La produzione di elettrodi in grafite viene perfezionata
Vetimec Soc Coop. di Calderara di Reno (BO) realizza stampi, anche per lo stampaggio a iniezione, per l’industria automobilistica internazionale e le fonderie. Poiché la produzione avviene principalmente mediante elettroerosione a tuffo, l’efficienza dipende dalla produzione degli elettrodi in grafite. Grazie al passaggio alle frese speciali di Hufschmied, oggi presso Vetimec la lavorazione della grafite è il 30% più veloce e il 20% più economica.
Il gruppo Vetimec, fondato nel 1962, gode di ottima fama nell’industria automobilistica grazie alla propria attività di produzione di stampi. Per la realizzazione di componenti meccanici e strutturali, Vetimec progetta, sviluppa e realizza stampi complessi e di grandi dimensioni per pressofusione, fusione a bassa pressione e fusione in conchiglia nonché casse di anima per l’impiego nell’industria automobilistica. Con gli stampi Vetimec vengono prodotti componenti strutturali e del motore in leghe di alluminio e magnesio. Per la fabbricazione di stampi per lo stampaggio a iniezione l’azienda bolognese punta sulla produzione in proprio degli utensili, per una maggiore efficienza dei processi. A tal fine Vetimec, in collaborazione con i partner Exeron e PCam, ha installato una cella di produzione costituita di due centri di fresatura CNC a 5 assi Exeron HSC600/5, quattro impianti per elettroerosione a tuffo Exeron EDM316 e una macchina di misura a coordinate dell’azienda Zeiss con un sistema di gestione di PCam. L’obiettivo di Vetimec con questa cella è la produzione completamente automatica e senza operatore di elettrodi in grafite, la loro misurazione tramite robot e la successiva elettroerosione. Per superare le sfide che ciò ha comportato, Exeron GmbH si è rivelata un partner importante, che ha messo a disposizione il proprio showroom per svolgere test di realizzazione automatizzata degli elettrodi, e ha offerto, inoltre, un interessante consiglio.

La sicurezza del processo dipende dall’utensile
“Per produrre di notte senza operatore, il processo deve essere affidabile ed esente da manutenzione. Un aspetto in particolare ci preoccupava: in precedenza non avevamo utensili di fresatura con una durata d’esercizio tale da poter essere lasciati in funzione l’intera notte in sicurezza senza supervisori”, spiega Massimo Lolli, Operations Manager presso Vetimec. “Exeron ci ha fatto conoscere il produttore di utensili speciali Hufschmied, di cui volevamo testare la serie Graftor®”. Ecco, quindi, che è entrata in gioco Hufschmied Zerspanungssysteme GmbH, specializzata in particolare in utensili per materiali di difficile lavorazione: compositi di vetro e fibre di carbonio, plastiche, ceramiche, acciai temprati fino a 72 HRC nonché grafite. “Per ottimizzare i processi di fresatura è sempre necessario considerare la situazione nel suo complesso: materiale, macchina, utensile, strategia di lavorazione e requisiti di qualità impostati. Abbiamo fornito consulenza a Vetimec e programmato delle strategie di fresatura con i parametri di processo esistenti, affinché l’azienda ottenesse risultati significativi dai test di fresatura”, afferma Stefano Barbagallo, Sales Director Europe presso Hufschmied Zerspanungssysteme.
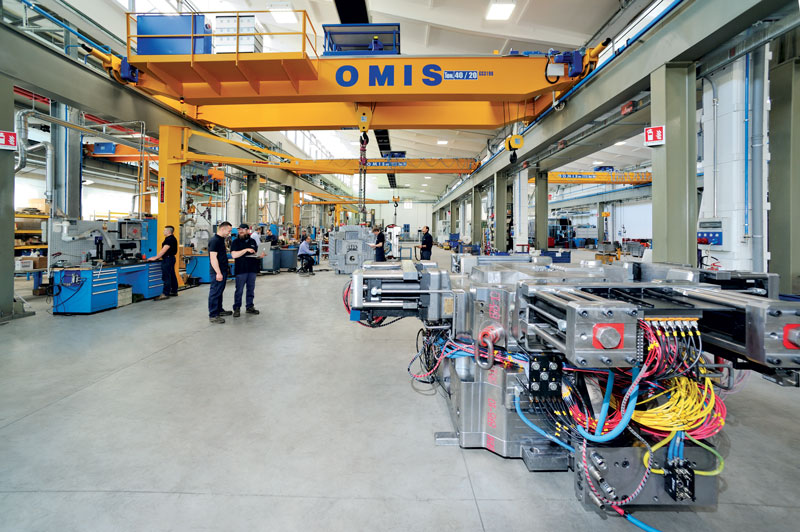
Test approfonditi
“Con i nostri test di fresatura abbiamo raffrontato le durate d’esercizio e i risultati di fresatura, nonché valutato i costi degli utensili, il numero di varianti di utensili necessarie e il relativo lavoro di programmazione”, sottolinea Lolli. “Il risultato: la strategia Graftor® di Hufschmied offre vantaggi evidenti sotto ogni punto di vista sia in termini di economicità sia in termini di sicurezza del processo. Lavoriamo con un funzionamento completamente automatizzato 24/7, garantendo le tolleranze di produzione richieste di ±0,010 mm mediante processi sicuri”. Vetimec ha aggiunto un test a lungo termine, e sei mesi dopo il primo incontro è stato concordato un contratto quadro annuale. Per la lavorazione della grafite si è deciso di passare completamente alla serie Graftor®. Con la serie Graftor®, disponibile con diametro da 0,5 a 12 mm, la sgrossatura e la finitura sono integrate in una singola operazione di fresatura. “La geometria a quattro taglienti brevettata offre una netta riduzione della forza di taglio grazie rispettivamente a due taglienti di sgrossatura e due di finitura contrapposti, posizionati in modo da spingere verso il basso e rimuovere il materiale”, spiega Barbagallo. “Un vantaggio decisivo è la possibilità di realizzare elevate qualità superficiali con avanzamenti elevati. È possibile la finitura dell’intero materiale residuo sfruttando l’intera lunghezza del tagliente”.

L’utensile Graftor® supporta profondità di taglio assiale (ap) fino a 3xD con una profondità di taglio radiale fino a 0,65xD (ae), consentendo così livelli di finitura significativamente maggiori. Per realizzare il contorno finale servono, quindi, meno fasi di lavorazione e meno utensili di diverse dimensioni. La ridotta pressione di taglio consente di produrre contorni complessi, ad esempio perni conici con un diametro di 0,080 mm. Le frese per grafite, molto precise dal punto di vista geometrico (±0,005 mm), si distinguono per un rivestimento diamantato nanocristallino (DIP®) sviluppato e brevettato da Hufschmied per la massima resistenza all’abrasione. Con questo utensile brevettato, l’azienda tedesca ha superato le sfide particolari poste dal materiale: la grafite in realtà non può essere truciolata nel vero senso del termine, in quanto il materiale non è deformabile plasticamente. La lavorazione non produce trucioli, bensì asporta granelli del composto. Si forma così la poco amata polvere di grafite, che ha un effetto altamente abrasivo sui taglienti dell’utensile. Poiché le strutture in grafite complesse degli elettrodi si scheggiano facilmente, la geometria dell’utensile di fresatura ottimizzata per il materiale non solo deve garantire una rimozione ottimale del materiale asportato, bensì eliminare le oscillazioni durante il processo di lavorazione e ridurre le forze.
Il funzionamento 24/7 senza operatore è consentito dai due centri di fresatura CNC a 5 assi Exeron HSC600/5, che integrando la cella di produzione PCam dispongono di un sistema automatico per il cambio degli elettrodi. ’utensile Graftor® supporta profondità di taglio assiale (ap) fino a 3xD con una profondità di taglio radiale fino a 0,65xD (ae) e riduce le fasi di lavorazione eliminando la prefinitura. Dalla bozza schematica all’utensile brevettato – il Graftor® di Hufschmied.
Riduzione dei tempi di inattività
Con gli utensili Graftor®, oggi la lavorazione della grafite presso Vetimec è il 30% più veloce. È interessante notare che il risparmio ottenuto è dovuto sia alle maggiori durate d’esercizio sia al fatto che gli utensili di sgrossatura e finitura sono molto più versatili. Di conseguenza sono necessari meno cambi del tipo di utensile. Il minor numero di utensili riduce a sua volta il lavoro per la programmazione NC e per le impostazioni preliminari degli utensili. Massimo Lolli afferma: “Gli utensili di Hufschmied hanno contribuito fortemente all’ottimizzazione dei nostri processi nell’ambito della produzione di elettrodi, che adesso è il 20% più economica. Ne beneficiano anche i clienti: infatti ora offriamo una fornitura ancora più rapida di stampi per lo stampaggio a iniezione altamente precisi”.