L’innovazione nasce dalla collaborazione
Gruppo Master è un’azienda di Conversano (BA) specializzata dal 1986 nella progettazione e realizzazione di accessori per serramenti in alluminio. All’efficienza in attrezzeria partecipa il produttore di utensili giapponese MOLDINO, ormai parte attiva da due anni del processo industriale dell’azienda pugliese.
di Alberto Marelli
“Una serie di macchine può fare il lavoro di trecento uomini ordinari, ma nessuna macchina può fare il lavoro di una squadra straordinaria”. Questa citazione di Michele Loperfido, cofondatore della società insieme a Maria Luigia Lacatena, racchiude in sé la filosofia che anima da quasi 40 anni quest’azienda specializzata nella progettazione e realizzazione di accessori per serramenti in alluminio. Il Gruppo Master pone infatti un’attenzione particolare nel mantenere la centralità del capitale umano nelle operazioni strategiche e produttive dell’azienda. “L’uomo è al centro dei processi aziendali e utilizza la tecnologia come strumento in grado di liberarlo dalle incombenze meno gratificanti del lavoro.
Per il successo della fabbrica del futuro, la persona deve essere al centro, sia come forza creatrice del cambiamento, sia come principale attore nella realizzazione delle idee”, afferma Michele Loperfido.
Gruppo Master: ricerca, investimenti e studio della cultura degli accessori per serramenti in alluminio
I continui investimenti hanno sicuramente contribuito alla crescita dell’azienda, che attualmente occupa 320 dipendenti ed esporta in 58 paesi. “Circa il 50% del nostro fatturato deriva dall’export”, spiega Giuseppe Giorgio, Manager Attrezzeria presso Master Italy. Del Gruppo Master fanno parte anche le branch estere Master Polska e Master West Africa, a conferma dell’importante processo di internazionalizzazione partito qualche anno fa.
“Dedichiamo una profonda attenzione alla qualità dei materiali, alla ricerca di tecnologie in grado di permettere la produzione di prodotti fabbricati per alte performance, all’individuazione delle nuove esigenze dei mercati e alla soddisfazione e cura continua del cliente”, sottolinea Giorgio.
Da evidenziare che il Gruppo Master realizza il 94% del valore aggiunto della propria produzione in house, coprendo tutte le fasi che precedono la commercializzazione del prodotto: dall’analisi dei bisogni del mercato alla progettazione, prototipazione e produzione dei manufatti.
Il Gruppo Master utilizza tecnologie abilitanti
Un passaggio importante per l’azienda pugliese è avvenuto nel 2013 quando il management decise di intraprendere un processo di miglioramento continuo con lo scopo di garantire la soddisfazione del cliente e gestire la crescente complessità aziendale. “Le logiche alla base del nostro programma di miglioramento sono quelle del lean thinking, ovvero, la lotta allo spreco attraverso la semplificazione dei processi, il coinvolgimento del personale e la spinta verso la creazione di flussi sincroni di processo”, spiega Giorgio. “A supporto delle attività c’è l’adozione di tecnologie abilitanti, ovvero automazioni, macchine e sistemi integrati, che permettono il mantenimento delle corrette condizioni di lavoro e l’analisi delle prestazioni in real time. Ad esempio, tutti i nostri impianti sono connessi a un sistema centrale in cloud che permette sia agli operatori che alla direzione di avere il controllo costante della produttività e della qualità durante tutte le fasi produttive”.
Nel 2018, dopo 5 anni di implementazione delle logiche lean, e importanti investimenti nell’automazione e digitalizzazione dei processi, il Gruppo Master ha capitalizzato le esperienze realizzate elaborando il Master Italy Process System, ovvero una raccolta dinamica delle tecniche ed i metodi lean da utilizzare nei vari ambiti operativi, degli strumenti di sviluppo delle risorse umane e delle best practices a cui ispirarsi per i nuovi progetti. Gli ambiti all’interno del quale si spazia, sono la sicurezza e l’ambiente, il miglioramento e l’innovazione continua, la digital trasformation e lo sviluppo delle competenze.
MasterLAB, un laboratorio dedicato alla ricerca e sviluppo
La convinzione che gli accessori rivestano un ruolo essenziale nelle performance dei serramenti è oggi più che mai condivisa sia dal mondo delle costruzioni che dal mondo della progettazione e del design. Ed è per questo motivo che un aspetto fondamentale per Master è sicuramente la fase di ricerca e sviluppo. Questa attività si concentra all’interno del Centro Ricerche & Sviluppo con laboratorio prove MasterLAB. “Dal 2008 siamo impegnati sul fronte dell’innovazione, dell’evoluzione normativa riguardante i serramenti e a quella sempre più rapida dei mercati”, afferma Giorgio. “MasterLAB è dotata dei più moderni strumenti software, metodologici e sperimentali, per fare attività di ricerca, studio e progettazione; sperimentale e di sviluppo; di assistenza al cliente”.
MasterLAB, già in possesso di numerosi brevetti/modelli di utilità nazionali e internazionali, molti dei quali depositati a livello internazionale, offre i propri servizi ponendo una costante attenzione su tutti gli aspetti legati alle attività di ricerca e sviluppo operando nel settore della progettazione, sviluppo e sperimentazione di accessori/componenti per sistemi di apertura e chiusura per porte e finestre.
L’attrezzeria di Master Italy è parte attiva del sistema di produzione
I reparti produttivi Master Italy sono vari: stampaggio alluminio pressofuso, stampaggio zama, stampaggio materie plastiche, stampaggio a freddo, tranciatura di alluminio, reparti di assemblaggio e imbustaggio. “Nel reparto di pressofusione di alluminio la produzione è 7/7 a ciclo continuo; negli altri reparti di trasformazione la produzione avviene su due turni ed in caso di picchi la produzione avviene su tre turni, anche 7/7”, dichiara Giorgio.
L’attrezzeria all’interno di Master Italy è parte attiva del sistema di produzione. “Siamo strutturati con circa 1.700 codici suddivisi per articoli in zama, plastica e alluminio”, sottolinea Giorgio. “Le principali attività dell’attrezzeria sono la progettazione e realizzazione di attrezzature a supporto della produzione. Nello specifico realizziamo tasselli per stampi, con dimensioni massime 300x300x100 mm e lo scorso anno abbiamo realizzato circa 164 attrezzature complete”.
L’attrezzeria Master Italy è equipaggiata con centri di lavoro a 3 e 5 assi, elettroerosioni a filo e a tuffo, rettifiche tangenziali, torni a CNC, oltre alle classiche macchine da officina.
Tutte le fasi di lavorazione possono essere quindi eseguite internamente. “Affidiamo esternamente solo il trattamento termico e la saldatura laser”, sostiene Giorgio.
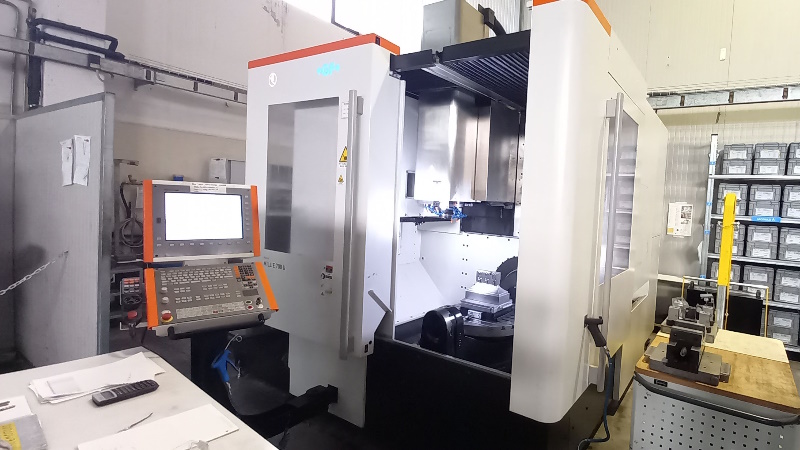
L’attrezzeria di Master Italy doveva abbattere i tempi necessari ai rifacimenti di stampi
“La necessità di attrezzature di produzione è in costante crescita. Circa il 60% della nostra forza lavoro è dedicata alla manutenzione e ai rifacimenti delle stesse, soprattutto quelle dedicate alla pressofusione e tranciatura a freddo”, spiega Daniel Menin, Tool Shop Group Area Leader presso Master Italy. “Inoltre Master Lab ci richiede la realizzazione di nuove attrezzature, negli ultimi anni sempre più customizzate e con tempistiche sempre più strette”.
“La principale difficoltà che Master Italy incontra nella costruzione/manutenzione dei propri stampi è la gestione dei flussi di richieste che arrivano sia dalla produzione che dal dipartimento di ricerca e sviluppo. Le richieste che arrivano dai dipartimenti di produzione possono a volte essere impreviste e devono essere gestiste in tempi rapidi al fine di impattare in maniera marginale sulla pianificazione”, afferma Giorgio.
Per la costruzione delle attrezzature, la criticità maggiore è dovuta ai molteplici passaggi tra le varie macchine utensili. “Ad esempio, per la realizzazione di un tassello pressofusione, avevamo la necessità di contemplare operazioni di fresatura pre e post tempra, rettifica, elettrodi ed erosione.
Bisognava altresì considerare il tempo di gestione della fase di trattamento termico, di 8 giorni lavorativi da fornitori esterni”, afferma Menin.
Per tentare di snellire questo processo produttivo, da circa due anni il Gruppo Master ha avviato la partnership con il produttore di utensili giapponese MOLDINO. “La criticità era intervenire su un sistema di produzione consolidato negli anni, con l’obiettivo di ridurre il lead time, liberare capacità produttiva interna e mitigare i costi di outsourcing”, spiega Giorgio.
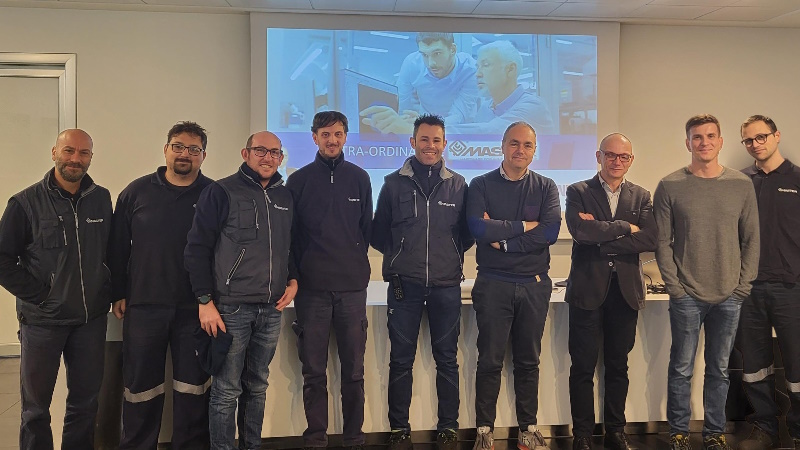
Il progetto strategico per l’anno 2022 di Master Italy e MOLDINO
L’interlocuzione con MOLDINO è iniziata nel 2021 quando i rispettivi team di lavoro si sono confrontati sugli aspetti fondamentali della produzione moderna nel comparto costruzione stampi.
Sulla condivisione dei valori di Pianificazione, Semplificazione, Standardizzazione, Automazione e Miglioramento Continuo, prende vita il progetto strategico per l’anno 2022.
“Tenendo conto dell’attuale potenziale tecnologico (impianti e risorse a disposizione) ma intervenendo in maniera critica su tutte le dinamiche chiave di processo, ci siamo concentranti sulla completa reingegnerizzazione del processo per la produzione dei tasselli di due componenti critici: manici e squadrette di cui è stata sviluppata, testata, implementata una metodologia innovativa”, afferma Patrizio Rongoni, Area Responsible South Italy di MOLDINO. “La filosofia Production50® sviluppata da MOLDINO per i propri clienti, si pone come obiettivo la riduzione dei costi operativi fino al 50% diventando quindi di valore strategico per le aziende dove essa viene implementata. Per realizzare concretamente tale vantaggio MOLDINO mette a disposizione presso i nostri partners un gruppo di professionisti in grado di agire su tutte le dinamiche determinanti nel processo di costruzione di stampi ed attrezzature”.
“Il nostro obiettivo è stato quello di realizzare i tasselli esclusivamente di fresatura partendo direttamente da grezzi temprati. Abbiamo quindi implementato un magazzino di tasselli trattati, standardizzati e pronti all’uso.
Abbiamo quindi sviluppato delle attrezzature ad-hoc che ci hanno permesso la realizzazione con il solo utilizzo di centro di lavoro a 5 assi.
Siamo riusciti a ridurre le fasi di piazzamento: ad esempio, per i tasselli squadretta, la fase di realizzazione prevede un unico posizionamento in macchina e quindi facilmente automatizzabili nel breve futuro.
Siamo riusciti ad abbattere i costi di processo in maniera significativa e determinante per il futuro”, spiega Menin.
Gli importanti risultati raggiunti nel 2022 e condivisi costantemente con tutti i livelli decisionali dell’azienda, hanno dato nuovo slancio e ambizioni per il futuro, confermando la volontà di proseguire la collaborazione con MOLDINO.
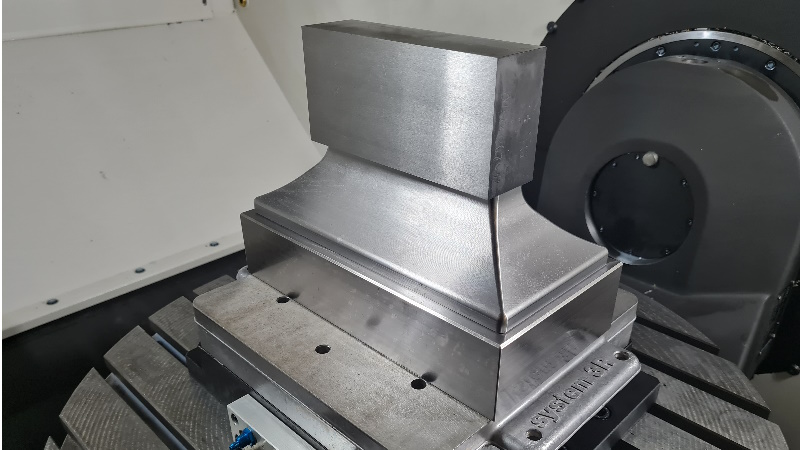
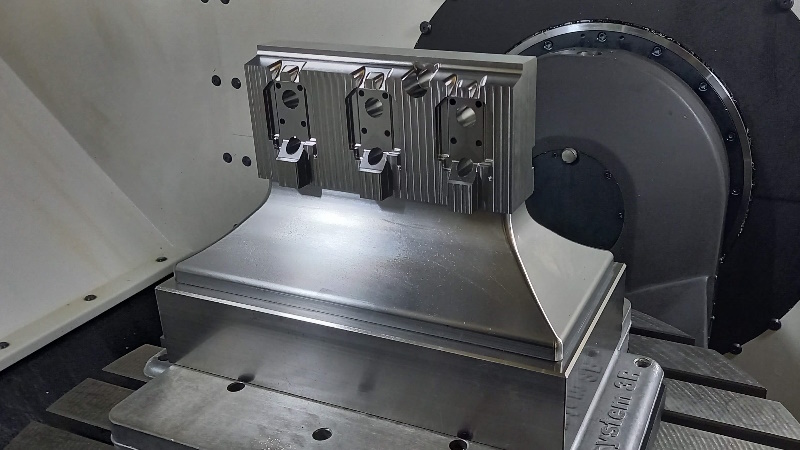
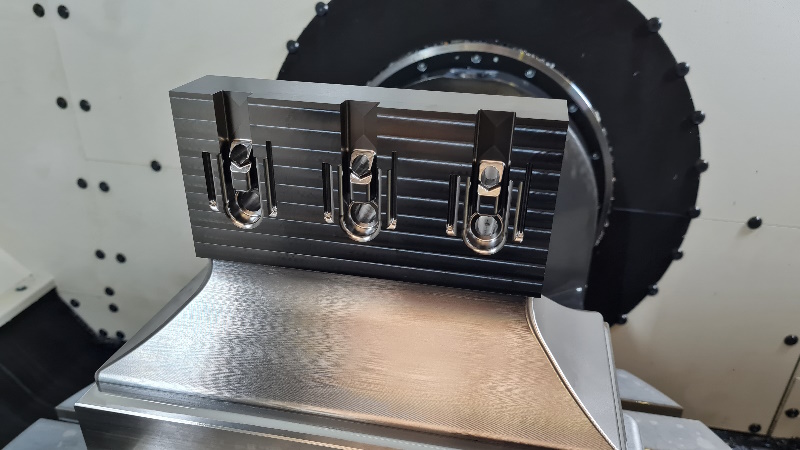
Dal grezzo di partenza temprato ai tasselli squadretta finiti in un unico posizionamento realizzati con tecnologia MOLDINO
Nuovi progetti per Master Italy e MOLDINO
“Per ottimizzare la produttività è necessario far lavorare le macchine durante la notte e i fine settimana e di conseguenza è indispensabile avere la certezza che quando togliamo il pezzo dalla macchina sia perfetto”, afferma Menin.
Visti gli importanti risultati ottenuti, l’azienda barese ha deciso di continuare la collaborazione con MOLDINO con un progetto che vedrà coinvolte le due aziende anche per i prossimi anni.
“Abbiamo deciso di dare continuità progettuale anche al futuro. I primi step riguarderanno la formazione, l’informatizzazione tecnologica mirata alla creazione dei “gemelli virtuali” al CAM degli impianti di fresatura nonché l’introduzione di un nuovo centro di lavoro a 5 assi pallettizzato con un magazzino utensili da 200 posti per una produzione h24”, conclude Giorgio.
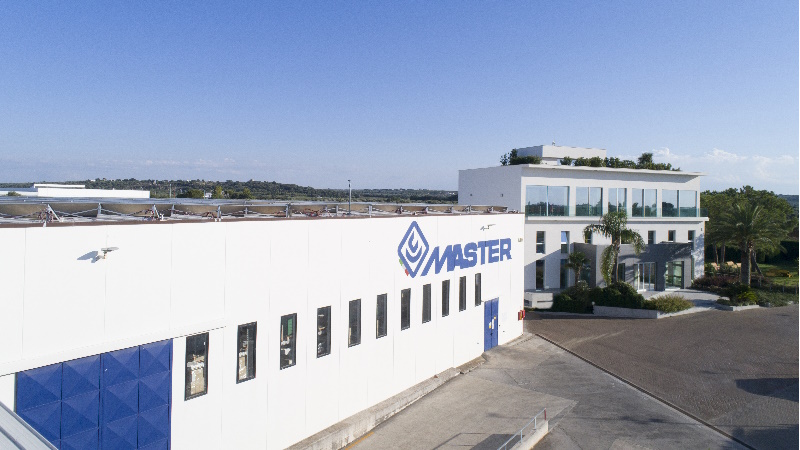
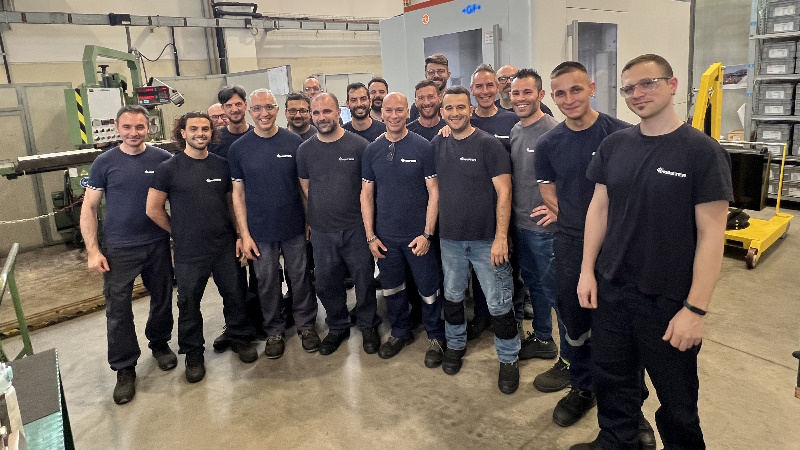
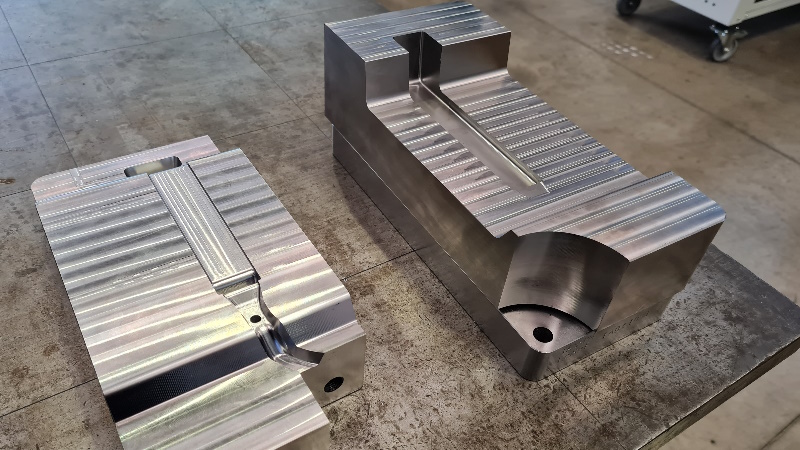
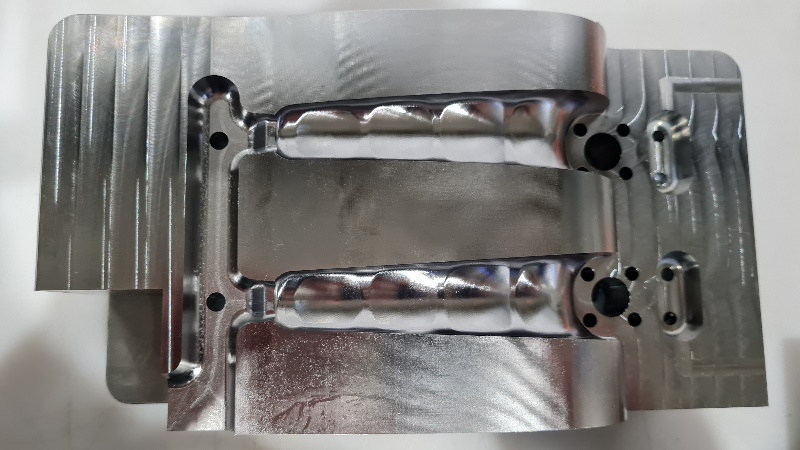