Assembling and disassembling: robot’s play
Backed by its 100 years of history, Mitsubishi Electric is one of the world’s leading robotics players, offering a complete solution for the assembly and even for the disassembly of products. From traditional industrial robots to cobots and automation platforms, Marco Filippis, Product Manager Robotics at Mitsubishi Electric, described the company’s philosophy during his speech at the Assembly Week.
2021 is an important year for Mitsubishi Electric: a century of history marked by innovation. Could you provide a brief introduction to the company?
For Mitsubishi Electric, 2021 represents an important milestone in its history, as it celebrates 100 years since its foundation marked by innovation and research and the development of solutions. Founded as a branch of the Mitsubishi group, becoming a separate reality in 1946, and dedicated to the production of electrical and electronic equipment, Mitsubishi Electric has a strong history in the world of Factory Automation thanks to a product portfolio covering industrial automation, process automation and numerical control machines.
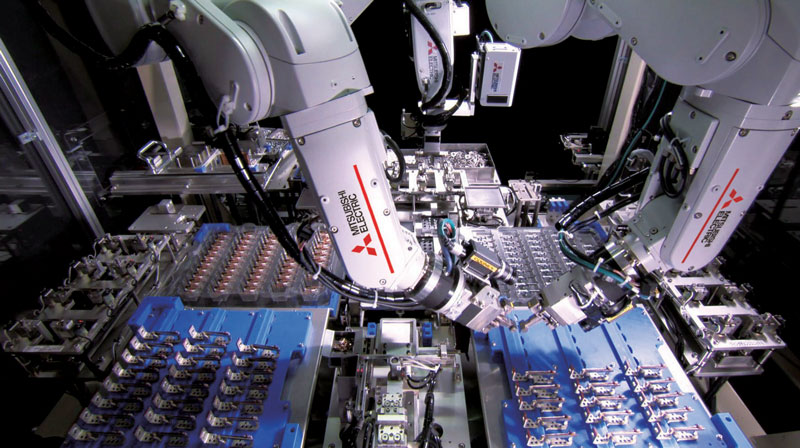
Let us look further into the assembly sector. What are the key points of Mitsubishi Electric robotics in this domain? I know you offer a complete automation solution, could you tell us about it?
Mitsubishi Electric’s robotics concept was introduced in 1980 to improve the production process in the group’s factories; but unlike many players on the market, robotics for Mitsubishi Electric is one of the elements of a complete automation solution. For this reason, the main feature of Mitsubishi Electric robots is their complete integration in the iQ-R automation platform, which results in native management of functions such as anti-collision and synchronised movements. These functions, especially for the assembly sector, represent an advantage both in terms of set-up and programming time, but at the same time they increase productivity remarkably. Another feature which makes Mitsubishi Electric robots particularly suitable for assembly is their proven repeatability, both for industrial robots, be they SCARA or anthropomorphic, and for the collaborative MELFA Assista family.
Over the years, you have always tried to pioneer the development of solutions to improve the performance of handlers. What is the innovative management of Mitsubishi Electric robotics in assembly? What impact does artificial intelligence have on different components, such as the force sensor, for instance?
Mitsubishi Electric’s pioneering role in the world of industrial automation has led over the years to the development of options which improve the already high performance of handlers. A classic example in the world of assembly is the force sensor, a load cell connected to the wrist of robots which ensures fine management of arm force. Especially for precision assemblies or those involving the handling of materials which tend to deform easily, the force sensor allows the torque on the robot joints to be controlled with high sensitivity. Its limitation in use is undoubtedly its speed, which must necessarily be reduced in order to achieve greater accuracy in fitting. To overcome this drawback, Mitsubishi Electric has chosen to exploit new technologies, and in particular to associate the sensor with Artificial Intelligence algorithms capable of learning what the speed limit is and optimizing the assembly process. This innovative technology is called optimized learning and can increase process performance by up to 40%.
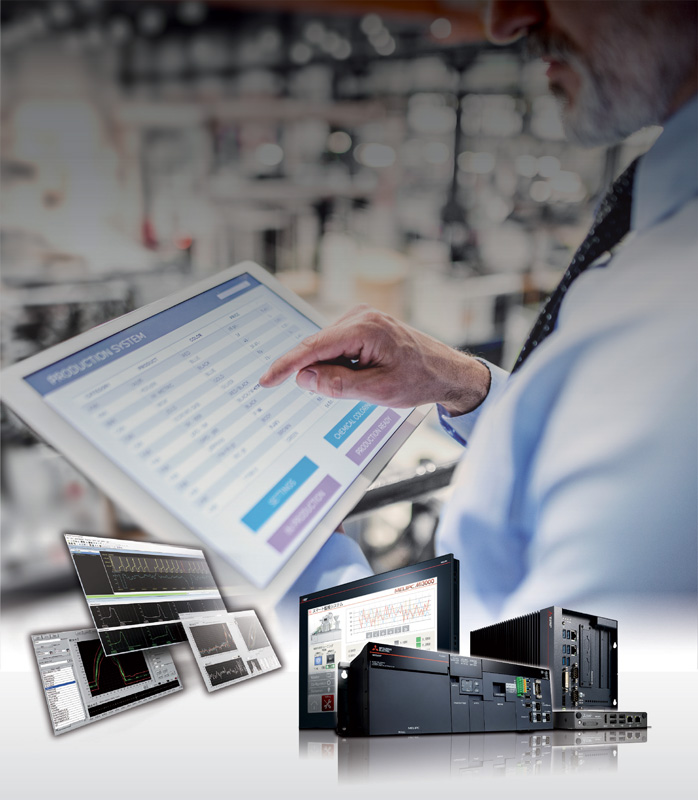
Dream big, but take small steps: this is your SMKL philosophy, involving targeted actions which can be achieved in the short term. Could you tell us something about it? How can it affect the improvement of the assembly process and companies in general?
As I said before, robotics for Mitsubishi Electric is a part of the whole industrial automation system which can be provided. Very often, however, products alone are not able to provide a solution to the problem, since experience and a clear vision must be added, also considering the speed at which industrial paradigms are changing. Today, the most discussed topic at industrial and institutional level is certainly the Digital Transformation process, which Mitsubishi Electric tackles with a purely Japanese approach and which is called SMKL (Smart Manufacturing Kaizen Level). This concept could be summarised as: “dream big, but take small steps”. This philosophy might seem, at a first glance, to be a fetter on the development of a process which is moving at a fast pace, but in reality it is a methodology in which priority is given to targeted actions which can be achieved in the short term, so that ROI is not an obstacle in the initial decision. Actually, by tackling the various problems present in companies with achievable and inexorable steps, a process will be converted by means of successive optimisations. In this vision, robotics takes on a fundamental aspect linked to the flexibility of machines and therefore to the calculation of defined and precise ROI.
Not only assembling, but also disassembling! In the world of electronics this is an important aspect, for example to recover individual parts of obsolete smartphones. This has a strong impact both in economic terms and in terms of saving raw materials. Could you describe some success stories?
In the world of assembly, the applications in which Mitsubishi Electric technology can be used are very different, but certainly a crucial aspect of our robots is their high repeatability, which takes on added value in repetitive and extremely precise tasks. One particularly interesting use comes from the world of electronics, where Mitsubishi Electric is a major supplier of robotic centres for both assembly and disassembly of components. A prestigious case history in this sense is the use of Mitsubishi Electric robotic solutions for the assembly of the console produced by a famous Japanese multinational. The Mitsubishi Electric automation and robotics systems allowed the production of consoles every 30 seconds, exploiting the potential of the iQ-R automation platform which, besides managing the integration of robots, motion systems and the logic part, is able to connect to the company management system to track the process and connect the factory environment to the IT systems. The same philosophy was applied to the disassembly of smartphones for a famous American brand, which uses Mitsubishi Electric technology to recover the individual parts of obsolete smartphones and reuse them, thus reducing the environmental and economic impact on the demand for raw materials.

To conclude, what do you think will be the future for Mitsubishi Electric? What are the trends in robotics in this industrial segment? Will robots increasingly become co-workers, or will they remain just tools, however advanced?
In my opinion, robots will increasingly take on a predominant role, not as an alternative to the operator, but as a colleague. What lies behind the Industry 4.0 paradigm is evolving, following technological and process innovations: today we are faced with an industry which is increasingly human centric, where operators are the throbbing heart of the factory and those who can bring real added value. The robot, in this context, is seen as a ‘colleague’ who is used to perform boring, dangerous and alienating tasks. We are in an evolutionary phase of the concept of robotics, as it is expanding more and more, leading to a qualitative upgrading of operators’ skills. And it is especially collaborative robotics which is going through the most important evolution: I expect that, in the next 4-5 years, there will be more cobots in factories and new application areas will be discovered. Collaborative robotics has had, and still has, one great advantage: it has brought robotics closer to those who were unfamiliar with this world, thanks to its ease of use, and it has “stirred” the consciences of those who previously did not consider it useful for their company. From a human centric point of view, I envisage many more cobots being installed within processes, but obviously they will never be able to replace industrial robots.