La formula giusta per ottimizzare la produzione
Le aziende che costruiscono, gestiscono e spediscono prodotti sono alla ricerca di modi per aumentare la produttività potenziando la produzione senza compromettere la precisione. Secondo Yamaha, il segreto per offrire il miglior valore possibile e il turnaround più veloce, in modo da ottimizzare la soddisfazione del cliente e mantenere il vantaggio a livello di concorrenza, è l’introduzione di un robot.
Come noto, l’introduzione di nuove tecnologie per automatizzare i processi di assemblaggio consente di potenziare produzione e qualità contribuendo al contempo a ridurre i costi. Le aziende che per prime riescono a individuare la formula giusta possono staccare rapidamente la concorrenza.
Parte della soluzione potrebbe essere l’introduzione di robot nelle attività industriali. Sebbene le cifre esatte dipendano dall’applicazione, si stima che l’introduzione di un robot per eseguire un singolo processo chiave in una linea di produzione possa aumentare la produzione fino al 40%. Ciò dipende dal fatto che i robot possono aumentare notevolmente velocità, precisione, affidabilità e ripetibilità. Inoltre, consentono di ridurre l’ingombro necessario per l’esecuzione di un determinato processo, permettendo un uso più efficiente degli spazi in fabbrica.
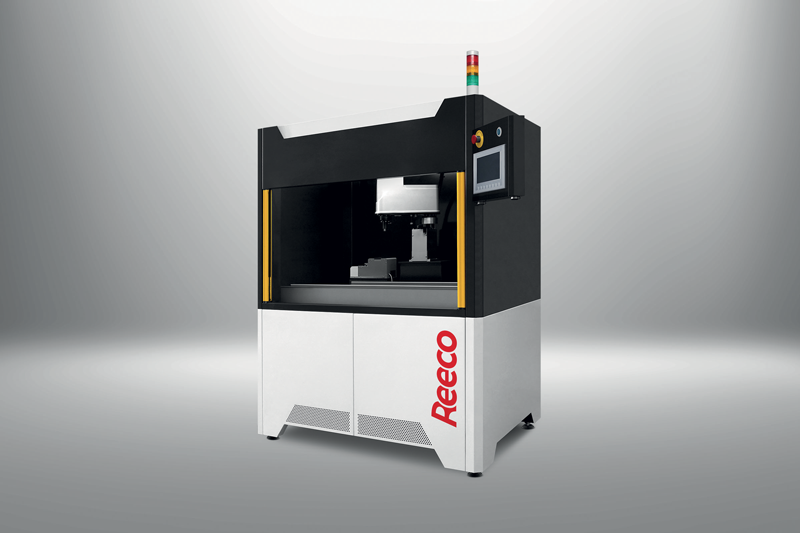
Gli ultimi modelli sono più convenienti che mai. Sono veloci e compatti e possono essere predisposti per interagire con l’automazione tradizionale o per supportare processi eseguiti manualmente dall’uomo. Ciò li rende facili da distribuire e utilizzare. Ma cosa possono fare veramente? Quali processi dovrebbero essere robotizzati per primi? Come dovrebbe essere riorganizzato il layout della fabbrica per far posto ai robot? E per quanto riguarda invece la scalabilità?
I robot odierni sono disponibili in dimensioni adatte alla movimentazione di articoli che pesano da pochi grammi a diversi chilogrammi. I tipi più diffusi includono robot SCARA, robot cartesiani e ad asse singolo o multiplo che possono essere utilizzati in un’applicazione indipendente dedicata a un processo o come parte di un gruppo o di una cella di assemblaggio configurata per processi in sequenza. Tali robot vengono utilizzati dalle aziende per realizzare progetti di automazione di vario tipo. Yamaha collabora con clienti e partner tecnologici per risolvere le sfide industriali attraverso l’implementazione creativa di robot, ottenendo una maggiore produttività e qualità.
Da un solo processo a molti Grazie all’ampio raggio di movimento, all’alta velocità e all’elevata precisione, i robot SCARA sono il veicolo ideale per eseguire processi di assemblaggio specifici. I robot SCARA YK-XG di Yamaha sono stati integrati in macchine autonome progettate per eseguire un processo specifico, come la saldatura, l’avvitamento o l’etichettatura.
Il robot SCARA, combinato con trasportatori, interfacce elettriche SMEMA e meccanismi associati, crea una soluzione pronta all’uso che le aziende industriali possono installare rapidamente in fabbrica. Le interfacce SMEMA standardizzate semplificano i collegamenti all’automazione a monte e a valle, dando vita a una soluzione completamente lineare. In alternativa, i pezzi possono essere introdotti manualmente o inseriti utilizzando un alimentatore. Queste stazioni robotiche consentono ai produttori di adottare un approccio flessibile e scalabile per l’introduzione dei robot nelle fabbriche. Uno per uno, i processi precedentemente eseguiti a mano, come la saldatura di cavi di collegamento o componenti con fori passanti nelle schede dei circuiti, il serraggio delle viti a una coppia specifica e l’apposizione di etichette, possono essere automatizzati per offrire maggiore velocità, ripetibilità e ritmi di produzione prevedibili. Aumentando progressivamente il numero di robot, è possibile configurare e far cooperare due o più robot SCARA e quindi automatizzare processi di assemblaggio più complessi combinando le rispettive capacità di prelievo, collocazione e posizionamento. Attualmente, alcuni esempi in azione includono l’assemblaggio di piccole parti automobilistiche in quantità elevate e con assoluta precisione. Prelevando i componenti da diversi pallet, controllando ogni parte mediante la visione con telecamera e garantendo l’orientamento esatto grazie a segni di riferimento, i due robot infine tengono insieme i pezzi per la saldatura o la saldatura a punti. Ogni componente assemblato viene quindi pallettizzato ed è pronto per essere rimosso dalla macchina per l’imballaggio finale e la spedizione. Questi sono solo due esempi che mostrano come la semplice automazione di una gamma limitata di processi, utilizzando robot SCARA a basso costo, possa offrire un ritorno rapido. Tuttavia, avvalersi di una combinazione maggiormente diversificata di tipi di robot, comprendente robot cartesiani e ad asse singolo o doppio, offre l’opportunità di passare progressivamente da solo uno o due processi di base fino all’assemblaggio completo, automatizzando del tutto la produzione di articoli che comprendono più componenti.
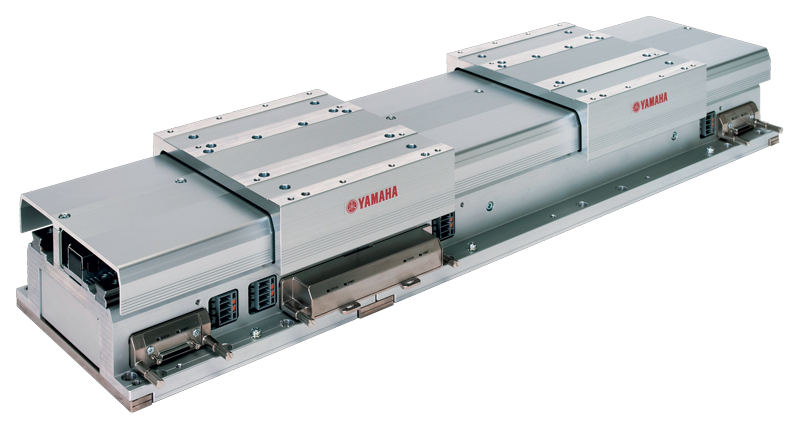
Automazione completa
La linea di robot Yamaha consente agli integratori di sistemi di creare una soluzione di assemblaggio completa, composta dalla combinazione più adatta di singoli robot. In un progetto di robot tipico, gli integratori di sistemi devono capire come spostare componenti o pezzi da lavorare da una macchina all’altra utilizzando un nastro trasportatore a rulli. Gli esclusivi moduli trasportatori lineari Yamaha, come l’LCMR200 hanno cambiato tutto introducendo il trasporto multi-programmabile che consente di configurare velocità, arresti di posizione e direzione utilizzando RCX-Studio 2020: lo stesso ambiente utilizzato per simulare, programmare e azionare tutti i robot nella cella. L’LCMR, con spostamenti bidirezionale ad alta velocità e rapida accelerazione, oltre a piccoli movimenti incrementali, è caratterizzato da azionamento diretto servocontrollato che elimina i fermi meccanici e i sensori di posizione tipicamente necessari per controllare un trasportatore convenzionale. Ogni slider può essere programmato e controllato indipendentemente, trasformando il “flusso passivo” di un normale trasportatore in un trasporto controllabile attivamente. Con le singole unità integrate e controllate tramite il controller universale Yamaha serie YHX, il trasporto tramite i moduli LCMR può far risparmiare circa il 65% dello spazio dietro il pannello di controllo e ridurre i tempi di cablaggio fino al 50%. Utilizzando RCX-Studio 2020, il trasporto dei pezzi può essere progettato come parte integrante della soluzione robotica, offrendo una preziosa flessibilità extra. I moduli possono essere specificati in varie lunghezze, offrendo l’opportunità di ottimizzare il layout della cella di assemblaggio per massimizzare completamente e garantire il minor ingombro possibile. L’LCMR200 offre una comodità extra grazie alla possibilità di eseguire processi come l’assemblaggio meccanico o i test elettrici sui componenti mentre rimangono sul modulo di trasporto. Dall’esterno, e anche dopo una dimostrazione introduttiva, un robot può assomigliare molto a un altro. Quando si sceglie, è importante valutare non solo la capacità di carico, facilmente confrontabile tramite le schede tecniche, ma anche altri aspetti del progetto quali velocità e tempo del ciclo, consumo energetico e affidabilità. Il sistema di rilevamento della posizione Yamaha, presente nei robot SCARA della serie YK-X, utilizza resolver invece dei tipici encoder, che possono essere influenzati da contaminazioni come grasso o polvere, nonché da campi magnetici o elettrici. Inoltre, la trasmissione senza cinghia presente su modelli selezionati garantisce una precisione costante a lungo termine senza deterioramento nel tempo. Sono disponibili anche modelli speciali come le varianti antipolvere e antigoccia per l’uso in ambienti come camere bianche e aree di preparazione dei cibi.
Visione robotica semplificata
Un semplice robot “cieco” è in grado di gestire in modo soddisfacente un’ampia varietà di processi industriali. Tuttavia, completare la soluzione introducendo la visione amplia le opportunità di affrontare processi più complessi, verificare l’accuratezza della posizione e migliorare la qualità. Si tratta spesso di una sfida complicata che richiede competenze speciali di visione artificiale per far dialogare il sistema di visione con il controller del robot. Con il sistema di visione iVY2+, Yamaha introduce la visione nell’ambiente di controllo e programmazione del robot. Il sistema include moduli telecamera di massimo 5 Mpixel e schede di interfaccia telecamera compatibili con i controller dei robot serie RCX3. Sono inoltre disponibili istruzioni di visione speciali che semplificano la programmazione utilizzando RCX-Studio 2020 e consentono la ricerca e il monitoraggio dei componenti ad alta velocità.
L’introduzione semplificata della visione artificiale nel robot consente agli utenti di sfruttare funzionalità avanzate come il rilevamento di regioni, che consente di prelevare, riconoscere la presenza di oggetti e contarli ad alta velocità quando si lavora con articoli di forma irregolare come alimenti e indumenti. Il sistema iVY2+ è provvisto inoltre di un motore di ricerca dei bordi delle immagini che migliora il rilevamento delle parti in condizioni di illuminazione difficili. Una procedura guidata per aiutare a calibrare il sistema e un processo semplificato in tre fasi per la registrazione del pezzo in lavorazione (che richiede all’utente di selezionare solo le impostazioni di acquisizione delle immagini, contorno e posizione di rilevamento), consentono di eliminare attività faticose e aiutano gli utenti a completare le impostazioni con una velocità fino all’80% più elevata rispetto ai sistemi di visione generici tradizionali.