Quality: Face Masks Are under Control
The autonomous machine vision system by Inspekto is installed by a German manufacturer to produce face masks: it flags up the items that present defects in the designated areas, as well as metal strips that could damage equipment
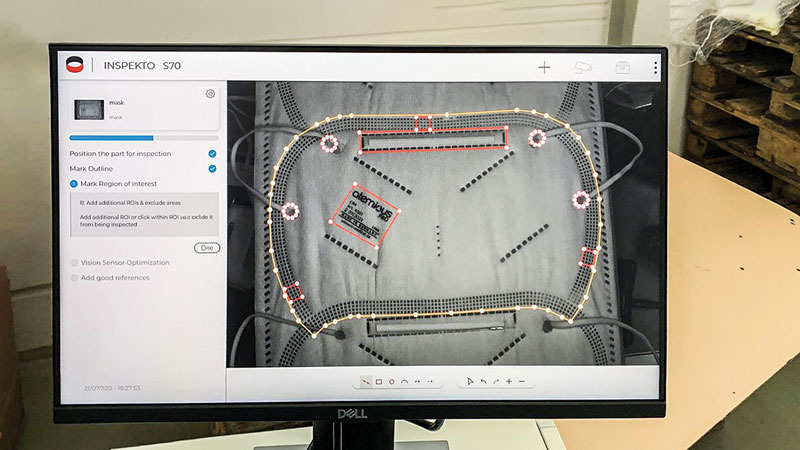
A German-Israeli company, Inspekto provides quick solution for new quality assurance need. The company, that is specialized in the machine vision field, has made its signature product available to the medical sector. Univent Medical, a manufacturer based in Baden-Württemberg in Germany, recently installed the Inspekto S70, an autonomous machine vision system on the market, for the quality inspection of FFP2 face masks, and the results are positive. The system ensures that masks are made to specifications, and that the manufacturing line is not damaged in the process.
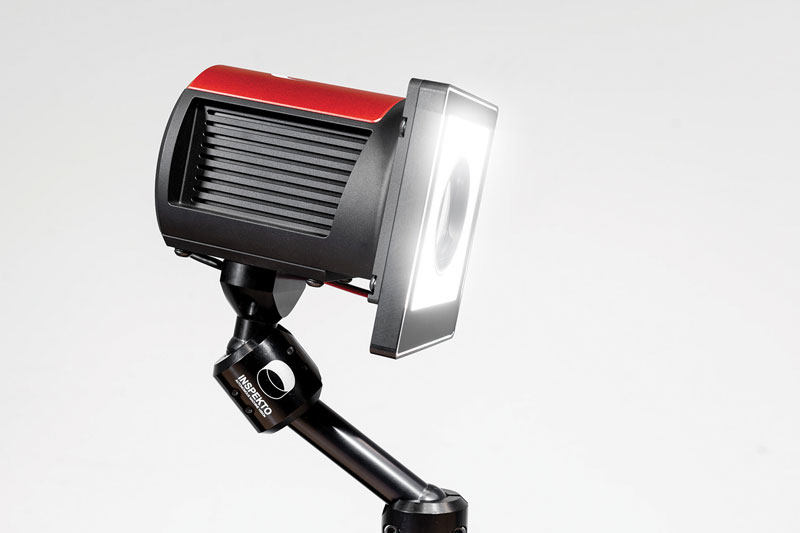
A fully configured device which comes ready to use
To help in the fight against Covid-19, Univent Medical recently established a new production line to respond to the pressing market demand for emergency supplies. The Inspekto S70 is a self-contained, out-of-the-box vision inspection system for industrial quality assurance. Unlike traditional machine vision solutions, which are custom-built, it is a fully configured device which comes ready to use, only requiring final integration on the production line. This makes the product ideal for manufacturers who need reliable quality assurance fast. Therefore, the Inspekto S70 has recently been installed for the quality inspection of FFP2 face masks. In particular, the system is expected to detect defects in the masks’ ultrasonic soldering, metal nose holder, company and CE-logo, and straps soldering. Inspection of the metal nose holder is of critical importance, as defective metal strips could permanently damage the cutting machine on the production line.
A vision solution that is quick to set up and easy to operate
The last weeks showed that the results of the installation are very positive, as the system was able to perform accurate and reliable quality assurance, flagging up masks that presented defects in the designated areas, as well as metal strips that could damage equipment. “Manual inspection carries a very high error rate, and we can’t allow that to happen when producing critical emergency supplies, such as face masks” stated Jürgen Eichinger, operations manager at Univent Medical. “Quality is at the core of all our operations, which is why we needed a flexible machine vision solution that would be quick to set up and easy to operate. We found the ideal partner in Inspekto.”
It learns the characteristics of any product from 20 good samples
“One of Inspekto’s goals is to allow all manufacturers, small or large, to deploy top notch automated quality assurance” declared Ofer Nir, CEO of the company. “We realised early on that manufacturers need a flexible and cost-effective option to inspect their products, and that this need would become critical at some point. Now the moment has come and we are ready to help.”
Vanessa Pfau, Manager for Germany at Inspekto, remarked that the flexibility of Inspekto’s systems will be essential to support manufacturers in the post-pandemic scene, and she explained: “The Inspekto S70 is not product-specific. It autonomously learns the characteristics of any new product in about an hour, from just 20 good samples, then flags up any abnormalities during inspection. This means that it can be used to inspect a huge variety of different items”.
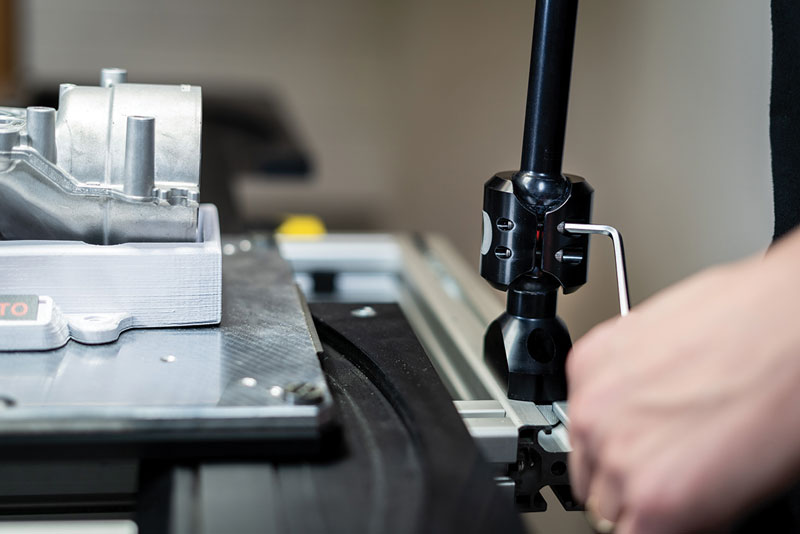
The same system can be used if they switch production again
The face mask production line didn’t even exist until a couple of months ago. It has been developed through funds from the German Government to help manufacturers adapt their production lines to produce emergency supplies. The Inspekto S70 quickly learned the characteristics of FFP2 masks, but if the plant managers decide to switch production again in the future, they can use the exact same system to inspect a completely different product. The Inspekto S70 could soon reach the plants of other medical equipment manufacturer to support them during the pandemic and beyond.