Collaborative Robotics is Already 5.0
Collaborative robotics has been a growing trend for ten years, and AutomationWare has not fallen behind. In fact, after its series of J-Actuators robot joints, the company is launching the AW-Tube cobot. The ROS robot operating system used for its realization will make it possible to offer a modular solution that can be customized in terms of work space and payload.
Since 2010, the demand for industrial robots has accelerated steadily, growing over the years, and many SMEs contribute to this escalation with a substantial increase in robot installations. AutomationWare did not fail to take action and accepted the challenge immediately by creating the AW-Tube collaborative robot, which will be on the market by the end of 2020. The AW-Tube will make it possible to combine human and robot capabilities, assisting and facilitating the operator in tasks within the same workspace. The result of this collaboration is an increase in the process quality, productivity and flexibility; consequently, making it more profitable for the company. Collaborative robots are considered one of the key elements of Industry 4.0 and future 5.0, together with artificial intelligence and Cloud systems. In order to be able to work side by side with humans, cobots must meet high safety requirements, be able to sense external forces and stop quickly in the event of a collision or contact. An essential requirement for collaborative applications is not to cause injury to people in the collaborative workspace in case of accidental impact.
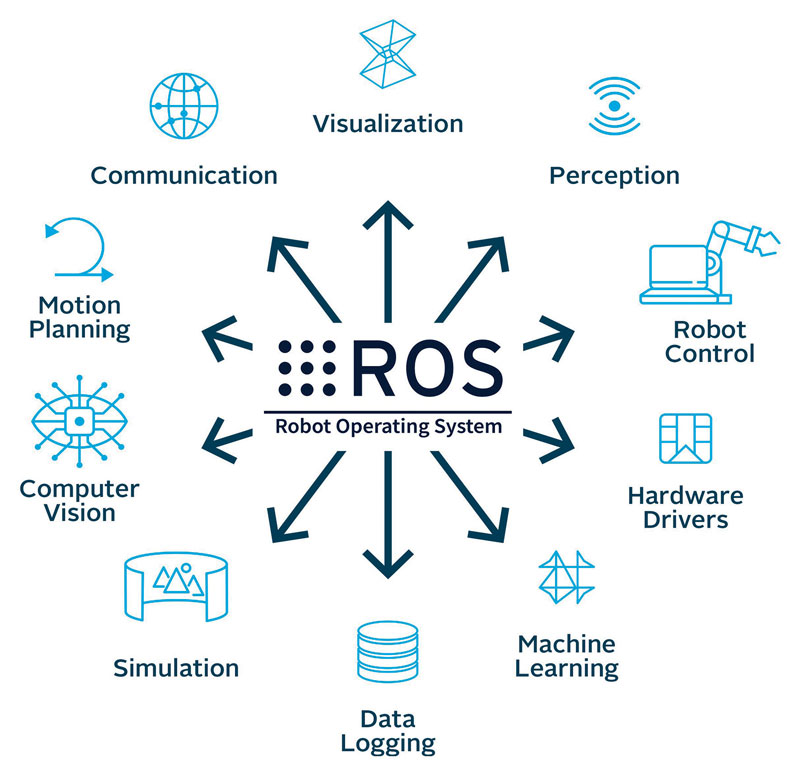
Robot joints for customizable robotics
In recent years, AutomationWare, taking advantage of the mechatronic skills acquired, entered the industrial robotics market with SCARA manipulators for Pick & Place activities. To expand its robot offer, the R&D department is currently focused on the design and manufacturing of the AW-Tube collaborative robot, to be launched on the market towards the end of 2020. The heart of the project are the J-Actuators, robot joints controllable via ROS, characterized by a light structure with external coating in special materials such as aluminum and plastic, rounded shapes to spread the contact force over a larger surface and thus reduce the applied pressure. The joints are equipped with a complex interconnection between electronics, software and sensors for safety management. The J-Actuators are a starting point for the manufacturing of new collaborative robotics solutions which are highly customizable in terms of loads and work area. ROS-Tube will consist of six J-Actuators joints, entirely designed and manufactured by AutomationWare, also using commercial components. With a view to a family of modular cobots, they are available in five different sizes (14-17-20-25-32), which differ from each other in terms of performance and therefore also in weight and size, and can be used in a wide variety of applications, in particular on rotary systems or machines, where torque performance on very small spaces and/or extremely sophisticated diagnostic control is required.
The latest addition, the J-32, is a highly performing joint: based on a high-performance torque motor, it develops a maximum torque of 353 Nm and a nominal 220 Nm thanks to a high-performance HD reducer. J-14, one of the smallest joints in the world, allows rotation at high speed while maintaining the maximum torque of 28 Nm. In collaborative robotics applications, one priority is represented by the joint output torque values which can be obtained in order to handle high loads. The requests for high torque and extremely low speed at the joint output make the use of harmonic reducers ideal. The J-Actuators integrate a synchronous motor with permanent hollow shaft magnets, a harmonic drive, an absolute multiturn magnetic encoder mounted on the fast shaft of the system and a parking brake as required by safety regulations for “emergency stop” and “protective stop”. The joint also includes a refined control electronics capable of communicating via EtherCAT bus with the robot motion controller, based on the ROS robot operating system; it integrates sensors and accelerometers to manage the safety of the manipulator collaborative operations. Vibration tests, movement availability tests and load tests were carried out on the joints. For vibration tests, the AwareVu diagnostic system patented by AutomationWare was used to offer real-time control of the joint. Using an FFT (Fast Fourier Transform) algorithm, the device, which in fact is an accelerometer, analyzes vibrations in three orthogonal axes and reports the results in the proprietary software “AwareVu App”: both acquisition in the time domain and the corresponding FFT are visualized.
The J-Actuators are robot joints controllable via ROS, characterized by a light structure. In the joint there is a refined control electronics capable of communicating via the EtherCAT bus.
The advantages of the ROS operating system
The ROS robot operating system was used to create the cobot, in particular the implementation of the mechanical project within it, the kinematics and the robot motion planning. The Robot Operating System is a very flexible open-source framework; it provides libraries and tools to create software for ROS robot applications, with supported programming languages C++, Phyton and Java. The advantages of this robot operating system are mainly two: the software architecture and the generality towards the specific robot model. For the developer, another big advantage of ROS is the independence between the specific robot model and the use of tools and algorithms available to it. The robot model is described in URDF (Unified Robot Description Format) containing the specifications with regards to geometry and graphics, as well as kinematics and dynamics, and is used within the framework for the study of direct and inverse kinematics, for visualization, simulation and management of the physical robot. Another very important aspect is the ROS-Control libraries that allow you to interface the software part with the robot physical hardware. They implement Real-Time and allow full robot control by fully exploiting the potential offered by the entire ROS framework. The MoveIt platform incorporates algorithms for motion planning, kinematics, control, 3D detection and manipulation and allows you to build the framework necessary for the creation and management of robot movements. ROS-Tube by AutomationWare will be able to offer its customers a modular cobot that can be customized in terms of work space and payload, with consequent energy optimization and related savings.