Funzioni per una semplice messa in servizio
Il controllo numerico Z32 dell’azienda fiorentina D.Electron è dotato di una serie di strumenti per la semplice messa in servizio e tuning avanzato di una macchina.
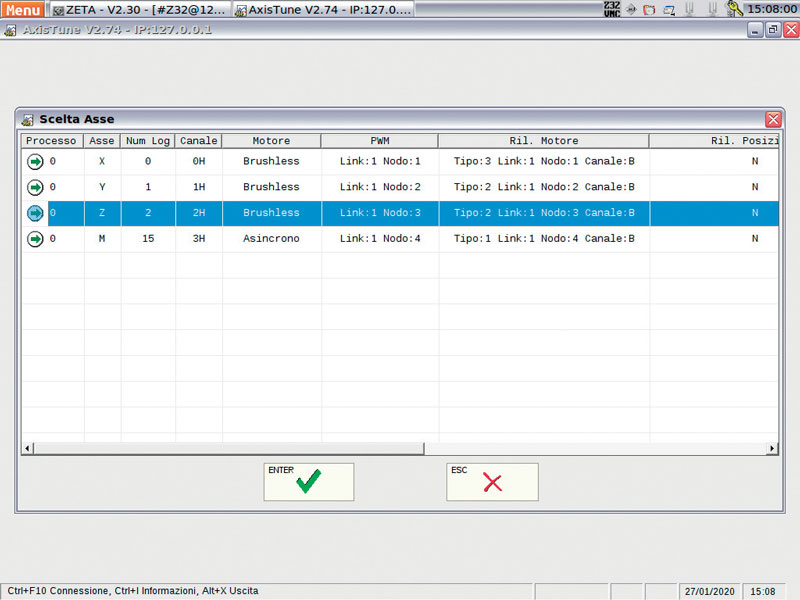
Il sistema di controllo Z32 della D.Electron può essere configurato in vari modi fra loro differenti in funzione delle esigenze di equipaggiamento della macchina che si dovrà realizzare. Tutte le configurazioni orbitano però intorno ad una unità centrale che contiene il sistema operativo FlorenZ ed il software vero e proprio del controllo numerico. L’unità centrale è collegata ad una Master Link che ha la funzione di instradare i pacchetti d’informazioni dalle periferiche e gli azionamenti verso il controllo numerico e viceversa.
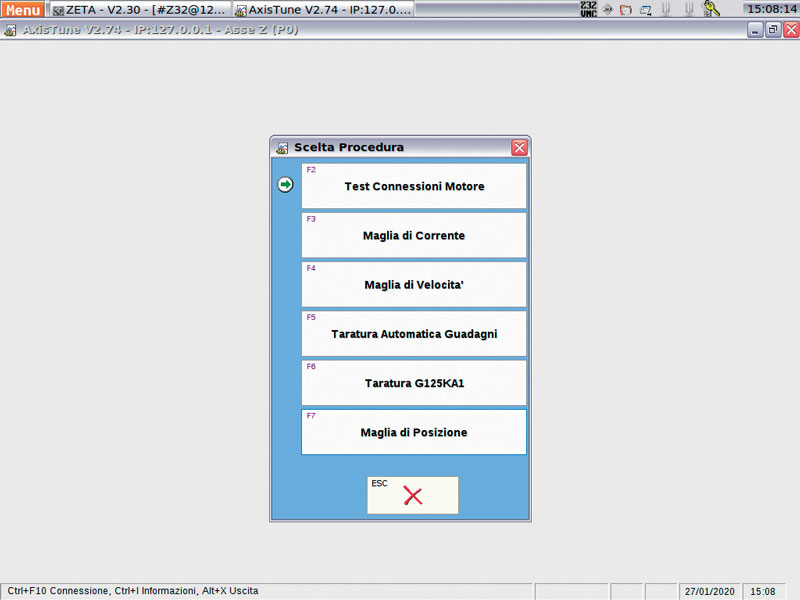
L’unità centrale è fornita col sistema operativo FlorenZ già installato così come il software del controllo numerico Z32. Viene preinstallata anche la suite software Z32 for Windows che contiene: Zeta, l’interfaccia operatore del CNC; ZFlash, il tool di programmazione a bordo macchina; Z32Info, che serve ad eseguire il backup completo e il ripristino dei dati del sistema. La suite contiene anche il software per la teleassistenza e tutta una serie di strumenti per configurare il sistema e metterlo in servizio. Rimarchiamo tra i molti: TARAT, il configuratore dell’architettura di sistema; MLEdit, l’editor e il compilatore della logica PLC della macchina; MLDeb, il potente debugger della logica PLC e che permette di leggere tutte le variabili di logica e di sistema; MLScope,
un oscilloscopio in tempo reale ed AXISTune per la messa in servizio e taratura degli assi macchina.
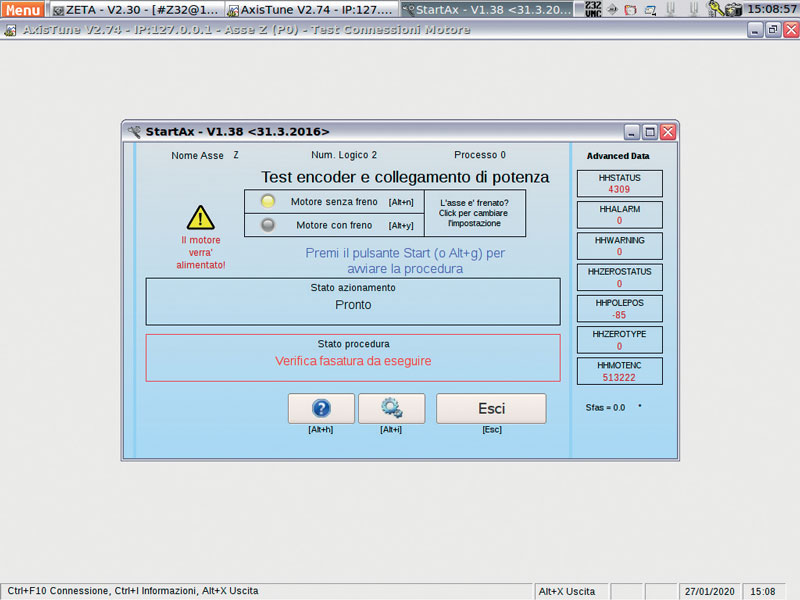
Taratura degli assi: cose complicate fatte in modo semplice e veloce
Lo strumento AXISTune permette di controllare il corretto cablaggio dell’hardware e dei servomotori asse della macchina nonché di eseguirne la messa a punto. I parametri che definiscono elettricamente i servomotori ed i relativi trasduttori di posizione sono preinstallati all’interno del configuratore TARAT e organizzati in liste; il tecnico addetto alla messa in servizio non deve far altro che selezionare il tipo di motore installato sull’asse che sta attivando e seguire la procedura guidata per la definizione dei parametri della cinematica. Successivamente procede alla messa in servizio degli assi usando AXISTune. Tutte le operazioni possono essere eseguite in modalità automatica, anche concatenate una all’altra, oppure in modalità manuale. In modalità manuale sarà il tecnico che, in base alla propria esperienza, sceglierà i parametri ottimali dei guadagni dei loop di controllo dell’asse non escludendo la possibilità di utilizzare come parametri di partenza quelli, già assai buoni, calcolati automaticamente dal controllo numerico. Tutti gli strumenti contenuti
in AXISTune racchiudono la pluriennale esperienza di D.Electron e permettono al costruttore della macchina di semplificare le procedure di messa in servizio tanto che, in condizioni normali di utilizzo, la taratura di un asse non richiede più di 15 minuti di tempo. Di seguito parleremo dei capisaldi principali della procedura.
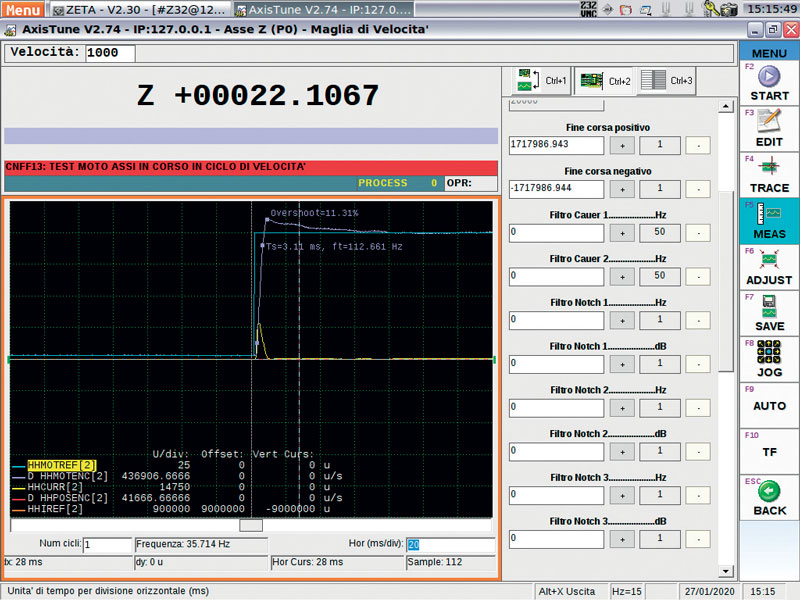
Test delle connessioni motore
Alla prima messa in servizio si procede col controllo della bontà delle connessioni elettriche di potenza e di segnale tra il servomotore e il sistema di controllo. Selezionando il comando dedicato alla funzione si apre la finestra StartAx che, oltre ad eseguire automaticamente tutti i test di connessione, esegue anche la verifica dell’angolo di fase del trasduttore di posizione del servomotore asse. Se del caso, l’angolo di fase rilevato può essere trascritto nella lista dei parametri che qualificano il motore asse.
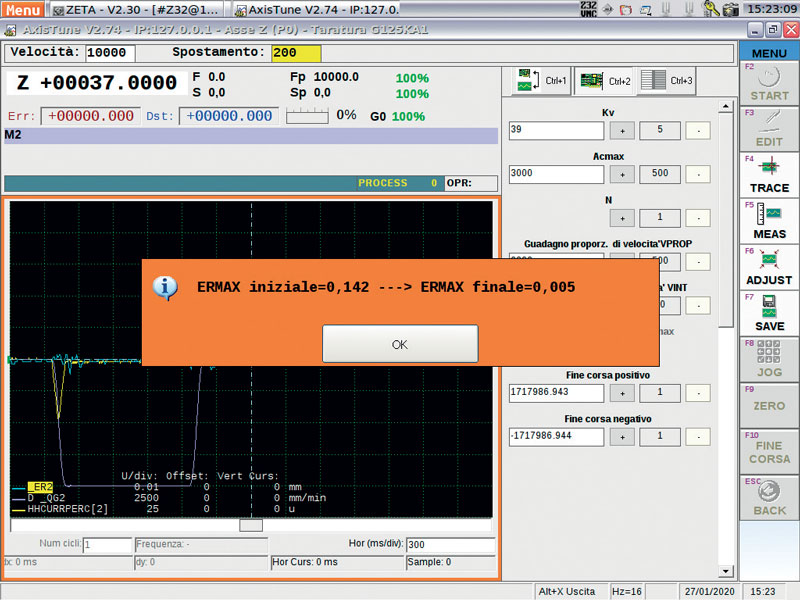
Taratura della maglia di corrente
Eseguite le necessarie verifiche di connessione, il tecnico può iniziare la messa a punto dell’asse vera e propria. Il primo passo è quello di definire i valori dei parametri della maglia di corrente e, per eseguire i calcoli necessari, in ingresso alla maglia AXISTune applica un riferimento di corrente con forma d’onda a gradino la cui ampiezza è pari al 30% della corrente massima. Il servomotore esegue piccolissimi movimenti e iterativamente viene calcolata la migliore risposta. La procedura può essere eseguita sia manualmente sia in modo automatico. La procedura automatica, come detto, è iterativa e, in genere, restituisce valori dei guadagni già buoni per la movimentazione dell’asse in manuale. I valori dei guadagni della maglia di corrente sono subito visibili, attivi ed acquisiti come taratura dell’asse, non occorre quindi perdere tempo per salvare dati, elaborarli con altri strumenti di calcolo e ricopiare manualmente i risultati in altri campi o pagine.
A verifica di quanto è stato calcolato, il tecnico può subito visualizzare la forma d’onda della risposta in corrente applicando un riferimento pari a quello applicato in modalità automatica visualizzando così graficamente la forma d’onda della risposta.
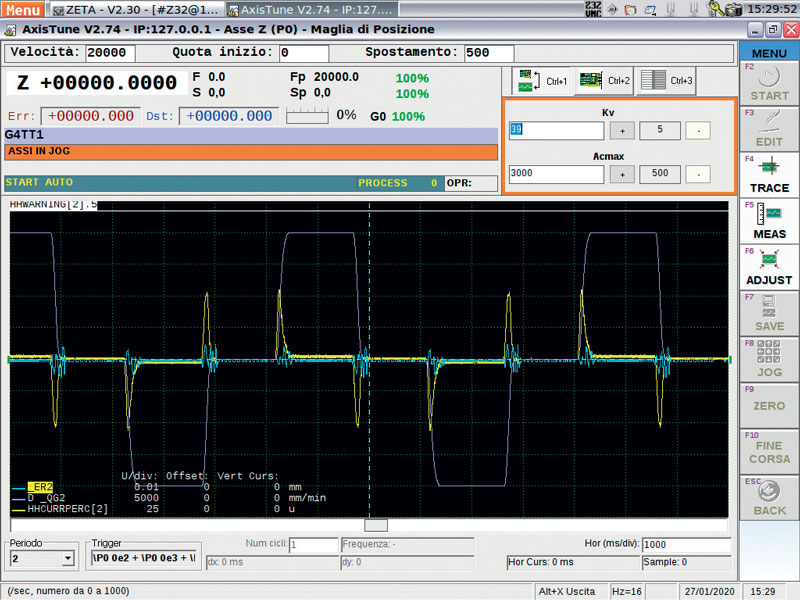
Taratura della maglia di velocità
Definiti i parametri della maglia di corrente, il tecnico passa alla taratura della maglia di velocità. Anche in questo caso viene applicato un riferimento di velocità la cui forma d’onda è di tipo a gradino. I movimenti del motore sono un po’ più ampi rispetto a quelli fatti per la maglia di corrente ed AXISTune se ne serve per rilevare l’inerzia meccanica dell’asse vista dal motore.
Anche in questo caso il tecnico può visualizzare graficamente i risultati dell’analisi eseguita applicando manualmente un riferimento di velocità identico a quello usato dalla procedura automatica e, come per la taratura dei guadagni della maglia di corrente, ha a disposizione tutti gli strumenti per eseguire l’analisi alle velocità più congeniali, lungo il tratto dell’asse più appropriato e per eseguire, se lo desidera, l’affinamento di alcuni parametri che sono sempre e comunque editabili. Nel caso in cui siano presenti risonanze del sistema meccanico, è possibile intervenire applicando opportuni filtri in corrispondenza delle frequenze caratteristiche.
Taratura G125 per l’alta velocità
Occorre premettere che i tools per la gestione dell’alta velocità a disposizione nel controllo numerico Z32 sono tanti e versatili al punto che D.Electron ha loro dedicato un intero manuale di riferimento. Alcune funzioni sono utilizzate per la messa a punto degli assi macchina e, nella fattispecie, definiti i valori dei parametri caratteristici della maglia di corrente e di quella di velocità si applica un ciclo di taratura e test denominato G125. Si tratta di una procedura automatica di tuning eseguita sfruttando uno degli strumenti per la gestione dell’alta velocità che sono a disposizione sia del tecnico installatore sia del programmatore dei cicli di lavoro.
La G125 muove l’asse ad una velocità e per una corsa definiti dal tecnico e serve a ridurre, anche drasticamente, gli errori d’inseguimento della risposta dell’asse individuando le migliori condizioni di moto ed introducendo in modo automatico le correzioni dei parametri necessarie all’ottimizzazione della dinamica del sistema.
Il test G125 è particolarmente potente, la semplicità d’uso è quasi disarmante e, poiché può essere utilizzato anche all’interno di un part program, permette all’utente finale della macchina di aver sempre le migliori prestazioni nelle zone più critiche dell’area di lavoro. L’efficacia dell’uso della funzione G125 “on demand” è particolarmente utile se la macchina ha condizioni dinamiche che possono cambiare in virtù della configurazione di lavoro oppure della posizione assunta dagli assi (caso tipico la mutevole massa del pezzo in lavorazione se piazzato su una tavola mobile). Il test G125 alla fine del ciclo presenta l’errore iniziale rilevato sul sistema, prima di applicare le compensazioni, e poi l’errore finale; può essere eseguito più volte fino ad avere l’errore più piccolo.
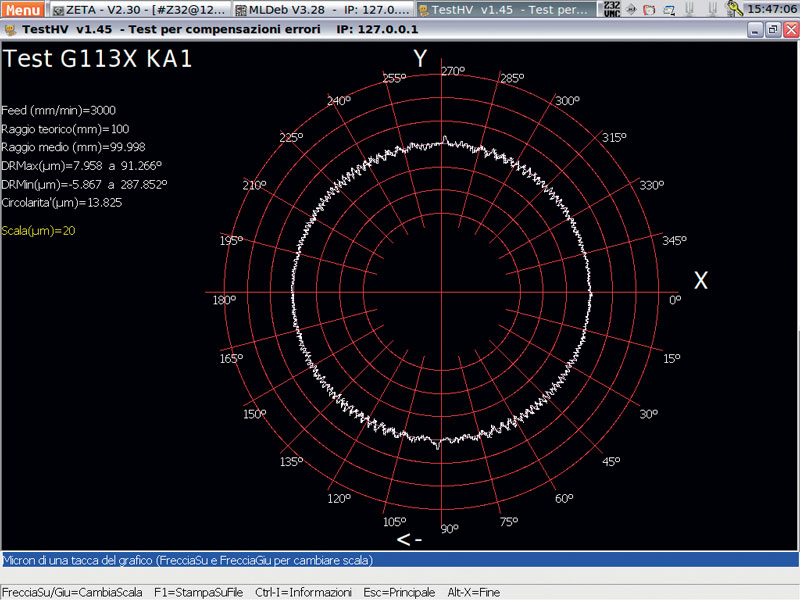
Test finale della maglia di posizione
Il test finale denominato di Maglia di Posizione viene eseguito su tutta la corsa dell’asse che si sta mettendo in servizio. Il test può essere eseguito ciclicamente e ha lo scopo di verificare che su tutta la corsa degli assi della macchina gli errori si inseguimento siano bassi ed uniformi e vi sia uniformità delle grandezze elettriche che entrano in gioco durante la movimentazione.
Analizzando i dati elettrici rilevati, questo test ha lo scopo di individuare possibili impuntamenti di natura meccanica o non uniformità permettendo così ai tecnici di porvi rimedio.
Test di geometria
Si tratta di un test del cerchio per individuare gli errori geometrici all’inversione dell’asse. Anche questo è uno degli strumenti della gestione dell’alta velocità, si chiama Test G113X KA1 ed è assimilabile ad una sorta di test di ballbar. Nella pagina di configurazione si definiscono il nome degli assi interessati al test, la Feed di movimento ed il diametro del cerchio da eseguire. Il centro del cerchio è definito dalla posizione della macchina in quel momento. Il tecnico ha la possibilità di misurare gli errori d’inversione e di impostare le eventuali compensazioni in velocità e tempo all’inversione dell’asse sia in direzione positiva sia negativa. Eseguendo nuovamente il test del cerchio è possibile verificare la bontà delle compensazioni apportate.
Analisi della regolarità di moto di un motore
Finora abbiamo fatto un rapido excursus sulle funzioni disponibili per la messa a punto dei sistemi di controllo degli assi a disposizione dei tecnici installatori, della loro efficacia e di come aiutino a risolvere problemi, anche complessi, impiegando poco tempo. Per avere un’idea della complessità dei sistemi che a volte è necessario mettere in servizio basti pensare alla gestione di un asse gantry dove ognuno dei due assi è movimentato da due servomotori che agiscono col loro pignone in antigioco meccanico uno con l’altro.
I tools di tuning permettono di portare la precisione di inseguimento della traiettoria a livelli micrometrici, ma in certe occasioni ciò potrebbe non essere sufficiente. Esiste tutto il mondo delle lavorazioni in alta velocità ed altissima finitura dove anche un micrometro d’errore può far la differenza. A tale scopo D.Electron ha sviluppato degli strumenti che, dopo aver consentito il tuning dell’asse, permettono l’esecuzione dell’analisi di regolarità del movimento del motore e quindi dell’asse stesso.
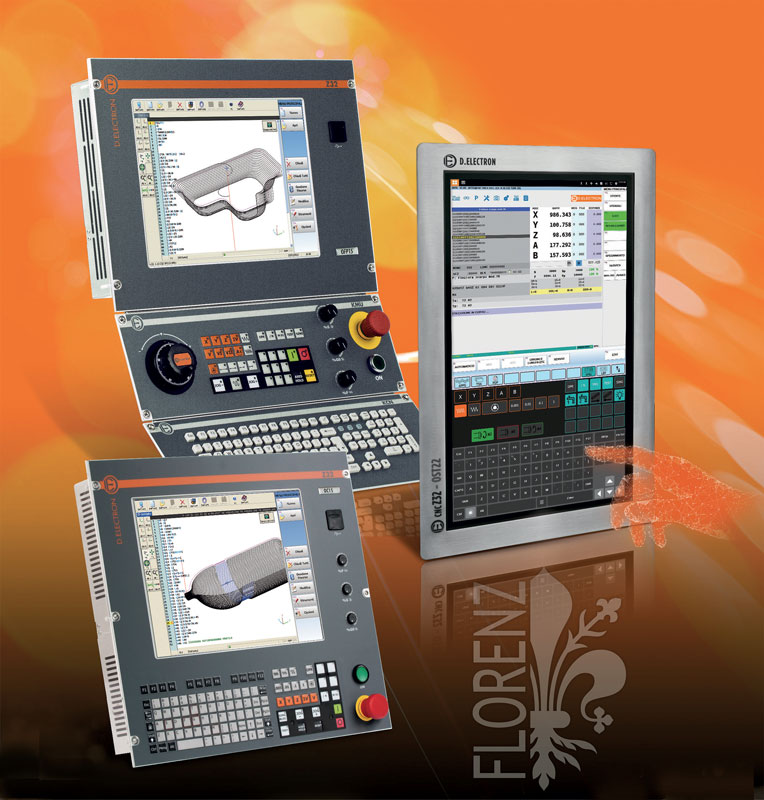
Per eseguire l’analisi si applica un riferimento di velocità all’asse gestito in anello di retroazione aperto ed ogni due millisecondi la velocità dell’asse viene campionata; il controllo numerico esegue un’analisi in frequenza dei campioni rilevati ricercando gli overshoot dei valori dinamici del motore.
I risultati dell’analisi sono presentati al tecnico in forma grafica affinché possa eseguire le misurazioni e le valutazioni del caso. In genere valori a basse frequenze oppure a frequenze molto elevate difficilmente sono presi in considerazione poiché non incidono sulla qualità finale della lavorazione, ma vi sono frequenze dove invece le perturbazioni della regolarità di moto possono produrre delle piccole ombreggiature sul pezzo.
A fronte dell’analisi si apre un bivio poiché la non regolarità può dipendere dalla qualità costruttiva del motore stesso oppure dalla meccanica. Lo strumento può eseguire l’analisi indifferentemente sia sul motore scollegato dalla meccanica della macchina sia quando vi è collegato permettendo così l’individuazione dell’origine dell’irregolarità.
Costruttori di macchine particolarmente raffinate includono l’analisi della regolarità di moto tra i test che qualificano i loro prodotti prima di consegnarli al cliente finale, così come includono questo test tra le prove da eseguire alla fine degli interventi di assistenza.
Se le irregolarità di moto sono concentrate in particolari frequenze il controllo numerico Z32 è in grado di compensarle utilizzando opportuni parametri degli azionamenti. In genere non serve arrivare all’utilizzo di questi strumenti estremi in quanto già la scelta di un motore di buone qualità dinamiche e la possibilità del controllo D.Electron di poter lavorare con guadagni di anello elevati riducono al minimo i problemi.
Motori mandrino sincroni deflussati
Con i medesimi strumenti software visti finora D.Electron rende possibile definire al meglio il sistema di controllo più appropriato per qualsiasi tipo di motore sincrono oppure asincrono. Di particolare interesse sono i motori sincroni a magneti permanenti, il cui pilotaggio è vettoriale come per tutti i motori brushless, permettendo di avere sempre chiaro e controllabile il livello della corrente di coppia e quella di magnetizzazione. A bassi giri e fino alla velocità di base, dove la corrente di magnetizzazione è pressoché nulla, tali motori seguono il medesimo iter di taratura dei motori brushless.
La tecnologia D.Electron riesce però a far sì che gli azionamenti della serie Z-Star EVO oppure della serie Slim possano erogare una ben determinata quantità di corrente di deflussaggio magnetico. In questo modo, a discapito della coppia disponibile e della temperatura del motore, si riescono a raggiungere giri di rotazione molto elevati. È chiaro che stiamo parlando di tecnologia sofisticatissima dove non è pensabile di eseguire la taratura e messa in servizio con procedure automatizzate, in questi casi la tecnologia va accompagnata una profonda conoscenza dei principi fisici che intervengono ed altrettanta esperienza sul campo. D.Electron è in grado di erogare il servizio di messa a punto di tal tipo di motori ai costruttori di macchine intervenendo direttamente sul campo e, come sempre, è disponibile a formare i tecnici che il cliente volesse dedicare a tal tipo di attività.