Arburg: per lo stampaggio ad iniezione
Il produttore tedesco Arburg, che celebra quest’anno cent’anni di attività, ha preso parte alla scorsa edizione di PLAST. L’azienda ha messo in mostra soluzioni in grado di garantire risparmio energetico e una maggiore sostenibilità. In evidenza la pressa ad iniezione Allrounder 470 H presentata nella variante Premium, configurata in modo specifico per la lavorazione di silicone solido.
di Alberto Marelli
In occasione di PLAST 2023, Arburg ha presentato un’ampia gamma di soluzioni per lo stampaggio ad iniezione in grado di rispondere alle esigenze del mercato legate al risparmio di energia e a una maggiore sostenibilità. “Il mercato si sta orientando verso macchine e azionamenti elettrici soprattutto per ragioni di precisione, efficienza energetica e sostenibilità”, afferma Raffaele Abbruzzetti, Amministratore Delegato di Arburg Italia. “PLAST è l’occasione giusta per gli operatori dell’industria delle materie plastiche per ripartire, guardarsi intorno e trovare idee che possano renderli più competitivi”.
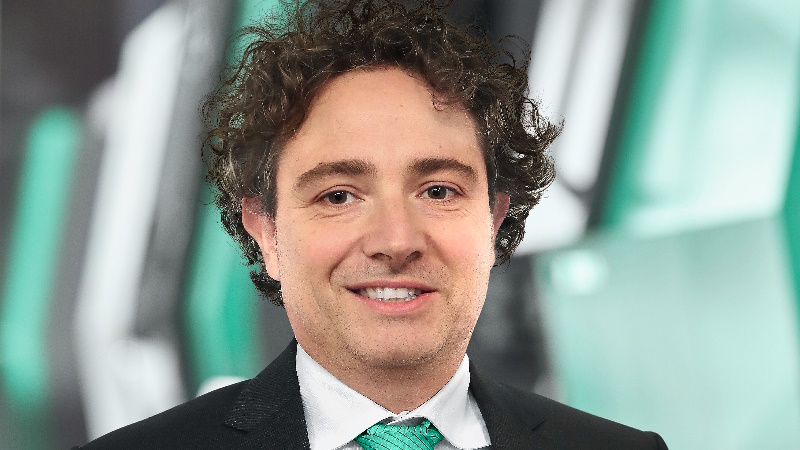
Arburg Allrounder 470 H: pressa ad iniezione ibrida
L’evento clou di Arburg a PLAST 2023 è stata l’anteprima italiana della Allrounder 470 H ibrida. La nuova pressa ad iniezione ibrida è particolarmente efficiente dal punto di vista energetico, delle risorse, della produzione, facile da usare e affidabile allo stesso tempo.
La combinazione di unità di chiusura elettrica e unità di iniezione idraulica riduce significativamente i costi di acquisto e di esercizio, nonché l’impronta di CO2. Allrounder 470 H ibrida è particolarmente interessante per gli utilizzatori che cercano un’alternativa a risparmio energetico alle macchine idrauliche o un’alternativa economica alle macchine elettriche.
La Allrounder 470 H presentata in fiera con forza di chiusura di 1.000 kN nella variante Premium era configurata in modo specifico per la lavorazione di silicone solido (HTV) con durezza 70 Shore A. La macchina esposta ha prodotto la parte in un tempo di ciclo di circa 43 s. L’alimentatore ACH Turnmix era utilizzato come dispositivo periferico, mentre un sistema robotico lineare Multilift Select 8 posizionava gli articoli sul nastro trasportatore.

Alternativa per il risparmio di costi e risorse
La serie Hidrive combina un’unità di chiusura elettrica ad alta efficienza energetica e di precisione con un’unità di iniezione idraulica potente e dinamica. Rispetto alle macchine completamente elettriche e idrauliche, è caratterizzata da costi di acquisto e operativi significativamente ridotti e da un migliore bilancio energetico e di CO2.
Una novità nella variante Premium è la ripartizione della portata di serie che, grazie alla più recente tecnologia delle valvole Varan, se necessario divide la portata disponibile della pompa principale. Ciò consente movimenti simultanei di assi secondari idraulici controllati in modo programmabile, come l’estrattore e comando anime. Ciò consente di risparmiare energia, costi e spazio sulla macchina e di aumentare l’efficienza produttiva.
Grazie a un nuovo concetto di gestione dell’olio, la nuova Allrounder 470 H richiede circa il 35% di olio in meno. L’acqua di raffreddamento necessaria può essere ridotta fino al 70% e anche il tempo di funzionamento a secco è ridotto di circa un terzo.
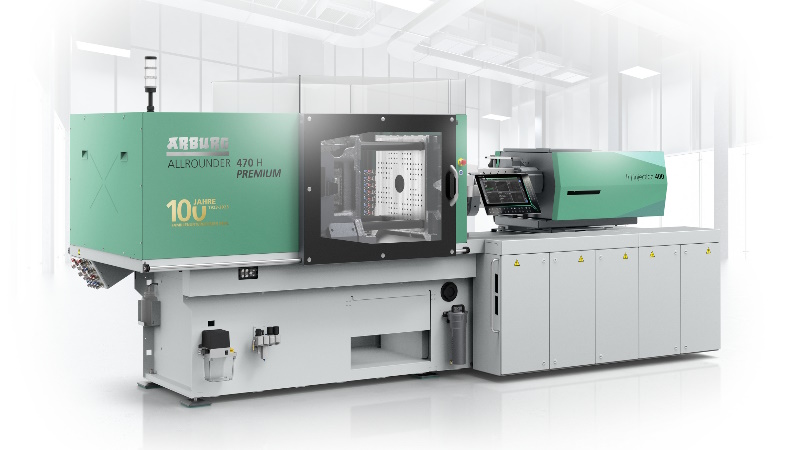
Arburg Allrounder 470 H: tre varianti di prestazioni
Grazie alle numerose opzioni, la Allrounder 470 H può essere adattata con precisione alle esigenze degli utilizzatori. È disponibile nelle tre varianti Comfort, Premium e Ultimate. Le prime due varianti sono dotate di serie di servoidraulica Arburg (Ash), in cui il servomotore raffreddato ad acqua a velocità controllata si adatta continuamente al fabbisogno effettivo di potenza, consentendo un funzionamento particolarmente efficiente dal punto di vista energetico e a basse emissioni. Allo stesso tempo, però, i requisiti di raffreddamento della macchina e il livello di rumorosità sono notevolmente ridotti.
Arburg Allrounder 470 H: facilità d’uso e manutenzione
Inoltre, la facilità d’uso e l’affidabilità sono criteri importanti per la nuova macchina al fine di risparmiare tempo e denaro in assistenza e manutenzione. La manutenzione predittiva è una parola chiave importante: ad esempio, la macchina segnala automaticamente quando il filtro dell’olio deve essere sostituito a breve. I filtri dell’olio e i collegamenti sono più accessibili e anche le posizioni di installazione della lubrificazione centralizzata, dei componenti pneumatici e delle interfacce sono state ottimizzate.
Chiusure Flip-top per flaconi di cosmetici realizzati su una Arburg Allrounder 570 A Comfort
Con una Allrounder 570 A Comfort elettrica, Arburg ha mostrato ai visitatori di PLAST 2023 una tipica applicazione per imballaggio. La pressa esposta ha trasformato il PP di Exxon Mobil in chiusure Flip-top di alta qualità utilizzate per i flaconi di cosmetici.
Un’altra pressa elettrica era presente presso lo stand del partner Sverital. Qui, una Allrounder 470 A con forza di chiusura di 1.000 kN ha trasformato il silicone liquido (LSR) in guarnizioni assiali per l’industria automobilistica. Grazie alla collaborazione del team di Arburg Italia con Sverital, è possibile offrire anche tutti gli accessori per il funzionamento di un tale impianto di stampaggio a iniezione.
Grazie alla loro precisione, all’efficienza energetica e alla sostenibilità, le macchine ad azionamento completamente elettrico come la pressa esposta della serie Alldrive sono molto richieste, soprattutto nel mercato italiano.
Il complesso stampo a sedici cavità è stato realizzato da Giurgola Stampi. La Allrounder 570 A elettrica con forza di chiusura di 2.000 kN produce quindi sedici chiusure Flip-top in PP di Exxon Mobil in un tempo di ciclo di circa 12 s. Tramite le interfacce OPC UA dei canali caldi e del sistema di raffreddamento è possibile gestire comodamente il processo di stampaggio a iniezione.
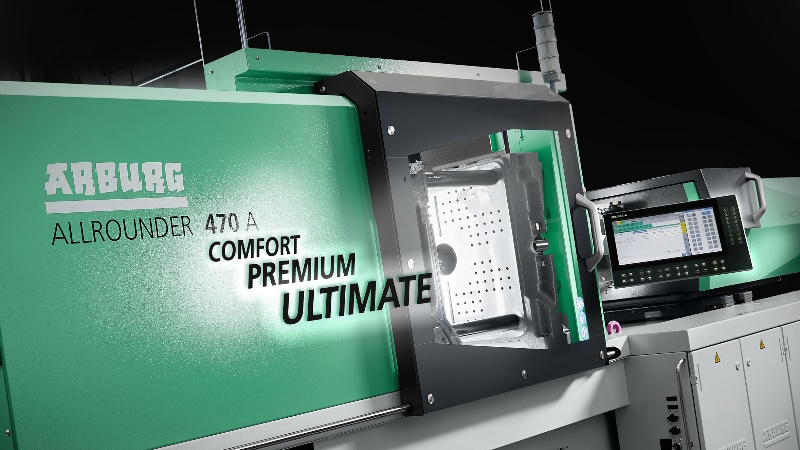
Gestica: le funzioni di assistenza forniscono un supporto attivo
Gli ulteriori sviluppi del sistema di controllo Gestica si concentrano su assistenti “intelligenti” e concetti di controllo adattivi che creano valore aggiunto. Le funzioni di assistenza forniscono supporto durante l’impostazione e il funzionamento, facilitano il lavoro sulla macchina e garantiscono un’elevata qualità dei pezzi. Il controllo Gestica della pressa esposta dispone di tre assistenti di questo tipo: aXw Control FillAssist, aXw Control CycleAssist e aXw Control PressurePilot.
La funzione “aXw Control FillAssist” è disponibile per la simulazione del riempimento direttamente nel sistema di controllo. In questo modo è possibile calcolare i parametri ottimali della macchina a partire dal disegno 3D del componente e accorciare la progettazione del pezzo stampato e dello stampo da diverse settimane a pochi giorni. L’”aXw Control CycleAssist” conosce la sequenza di ciclo programmata e confronta graficamente i tempi attuali di ogni fase del ciclo con i valori di riferimento precedentemente definiti. Infine, “aXw Control PressurePilot” garantisce una regolazione della pressione ottimizzata bionicamente nel processo di stampaggio a iniezione. In questo modo vengono ridotti gli scostamenti di qualità delle parti stampate e quindi anche le perdite di materiale.
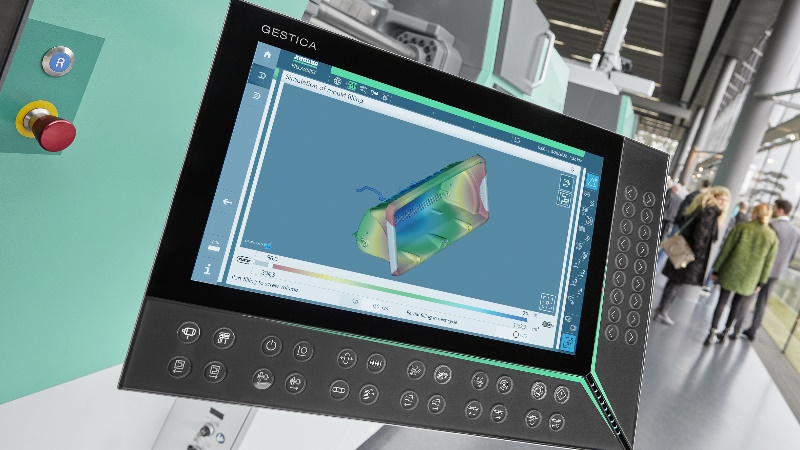
Alldrive: macchine elettriche, precise ed efficienti dal punto di vista energetico
Nelle macchine ad alte prestazioni della serie elettrica Alldrive, i servomotori di alta qualità e gli ingranaggi del mandrino ad azione diretta garantiscono movimenti rapidi e simultanei e un’elevata riproducibilità. La base per l’efficienza energetica è costituita dall’unità di chiusura a ginocchiera a cinque punti, dall’elevata efficienza degli azionamenti servoelettrici e dal recupero dell’energia di frenata. Inoltre, gli azionamenti chiusi e raffreddati a liquido funzionano in modo silenzioso, evitano l’esposizione alla polvere e le turbolenze dell’aria e sono indicati anche in ambienti di produzione sterili. Le Allrounder Alldrive sono disponibili nelle varianti Comfort, Premium e Ultimate e possono essere adattate con precisione al singolo caso.
Arburg Allrounder elettrica 720 A: ottimizzata per le alte prestazioni
Che la tecnologia di stampaggio a iniezione di alta qualità possa essere un’alternativa alla termoformatura, lo ha dimostrato Arburg in fiera con una Allrounder elettrica 720 A nella variante Ultimate. La pressa esposta ha utilizzato il processo di stampaggio a inietto-compressione per produrre bicchieri IML a parete sottile, che possono essere facilmente riciclati dopo l’uso.
La macchina ad alte prestazioni ad azionamento diretto con forza di chiusura di 2.900 kN è dotata di un’unità di iniezione di grandezza 1300, appositamente ottimizzata per le alte prestazioni.
Grazie ai servomotori ad alta precisione della consociata AMK, si ottengono portate volumetriche di iniezione molto elevate e velocità di iniezione fino a 400 mm/s.
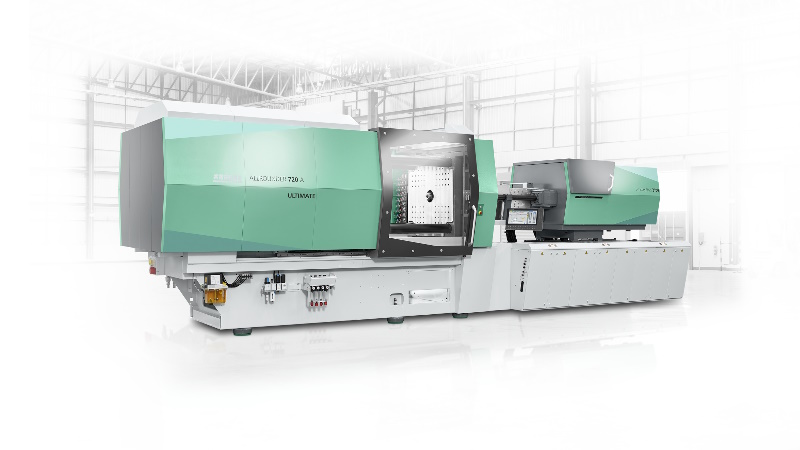
Bicchieri IML di soli 0,37 mm di spessore
La pressa esposta ha utilizzato uno stampo a quattro cavità di Brink per produrre bicchieri a sezione rotonda IML a parete sottile da polipropilene (PP) con il processo di stampaggio a inietto-compressione. Per il monitoraggio del processo, lo stampo è dotato di quattro sensori della corsa di inietto-compressione. In un tempo ciclo di 3,95 s vengono prodotti quattro pezzi stampati, ciascuno del peso di 10,8 g e con spessore della parete di soli 0,37 mm. La plastica è bilanciata con biomassa e certificata ISCC. Nell’unità di produzione era integrato anche il robot side-entry di Brink, che inseriva le etichette, rimuoveva i bicchieri finiti e li impilava sul nastro trasportatore.
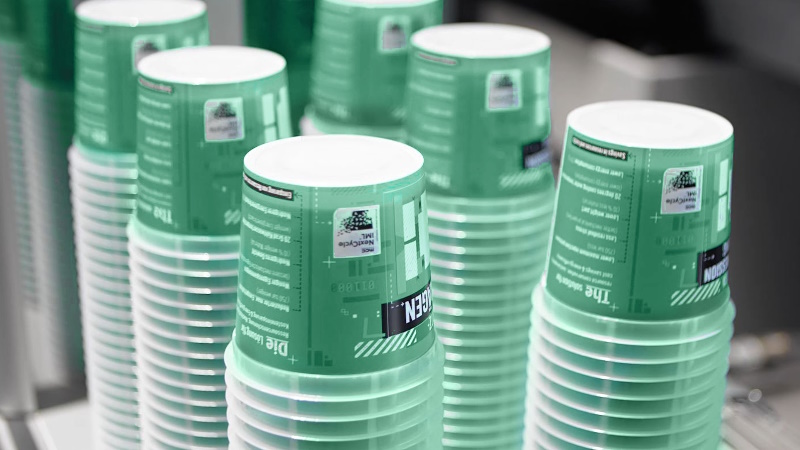
Risparmio di risorse e riciclabilità
In questa applicazione per l’industria dell’imballaggio, particolarmente attenta al risparmio di risorse, è stata prestata particolare attenzione alla progettazione di componenti a risparmio di materiale e all’efficienza energetica.
Grazie alla macchina completamente elettrica in combinazione con lo stampaggio a inietto-compressione, il bilancio energetico migliora del 20% con una significativa riduzione del peso dei componenti da 13 a 10,8 g. Il rapporto tra il percorso del flusso e lo spessore della parete è di 380:1. Convenzionalmente, ciò richiederebbe una pressione di iniezione molto elevata, a scapito del consumo di energia e dell’usura dello stampo. Questo è il motivo per cui per questa applicazione è stato utilizzato lo stampaggio a inietto-compressione. Rispetto allo stampaggio a iniezione classico, questo processo richiede una pressione di iniezione significativamente inferiore e può essere utilizzato con temperature dello stampo di 20 °C anziché 12 °C. La speciale etichetta “Next Cycle IML” può essere completamente separata dal PP del bicchiere durante il riciclaggio, in modo che il prodotto possa essere riciclato separatamente per tipo dopo l’uso. A differenza della termoformatura, inoltre, non vengono utilizzate pellicole pre-prodotte e non vengono prodotti scarti di punzonatura.
Arburg Allrounder More 1600: per ridurre sensibilmente i costi di fabbricazione
Durante i quattro giorni di manifestazione, Arburg e il suo partner per gli stampi Braunform hanno mostrato come l’integrazione delle funzioni possa far risparmiare tempo e costi, utilizzando l’esempio dei connettori Luer, che vengono utilizzati come tappi di chiusura nell’industria farmaceutica. Una Allrounder More 1600 ha prodotto i pezzi stampati a iniezione bicomponente, mentre la manipolazione dei pezzi era affidata a un robot a sei assi Yaskawa. La chiusura dei tappi e la realizzazione dei filetti sono state eseguite direttamente nello stampo.
La soluzione high-end innovativa elimina la necessità di un secondo stampo e di una linea di assemblaggio aggiuntiva. In questo modo si riducono sensibilmente i costi per la fabbricazione.

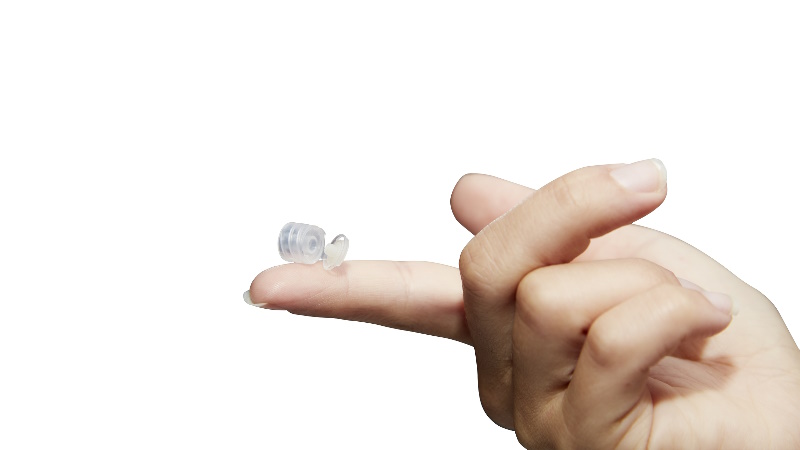
Precisione negli spazi più ristretti
In un tempo ciclo di circa 10 s sono stati prodotti quattro connettori Luer pronti all’uso. Lo stampaggio a iniezione richiede sensibilità e precisione: il peso del pezzo in componente PP è di 0,2 g, mentre il componente TPE morbido pesa solo 0,05 g. Il materiale è stato realizzato con materie prime rinnovabili o riciclate chimicamente (ISCC Bilancio di Massa). Lo stampo a 4+4 cavità è provvisto della tecnologia RotaricE2® di Braunform. Quattro assi servoelettrici della consociata AMKmotion di Arburg, monitorati dall’unità di comando Gestica, svolgono un ruolo centrale: controllano direttamente nello stampo i cicli per il core-back, il sollevamento del coperchio, la chiusura dei tappi e lo svitamento dei filetti Luer. Il design compatto consente un elevato numero di cavità in uno spazio ridotto. Sono possibili stampi in serie con un massimo di 64+64 cavità.
Nell’unità di comando Gestica è inoltre integrato un robot Yaskawa a sei assi. Questo, analogamente a un sistema robot Multilift lineare, può essere programmato in modo semplice e rapido direttamente tramite l’unità di comando della macchina. Il robot industriale “powered by Arburg” è arrivato ampliando il programma di automazione nella primavera di quest’anno. Arburg assume qui il ruolo di integratore di sistemi e offre celle di produzione coordinate da un’unica fonte. Durante la dimostrazione in fiera, il robot Yaskawa prelevava i pezzi finiti dallo stampo con una pinza quadrupla e li sottoponeva singolarmente a un controllo della telecamera in linea, prima di depositarli in contenitori separati da cavità tramite un sistema di cassetti.
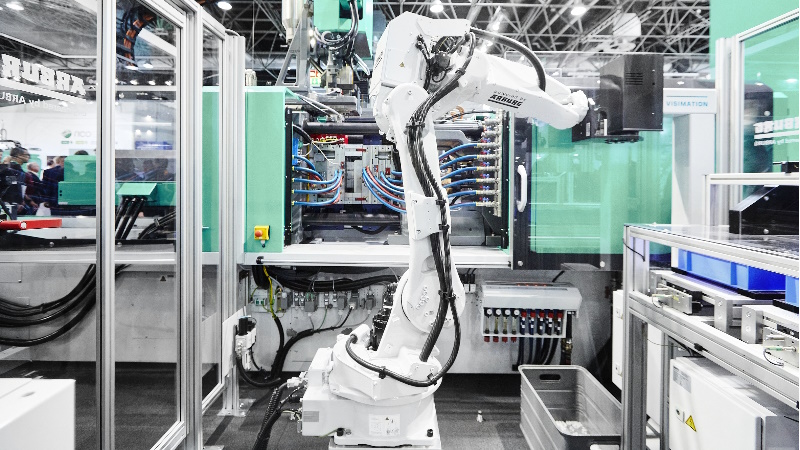
Allrounder More: più spazio, modularità e comfort
La serie More, modulare ed efficiente nella produzione, è appositamente progettata per lo stampaggio a iniezione di multicomponente. Le Allrounder More possono essere adattate in modo flessibile alle esigenze della clientela. Offrono più spazio per stampi più grandi e corsa utile dell’espulsore, maggiore modularità nella struttura e numerose funzioni ottimizzate per una maggiore facilità d’uso e una facile manutenzione. Le macchine sono dotate di serie di un’unità di chiusura a ginocchiera elettrica altamente dinamica con servomotori raffreddati a liquido ad alta efficienza energetica, due unità di iniezione elettrica e una forza di chiusura a scelta tra 1.600 o 2.000 kN. In questo modo è possibile realizzare tutte le più comuni applicazioni a due componenti.
Arburg è un partner a 360 gradi
Presse per stampaggio a iniezione, produzione additiva, sistemi robot, controllo del processo, digitalizzazione: Arburg è in grado di fornire tutte queste tecnologie come unico fornitore. “Siamo un partner a 360 gradi per i nostri clienti, coprendo ogni singolo aspetto: dalla consulenza per la preparazione di un progetto, la scelta della macchina giusta e il supporto del servizio clienti post-vendita, alla realizzazione di progetti chiavi in mano con automazione, formazione e supporto tecnologico. E poi ci sono i nostri prodotti digitali, come ALS e il portale clienti arburgXworld con le sue ampie funzionalità per il contatto diretto con Arburg”, conclude Abbruzzetti.