Nuove frontiere per il Laser Metal Deposition
Al Politecnico di Milano si è consolidato un forte know-how sul design e sulla produzione di componenti ad alta complessità per la tecnologia Laser Metal Deposition. In questo articolo parliamo dei due casi LMD più emblematici del progetto che sono stati prodotti al Dipartimento di Meccanica del Politecnico in cui è installata la cella di deposizione BLM Additube.
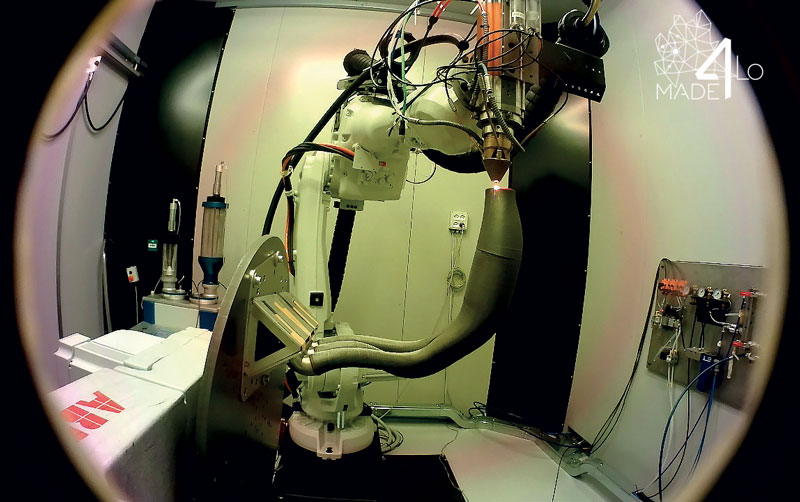
Nel 2017 nasce il progetto Made4Lo, acronimo di Metal Additive for Lombardy, con l’intento di creare una fabbrica diffusa per lo sviluppo delle tecnologie di produzione additiva per metalli all’interno del territorio lombardo, costituendo una rete di aziende e centri di ricerca che condividono le loro competenze. Nell’evoluzione del progetto ampio spazio è stato lasciato alla ricerca sul processo LMD-Laser Metal Deposition dove i partner BLM Group, Politecnico di Milano, Lafranconi silenziatori e Tenova hanno portato la tecnologia a un livello più maturo, tramite la produzione di prototipi funzionali altamente innovativi. I due casi LMD più emblematici del progetto sono stati prodotti al Dipartimento di Meccanica del Politecnico di Milano, in cui è installata la cella di deposizione BLM Additube. Il setup, costituito da un’unità robotizzata a 8 assi, permette di avere piena liberà nella costruzione additiva delle forme più complesse e di grandi dimensioni, risultando efficace nella produzione sia di componenti massivi sia a parete sottile. La testa di deposizione è integrata con un sistema di monitoraggio coassiale a tre segnali: controllo della temperatura mediante pirometro a due colori, misura della pozza fusa tramite camera NIR e rilevamento dell’altezza con triangolatore laser. Grazie alla collaborazione con Team3D e CNR Stiima, la movimentazione della cella è gestita tramite l’interfaccia CAM di Siemens NX, che non solo permette di automatizzare il processo ma anche di creare percorsi macchina di elevata complessità grazie al modulo additive integrato.
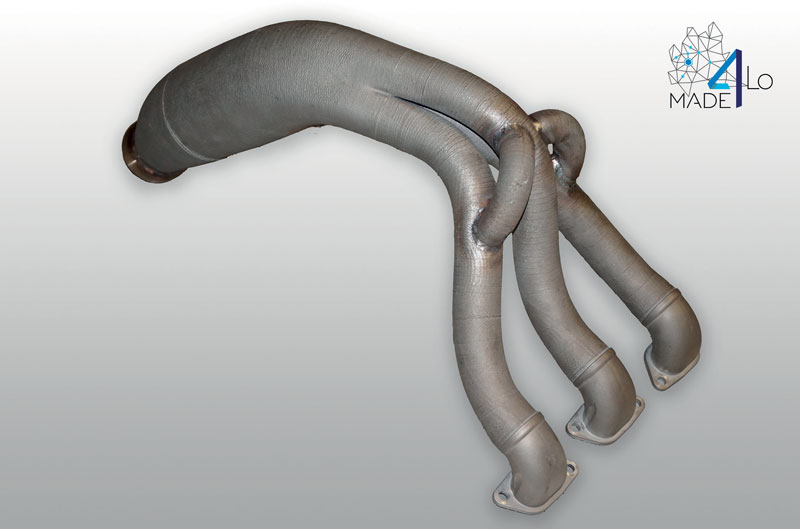
Scarico per motocicletta
Il primo caso riguarda la creazione di uno scarico di motocicletta a tre cilindri, ridisegnato e stampato LMD presso il Sitec. Basandosi su un modello di serie è stato ridisegnato e prodotto un prototipo monolitico con lo scopo di andare a ridurre notevolmente la fase di assemblaggio dei numerosi pezzi che compongono il modello originale. La fase di prototipazione tradizionale di questi componenti richiede la produzione di stampi, matrici di piegatura e un’incisiva presenza di manodopera, aumentando costi e tempi per la produzione. Il processo LMD è in grado di produrre un modello in poche ore, eliminando i costi delle attrezzature e riducendo quindi il time to market dei prodotti. Partendo dalle flange di accoppiamento del modello di serie, è stato creato un percorso macchina in grado di costruire i tre tubi in contemporanea ottimizzando i tempi ed evitando collisioni fino al loro punto di giunzione. Grazie al redesign, al corretto uso dei parametri di processo e alle strategie di deposizione è stato possibile sigillare in automatico la connessione senza l’intervento degli operatori. In seguito allo studio di strategie CAM innovative si è passati ad affrontare la costruzione del collettore, con cambi di sezione e curvature particolarmente marcate e critiche per il processo. Sfruttando la flessibilità della cella BLM Additube è stato inserito all’interno del collettore il filtro catalizzatore, saldato e utilizzato come substrato per la successiva parte di stampa, portando a completamento il processo durato in tutto 14 ore. Sono poi stati assemblati gli elementi di connessione e i tubi secondari, stampati separatamente dallo scarico. Grazie allo sforzo congiunto di Lafranconi e Politecnico di Milano il prototipo è stato testato su banco prova e i risultati confrontati con quelli del modello di serie, ottenendo performance equivalenti in potenza e coppia.
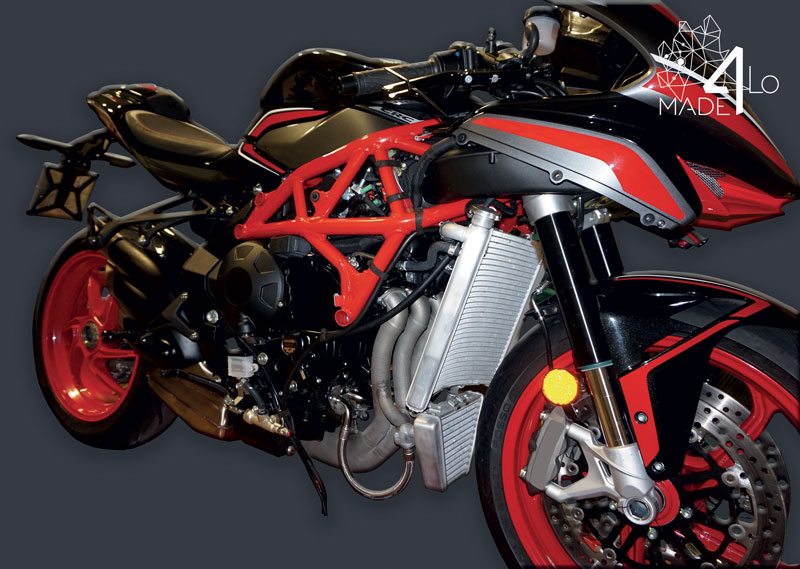
Recuperatore Multimateriale
Il secondo caso, anch’esso stampato LMD presso il Sitec, riguarda la produzione di un recuperatore per bruciatori recuperativi utilizzati nei forni da trattamento termico. I modelli tradizionali, prodotti tramite l’assemblaggio di molteplici sezioni, per massimizzare lo scambio termico fra i flussi di aria fredda e gas bollenti hanno superfici alettate con spessore elevato dato il processo di colata con cui sono prodotte. Su brevetto di Tenova e redesign del Politecnico di Milano è stato costruito un diverso concept di recuperatore che, sfruttando le potenzialità della tecnologia LMD, porta a un’ottimizzazione dei materiali e delle fasi di assemblaggio a fronte di prestazioni elevate. Considerando la lunghezza di 500 mm la temperatura di lavoro decresce dalla testa verso la base. Si è quindi deciso di utilizzare due materiali per la stampa: Inconel 625 per la prima metà che incontra i gas più caldi, AISI 316L per la seconda metà che opera a temperature più basse. Così facendo è stato possibile dimezzare l’utilizzo di costose leghe a base Nichel dedicandole alla zona strettamente necessaria. Dal punto di vista del design, la superficie alettata è stata sostituita con una ondulata. L’avanzato modulo additive di Siemens NX ha permesso di costruire il corpo centrale con una deposizione a passata singola dello spessore di 1 mm. Alle estremità, dedicate alla successiva saldatura col sistema, lo spessore è stato gradualmente aumentato a 3 mm sfruttando una strategia di scansione multi-passata. Così facendo è stato quindi prodotto un componente monolitico multimateriale con spessore di parete variabile, che ha permesso di semplificare le fasi di assemblaggio e ridurre il consumo di materiale del 75%.
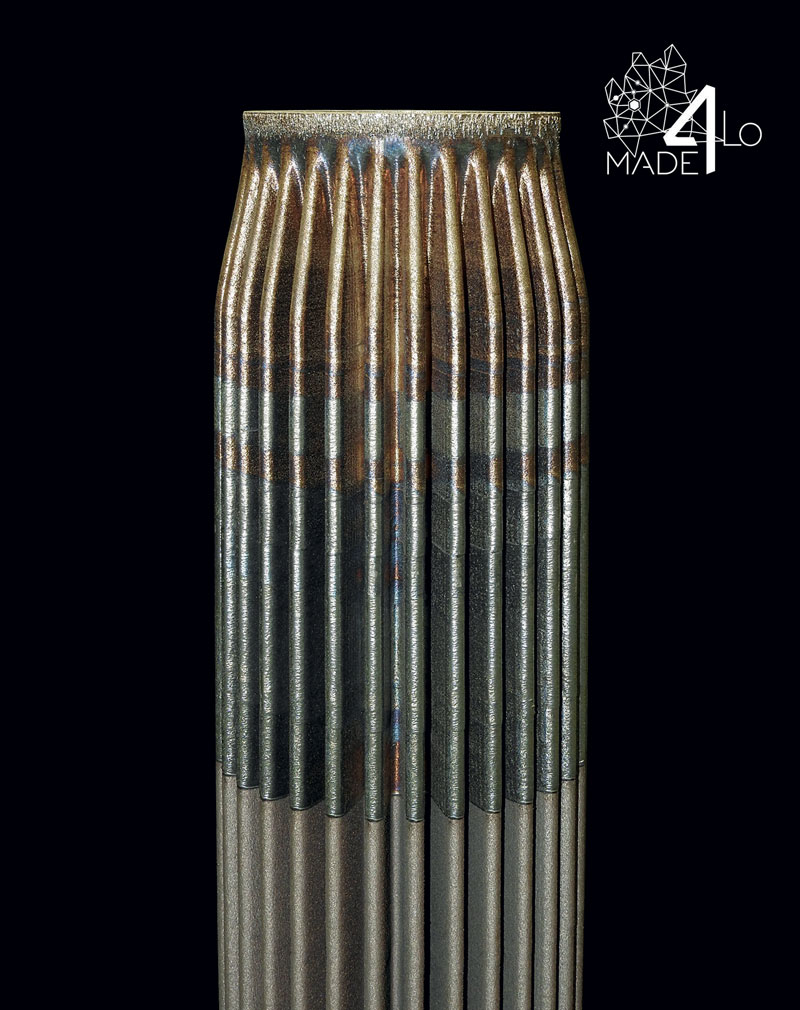
Considerazioni finali
La sperimentazione affrontata nel progetto Made4Lo in ambito di processo, movimentazione CAM e Design for Additive Manufacturing ha portato alla produzione di componenti unici nel loro genere, le cui geometrie e caratteristiche tecniche sarebbero impossibili da riprodurre con altri processi manufatturieri. Il lavoro svolto ha inoltre permesso ai processi additivi di introdursi in ambiti tecnologici ancora inesplorati, portando già nelle prime applicazioni innovazioni di importante rilevanza.