Machines for 4.0 Baking
Eaton supported a customer in its challenge to automate and digitize its plants for the pasta and baking industry. Remote client and predictive maintenance benefits are among the most appreciated features
Since 1960, Turri F.lli has been designing and manufacturing machines for bakeries, pasta factories, pastry shops and pizza restaurants. The company has to meet very high quality requirements, addressing the challenges posed by today’s food industry. These include the need to support continuous production cycles, which nevertheless require variety and flexibility, even in extreme temperature conditions. Turri relied on Eaton to automate and digitalise its bakery equipment, enable remote control and management of the machines and reduce unwanted downtime. By implementing Eaton’s technologies and intelligent automation, it was able to offer its customers complete, customised solutions, characterised by high performances and flexibility.
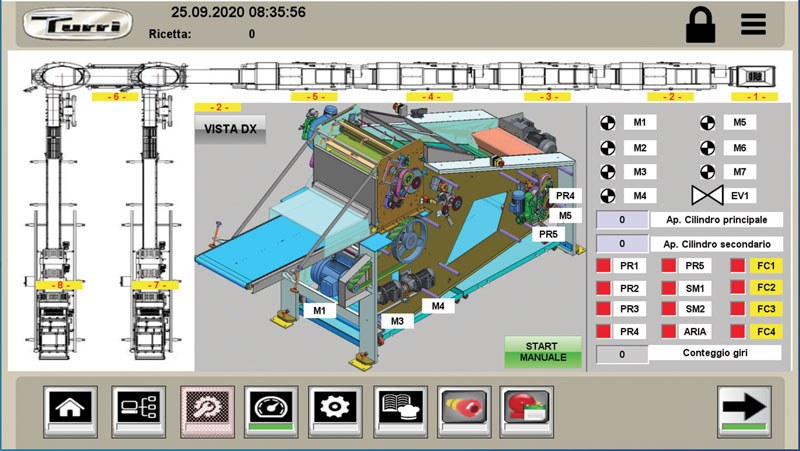
The need for remote control and planning of the production cycle
Specifically, in the past Turri supplied a customer with a line for the production and processing of large quantities of dough, designing complex, multi-cylinder machines capable of working in succession. Last year, it accepted a further challenge from its customer: to automate the rolling cylinders, that is, those machines for the production of sandwich dough that make its texture more uniform.
To ensure the optimisation and flexibility of the 24-hour production cycle, the company had to offer intelligent machines which would not only allow managing production according to the recipe sent, taking into account the quantity and type of dough to be supplied, but also enable remote control and planning of the production cycle. Besides, the solution had to be competitive, but at the same time easy to install and use.
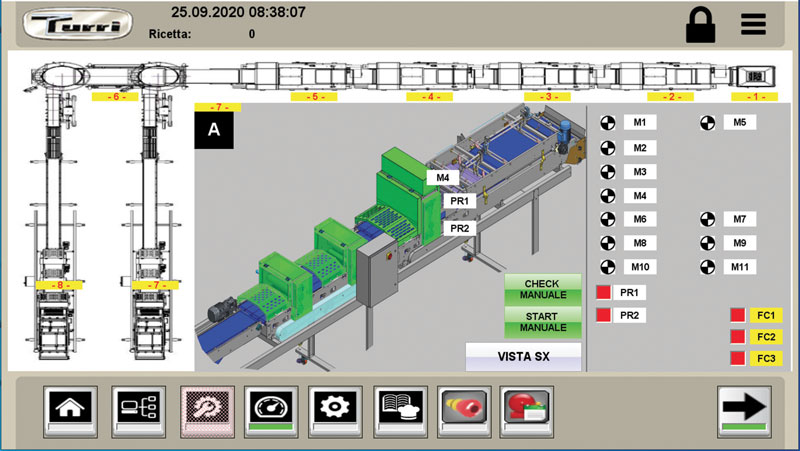
4.0 automation and flexibility
Eaton found the right solution to integrate new levels of a 4.0 automation and flexibility on the machines, able to optimise production and support every phase of the process. From implementation to software management and service, even thanks to collaboration with a specialist system integrator, Turri was able to have a single counterpart for the entire project. Eaton therefore proposed to implement a system which sends the production batch and the recipe to be processed to the Eaton XV300 PLC. Based on the recipe acquired, the PLC sets the various parameters of the production line including: hopper emptying speed, die thickness, number of passages, roller rotation speed and conveyor belt speed. Finally, the process is optimised by the advanced graphics of the XV300 HMI PLC, which allows operations to be loaded quickly, even when detailed pages are involved.
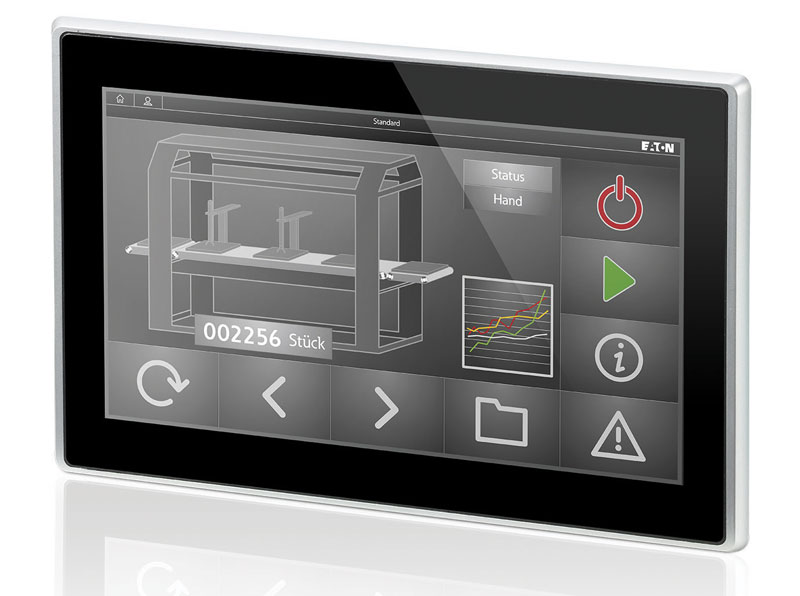
The remote client allows immediate identification of problems
In the production line, the machine’s motors are controlled by 60 Eaton DE11 type inverters connected via Canbus which, together with the PLC, allow full control of thermal protection, number of working hours, power consumption, speed and consumption of each individual motor.
Thanks to the easy connectivity of the Eaton XV300 PLC, the company’s IT system can access all the operating parameters, and integrate the rolling and moulding line into the overall production management automation, thus applying the concepts of Industry 4.0.
“Among the features which made the difference, and which Eaton offers as an integral part of the offer, is the remote client with a state-of-the-art human-machine interface, thanks to which we have a duplicate of the panel working on the machine in the company. In this way, we can immediately identify problems and intervene promptly,” Andrea Saggioro, CEO of Turri, said.
The benefit of predictive maintenance
Eaton’s solution provided Turri with effective support in its digital transformation journey. Besides the advantage of offering the customer a turnkey solution completely managed at every stage, the predictive maintenance enabled by Eaton’s XV300 provided added value. In the event of a problem, the central system software receives alerts which indicate the fault accurately, and the maintainer can act on the production line at the exact point where the problem occurs. Furthermore, the data obtained from the machines were essential for the analysis of consumption: for each batch it was possible to calculate the energy costs precisely.