Power Quality and advanced components to optimise efficiency
Automated and interconnected systems are increasingly used in assembly plants. The number of fully digitalised and automated plants is growing, especially in the automotive sector, also thanks to the incentives provided by the Transition 4.0 Plan and the related National Recovery and Resilience Programme (PNRR). To optimise their performance, attention must be paid to various aspects, from power quality to component performance.
With the major role played by automation in the industrial sector today, from the simplest machine monitor to the most specialised robot, it is clear that it is essential to prevent the failure of electrical components as well as traditional mechanical failure. Indeed, the unforeseen failures which most frequently affect automation are not only caused by mechanical wear or incorrect design of industrial equipment, but also, to a large extent, by Power Quality issues.
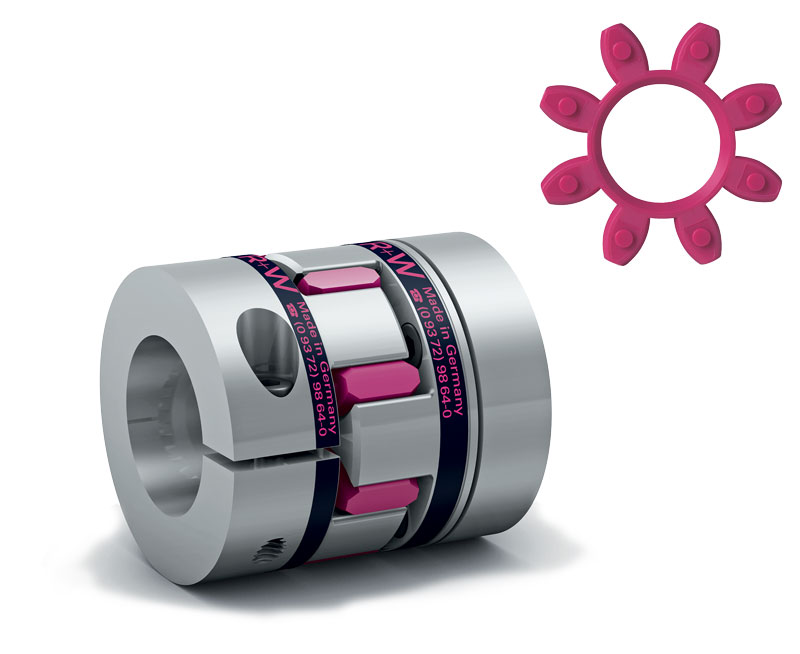
What are the most important factors in its decline? How do we explain their origins, their form, their effects on industrial equipment and the danger they pose to workers? What is meant by Power Quality problems?
The definition of Power Quality connects two aspects which characterise mains voltage: voltage continuity, that is, the absence of total or partial failure, and voltage quality, in terms of frequency, effective value and waveform. Problems related to Power Quality can depend on circumstances within the company, such as construction work, turning on high loads, faulty distribution components and particular electrical background noise, or on external occurrences, such as atmospheric events (hurricanes, lightning, snow, ice and flooding) and faults in the distribution network. Research work carried out in the United States by the Electric Power Research Institute provides a clear overview of the consequences of electrical faults, especially in economic sectors such as industry and services typical of the 2.0 economy, where losses are estimated at around 45.7 billion dollars a year. If the analysis is extended to all economic sectors, the total loss is estimated to be between 104 and 160 billion dollars.
Phenomena and effects
Let us therefore analyse which phenomena most affect the above-mentioned aspects of continuity and voltage quality. Interruptions: more or less prolonged losses of electrical voltage, normally caused by atmospheric events or a major fault in an element connected to the electrical network. The damage resulting from such interruptions mostly concerns the loss of unsaved data. Transient disturbances: these can be impulsive or oscillatory. The former are characterised by high current peaks of short duration, for example due to lightning or electrical discharge, while the latter are caused by a sudden change in the voltage load, as in the case of the unexpected shutdown of a high-consumption machine. Undervoltage: Reductions in electrical voltage within the circuit. The damage they cause may not be immediately visible but will show up over time as the phenomenon recurs. The effects of such a malfunction are the possible corruption of stored data and, in the event of a repetition of the event, overheating or damage to the power supply system. Overvoltages: the phenomenon opposite to the one mentioned above. They are normally caused by a high load reduction and can give rise to data transcription errors. Waveform distortions: these are anomalies in the waveform. They can be caused by obsolete technology, voltage transformers with a different frequency from the original one (typical of cycloconverters in mining plants) or insufficient earthing connections. They cause overheating, flickering in monitors and communication interference. All of these phenomena and the above effects are highly devious, as they are responsible not only for equipment failure but also for intermittent faults, that is, those malfunctions for which the reasons are often not identified due to their almost unpredictable presence (the typical fault which can be solved by switching the machine off and on again, but whose cause is never discovered).

Modern technology comes to the rescue
In order to solve all these long-standing problems and safeguard the automatic machines, researchers at the Massachusetts Institute of Technology Donnal, Leeb et al. have devised and tested an innovative solution. With the help of a control unit which monitors the electrical network in question, called NILM (Non-Intrusive Load Monitoring), data are collected on the current and voltage required from the network and a real-time diagnosis is made of the health of the various connected utilities. The innovative device is able to break down the information collected and allocate each connected machine its own share of current and voltage requirements, as if each utility had its own distinctive stamp; all this is the result of a complex system of algorithms based on neural networks. In this way, whenever a device connected to the network presents an electrical anomaly, the NILM system detects the information which, if repeated over time, leads to the signalling of a possible impending failure of the equipment. Therefore, as a consequence, it becomes possible to implement predictive maintenance, in order to better organise the timing of intervention and, in the case of applications which are particularly dangerous in the event of a fault, to prepare preventive replacements. For the trial phase, since this technology is currently only suitable for monitoring small lines, albeit with many utilities, the choice fell on an American coastguard ship, which proved effective in detecting faults in equipment and machinery on board in advance. In order to monitor more complex networks, the developers have chosen to have several NILMs communicating with each other, each connected to a subnetwork, so that all the data collected could be presented in a compact graph. The developers also emphasise the possibility of using monitoring tools such as the one described above even to examine the consumption and efficiency of various utilities, so as to optimise energy savings.
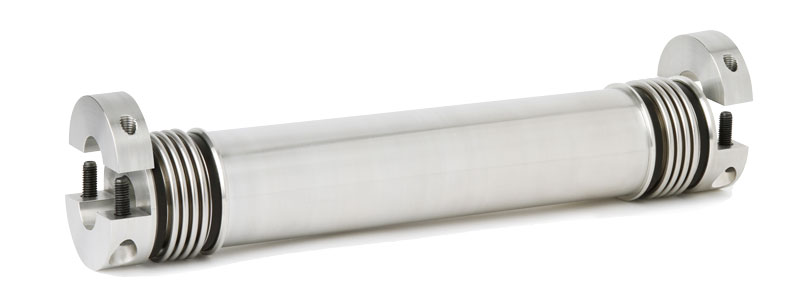
The role of the component supplier
In the event of failure of electronic equipment in assembly lines or automatic machines, the most important thing to avoid is the propagation of damage. This is particularly true when working in hazardous atmospheres, such as extremely reactive or explosive ones, defined as ATEX, where even a simple spark could compromise the worker’s safety. The term comes from the French name of the 2003 directive ‘Les appareils et les systèmes de protection destinés à être utilisés en ATmosphères EXplosibles’ (explosive atmospheres). European legislation has adopted two health and safety directives, ATEX 2014/34/EU (also ATEX 114) and ATEX 99/92/EC (also ATEX 137 now ATEX 153). The two documents impose, depending on the level of risk, a given level of protection for the equipment used, which can be achieved, for example, by dispersing or hindering the spreading of free charges, through to disconnecting the power supply in the presence of hazardous atmospheres. In the field of industrial automation, R+W provides specific solutions for torque transmission and control requirements. In these areas, the most commonly used couplings include the EK elastomer couplings and the EZ2 and ZAE line shafts. In elastomer couplings, the calibration of the elastomer insert ensures backlash-free transmission and perfect adhesion to the elastomer seats created in the hubs, guaranteeing high concentricity for precise operation. The damping capacity of elastomer couplings can have a particularly positive effect on the service life of adjacent equipment, especially in the case of vibration, shock load and dynamic movements. Electrical conductivity is another important feature of the special ATEX-certified version, which allows any electrostatic charges to be earthed, thus eliminating potential sparking and consequently the potential for explosions when used in hazardous environments. As for the EZ2 and ZAE line shafts, these have been designed with a very high level of balancing, enabling them to connect even very distant shafts at high speed. In general, all R+W products are perfectly adapted to the requirements of assembly, as the entire range is characterised by qualities such as zero angular backlash, precision, lightness and solidity. These properties are highly appreciated by operators in the sector, as is the assistance service offered by R+W during the design and sizing phase, in order to be able to offer a tailor-made product based on individual requirements.