Safety In Collaborative Robots
The issue of security in collaborative robotics is very complex. Thanks to the 17 native safety, UR cobots are intrinsically safe and they guarantee the safety of the operator in all conditions, affecting many aspects
Compared to the traditional robotic offer, cobots have immediately distinguished themselves for some substantial differences since their entry into the field of automation. The intrinsic safety level of cobots has demonstrated the possibility of a robotics capable of being implemented quickly, with contained tooling costs, in saturated layouts and without the need to segregate portions of space to be allocated to the robot’s operation, separate from that of man. In essence, a new way of producing and automating has been created for companies. The cobots of Universal Robots, specialized in the collaborative automation sector, were born in 2005with the first prototype, a UR5. Since then, the range increased with new proposals till the UR16e in 2019.
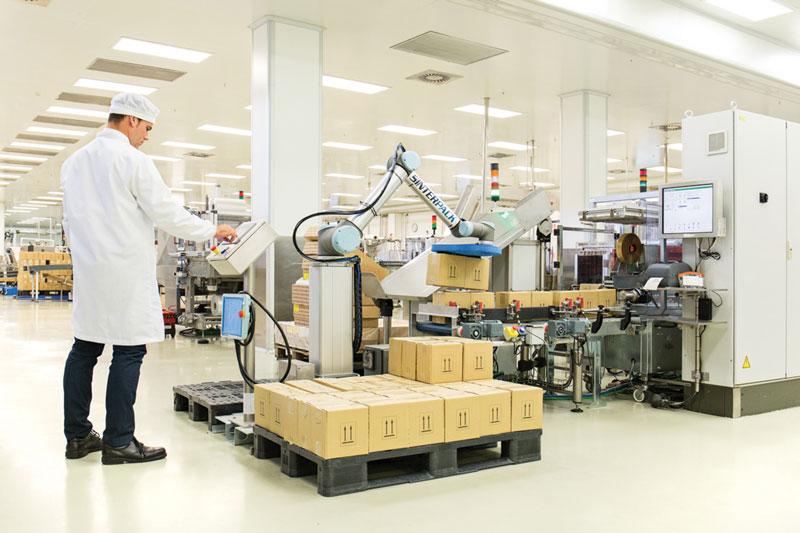
To assess the risks of the individual application
Cobots were born mainly in response to a need for flexibility to automate simple operations and productions with high variability. The problem of security immediately arose: being tools with a rapid deployment, they also had to guarantee the possibility of being applied in any operating condition, even without protective cages. Cobots are defined as “quasi-machines” because they are non-specific automations, capable of carrying out dozens of different applications. The combination with an end effector allows the automation of specific tasks. UR cobots are intrinsically safe because, by virtue of the 17 native safety, they are able to guarantee the safety of the operator in all conditions. What must be conducted – according to current legislation – is instead the analysis of the risk and the safety of the application. A cobot will always be safe, but if, for example, in the execution of the task it should handle sharp or pointed tools, then it is necessary to verify that the application as a whole is safe for the operator. This is therefore a first specific fundamental to keep in mind: to assess the risks of the individual application.
What are the safety standards?
The issue of security is extremely complex. The standards are basically of three types, with the addition of a technical specification that has no mandatory value, but acts as a guideline. Type A standards such as ISO 12100 are in force, which generally concerns risk analysis, and type B standards such as ISO 13849-1, which details the behavior of the individual parts of the application. Finally, the type C standards that specifically concern robots and give indications to manufacturers (ISO 10218-1) and integrators (ISO 10218-2). Then there is the ISO/TS 15066 which is a technical specification that provides some indications on parameters such as force and pressure. There are no fixed parameters that define an application safe: even at low speed and with a reduced degree of force, handling a sharp object can be dangerous. The cases must be evaluated one by one by conducting the analysis not so much on the cobot, which is intrinsically safe, nor on the cell, but on the robotic application as a whole.
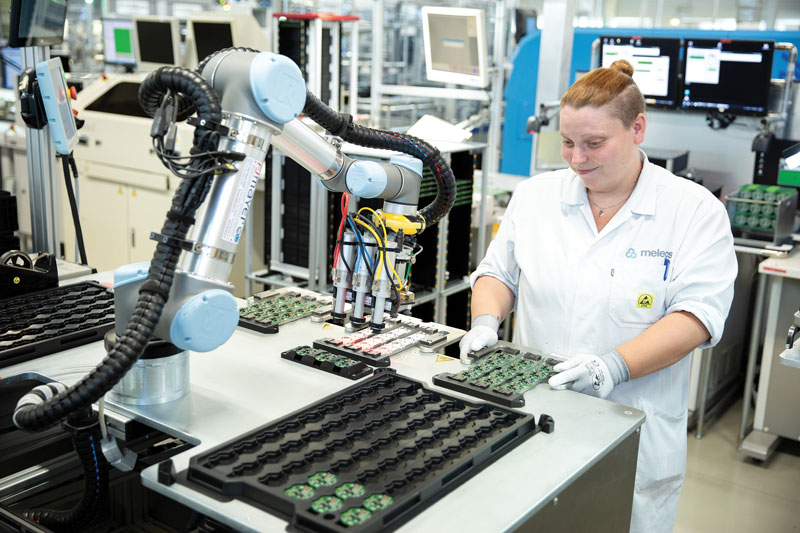
Collaborative in a native way
The safety functions natively integrated on the UR cobots are all designed according to UNI EN ISO 10218-1, and in compliance with the indications of TS 15066. They also make use of TUV certification (which makes UR cobots applicable for example in cleanrooms) and have the characteristic of be redundant, i.e. they always require the presence of at least two programmable electronic systems communicating with each other in the same control unit. This is the field in which UR has developed its expertise the most. Due to the very high level of guaranteed safety, 80% of UR cobots operate without protective fences around them, after a risk analysis. A good collaborative robot must offer the user the ability to affect many and different safety parameters to make the risk for the operator null and void. UR cobots offer no less than 17 PLD safety functions in category 3, which means that there is a double check on each function and that in the event of one control malfunction, the second takes over. The safeties go to adjust speed, force, angular momentum, possibility of movement of the single degrees of freedom of the cobot. But they don’t just do that.
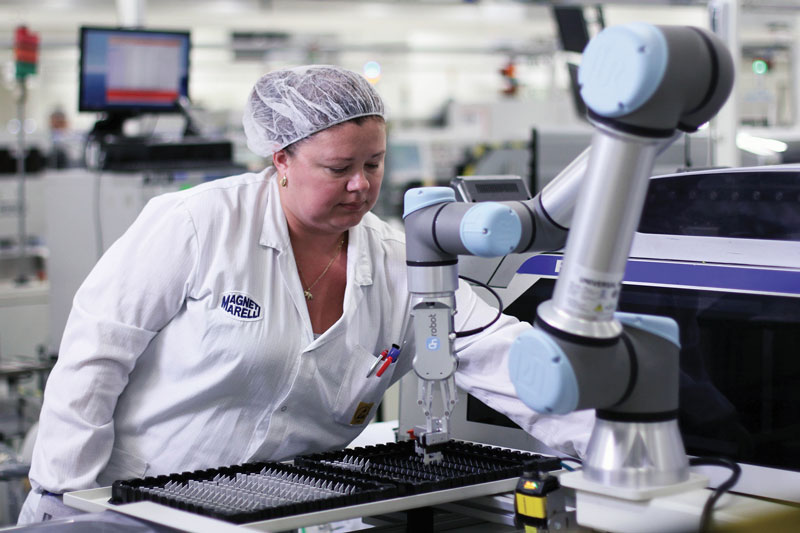
The concept of safety
For Universal Robots the concept of safety has always been associated with that of collaboration, understood as simplicity of programming, flexibility, ease and speed of use and reuse. Native safety also affects these aspects. For example, it is possible to create a shared work area in which the movement of the cobot occurs at “reduced” parameters (reduced mode: an even more collaborative and shock-sensitive behavior) or even areas in which the cobot is prohibited from working (restricted areas). It is sufficient to set a virtual vertical plane in the programming (there are up to 8 configurable virtual plans). As the virtual plane approaches, the cobot slows down until it stops and will never go beyond it, if it is programmed as impassable. In this way, you can make the employee and the robot work side by side while keeping the layout open. This cuts down on tooling costs and downtime. Or it is possible to increase the degree of “sensitivity” of the cobot when it enters the area shared with the operator: speed and power will decrease. The safety devices must therefore be interpreted not only as a way to make the robot safe, but also to make the application more flexible and accessible and its development simpler and faster. Moreover, cobots are not only safe tools (intrinsically) but also able to increase the safety of the working environment precisely, because they improve the ergonomic conditions of the same. Cobots perform best when applied in so-called DDD (dull, dirty, dangerous) tasks. For example, palletizing.