Si rinnovano le macchine per lavorazione e deformazione tubi
Frena il mercato dell’acciaio ma il segmento dei tubi resiste, anche grazie all’innovazione nei macchinari per la loro lavorazione e relativi componenti. La lavorazione dei tubi ha infatti raggiunto ottimi livelli di automazione, flessibilità e integrazione nonché, grazie al CNC, produttività e risparmio energetico.
di Stefano Vinto
L’andamento in frenata del mercato dell’acciaio non ha fermato l’innovazione dei macchinari per la lavorazione e deformazione dei tubi, che negli ultimi anni si sono innovati nel nome di una qualità e precisione dei prodotti sempre più elevata. Grazie anche all’utilizzo di componenti robusti e sofisticati.
Sulla performance della siderurgia pesa chiaramente l’andamento dei settori di sbocco a cominciare dall’auto e dai mezzi di trasporto con la relativa componentistica. I tubi, peraltro, sono a volte in controtendenza rispetto ad altri prodotti dell’acciaieria: anche perché l’innovazione in questo segmento non si è fermata, specie nell’ambito della lavorazione dei tubi in acciaio.
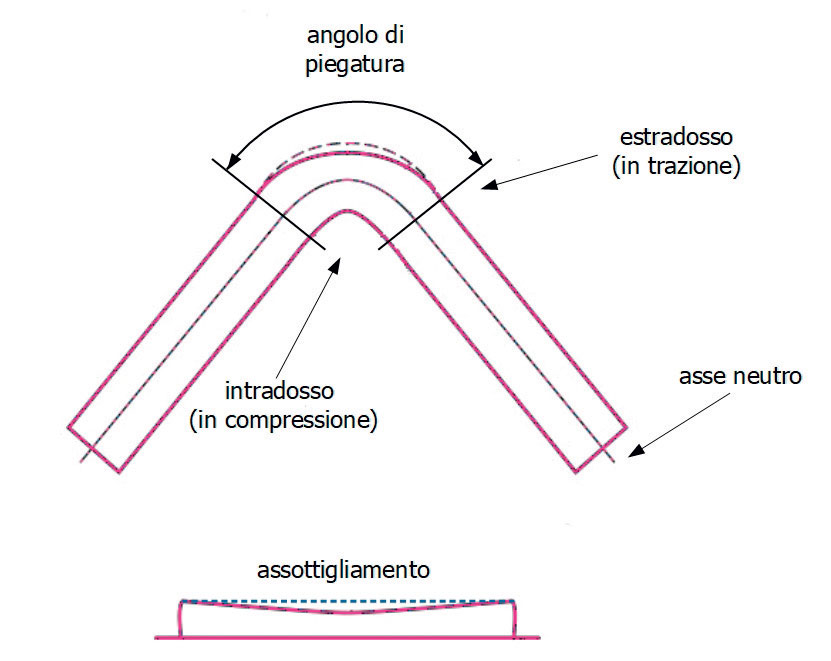
Macchinari sempre più sofisticati
In questi ultimi anni, l’utilizzo dei tubi in diversi ambiti, dall’automotive, all’industria del ciclo e motociclo, fino a quella dei mobili per arredamento e l’edilizia, ha portato inevitabilmente a un’evoluzione dei macchinari dedicati nello specifico alla deformazione di tubi in acciaio. Per rispondere alle nuove e crescenti esigenze del mercato, l’ingegneria meccanica del settore ha subìto un lungo percorso di innovazione con l’obiettivo di produrre con una precisione e volumi crescenti, impossibili da ottenere con le vecchie tecnologie tradizionali. Se fino a vent’anni fa sul mercato esistevano prevalentemente macchinari manuali in grado di soddisfare una produzione limitata e artigianale, oggi invece siamo in presenza di macchine completamente automatizzate e di alta precisione destinate alla grande industria. Apparecchiature che utilizzano numerosi servo-assi e che, quindi, richiedono componenti sempre più sofisticati, tra questi anche i giunti di precisione ad alta rigidità torsionale, come i prodotti di R+W della serie lamellare LP, ideali in tutte le applicazioni con Servomotori, o a soffietto BK. Robusti e compatti possono essere utilizzati in diverse applicazioni dell’ingegneria meccanica. In particolare, nei nostri lamellari la trasmissione di coppia non avviene per sollecitazione a taglio delle viti sulle lamelle ma, grazie all’attrito tra le parti assemblate e il pacco lamellare, la trasmissione di coppia è interamente a carico della lamella, consentendo un’elevata densità di coppia e zero gioco. Queste caratteristiche consentono ai costruttori di macchinari di raggiungere il massimo livello di qualità nella progettazione delle loro tecnologie. Qualità che da sempre contraddistingue il Made in Italy in tutti i settori.
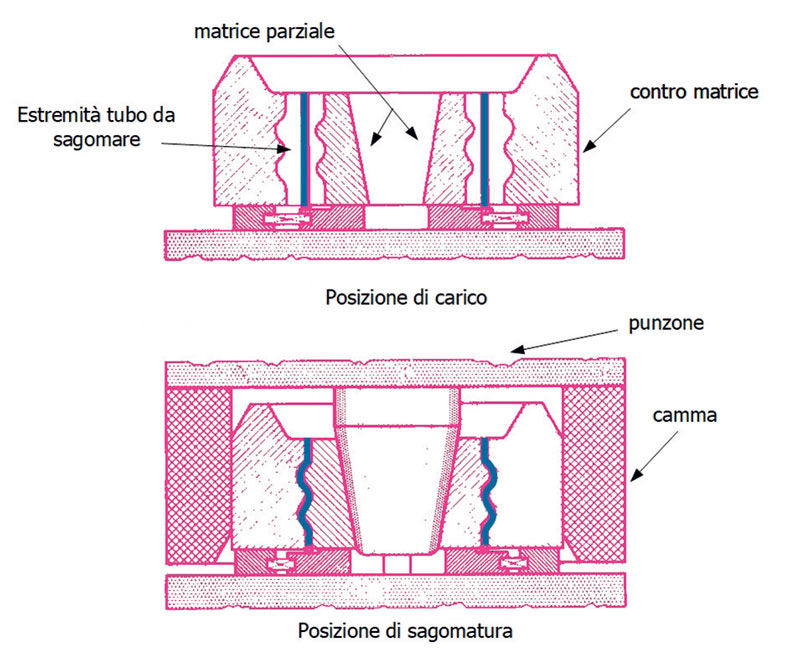
I processi di lavorazione dei metalli
I processi di lavorazione dei metalli per deformazione plastica vengono abitualmente classificati in processi primari e processi secondari.
I processi primari impiegano materiali da fusione, da cui vengono ricavati semilavorati commerciali tramite l’impiego di macchinari pesanti, che applicano stati di tensione tridimensionali. I semilavorati ottenuti vengono così destinati sia ad utenze finali che ad ulteriori processi di trasformazione.
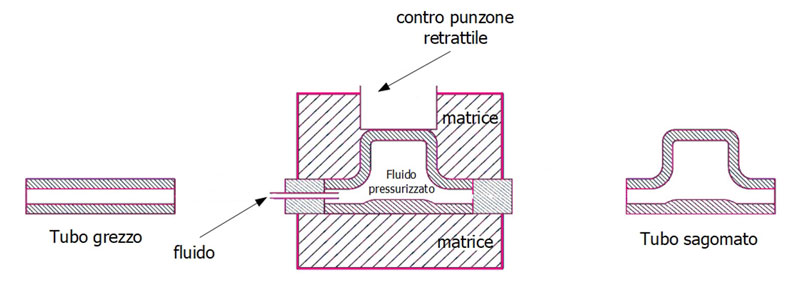
I processi secondari partono dai suddetti prodotti ed applicano stati piani di tensione e carichi di minore entità rispetto a quelli dei processi primari, al fine di conferire al semilavorato una forma finale.
Di seguito verranno brevemente esaminati i processi secondari relativi alla piegatura ed alla sagomatura dei tubi, evidenziandone gli aspetti relativi ai livelli di precisione ed alle prestazioni attualmente ottenibili con i macchinari a disposizione.
La piegatura e la sagomatura dei tubi: concetti fondamentali
I principi alla base della piegatura dei tubi sono abbastanza simili a quelli della piegatura delle barre. Due accorgimenti aggiuntivi, fondamentali nella piegatura dei tubi, sono dati dall’impiego di un supporto all’interno del tubo stesso e dall’impiego di uno analogo anche sul lato interno della piegatura. Lo spessore di parete del tubo influenza in maniera determinante la distribuzione delle tensioni di trazione e di compressione, che insorgono durante l’esecuzione della piegatura. Infatti, un tubo dalla parete spessa si piega ad un piccolo raggio di curvatura di solito più facilmente rispetto ad un tubo a parete sottile. Al fine di comprendere meglio questo aspetto, risulta utile ricordare brevemente gli aspetti fondamentali del processo di piegatura.
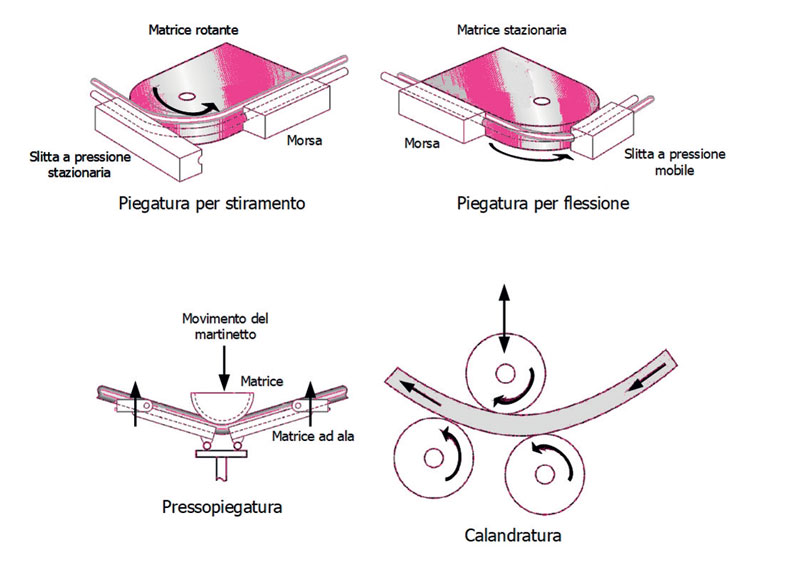
La piegatura può essere definita come il processo di deformazione plastica dei metalli intorno ad un asse con poca o nulla variazione dell’area superficiale. In genere, i processi di piegatura della lamiera consistono in ripetizioni multiple al fine di ottenere risultati di un certo grado di complessità, per cui lo studio di tale processo (tramite l’approssimazione alla teoria della flessione semplice) risulta valido solo nei casi in cui ciascun asse di una piegatura multipla sia lineare ed indipendente dagli altri.
Nei casi in cui le pieghe multiple vengano realizzate tramite una matrice singola, il processo prende il nome di sagomatura. In tutti gli altri casi in cui gli assi di deformazione non siano lineari o non siano indipendenti, si dà origine a processi quali tra trafilatura e la formatura per stiramento.
Come mostrato schematicamente in Figura 1, il processo di piegatura fa sì che il metallo sulla parte esterna (estradosso) sia in trazione mentre quello sulla parte interna (intradosso) sia in compressione.
La posizione in cui il materiale non risulta né compresso né allungato, avendo così l’equilibrio dello stato tensionale nel componente, viene chiamato asse neutro della piegatura. Poiché la resistenza allo snervamento dei metalli a compressione è notevolmente più alta della resistenza allo snervamento a trazione, il metallo sull’estradosso snerva per prima e l’asse neutro viene spostato dal punto medio della sezione del materiale. In genere l’asse neutro è posizionato tra 1/3 e 1/2 della distanza misurata a partire dalla superficie interna fino al punto medio della sezione. Tale distanza varia a seconda del raggio di piegatura e delle caratteristiche meccaniche del materiale. Sulla base di questo comportamento asimmetrico e della preponderanza delle deformazioni da trazione, la sezione del metallo si assottiglia in corrispondenza della piegatura, come mostrato in Figura 1. In caso di piegatura lineare, l’assottigliamento è massimo nel centro della sezione e minore in prossimità dei bordi liberi, dove uno spostamento diretto verso l’interno del materiale può fornire un minimo grado di compensazione.
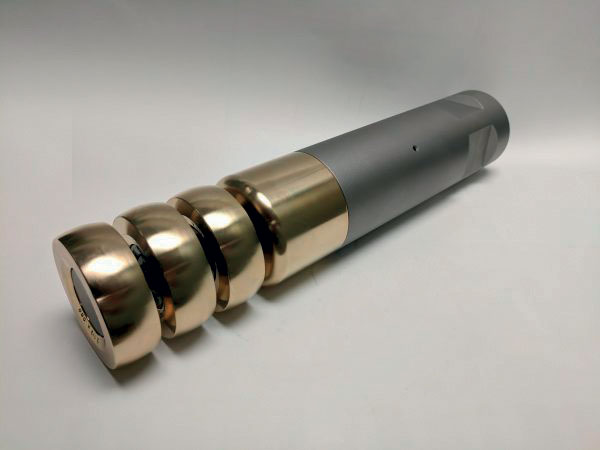
All’intradosso della piegatura, le tensioni da compressione possono indurre distorsioni localizzate ed un contestuale ispessimento del materiale. Sebbene questo ispessimento vada, in qualche modo, a compensare l’assottigliamento all’estradosso, le distorsioni localizzate possono determinare un movimento verso l’esterno dei bordi liberi. Questa combinazione di contrazione della faccia in trazione e di dilatazione della faccia in compressione può produrre una distorsione significativa delle superfici dei bordi terminali di una piegatura lineare. Tale distorsione, per esempio, è particolarmente pronunciata nella piegatura di piastre spesse e strette. Estendendo tali osservazioni al caso dei tubi (unitamente alle problematiche relative al fenomeno del ritorno elastico, che si manifesta alla rimozione del carico di piegatura ed è anch’esso determinato dalla suddetta compresenza di trazione e compressione), vanno tenute in conto ulteriori problematiche connesse alla geometria.
I parametri chiave nella piegatura dei tubi sono il diametro esterno, lo spessore di parete ed il raggio di piegatura. Tubi di piccolo diametro e con alti spessori di parete determinano bassi livelli di difficoltà di piegatura. Al crescere del diametro esterno, lo spessore di parete diminuisce oppure il raggio di piegatura diventa più piccolo; l’estradosso del tubo tende a tirare verso il centro, appiattendo il tubo e determinando il corrugamento della superficie interna.
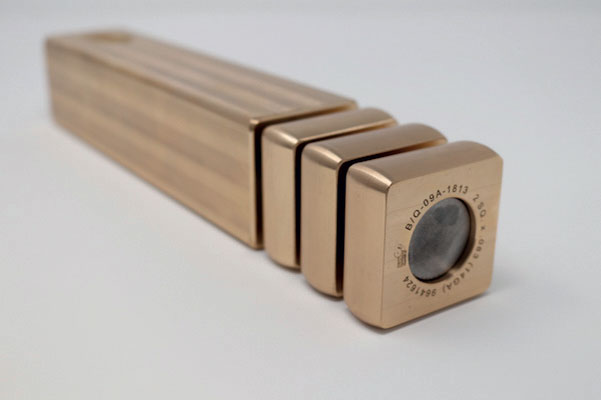
Con il termine sagomatura si individuano, invece, tutte quelle lavorazioni che consentono la conversione di una sezione tubolare di partenza in un’ampia varietà di prodotti. Tali lavorazioni possono essere usate sia singolarmente che in successione e tra queste si ricordano la pressatura con matrici progressive (mostrata schematicamente in Figura 2), la formatura a freddo, la rastremazione tramite rollatura, l’imbutitura al tornio (detta anche tornitura in lastra) e l’intestatura (o sfacciatura).
A queste lavorazioni si è di recente aggiunta anche quella di idroformatura, che rappresenta attualmente un processo di lavorazione significativo per la produzione di componenti tubolari resistenti e leggeri. In Figura 3 vengono schematicamente mostrate le fasi del processo. L’idroformatura ha avuto grande diffusione a partire dal settore dell’automotive. Interessanti varianti, concepite successivamente, sono l’idroformatura a bassa o alta pressione, a pressione sequenziale e a pressione pulsante o vibrante. Queste varianti estendono l’uso dei materiali ad alte prestazioni ottimizzando le forme dei prodotti finali e la resistenza finale per effetto dell’incrudimento. Il vantaggio principale, che le stesse consentono di conseguire, è il minor ricorso alle più costose lavorazioni di stampaggio e saldatura di lamiera. Tutte queste caratteristiche, unitamente alle esigenze di mantenere alti livelli di stabilità dimensionale e di qualità della lavorazione per tassi di produttività tipici dei contesti industriali, sono stati determinanti nella concezione e nell’evoluzione delle moderne macchine di piegatura e sagomatura dei tubi.
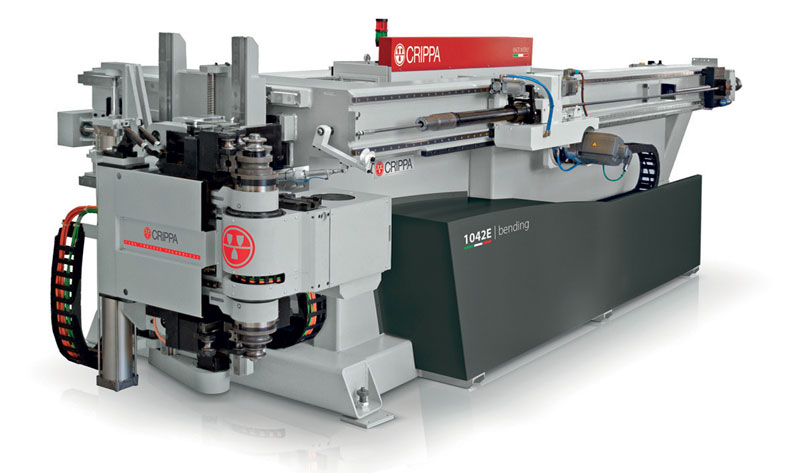
Le macchine di piegatura e sagomatura dei tubi e la loro evoluzione
Il processo di piegatura dei tubi veniva realizzato, in passato, esclusivamente tramite macchinari ad azionamento manuale, dotate successivamente di dentature di arresto, leveraggi e ruote dentate, al fine di fornire all’operatore un vantaggio meccanico. Tali macchinari, molto simili a quelli impiegati per le piegature delle barre, sono in uso anche attualmente, specie nella realizzazione di piegature di tubi di grosso spessore e come attrezzature di officina. Un tipico esempio di questi macchinari è mostrato in Figura 4, con capacità di piegatura massima pari ad un diametro esterno di 64 mm con spessore di parete pari a 3 mm (acciaio con percentuale di carbonio compreso tra 0.15% e 0.25%) o ad un diametro esterno di 50 mm con spessore di parete pari a 3mm (acciaio inox).
Nell’impiego dei macchinari ad azionamento manuale, le soluzioni per fare fronte alle problematiche di appiattimento dei tubi durante la piegatura, su accennate, consistevano nell’impiego di sabbia umida con cui riempire il tubo prima della lavorazione. Attualmente vengono impiegati mandrini flessibili, il cui tipo più ricorrente viene mostrato in Figura 5. Questi mandrini sono disponibili in un’ampia varietà di dimensioni e sezioni, come quello a sezione quadrata mostrato in Figura 6.
Le tipologie di lavorazione di piegatura dei tubi sono mostrate in Figura 7. Nella piegatura per stiramento, il tubo viene fissato su una matrice rotante e viene stirato, durante la rotazione dell’intero assieme, tramite una slitta a pressione stazionaria. Nella piegatura per flessione, la matrice rimane stazionaria e la slitta a pressione è mobile, spostandosi lungo la superficie del tubo. Nella pressopiegatura, un martinetto spinge verso il basso una matrice, che agisce nel centro del tubo che è supportato a entrambe le estremità da matrici ad ala. Mentre il martinetto si abbassa, le matrici ad ala ruotano verso l’alto piegando il tubo attorno alla matrice del martinetto. È evidente il limite di tale tipologia di lavorazione, dovuto alla porzione di materiale necessaria per il fissaggio sulle matrici ad ala. Nella calandratura, la piegatura dei tubi viene realizzata in tre punti tramite tre rulli sagomatori. I due rulli inferiori sono trascinatori e la posizione del rullo superiore viene regolata al fine di controllare il grado di curvatura della piegatura.
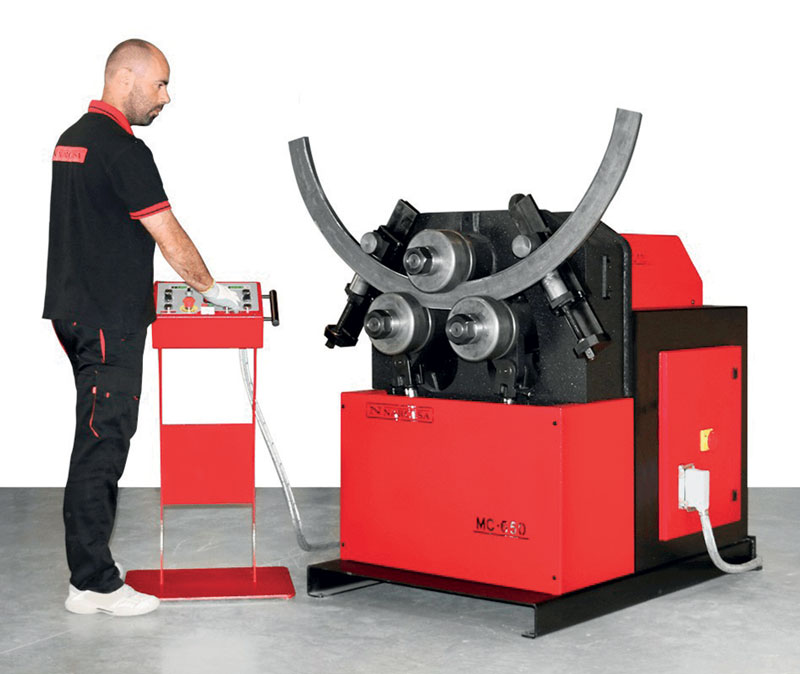
Sulla base delle caratteristiche delle varie tipologie di piegatura su esposte, il passaggio dalle lavorazioni su macchinari ad azionamento manuale a quelle su macchinari ad azionamento elettrico o elettroidraulico si è reso necessario a causa dei problemi dovuti alla lentezza della lavorazione e alla non ripetibilità della stessa.
Sebbene la maggior parte delle macchine per piegatura di tubi siano basate sulle lavorazioni di piegatura per stiramento e di piegatura per flessione, prima esposte, la loro evoluzione è stata determinata principalmente dalla necessità di implementazione dei sistemi CN e di automazione del ciclo di lavorazione. Su questa base, le moderne macchine di piegatura dei tubi (dette macchine curvatubi) presentano caratteristiche sia di intercambiabilità tra attrezzature con diversi raggi e bloccaggi che di utilizzo contemporaneo delle stesse. Il tutto concepito in modo da ridurre i tempi riconfigurazione, rispettando le esigenze di ergonomia per l’operatore. Unitamente a queste soluzioni, risulta sempre più diffuso il ricorso ad azionamenti elettrici tramite motori brushless, che presentano indubbi vantaggi quali il risparmio energetico, l’ottenimento di grandi qualità di lavorazione, la consistente riduzione dei tempi di fermo macchina per attrezzaggio e per riavvio, oltre che la ridotta resistenza meccanica e la possibilità di un controllo diretto digitale da parte del sistema CNC.
Risulta evidente come il conseguimento degli elevati livelli di produttività e di precisione necessitino di un’attività di progettazione finalizzata all’ottenimento delle apposite catene cinematiche, tramite l’opportuna scelta degli accoppiamenti. Gli stessi devono infatti fare fronte alle esigenze di compensazione dei disallineamenti e di assenza di gioco angolare. Un esempio attuale di una scelta ottimale di tutte queste soluzioni è mostrato nella macchina curvatubi a controllo numerico mostrata in Figura 8; questa macchina consente di realizzare cicli di lavorazione completamente automatici, di utilizzare contemporaneamente più attrezzaggi con raggi di piegatura e bloccaggi diversi, che permettono non solo la realizzazione di geometrie di tubo che richiederebbero anche operazioni di ripresa (con conseguenti tempi di fermo macchina), ma anche l’integrazione dei cicli di carico e scarico del tubo nella movimentazione. I livelli di precisione ottenibili con macchine di questo tipo rendono possibile anche il soddisfacimento dei requisiti di qualità previsti nel settore aerospace, oltre che i livelli di precisione necessari per la realizzazione di tubazioni la cui complessità della geometria viene mostrata in Figura 9.
Le macchine che realizzano la piegatura di tubi tramite calandratura vengono dette macchine curvatrici. Tali macchine, ad azionamento prevalentemente elettroidraulico, presentano il supporto per i rulli da un solo lato, come mostrato nella macchina in Figura 10, qualora siano destinate alla lavorazione di tubi di varia sezione, oltre che di barre e profilati. Le stesse macchine consentono, inoltre, la piegatura di tubi anche lungo traiettorie circolari complete, consentendo la realizzazione di geometrie ad avvolgimento elicoidale.
Le macchine che realizzano le lavorazioni di sagomatura dei tubi, descritte in precedenza, vengono dette macchine sagomatubi. L’evoluzione di questa tipologia di macchine consente l’integrazione delle suddette lavorazioni con quelle di asportazione di truciolo, vista anche la possibilità di comprendere la lavorazione di intestatura (e quindi di preparazione del tubo alla tornitura) prima accennata.
Tra le lavorazioni per asportazione di truciolo si ricordano la barenatura, la tornitura, la filettatura e la foratura. Come nel caso delle macchine piegatubi, anche queste vengono caratterizzate dall’implementazione di sistemi CNC, al fine di ottimizzare in velocità e posizionamento il cambio degli utensili. Anche per le moderne sagomatubi si ricorre ad un impiego sempre più esteso dei motori brushless, al fine di garantire elevati livelli qualitativi della lavorazione con conseguente risparmio sia in termini energetici che di tempi di fermo macchina. Anche in questo caso valgono le considerazioni fatte per le macchine piegatubi in relazione alla scelta opportuna degli accoppiamenti cinematici, necessari alla realizzazione dei sistemi automatici o semi automatici di carico e scarico dei tubi, di cui possono essere corredate.
In Figura 11 è mostrato una macchina sagomatubi concepita tenendo presente tutti questi aspetti in maniera ottimale e che comprende anche l’integrazione della lavorazione di idroformatura.
La compattezza del design della macchina mostrata in precedenza, in aggiunta agli accorgimenti relativi all’ergonomia ed alla praticità di accedere all’interfaccia di programmazione per l’operatore, ne fanno una soluzione estremamente interessante per l’upgrade di celle di lavorazione, fermo restando la predisposizione all’integrazione con sistemi rispondenti alle prerogative di digitalizzazione della produzione.
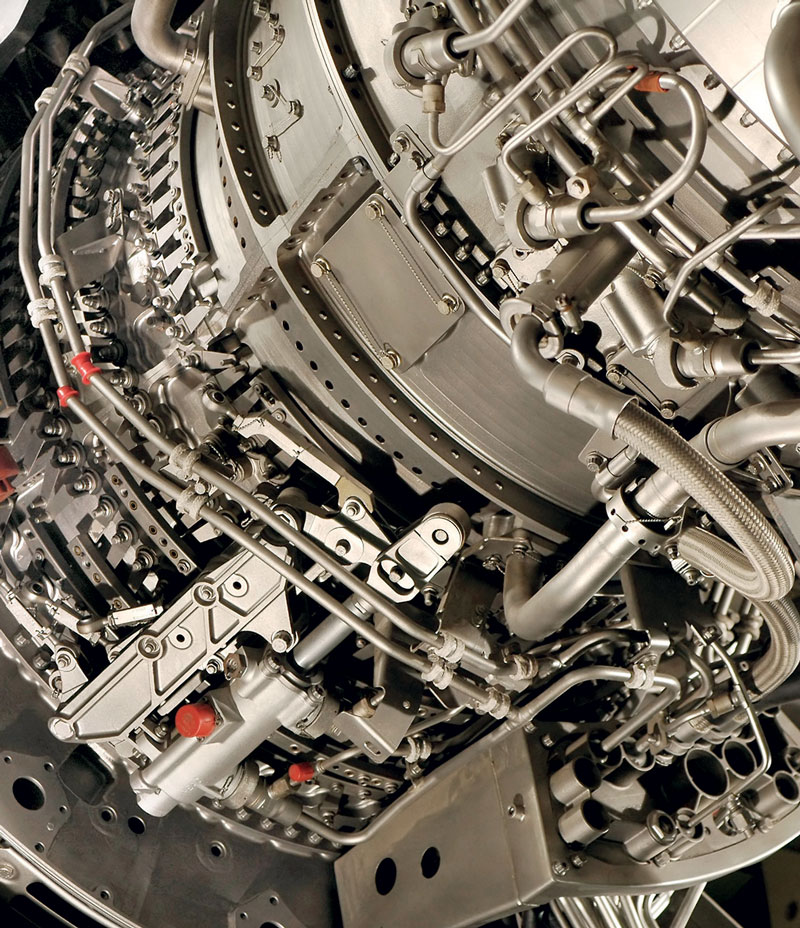
Il ruolo del fornitore di componenti
Un’attività complessa come la progettazione delle macchine per la piegatura e la sagomatura dei tubi, può trovare un valido supporto nei fornitori di componenti. È il caso di R+W, azienda leader nella produzione di giunti e alberi di trasmissione, in grado di mettere la sua esperienza a disposizione del progettista.
Nel settore delle macchine per la piegatura e la sagomatura dei tubi, R+W fornisce soluzioni specifiche per le esigenze di trasmissione della coppia. Oltre ai giunti di precisione a soffietto metallico della serie BK, R+W rende disponibili i giunti di trasmissione lamellare della serie LP.
I giunti BK a soffietto metallico, precisi e senza gioco, sono inoltre molto apprezzati per il basso momento di inerzia, la totale assenza di necessità di manutenzione, la durata praticamente infinita e soprattutto la totale affidabilità. I giunti lamellari LP, robusti e compatti, sono torsionalmente rigidi e praticamene privi di necessità di manutenzione; compensano i disallineamenti e trasmettono valori di coppia elevati. Oltre che nella deformazione dei tubi trovano applicazione anche nelle macchine da stampa, nelle pompe centrifughe, nei banchi prova e in molti altri segmenti. Realizzati in acciaio molto elastico, le lamelle compensano i movimenti angolari durante la rotazione rimanendo del tutto rigidi nella direzione della rotazione e in quella laterale. Privi di gioco grazie all’utilizzo di viti ad alta resistenza per il fissaggio delle lamelle e alla trasmissione della coppia mediante forza di attrito, non consentono micromovimenti e sono quindi particolarmente affidabili. Sono equipaggiabili con meccanismi di sicurezza per prevenire i danni in caso di sovraccarico.