Qui la stampa 3D è davvero un servizio end-to-end completo
Il mercato per i servizi specialistici di stampa 3D in metallo (AM) si sta rapidamente evolvendo, ciò è dovuto al fatto che sta aumentando notevolmente il numero di aziende che riconoscono i vantaggi di questa tecnologia rispetto alle tecniche di progettazione e produzione convenzionali. L’obiettivo di 3D Metalforge, azienda operante nel settore dal 2016, è offrire ai propri clienti un servizio di stampa 3D in metallo end-to-end completo, in grado di produrre componenti metallici complessi, di alta qualità e pronti all’uso.
In quest’ottica, i macchinari di produzione additiva utilizzati sono fondamentali per raggiungere questi importanti traguardi, non solo in termini qualitativi, ma anche rispettando i volumi richiesti. Al momento della scelta dei sistemi AM migliori, 3D Metalforge ha dato grande importanza al supporto tecnico che avrebbe ricevuto e alla capacità dei macchinari di soddisfare i requisiti dell’Industry 4.0. Questi dovevano garantire qualità, flessibilità e affidabilità ad alti livelli.
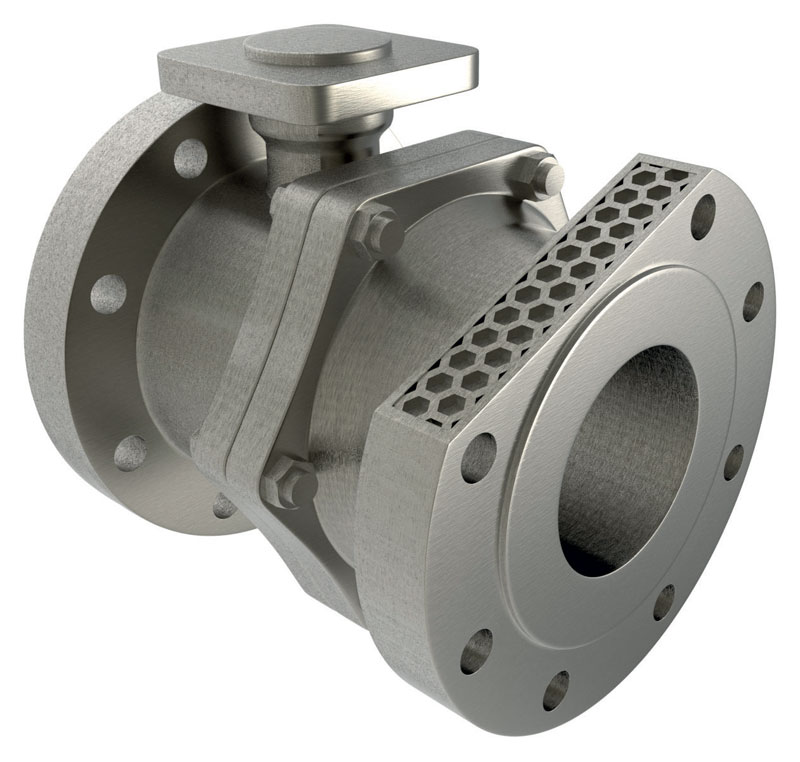
Un servizio di stampa 3D in metallo end-to-end completo
3D Metalforge è un’azienda di stampa 3D in metallo fondata a Singapore alla fine del 2016. L’azienda, nata a seguito della crescente domanda di componenti metallici complessi, fa parte del Gruppo 3D Matters, una delle realtà più importanti e in espansione nel settore AM del Sud-Est asiatico.
Per ciò che concerne la stampa 3D di metalli, le richieste dei clienti industriali stanno cambiando radicalmente negli ultimi tempi: dalla prototipazione e produzione di modelli singoli si tende ora a produrre pezzi in serie pronti all’uso. Questo ha richiesto una nuova struttura produttiva con notevoli investimenti in macchinari per la produzione additiva in metallo. Matthew Waterhouse, CEO di 3D Metalforge, spiega: “I clienti sono passati ben presto dal non sapere che alcuni pezzi potessero essere stampati in metallo all’avere ben chiari i vantaggi dell’Additive Manufacturing rispetto ai metodi di produzione convenzionali, anche in termini di complessità e alta qualità dei componenti”. Oggi, l’impianto produttivo di 3D Metalforge è certificato ISO e soddisfa le richieste di clienti industriali che operano in settori come il nautico, l’oil & gas, le lavorazioni di precisione e il manifatturiero. L’azienda produce componenti avanzati stampati in metallo come giranti, supporti per antenne, ganci di sollevamento e giunti snodati. Come azienda ad alta specializzazione, 3D Metalforge fornisce ai propri clienti un servizio di stampa 3D in metallo end-to-end completo, che include consulenza e diagnostica, progettazione e ri-progettazione delle parti, stampa di pezzi di alta qualità e successiva post-produzione (trattamento termico, segatura, pallinatura, lucidatura e finitura).
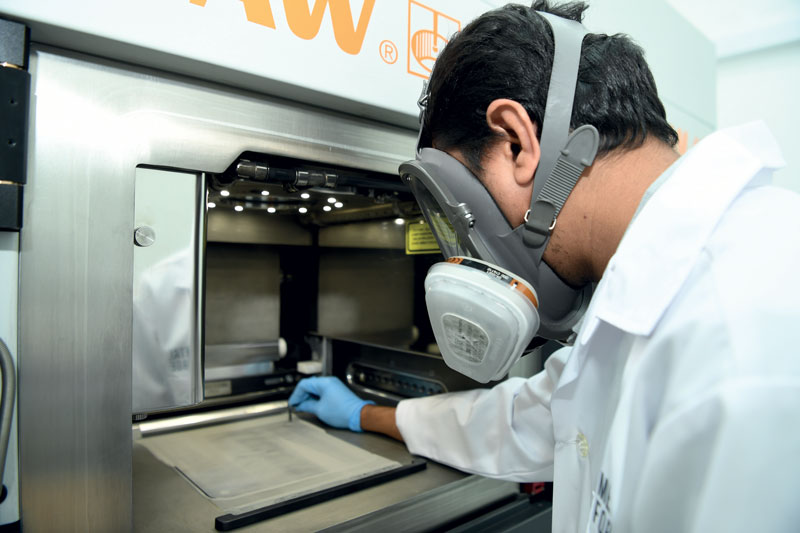
La sfida tecnologica
Come nuova impresa che opera in un settore manifatturiero in rapida espansione, 3D Metalforge ha criteri di selezione molto rigidi quando acquista sistemi di stampa 3D in metallo. Di fronte a un’ampia gamma di alternative, l’azienda doveva essere certa che i capitali investiti fossero in grado di soddisfare le esigenze attuali e future dei propri clienti e che rispettassero i seguenti criteri: I criteri includevano: I campioni creati in Additive Manufacturing dovevano essere di alta qualità e dimostrare la capacità di produrre un’ampia gamma di parti molto complesse con strutture e pareti sottili. L’assistenza tecnica doveva essere offerta dal produttore a livello locale, sia prima che dopo la vendita. L’affidabilità del sistema è di vitale importanza per la produzione di parti pronte all’uso, quindi questa doveva essere al top. Il sistema doveva essere di facile utilizzo, con una curva di apprendimento ridotta al minimo. Il produttore del sistema doveva inoltre dimostrare un’ottima conoscenza e comprensione delle esigenze produttive di 3D Metalforge. 3D Metalforge è inoltre estremamente attenta alle attuali tendenze dell’Industry 4.0. Il sistema di stampa 3D in metallo da acquistare doveva essere in grado di supportare i principi chiave della “quarta rivoluzione industriale”, come la trasparenza dei dati, la connettività e l’interconnessione uomo-macchina. Spiega Waterhouse: “Riteniamo che la stampa 3D in metallo non sia solo una parte integrante della rivoluzione Industry 4.0 ma pensiamo che sia soprattutto il motore trainante del cambiamento del mondo manifatturiero. Le aziende più lungimiranti a Singapore, e nel resto dell’Asia, stanno abbracciando completamente il concetto di Industry 4.0 e le decisioni che prendiamo devono riflettere tutto ciò”.
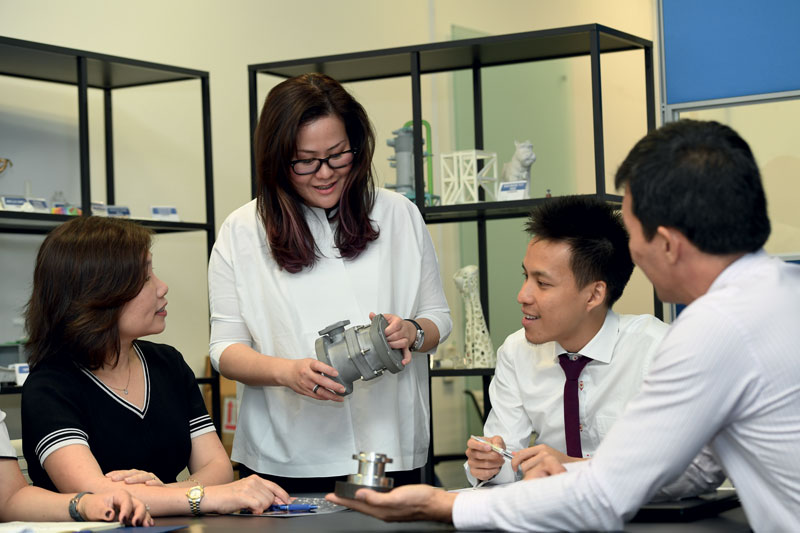
Facilitare le lavorazioni post produzione
Uno dei primi sistemi a soddisfare i criteri di selezione di 3D Metalforge è stato il sistema di produzione additiva AM 400 di Renishaw. La macchina ha una camera di lavorazione da 250 x 250 x 300 mm e un sistema laser da 400 W, con fascio di diametro pari ad appena 70 µm. La sua interfaccia uomo-macchina è molto semplice e intuitiva. Grazie alla scelta di Renishaw di tenere aperti i parametri della macchina, la AM 400 dà a 3D Metalforge la libertà di ottimizzare le impostazioni dei dati macchina in base alla polvere metallica utilizzata e alla specifica geometria da ottenere. L’atmosfera di gas inerte della macchina è ai vertici del settore, mentre il sistema SafeChange™ di gestione dei filtri minimizza l’esposizione degli operatori alle polveri e alle emissioni di processo.Il signor Waterhouse afferma: “Conoscevamo già molto bene Renishaw per i suoi prodotti di metrologia tecnologicamente avanzati. Ma, ancora più importante, Renishaw comprende perfettamente le esigenze della manifattura, conosce le problematiche d’impostazione e calibrazione dei materiali e sa come vogliamo che debba funzionare il nostro impianto produttivo”. “Fin dall’inizio siamo stati molto colpiti dall’altissima qualità dei primi campioni prodotti. Riteniamo che la stampa 3D in metallo e i processi di lavorazione tradizionali debbano integrarsi l’uno con l’altro ed è nostra convinzione che la Renishaw AM 400 possa facilitare le lavorazioni post produzione. Conoscevamo già molto bene Renishaw per i suoi prodotti di metrologia tecnologicamente avanzati. Ma, ancora più importante, Renishaw comprende perfettamente le esigenze della manifattura, conosce le problematiche d’impostazione e calibrazione dei materiali e sa come vogliamo che debba funzionare il nostro impianto”.
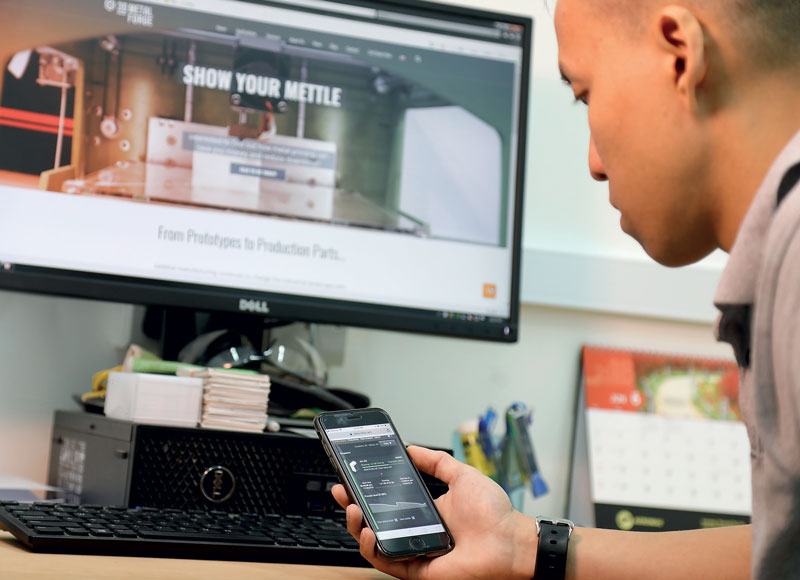
I software impiegati
Per la grande maggioranza dei lavori effettuati con la Renishaw AM 400, 3D Metalforge utilizza il software Solid Works per la progettazione iniziale in 3D CAD e il software Autodesk per lavorare sulla stampabilità delle parti quando necessario. Il software Renishaw QuantAM di preparazione alla stampa viene quindi utilizzato per ottimizzare le strutture di supporto, allineare il pezzo all’interno della camera di lavorazione e predisporre il file di stampa finale. 3D Metalforge utilizza anche InfiniAM Central di Renishaw, il software progettato specificatamente per il monitoraggio remoto dei processi nei sistemi di produzione additiva. Offre dati in tempo reale durante la costruzione dei pezzi, fornisce uno storico dei dati sulle lavorazioni passate e mostra analisi dettagliate sottoforma di grafici molto intuitivi.
Grandi doti di precisione e affidabilità
Nei 18 mesi successivi alla sua installazione, la Renishaw AM 400 è stata la stampante 3D in metallo più utilizzata da 3D Metalforge e Waterhouse ne esalta le grandi doti di precisione e affidabilità. Cita un esempio di come 3D Metalforge abbia potuto fornire un servizio di stampa 3D in metallo end-to-end completo a un’azienda di componenti tecnologici: l’azienda stava cercando un modo per ottimizzare il suo componente, un recipiente metallico, e migliorarne le prestazioni all’interno del prodotto finale. Poiché le tecniche di produzione tradizionali non erano in grado di ottenere il risultato desiderato, l’azienda si rivolse a 3D Metalforge per un’alternativa prodotta tramite stampa 3D in metallo. Ma il progetto del pezzo originale non era ottimizzato per la produzione additiva, quindi venne prima riprogettato. 3D Metalforge introdusse strutture reticolari per ridurre il peso e una nuova forma per migliorare l’allineamento del componente. Prima della finalizzazione del progetto, furono creati alcuni prototipi che vennero assemblati all’interno del prodotto finito. A oggi, sono state prodotte con l’AM 400 alcune centinaia di questi componenti metallici complessi, con un tasso di superamento del controllo qualità pari al 100%. La progettazione per l’Additive Manufacturing ha ridotto il peso e migliorato le prestazioni del componente. Per il futuro, 3D Metalforge prevede molto più lavoro nel campo degli standard e delle certificazioni per la produzione additiva, la cui conseguenza sarà la creazione di componenti industriali ancora più avanzati. Al crescere dei settori che si rivolgono alla stampa 3D di metallo, prevede inoltre l’espansione della gamma di polveri metalliche speciali. 3D Metalforge conta di espandere la gamma dei sistemi che utilizza e di estendere sia la varietà dimensionale dei pezzi prodotti che la tipologia di polveri metalliche utilizzate. L’azienda intende aprire ulteriori stabilimenti nei mercati asiatici in via di sviluppo e sta attualmente ampliando la sua presenza negli Stati Uniti, uno dei mercati più grandi per il suo business. “Per noi era fondamentale lavorare con un’azienda che conoscesse le problematiche del settore manifatturiero, anziché con un’azienda che produceva solo stampanti 3D, e la differenza si vede nelle prestazioni che ci garantisce questa macchina” conclude Waterhouse.