniamo a combattere contro queste proprietà del materiale?
La risposta sta nella nostra visione di futuro dell’industria manifatturiera, che corrisponde a un modello di produzione decentralizzato e on-demand basato sulla fabbricazione additiva. L’ABS stampato ad iniezione resterà la scelta migliore per la produzione in serie per molti anni a venire per via della sua velocità e del suo basso costo, ma quando sono richiesti volumi dell’ordine di decine, centinaia o addirittura migliaia di unità o è indispensabile una produzione personalizzata, la fabbricazione additiva prende davvero il sopravvento. La tradizionale analisi costi-benefici a corredo della creazione di uno strumento, di un prototipo o di un pezzo di uso finale viene stravolta. I progetti possono essere testati e iterati più velocemente, accelerando l’innovazione e i tempi di commercializzazione, il tutto a un costo molto più basso rispetto ai metodi convenzionali”.
La possibilità di utilizzare un ABS di livello ingegneristico non modificato su macchine che sono poco di più delle tradizionali stampanti 3D mette i vantaggi propri della fabbricazione additiva a disposizione di un’utenza molto più ampia di ingegneri, fino ad ora costretti a utilizzare costose stampanti industriali 3D per produzioni su larga scala per soddisfare i requisiti di impiego dell’ABS. “Ecco perché la stampante 3D METHOD X lanciata recentemente rappresenta un cambio di passo per la fabbricazione additiva di tipo industriale. Offrendo per la prima volta la possibilità di utilizzare l’autentico ABS su una stampante 3D più accessibile, consente al designer o ingegnere di avere accesso tutti i giorni a un ABS di livello ingegneristico per prototipi più accurati e funzionali, nonché per parti di produzione più robuste e affidabili”, spiega Veisz.
All Axis Robotics è un interessante esempio di quello che METHOD X permette di ottenere. “Per adattare i suoi progetti di dispositivi di estremità per bracci robotici (EOAT) al reparto, l’azienda aveva bisogno di produrre una levigatrice in ABS personalizzata”, afferma Veisz. “Utilizzando METHOD X, nel giro di poche ore il team è stato in grado di produrre la levigatrice utilizzando materiali ABS altamente resistenti e durevoli, evitando i costi elevati e i lunghi tempi di consegna generalmente connessi con una fornitura esterna.
Considerato che l’ABS non è mai stato così rilevante nell’ambito della produzione, è importante che gli sviluppi della fabbricazione additiva possano estendere questa capacità all’industria in generale come alternativa ai metodi tradizionali. Mentre le più costose stampanti 3D per produzioni in serie rimangono ancora uno strumento importante per soddisfare determinati requisiti industriali per l’ABS, non c’è dubbio che le versioni meno costose che consentono l’utilizzo dell’autentico ABS di tipo ingegneristico possano aprire infinite opportunità a un’utenza tecnica molto più ampia.