Micron and Durox, Electroless Nickel and Hard Anodizing for Hi-Tech Mechanics
Micron Coatings Group has chosen the most complex sector of metal surface finishes, that of high-precision mechanics, focusing on an extreme customisation of its service
The range of companies operating in the aluminium sector is truly incredible. In spite of years of experience, knowledge and meetings, we are always impressed by the industriousness and ability of our entrepreneurs. Micron Coatings Group, with its two production units Micron and Durox, is a further example of managerial intelligence. In a very competitive sector, the choice of this industrial concern, which has focused entirely on customising its service to meet the needs of its customers, is striking: from the initial design, carried out on each product, to the creation of the customised “recipe”, through to the finishing of the materials by thick anodising or nickel plating. There are in fact several possible combinations of finishes which vary according to the performance expected from the finished component. From low roughness and low friction coefficient finishes, to coatings that greatly improve wear or corrosion resistance, through heat dispersing and dielectric coatings. Not only aluminium, which is still the main metal treated, but also copper, steel, titanium and magnesium. We spoke today with the Bordiga family, who have been managing this excellent business, Micron Durox, from the very beginning.

Let’s start with the current situation: how did your company react to the Covid-19 crisis?
Fortunately, we managed to end 2020 with a result which exceeded expectations, even though it was slightly lower than the previous year in terms of turnover. The great diversification of products and market niches certainly helped us, we suffered like everyone else from the crisis in the automotive sector in the first few months of last year, but we were able to compensate easily with other sectors. This year has started in a very encouraging way and we hope that the trend will continue.
Could you briefly outline the history and current situation of your company?
Micron was founded by the Bordiga family (the three siblings Aldo, Carla and Sergio Bordiga, who are now present in the company even with the second generations) in 1985 and specialized in chemical nickel-plating treatments, with the construction in 1992 of a new plant in Soncino (Cremona). The acquisition of Durox, a historic company based in Remanzacco (Udine) and specialised in aluminium and titanium anodising, took place in 2000 and has certainly given a boost to the group’s growth. Today, the two companies have a combined turnover of over 12 million euros and employ 110 people. Micron, which as mentioned covers the chemical nickel-plating segment of both aluminium alloys and other metals, accounts for about 70% of the total turnover, while the rest is represented by the hard aluminium anodizing activities carried out by Durox.

What are the main sectors in which you operate today?
Precision mechanics in general, producing components for various sectors, from automotive to pneumatics, hydraulics and sports equipment, is our main specialisation. Of course, depending on the alloys to be treated and the properties required, we propose anodic oxidation or nickel plating for materials that are difficult to anodise. Unlike many of our competitors, we start with the co-design of the component, working alongside our customers to define the most suitable treatment, with a technology partner approach.
Are you therefore completely out of the definitely more crowded sector of extrusions for the building industry?
Certainly, and this was a precise strategic choice. We realised some time ago that in order to differentiate ourselves, to compete internationally and to become acknowledged and appreciated players, we absolutely had to offer a very specific and qualitatively superior service and product.

Up to what size or weight can you oxidise components?
Normally the items to be treated are small or medium-sized, especially for precision mechanics. However, we are able to carry out hard anodising on components up to 7.5 metres long and two metres high. This is the case, for example, with cylinders, linear guides or rails which need to offer certain wear characteristics. However, our core business is represented by smaller components, especially for the automotive sector, such as brake and engine components, which are all small in size.
How does hard anodising differ from ‘normal’ anodising and what are your strengths?
In hard anodising, lower operating temperatures, higher voltage and longer average times are required. This mix makes it possible to obtain anodic thicknesses which are more compact and more suitable for protecting components from wear, while at the same time increasing resistance to corrosion. As far as our strengths are concerned, we certainly intend to differentiate ourselves in terms of the technological content of our processes and the assistance we provide to our customers, in order to supply a tailor-made product modelled on their specific needs. In order to supply components for Formula One or Moto GP, it is necessary to be able to solve problems which other companies consider insignificant or even non-existent. It is clear that only a process kept under control can guarantee supplies which strictly correspond to the requirements of the designer and offer consistent quality. All this can only be achieved with a great deal of technical expertise, experienced staff, consolidated production procedures, great attention to technological content, a strong partnership with the customer in the mutual interest of quality work capable of generating competitiveness, without being attracted by the easy myths of large quantities churned out or higher turnover volumes. With this company philosophy we have always proved to be reliable and always in touch with our customers’ requirements, a special partnership made up of long-term relationships; we can safely say that our excellent strengths are the experience and expertise of our technicians and the almost zero turnover of our staff, a strong sign of lasting relationships and customised service.
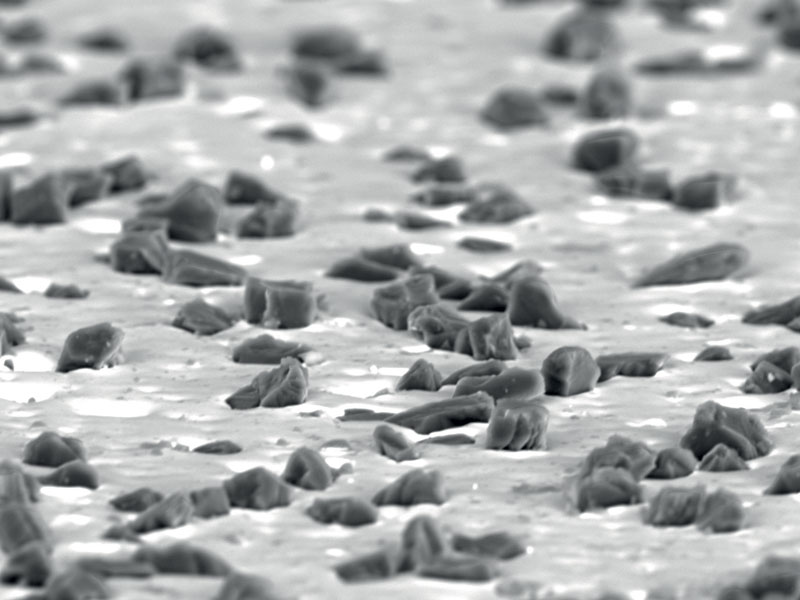
Could you tell us about your reference markets?
Italy is our main market; our customers then export their products all over the world. This means that the treatment processes we carry out must in any case comply with the specifications of foreign customers; for instance, we are in the process of obtaining IATF 16949 certification for the automotive sector. The components are fitted by the leading and most prestigious car manufacturers and by world famous component companies. To name but a few, we are suppliers to Brembo, Ducati and Ferrari.
Have you developed any special finishing processes?
We are talking about niche markets, but they are interesting for our company. We are able to treat light metals aluminium and magnesium with nanoceramic coatings by means of an electrolytic plasma of the metal substrate in a colloidal electrolyte applying a modulated high voltage, which converts the metal oxide into a crystalline form. The nanocrystalline oxide formed can have a thickness of 5 to 50 microns and a microhardness which, depending on the aluminium alloy treated, ranges from 1000 to 1600 HV. The treatment makes it possible to maintain the machining values unaltered.
Are your plants automated and what services can you offer your customers?
The most recent plants have been built according to Industry 4.0 logic, that is, automated and computer-controlled. Of course, the assembly and disassembly of the parts are manual; the shapes to be processed are countless and it is practically impossible to fully automate the process. Regarding service, which is certainly one of our company’s strengths, we are able, for instance, to carry out machining in 48 hours for specific customers to allow them to reduce their stock, according to a Lean Production model, and we carry out “Free Pass” code machining for important companies in the automotive sector. Of course we use non-polluting products in full compliance with environmental regulations. Besides, we guarantee complete traceability of the production process.

Nickel plating is an interesting process. Could you explain your NIPLATE® process?
Chemical nickel plating is a process of depositing a nickel-phosphorus alloy on metal parts. It is done by immersion in treatment solutions following specific steps, which are different for each metal. The deposition is electroless, that is, it occurs without the use of electric current and is based on an oxidation-reduction reaction. This allows a uniform and calibrated coating to be created over the entire surface of the part, regardless of its geometry. The nickel coating applied by this process has a bright metallic surface appearance, or matt if preceded by sandblasting. NIPLATE® is the European registered trademark, owned by Micron srl, which identifies the nickel plating we supply. For example, the Niplate 500 PTFE treatment is a nickel codeposit with uniformly dispersed PTFE particles which provide anti-adhesion properties and a low coefficient of friction. The Niplate 600 SiC codeposit gives very high hardness and wear resistance because it contains silicon carbide particles. Chemical nickel plating can be applied to almost all metals, for instance stainless steel, brass, copper alloys, titanium and of course aluminium. The latter represents about 30% of all nickel-plating treatments. Excellent results can be achieved especially on die castings in alloys with a high silicon content, which are normally difficult to oxidise in the traditional way. With chemical nickel plating, surface hardnesses of around 600 HV can normally be obtained, but with suitable subsequent heat treatments, values of over 800 HV can be achieved. Chemical nickel plating maintains roughness unchanged, has a low coefficient of friction and, unlike anodising, is a conductive coating which disperses heat better.
For more information: https://www.microncoatings.it/it/