An assembly line full of technology
OTS Assembly is a company based in Rivalta di Torino, near Piedmont’s capital city, with more than half a century of history. A small concern but at the same time a great company, which interfaces with several multinationals, such as Schneider Electric. Precisely for the latter, OTS Assembly has recently designed and built a system for the assembly of thermal-magnetic circuit breakers, which has been shipped to the United States. Sandro Scarasso, the company’s current Managing Director, told us about it.
“The company was born in the garage of my family’s house, on my father’s initiative,” Sandro Scarasso told us. The company was founded in Castagnole Piemonte, near Turin, in 1968 – initially to build mechanical units to customers’ specifications. Over time, the company’s skills increased, along with the number of employees, and in the mid-1980s Leonardo Rossella joined the company, going from being an OTS Assembly customer to working “on the other side of the fence”, bringing new contacts and more important orders. It was during this period that production was transformed, shifting more towards automatic machining and assembly systems, which include robotic systems and test benches, among others. “ At the beginning of the Nineties, our network expanded even further,” Sandro Scarasso continued, “and our lines began to be successful, above all thanks to the passion we put into our work, which leads us to ensure that the machines operate perfectly. Little by little, we began to develop increasingly important and complex projects, and we met the world of multinationals. We are among the few, I should point out, able to offer high-speed automatic assembly systems and machines for small and very small products”. During this growth process, OTS went through a generational changeover which led Sandro Scarasso and his partner Alessio Rossella, the current Technical Director and son of Leonardo Rossella, to gradually take over the management of the company. In the 2000s, OTS Assembly met Schneider Electric, for whom it designed and built an assembly machine for the plant in Cognac, France. “Today,” Scarasso explained, “with Schneider, we have brought machines all over the world, and at present they are definitely our main customer: we actually produce about two plants a year for them”. The latest addition is a machine for assembling thermal-magnetic circuit breakers.

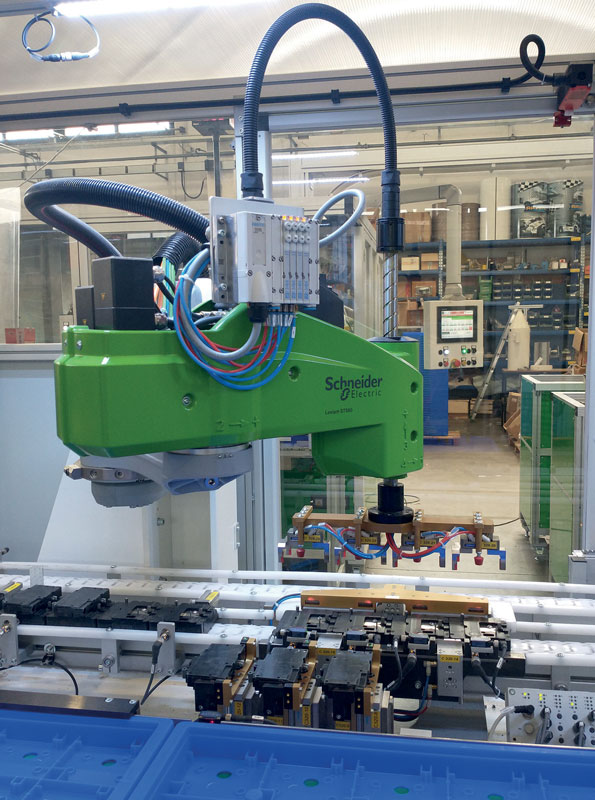
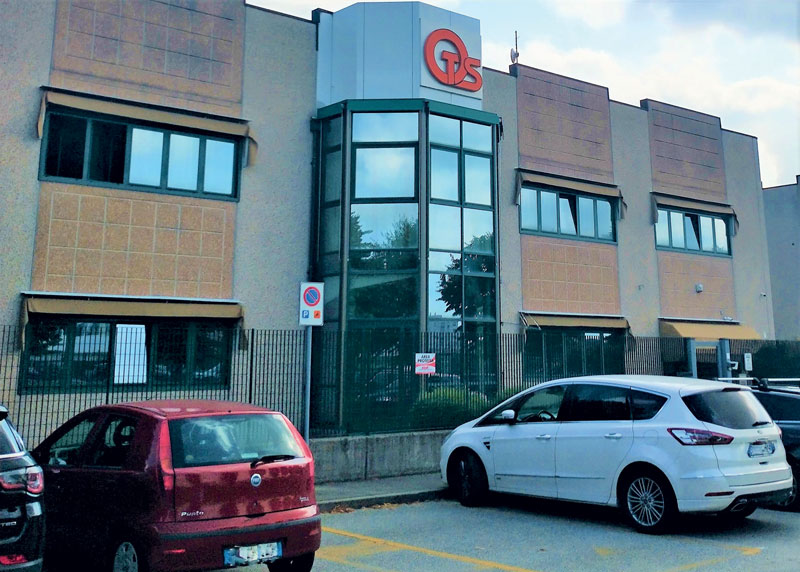
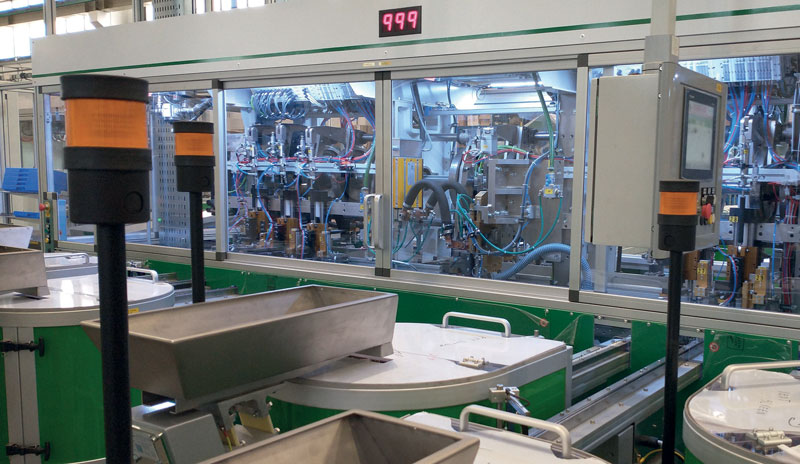
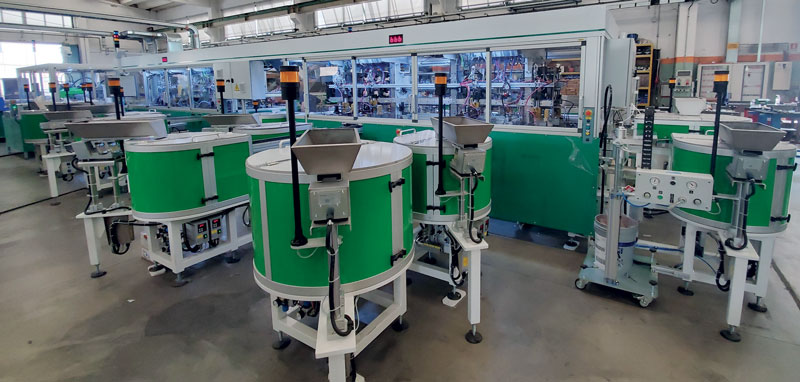
What the plant will do
OTS Assembly’s plant, which is considerable in size, has been shipped to one of Schneider’s US plants in Nebraska, where it will work for the US and Mexican markets and partially assemble a thermal-magnetic circuit breaker. It will work on the innovative CAFI version, that is, Combination Arc Fault Interrupter, which is designed to protect installations from potential damage caused by faults due to parallel and series arcs, and has an electronic card inside. “Our solution,” Sandro Scarasso explained, “will only assemble one part of this product, specifically the final part: the assembly of the barrel is very complex, so it is impossible to perform automatically, therefore our machine will work on a product pre-assembled manually by an operator. The OTS Assembly system is designed to assemble 15 different components (buttons, springs, contacts, etc.) for each circuit breaker. There are also 18 different power supply systems, each dedicated to one type of component, and an operator panel which allows the entire system to be managed and controlled intuitively.
There are many technologies within this plant, as well as assembly stations: there are those dealing with the gluing of components, welding, mechanical assembly, etc. There is also a robotic cell at the end of the line, where two Schneider Electric SCARA robots are dedicated to loading and unloading the assembled product. Riveting and adjustment, on the other hand, are carried out by a third-party machine integrated in the process. “We only deal with the actual assembly part,” Sandro Scarasso explained, “which according to our concept consists of assembling a part and inspecting it: for each assembly station, there is a control station which immediately follows to check that no mistakes have been made. If a step is not successful, the object is immediately stopped and does not proceed to the next ones, thus avoiding unnecessary expenditure of energy and waste of components. We can do this also because we work on platforms with mechanical cam movements, and the object travels on small pallets which are also moved mechanically. This is the best way to achieve a performance of 3,000 parts/hour, with a cycle time of 50 parts per minute: we are therefore talking about very high production figures, which cannot afford too much waste”. Just as there are several assembly cells, so there are different types of control and inspection systems: sensors and slide systems to check each component, fiber optic photocells at the end of the line, or a camera to check the trays after loading. “We have included a lot of technology in this plant,” Scarasso said, “also because our work requires a great deal of attention, both as regards the mechanical and electronic parts, so that the customer receives a machine which lives up to the performance required: only a multiplicity of perfectly integrated high-level technologies can guarantee this”.
Human capabilities are unrivalled
If there is a lot of technology, does it mean that artificial intelligence is present? “We have also integrated artificial intelligence,’ Sandro Scarasso explained, ‘but for the best part, it is a mechanical assembly. I would like to point out, however, that even if we talk about artificial intelligence, we can never do without human intelligence. We cannot, therefore, delegate everything to machines, because they would not be able to manage on their own: human beings remain at the heart of the factory system, where, thanks to technology, their intelligence and skills are enhanced by eliminating or reducing alienating jobs to a minimum’. Besides, without the human being, it is impossible to manage unforeseen scenarios such as those created by the pandemic, with all the consequences it has brought to the industrial world. “This plant,” Scarasso said, “was originally destined for a plant in Mexico, but due to the expansion of the market in the post-lockdown period, Schneider Electric decided to relocate it to the US site, and build another one for the Mexican site.” The design and the construction of this second plant were also entrusted to OTS Assembly. “Our machines,” Sandro Scarasso continued, “are all dedicated, customised and tailor-made to the needs of individual customers. What we do does not exist beforehand, we have to invent it: this means that for the most complex plants it can take up to 12 months of work, from design to construction, which implies total reliability of the project. Given the high worldwide demand and the urgency to meet the demand, Schneider has now commissioned OTS to carry out a second, almost identical project for Mexico”.
Reliability is also ensured by OTS Assembly’s flexibility and ability to solve unforeseen problems. For instance, in this period, the main problem is procurement: “Like everyone else at the moment,” Scarasso explained, “we have difficulty finding material, especially for electronic parts and iron. But we carry on anyway, indeed we try to work around the problem: if a product does not arrive, we look for a different one which can be adapted to the machine or we even modify the machine design. Our ability to adapt to needs with great flexibility, solve problems promptly and supply high quality products has allowed us to grow and gain the loyalty of important customers, who have been reaping the benefits of our collaboration for years”.