Saldobrasatura robotizzata per la meccanica di precisione
Un ammodernamento periodico e oculato delle tecnologie produttive rappresenta un investimento fondamentale per un’azienda. Ben lo dimostra il caso di una cella di saldobrasatura a induzione sviluppata per Torneria Castiglioni con i robot Yaskawa: una soluzione compatta, versatile e capace
di garantire importanti ritorni già dal momento dell’acquisto.
di Mario Lepo
Siamo presso la Torneria Castiglioni, un’importante realtà mantovana che opera da circa trent’anni nel settore della meccanica di precisione destinata a vari settori applicativi, quali oleodinamica, automotive, raccorderie, piscine e parchi acquatici e illuminotecnica – solo per citarne alcuni.
L’azienda è sempre stata caratterizzata da un orientamento continuo all’innovazione tecnologica e una forte attenzione alle esigenze di una clientela in costante crescita. Tutto ciò ha portato Torneria Castiglioni ad adottare già dal 2016 un sistema produttivo fortemente orientato verso le tecnologie 4.0, integrando nei propri impianti soluzioni avanzate di robotica, sensoristica e adottando un avanzato sistema di interconnessione con il sistema gestionale, per un controllo costante del processo produttivo. Questo percorso evolutivo della produzione ha apportato notevoli miglioramenti in termini di efficienza lavorativa e qualitativa.
La ragione della nostra visita è legata a una cella robotizzata destinata ad attività di saldobrasatura a induzione il cui impiego contribuisce, non solo ad automatizzare il processo produttivo, ma anche a ottimizzarne i tempi produttivi consentendo una gestione efficiente sia delle lavorazioni di articoli in grandi serie, sia dello sviluppo di soluzioni personalizzate.
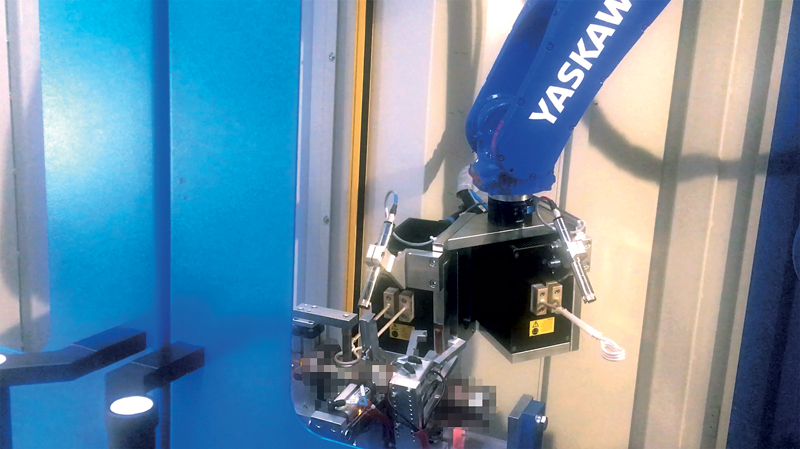
I tempi di lavorazione sono praticamente dimezzati
Cuore della cella è un robot antropomorfo a 6 assi Motoman GP25, equipaggiato con una doppia testa di saldobrasatura alimentata da un generatore a induzione CEIA. Questa soluzione fa sì che il pezzo da saldare possa venire gestito in un’unica lavorazione anche in caso siano necessari due distinti tipi di saldatura, senza bisogno di venire ripreso più volte. Il ricorso a un unico robot antropomorfo con due teste di saldatura anziché due distinte unità robotizzate crea immediate efficienze in termini di costi sia di acquisto che di gestione.
Inoltre, il robot Motoman GP25 è in grado di operare a velocità superiori agli standard, grazie a un controllo migliorato dell’accelerazione/decelerazione in tutte le posizioni. Il risultato è una notevole ottimizzazione del tempo di lavorazione dei singoli pezzi. Ma l’ottimizzazione in termini di tempi operativi non si limita a questo: la cella è stata dotata di una doppia postazione di saldatura, in modo da poter eseguire lavorazioni pendolate che permettono di gestire le attività di carico/scarico dei pezzi in tempo mascherato, abbattendo quasi totalmente i fermi legati a queste fasi. La produttività risulta così continua, con tempi di lavorazione praticamente dimezzati.
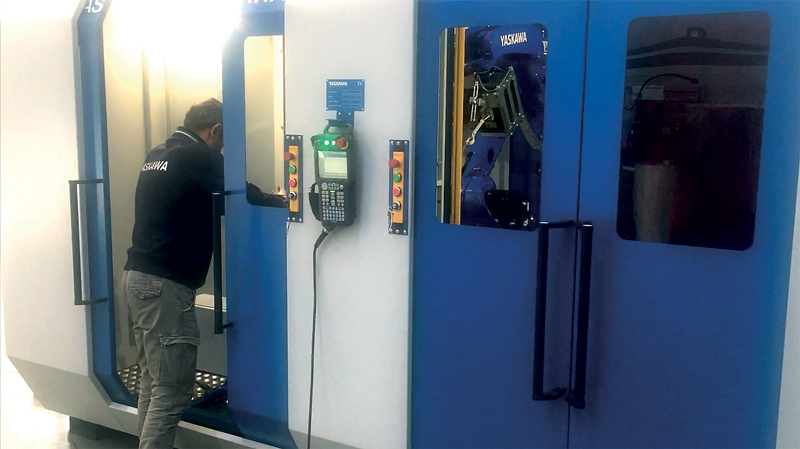
Compattezza e versatilità Plug&Play
Accanto alla riduzione dei tempi morti, la nova cella si distingue anche per un notevole contenimento degli ingombri. Tutti i suoi componenti sono infatti caratterizzati per la loro compattezza, a partire dai generatori CEIA, che combinano rendimenti energetici elevatissimi (> 95%) con dimensioni d’ingombro molto contenute e affidabilità garantita nel tempo.
Egualmente, il robot Motoman GP25 rappresenta il connubio ideale tra compattezza, velocità e precisione. Caratterizzato da un carico utile di 25 kg e uno sbraccio di 1.730 mm, il sistema ha richiesto uno spazio di installazione minimo: il design sottile del braccio ha reso possibile collocare il robot in prossimità di pezzi in lavorazione e ridurre al minimo l’interferenza con i dispositivi periferici, e il controllo YRC1000 garantisce un’elevata precisione della traiettoria e un’alta efficienza in un volume d’ingombro di soli 125 l.
L’operatore può comandare il robot in massima sicurezza dall’esterno della cella mediante il Teach Pendant, dotato di display in 3D per mostrare le posizioni del robot. Il touch screen permette il funzionamento intuitivo e quindi un facile movimento e scorrimento con il cursore.
Il risultato è una cella monoscocca completa, compatta e forcolabile. Una soluzione facilmente trasportabile e pronta a essere inserita in qualsiasi reparto produttivo del cliente e collegata con un meccanismo plug&play che ne renderà agevoli anche eventuali spostamenti futuri. Il tutto senza rinunciare a un’elevata versatilità di lavorazione, fondamentale per aggiungere valore alle produzioni di serie piccole e medie.
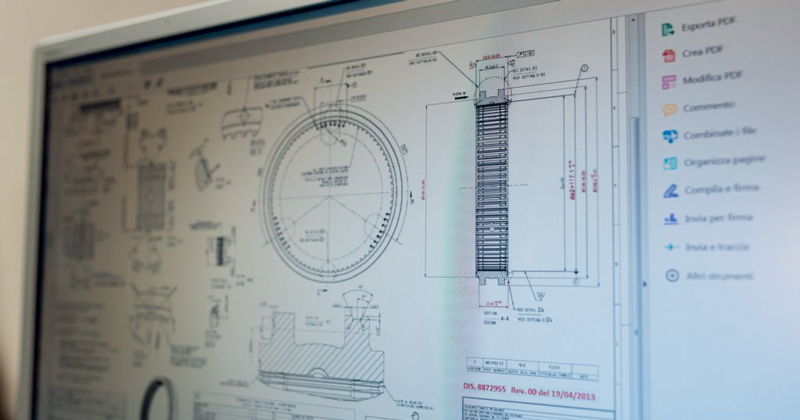
Piccolo e versatile
Con soli 730 g, il Teach Pendant del controllo YRC1000 è uno dei dispositivi di programmazione più leggeri della sua categoria. Il collegamento tra il manipolatore e il controllo avviene per mezzo di un solo cavo robot, con molteplici vantaggi: meno elementi di cablaggio, quindi riduzione di requisiti di usura e ingombro, diminuzione dei costi e minore spazio necessario per le parti di ricambio.
L’interfaccia utente supporta operazioni touch come smartphone e consente all’utente di simulare in 3D il movimento dei robot sullo schermo prima e durante l’esecuzione da parte del braccio robot reale. Il nuovo controller semplifica la manutenzione offrendo informazioni utili a gestire una manutenzione preventiva, accessibilità da remoto e potenti strumenti software per l’analisi e la comunicazione.