Automotive and IO-Link: the Production is Easier
Ease, speed, efficiency: at the production plant of components and auto spare parts, Turck Banner showed the benefits of its IO-Link solution for signal connection. All with a transparent network structure
by Ginevra Leonardi
The automotive industry is currently a highly competitive sector. Plants build cars whose quality differences between the various classes of vehicles are increasingly subtle. Competitive pressure is also felt by the sector of components and spare parts suppliers. An example is the production of axle differential gears for automobiles. In this sector, Turck Banner developed a solution for connecting sensors and actuators to fieldbus gateways in a production site for components and spare parts. Several magnetic field sensors on the production line of the differential gears detect the positions of pneumatic cylinders and clamps, while proximity switches detect components of the differentials themselves.
There are also many actuators such as air valves, solenoid valves and other devices, which perform the commands of the controller.
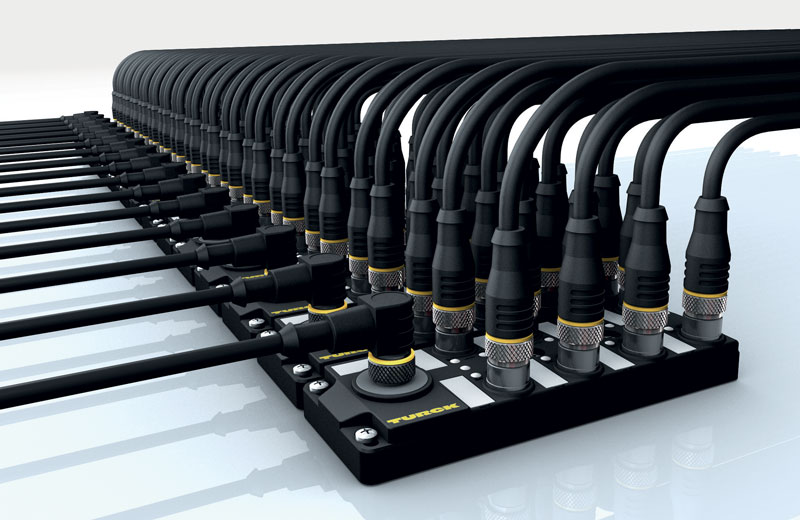
The disadvantages of multicore cables and passive junctions
At the beginning, it was intended to connect the signals of sensors and actuators to the fieldbus gateways in the control cabinet with passive junctions and multicore cables. However, this solution did not meet all the specific requirements. The costs for cable lengths and the commitment for wiring would have had a negative effect on the overall cost. Many passive junction cables would have to be prepared manually and then reconnected to the IO modules in the control cabinet. Commissioning would have been particularly error-prone, as well as taking a long time. The solution would also have been very expensive and difficult to maintain.
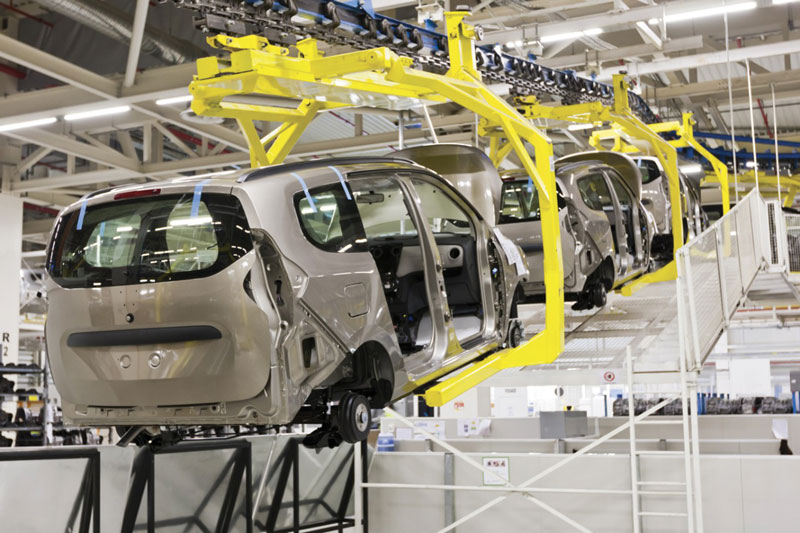
The solution that ensure speed and efficiency
Turck Banner offered a space-saving solution that simplifies the wiring of production workbenches and is also cost-effective. It allowed the implementation of diagnostics down to the sensor level. The customer used a Siemens controller with Profibus-DP. As a result, Turck Banner proposed a BL20 Profibus gateway for the control cabinet in combination with the IO-Link master modules. Turck Banner’s IO-Link compatible TBIL junction boxes are ideal for the connection of sensors and actuators in the field. These IO hubs use IO-Link to bring up to 16 binary signals to the IO-Link master via a standard sensor cable. The 16-bit process signal of the IO-Link protocol is therefore not used for an analog process value, but for transferring 16 individual switch signals for digital input or output signals. As the TBIL I/O hubs offer protection to IP67, they can be mounted directly in the field as close as possible to the sensors and actuators. IO-Link is a digital protocol that allows the use of standard three-wire cables, which eliminates the need for any expensive shielding and lengthy cable commissioning.
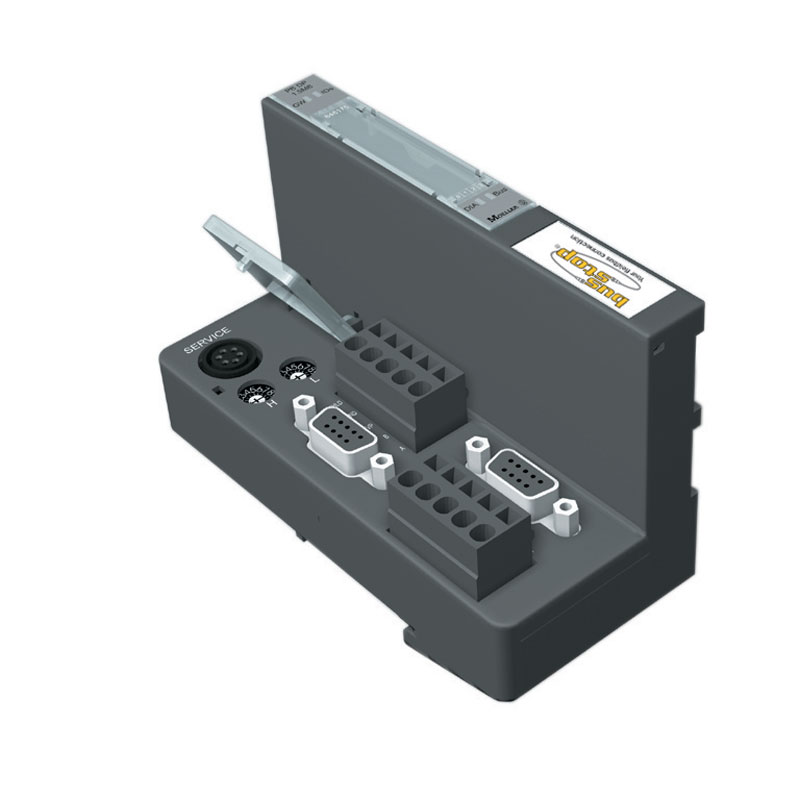
An efficient network structure and an easy maintenance
This network structure, consisting of IO hubs and Profibus DP gateways with IO-Link master modules enabled the user to avoid long wiring in the control cabinet and allowed to save on terminals, on expensive cables and on the space required.
The solution also provided an outstandingly simple and clear network structure that prevented faults already at the installation stage. If any faults occurred later, maintenance can be simple thanks to the use of IO-Link. The identification of faults can go down to the single field device and differentiates between a wire break or a short circuit. Central configuration of the entire system from the controller ensures central availability of all relevant information. This simplifies both maintenance and documentation.
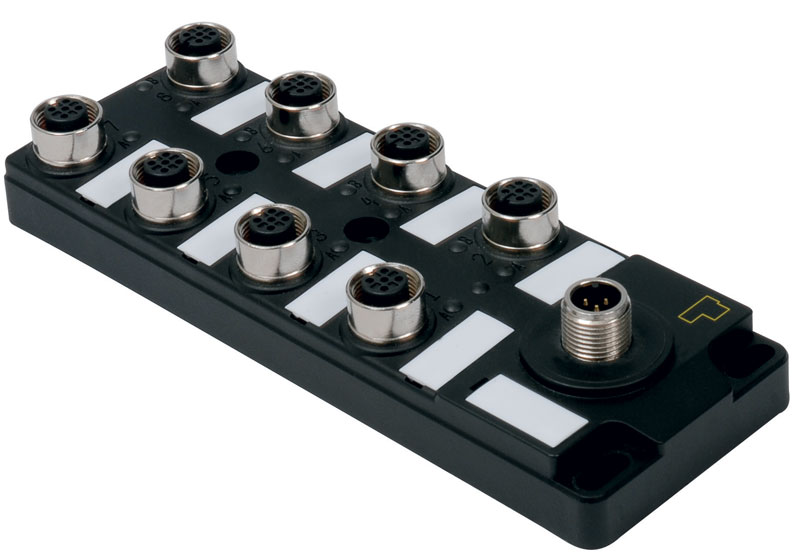
The costumer appreciated the benefits
An IO-Link module on the BL20 gateway provides four IO-Link masters. This means that up to 64 binary signals can be connected with a single module. The flexibility of the overall solution is always guaranteed. Additional IO-Link master modules or other IO modules can easily be connected to the BL20 gateway. The customer was therefore able to complete the commissioning of the system quickly and successfully. The workload was still manageable, thanks to the use of identical sensors connected and only IO TBIL hubs used as IO-Link devices. Even though IO-Link is still unfamiliar territory for many customers, the initial skepticism, in particular due to the unusual setting in the controller, turns into an enthusiastic belief about the benefits at the end of the installation of IO-Link. The project engineer for the customer said: “We have good reason to believe that the IO-Link communication interface will be the best choice for the new generation of smart devices. Devices with IO-Link communicate data digitally and can therefore exchange process values, as well as configuration information and diagnostic data. The exchange of information is transparent across the section from the sensor to the controller”.
A wide IO-Link portfolios
From measuring and switching sensors, to connection technology and the TBIL I/O hub, to the IO-Link masters for the most important fieldbuses and Ethernet protocols in IP20 and IP67: this system diversity is Turck Banner’s pride and joy. In the future, the integration of IO-Link devices on the IO-Link Turck Banner masters via the controller will be even easier. The setting options of the Turck Banner devices are integrated in the GSDML file of the Turck Banner IO-Link master. For the customer, this means it is only necessary to read GSDML in the controller software to set up a device. Devices just have to be selected on the master. The IO-Link device parameters to be set can be selected via drop-down fields instead of having to program IO-Link call function blocks manually. The time saved means that the installation can be put into production even faster, thus offering an advantage in highly competitive markets such as the automotive components and spare parts industry.