Finding the best robot for a smart factory
If you’re planning a strategy for developing a smart factory, how do you decide upon the best robotics solutions to adopt? An industrial robot or a collaborative robot? Autonomous mobile robot technology or a fixed SCARA? It isn’t easy to find the ideal solution for your company’s specific needs. A sophisticated catalogue of requirements is needed to guide robot selection and, ultimately, future success, how tells Omron.
New production requirements, increased automation, innovation efforts and global markets have all contributed to an 85% increase in the number of industrial robots in use worldwide over the past five years. This is the conclusion of the World Robotics 2020 Industrial Robots Report. Despite the coronavirus pandemic’s impact on the forecasted global sales of robots, actual sales figures remain high. Another trend identified by the report is the wider use of robots. The cooperation between people and machines (or robots) is high on the agenda of many CEOs in a bid to reduce employee workloads, increase efficiency and safety and improve processes. As part of this trend, many companies are asking, “Which system should we choose in order to meet our needs?”

Different robot and kinematics solutions
Robots differ according to technology, type and structure, as well as the field of application. They vary from fixed robots through to AMRs, which are currently replacing track-bound systems in many factories. In addition, there are standard industrial robots as well as the popular cobots. Cobots are increasingly being found in applications that enable them to provide concrete support to people – for example, when removing goods from crates or refilling them. Conventional industrial robots usually work independently rather than interacting with human colleagues. The types of kinematic construction include the four main categories: Cartesian, SCARA, articulated arm and Delta/parallel. A company’s choice will depend strongly on its particular location and scenario. Cartesian kinematics is a highly configurable approach, as it includes everything from the degree of freedom via a single axis to multiple axes of motion. Cartesian robots have several optimised drives, using either a ball screw mechanism or a belt-driven system. They can be used to assemble small parts, but also for very long part transfers such as suspension cranes, which can be found under the ceiling in production halls.
In contrast, SCARA robots are horizontal articulated arm robots. They have a cylindrical work area and work much faster than Cartesian and articulated arm robots. SCARAs are suitable for pick & place applications and other handling processes with low payloads – for example, in assembly, packaging or material handling. Compared with SCARA systems, articulated (or jointed) arm robots have a spherical working area. This is the largest robot segment as there are many application possibilities. Jointed-arm robots are often used in process-intensive applications such as welding, painting, adhesive application, assembly or material handling, as these enable their agility and dexterity to be fully exploited.
Delta or parallel robots have a cylindrical work area. They often support applications where products remain on the same surface during the pick & place process. The low-maintenance parallel robot is an overhead assembly solution that maximises access and reduces floor space. It’s particularly suitable for high-speed applications and lightweight products.

Selecting a robot
Depending on the location, production focus and individual needs, parameters such as range, load capacity, movement requirements, flexible expandability and interaction with other technologies such as artificial intelligence or image processing can all play a role when choosing a suitable robot. Therefore, before making a choice, it’s always necessary to define your exact process requirements. Only then can you determine the performance and functions needed from a robot solution. What products need to be manufactured or processed and how? Which movements should the robot perform? What distances should it be able to cover? Are tasks frequently changed? Are there in-house experts or should a machine operator control the robot? This isn’t only about the simple movement of a pick & place application, but also about existing interferences between the robot and its kinematics, as well as other parts that could move within the cell. But you must also consider the type of part production and throughput. The repeatability of a robot shows its ability (once learned) to return from the same position to the desired one. Precision is about specifying a certain position and moving the robot to that exact point. Finally, the topic of image processing should be taken into account, as this is becoming increasingly important for improving the productivity of robot automation. Image processing enables the system to take images, calculate the placement and orientation of the respective parts and guide the robot to the parts via robot-to-camera transformation. Image processing systems increase flexibility and reduce costs because parts don’t have to be fixed. A vision solution integrated into the robot system also allows the simultaneous inspection of the parts during the machining process, which reduces cycle times and increases throughput.
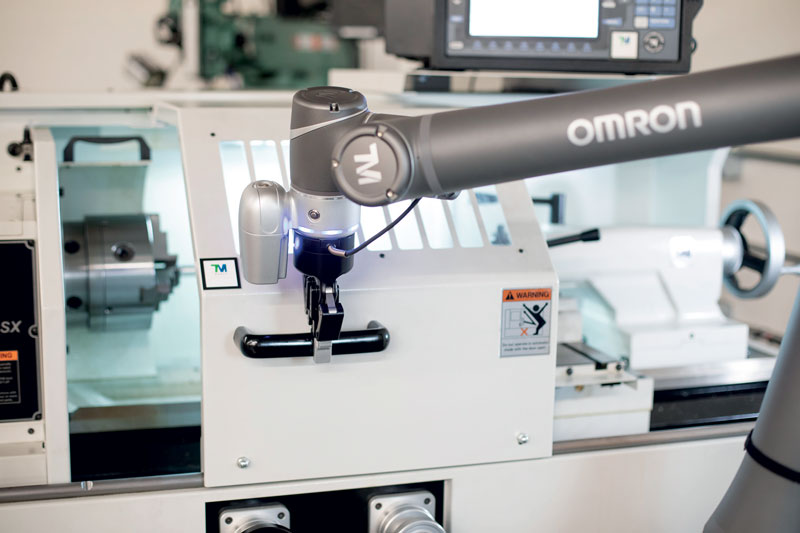
A permanently mounted system or a flexible cobot?
One question that many companies are currently asking is whether a cobot will meet their specific requirements. The answer depends on the situation. Fixed-mounted robots have the benefit of high speeds, precision, re-programmability, safety and high-performance technology. Flexible production lines can also be achieved with such systems, but experts are needed to reprogramme the robots. They also require significantly more space.
In contrast, cobots are easier to use. They are the ideal partner for high-mix, low-volume scenarios. They offer integrated security, can cooperate with employees and are more flexible and mobile. As they are also much simpler to programme and their software is more intuitive to understand, even regular machine operators can implement a new application, and external specialists aren’t usually required. Cobots can also be mounted on mobile robots. But which technology is best for which applications? Companies with short production cycles and throughput times might find traditional assembly robots more suitable because they work faster. Cobots are significantly slower, especially when working directly with people. In terms of safety though, standard robots have to be shielded from human colleagues (cooperative), whereas cobots can operate in closer proximity to people (collaborative). There’s a collaborative and a safety mode depending on the application.
Another aspect that can support the choice between traditional industrial robots and cobots is connectivity. Certain devices can be connected to machine controllers and have integrated vision technology with various camera options. Both fixed and collaborative OMRON TM technologies also support various interfaces and IEC 61131-3 programming. All machine information is therefore accessible via the controller. The cobot should also be able to interface with third-party technologies to give further flexibility. Various gripper modules, camera technology, attachments etc. increase the possibilities.
Another important point to consider is the return on investment (RoI). While fixed, more complex robots usually require training and external expertise, a cobot like OMRON’s TM series provides simpler online tutorials and quick start-ups. Traditional systems need to be managed by specialist robotics experts, while cobots are managed by their users. Fixed solutions often require additional hardware for more extensive tasks and protection (such as light fences or cages), whereas cobots are usually easier and less expensive to expand. They have the advantage of a shorter RoI.
SCARAs are suitable for pick & place applications and other handling processes with low payloads. The low-maintenance parallel robot is an overhead assembly solution that maximises access and reduces floor space.
AI essential for real-time applications
In summary, traditional industrial robots are often better suited for many applications in the field of high-speed, high-precision assembly. Cobots, on the other hand, are better for palletising, machine maintenance and material handling. Other applications include machine loading, order picking, packaging and testing. Cobots are also much more flexible and versatile when combined with mobile devices (such as OMRON’s LD series). Currently, these devices are available, for example, with special UV light attachments for disinfecting rooms. Cobots close a gap in the robotics market for applications in which flexibility is more important than speed, due to software tools and integrated sensor functions such as image processing, location determination and integration into storage systems.
However, there’s no single technology that’s suitable for every application. Therefore, a detailed catalogue of requirements and fixed project goals are vital for every successful robotics project in a modern, smart factory. The use of artificial intelligence is also becoming increasingly important in this context. At the machine level (at the edge), AI is crucial for real-time applications. Production lines and devices are monitored with real-time sensors, and data is collected and processed at high speed to quickly detect any anomalies.
So, companies that want to successfully meet future challenges need to start evaluating the robotics partner that will best meet their needs. Whether this is mobile or stationary, assembled or flexible, depends entirely on the type of application.