Maggior efficienza con il magazzino automatico SILO² di ICAM
Moretto Brakes Components, ai vertici nella produzione di dispositivi antirumore (Anti Noise Shim) per pastiglie freno di tutte le case automobilistiche, si è affidata a ICAM per la riorganizzazione del magazzino stampi nel suo stabilimento di Casarano (LE). Obiettivo: proteggere gli stampi, recuperare spazio prezioso a pavimento, tracciare tutte le operazioni di prelievo e deposito eseguite e migliorare l’ergonomia e la sicurezza durante le fasi di picking.
di Adriano Moroni in collaborazione con l’Ufficio Marketing & Comunicazione di ICAM
Se la qualità di ogni singolo componente concorre al valore del prodotto finale, nell’industria automobilistica, dove i prodotti devono rispondere ai massimi requisiti di qualità, sicurezza e affidabilità, questo concetto assume un significato particolarmente importante. Alti standard qualitativi richiedono una selezione accurata dei materiali, rigorosi controlli dei processi produttivi e massima efficienza produttiva. Ed è su questi principi che ha incentrato la propria strategia, Moretto Brakes Components, azienda italiana, con sede a Casarano, in provincia di Lecce, specializzata nella produzione di dispositivi antirumore per le pastiglie freno (Anti Noise Shim) di tutte le case automobilistiche. Fondata nel 1999 dalla famiglia Moretto, l’azienda alle origini era specializzata nella progettazione e realizzazione di stampi tecnici per il settore calzaturiero e stampi per il settore automotive, nello specifico stampi per pastiglie freni auto e stampi per filtri auto. Negli anni, la crescita della domanda da parte del settore automotive, ha spinto l’azienda a stringere relazioni sempre più solide con i produttori di impianti frenanti per le auto. La sostituzione dell’amianto con i polimeri di acciaio ha aperto nuove opportunità. Per stare al passo con le esigenze dei clienti, nel 2005/2006, il core-business dell’azienda si diversifica con la produzione di dispositivi antirumore (Anti Noise Shim) per le pastiglie freno delle auto e, nel 2009, la produzione degli stampi viene dismessa.
Moretto Brakes Components è un partner di primissimo livello
Grazie all’utilizzo di materiali e tecnologie all’avanguardia, gli Anti Noise Shim di Moretto Brakes Components sono realizzati per offrire il più alto livello di sicurezza, performance e comfort al mercato OEM (Original Equipment Manufacturer) e Aftermarket, che oggi costituisce quello di riferimento per l’azienda. Questo approccio senza compromessi, principio ispiratore sin dalla nascita, ha reso Moretto Brakes Components un partner di primissimo livello. Oggi, l’azienda guidata da Marco Moretto e da suo padre Francesco, è tra i player di mercato di riferimento nei dispositivi antirumore e viene scelto dai più importanti costruttori di impianti frenanti a livello mondiale, alla ricerca di soluzioni sempre più sicure ed affidabili. Lo stabilimento è situato nell’area industriale di Casarano (LE), e occupa una superficie complessiva di circa 1.360 m2, di cui 165 m2 adibiti a magazzino e 800 m² ai processi produttivi. Realtà in forte espansione con un team di 12 dipendenti, Moretto Brakes Components ha chiuso il 2021 con oltre 3 milioni di euro di fatturato ed una capacità produttiva di 20 milioni di pezzi annui equivalenti a circa 80 mila pezzi giornalieri caratterizzati da una percentuale di errore pari allo 0,01%. Per il 2022, l’azienda stima di incrementare ulteriormente la capacità produttiva arrivando a produrre più di 21 milioni di pezzi e di aumentare la quota export che raggiungerà il 60% dell’intero fatturato. Moretto Brakes Components si distingue sul mercato per quattro peculiarità distintive: flessibilità nei volumi produttivi, tempi rapidi di consegna, qualità eccellente degli output prodotti e prezzi competitivi. A queste, va aggiunta la crescente sensibilità verso la tutela ambientale unitamente all’attenzione nel limitare il proprio impatto sul territorio che ha portato l’azienda a decidere di riciclare gli sfridi di lavorazione: da materiali di scarto diventano, infatti, risorsa preziosa per una fonderia locale che dona loro una seconda vita.
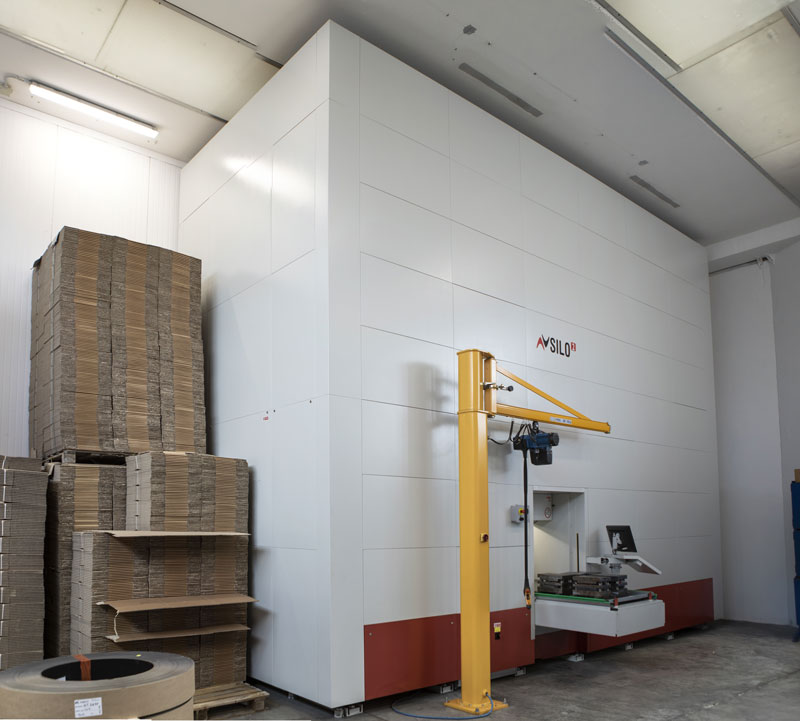

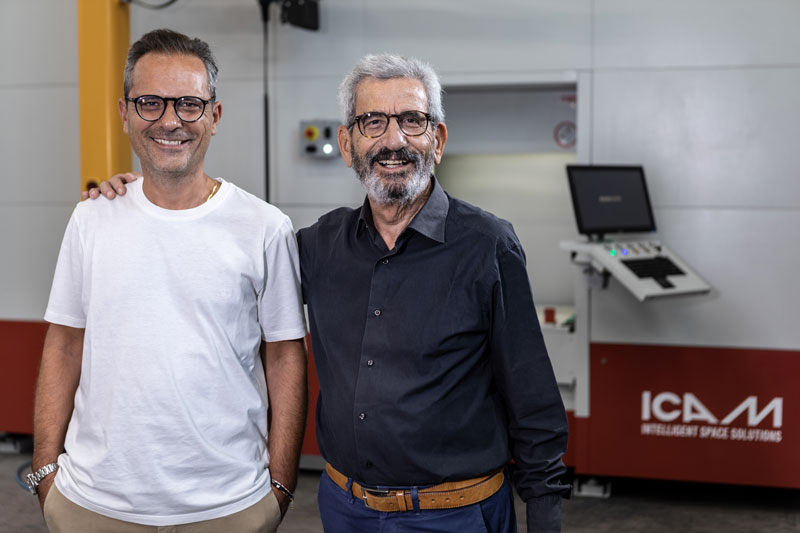

Shim antirumore: massima sicurezza e comfort di guida
Gli shim antirumore rappresentano elementi chiave di rilievo nella struttura dei freni: assicurano il massimo comfort di frenata evitando il contatto diretto tra la piastrina e il pistone, riducendo le vibrazioni e lo stridio che la frenata può generare. Per la qualità e il corretto funzionamento di questi dispositivi la scelta del materiale giusto è fondamentale. Va da sé che la sottoscrizione di accordi di partnership con fornitori qualificati è strategica per garantire gli elevati standard qualitativi richiesti dal mercato: il materiale deve, infatti, perentoriamente rispettare determinati requisiti tecnici come il mantenimento del rumore, della temperatura, ecc. e devono essere corredati di tutte le validazioni necessarie, report e certificati di qualità. La grande attenzione posta sugli aspetti di qualità, ha portato Moretto Brakes Components a creare un Ufficio Qualità interno dove un operatore monitora costantemente la produzione attraverso scrupolosi e regolari controlli effettuati con macchine di misura a coordinate, micrometri, tamponi e dime di controllo. I polimeri giungono in azienda sotto forma di coil per poi essere sottoposti al processo di tranciatura che consente di ottenere i diversi componenti con le sagomature desiderate. In stabilimento sono presenti 8 presse per tranciatura, più una di backup così da evitare fermi o rallentamenti produttivi in caso di malfunzionamenti, e ogni singolo componente, viene controllato da ciascun operatore prima di essere messo in spedizione. Con i clienti più importanti, Moretto Brakes Components lavora a SAL mediante la visibilità su loro piattaforme con pianificazione dell’ordine con un tempo medio di preavviso di 3-5 settimane prima dell’evasione. Gli ordini sono per lo più ripetitivi però, in base al cliente, lo stesso articolo può essere realizzato con materiale differente.
Le criticità logistiche risolte con il magazzino automatico verticale SILO² di ICAM
Gli stampi rappresentano il capitale più prezioso per Moretto Brakes Components perché sono loro a dare la forma ai dispositivi anti-rumore. Custodirli in maniera adeguata e sicura è fondamentale affinché le loro prestazioni restino eccellenti il più a lungo possibile. Inizialmente, venivano stoccati in armadietti metallici completamente chiusi per preservarli da agenti esterni come polvere e umidità, con la parte frontale realizzata in plexiglass trasparente così da consentire agli operatori di individuarli più velocemente. Nonostante questo escamotage, negli anni, a fronte dell’incremento del business e dell’ampliamento dei mercati e dei clienti da servire, il numero degli stampi da gestire stava crescendo enormemente e gli armadietti presenti non erano più sufficienti a contenere tutto. In aggiunta a ciò, la ricerca manuale degli articoli rallentava notevolmente le attività di presa e deposito stampi con inevitabili ripercussioni sui tempi di attrezzaggio presse e sull’ergonomia e sicurezza operativa dei diversi collaboratori. Per far fronte a queste criticità, l’azienda decide che è il momento di rimettere in discussione il sistema di gestione e stoccaggio stampi utilizzato fino ad allora e individuare una soluzione più in linea con l’evoluzione delle esigenze di business. Comincia così uno scouting di mercato per individuare un fornitore in grado di offrire una soluzione rispondente a questi requisiti. La scelta ricade sul magazzino automatico verticale SILO² di ICAM.
SILO² di ICAM è un magazzino verticale su misura per lo stoccaggio stampi
Alto 5,6 metri, il magazzino verticale SILO² assicura una capacità di stoccaggio di 33,84 m3 su una superficiedi soli 20,75 m2 a pavimento. La struttura modulare si compone di 6 colonne di stoccaggio e 1 baia di prelievo/deposito dotata di sistema automatico di estrazione vassoi, collocata nella terza colonna di stoccaggio, che consente agli operatori di ricevere e movimentare gli stampi in totale sicurezza e comfort senza alcun ingombro fisso a pavimento. Al suo interno sono stoccati oltre 500 stampi di tranciatura per presse meccaniche, organizzati in 188 vassoi di dimensioni pari a L 853 x P 802 x H 41 mm. Ciascun vassoio, progettato per un carico massimo pari a 400 kg e portata specifica pari a 556 kg/m², ospita 4 o 6 stampi di dimensioni pari a L 350 x P 350 x H 250 mm e peso di 100 kg cadauno. I vassoi, con altezza utile di carico di 250 mm, posizionati a passo 275 mm, assicurano lo stoccaggio sicuro ed efficiente di tutti gli articoli stoccati all’interno del magazzino SILO². In termini di produttività, il magazzino SILO² garantisce la movimentazione di 66 vassoi all’ora.
SILO²: i vantaggi di una soluzione su misura
Grazie al design modulare e alla disponibilità di vassoi piccoli con una portata specifica molto elevata (556 kg/m²), il magazzino verticale SILO² di ICAM è risultato la soluzione ottimale per rispondere alle esigenze di Moretto Brakes Components, in termini di capacità di stoccaggio, protezione degli stampi, tracciabilità delle operazioni eseguite e innalzamento degli standard operativi e di sicurezza per gli operatori. Rispetto alla precedente soluzione di stoccaggio, ovvero gli armadietti metallici che occupavano circa 300 m² a pavimento, oggi, tutti gli stampi sono custoditi in soli 20,75 m2 con un risparmio di superficie superiore al 90%. Gli operatori non sono più costretti a cercarli a vista ma è sufficiente che digitino sul PC a bordo macchina il codice dello stampo di cui hanno bisogno per riceverlo direttamente presso la baia di prelievo e deposito, ad altezza uomo. In più, l’integrazione in baia di una gru a bandiera con paranco elettrico a catena, rende le operazioni di prelievo e deposito stampi ancora più ergonomiche, veloci e sicure. La gestione informatizzata, inoltre, garantisce la completa tracciabilità di tutte le operazioni in/out eseguite e di tutti gli stampi stoccati. Ne è derivato un notevole incremento dell’efficienza operativa che si è tradotto in una drastica riduzione dei tempi di attrezzaggio delle presse e significativa riduzione dei costi di gestione.
I progetti di Moretto Brakes Components per il futuro
Tra i prossimi obiettivi di Moretto Brakes Components c’è quello di ottimizzare l’area adibita allo stoccaggio dei coil di materia prima tramite l’automatizzazione delle attività di prelievo e deposito. Come accadeva precedentemente per gli stampi, infatti, lo stoccaggio di questi materiali su scaffalatura tradizionale, oltre ad occupare molto spazio prezioso in magazzino, costringe gli operatori a cercare a vista i rotoli di polimeri di cui hanno bisogno perdendo molto tempo e con un rischio di commettere errori maggiore. La consapevolezza che gli investimenti in automazione e digitalizzazione dei processi intralogistici rappresentano un aspetto strategico fondamentale per continuare ad operare con successo in un mercato sempre più complesso ed esigente quale quello della filiera Automotive, consentirà a Moretto Brakes Components di continuare ad offrire ai suoi clienti componenti di valore, qualitativamente eccellenti, ed essere considerato sempre più come un partner strategico e non un mero fornitore di dispositivi.