La customizzazione parte dai prodotti standard della gamma
Alessandro Redavide, Marketing & Communication Manager di Yaskawa Italia, nel corso del suo Tech Talks dei Robotic Days, ha parlato di standardizzazione e di come questa giochi un ruolo fondamentale per Yaskawa nel campo delle celle di saldatura robotizzate poiché la customizzazione viene realizzata a partire da prodotti e celle standard.
Parlando di saldatura robotizzata, qual è il vostro approccio al mercato e quali sono gli ambiti manifatturieri cui vi rivolgete? Può parlarci della filosofia costruttiva che vi guida in termini di sviluppo prodotto e quali sono i capisaldi tecnologici che portate avanti. Pensando alle celle, è ancora possibile parlare di gamma di prodotto standard o parliamo, per lo più, di soluzioni customizzate sulle specifiche esigenze del cliente?
Yaskawa Italia vanta un’ampia esperienza nel campo della saldatura, tanto da essere considerata il centro di eccellenza di Yaskawa in Europa per la saldatura a punti. Alla base della nostra attività c’è una filosofia che punta all’ottimizzazione del processo di saldatura intervenendo su due voci fondamentali: i tempi ciclo e i costi. Su questo secondo versante, la standardizzazione gioca anche oggi un ruolo fondamentale: è vero che le soluzioni, soprattutto quelle destinate a rispondere a esigenze di lavorazione più particolari, sono spesso custom, ma questa customizzazione viene realizzata a partire da prodotti e celle standard. In questo modo riusciamo a ottenere un’efficienza di costo veramente importante per i nostri clienti e una più rapida disponibilità delle soluzioni, riducendo anche i tempi di sviluppo e avvio delle applicazioni. Inoltre, l’impiego di postazioni di lavoro multiple – fondamentale per abilitare soluzioni di lavorazione in tempo mascherato – combinato con la rapidità dei nostri robot, ci permette di ottimizzare i tempi ciclo in modo veramente sensibile.
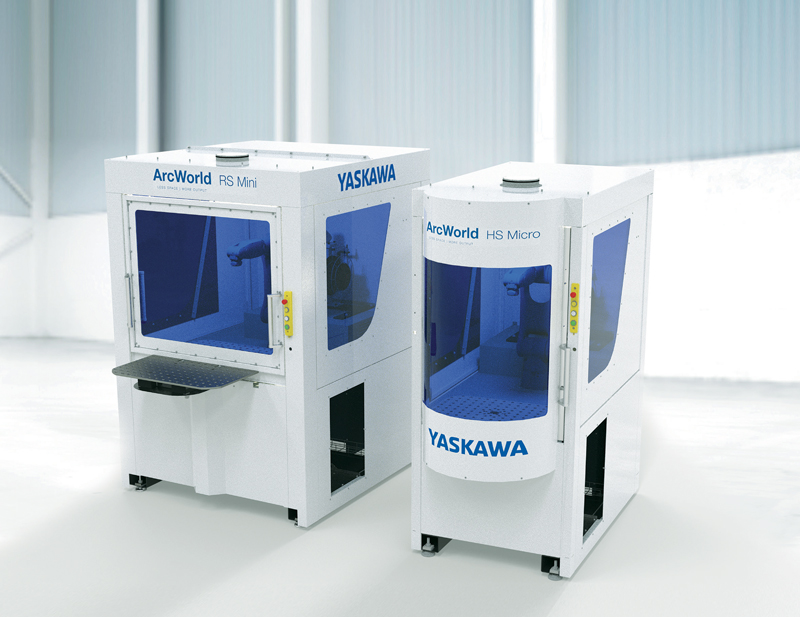
Qual è il vostro concetto di cella di saldatura? Penso per esempio al concetto di cella plug & play che sta prendendo sempre più piede sul mercato. Esiste una configurazione ottimale? Se si, quali sono le caratteristiche che deve avere?
Indubbiamente il concetto di cella plug & play è ormai un trend innegabile sul mercato, per svariati motivi. Basti pensare alla facilità di messa in opera: il sistema non richiede più una progettazione accurata dei singoli componenti e si presta a un agevole inserimento in impianti pre-esistenti. Inoltre una cella plug & play può essere facilmente spostata e riposizionata nel momento in cui si rendono necessarie delle revisioni al layout degli impianti produttivi. Da ultimo, una cella plug & play – sia essa completamente standard oppure parzialmente customizzata – è già ottimizzata per rispondere al meglio alle esigenze della specifica applicazione. Per questo, la cella deve indubbiamente comprendere non solo il robot e il sistema di saldatura, ma anche tutte le periferiche necessarie al corretto posizionamento del pezzo – generalmente con una doppia postazione per ridurre i tempi morti legati al carico/scarico dei pezzi da saldare, la parte di impiantistica elettrica e pneumatica, i sistemi di interfacciamento in rete e tutto quanto necessario al corretto funzionamento. Tutto ottimizzato per permettere la più efficace raggiungibilità delle parti da saldare e la maggior compattezza del sistema nel suo complesso.
Prendiamo in considerazione il robot; quali peculiarità deve avere dal punto di vista meccanico ed elettronico per essere sincronizzato al meglio con tutte le periferiche della cella ed essere aperto verso il generatore con cui, a prescindere dalla tecnologia, deve avere un’integrazione profonda per essere affidabili e produttivi?
È fondamentale la capacità di integrare i controlli di tutti gli assi, siano essi assi robot oppure assi esterni, come quelli del posizionatore, in un controller unico. Questo per noi è l’elemento veramente differenziante, in quanto permette di gestire al meglio la movimentazione reciproca di tutti gli elementi in gioco. Ne risultano non solo processi notevolmente più veloci e meno gravosi per l’operatore, ma anche un notevole aumento della flessibilità, tale da permettere di gestire programmi di saldatura omologhi su oggetti diversi, per esempio. Disporre di un posizionatore controllato direttamente dal controller del robot abilita inoltre lavorazioni ad assi vincolati, indispensabili per alcuni particolari processi. La gestione di tutti gli elementi con un unico controller permette poi di raccogliere e gestire in modo organico i dati di funzionamento e di processo relativi a tutti gli elementi che entrano in gioco nella lavorazione. Si ha così una visione completa della stessa e, al contempo, la possibilità di intervenire in modo più efficace per gestire eventuali modifiche di parametri o di ricette di lavorazione. Non a caso Yaskawa fa sì che tutto il necessario alla saldatura – dai robot di saldatura speciali, ai posizionatori e ai sistemi a portale, fino a soluzioni complete e personalizzate – possa essere gestito con un unico controller. I nostri controller robot permettono il coordinamento completamente sincronizzato di fino a 8 robot o 72 assi con un singolo dispositivo. Ma non solo: con il nuovo Machine Controller compatto MP3300iec RBT si abilita il concetto di “Singular Control”, ovvero una produzione gestita con continuità lungo l’intera linea, comprendendo robot, motion control, inverter e sistemi di I/O distribuiti.
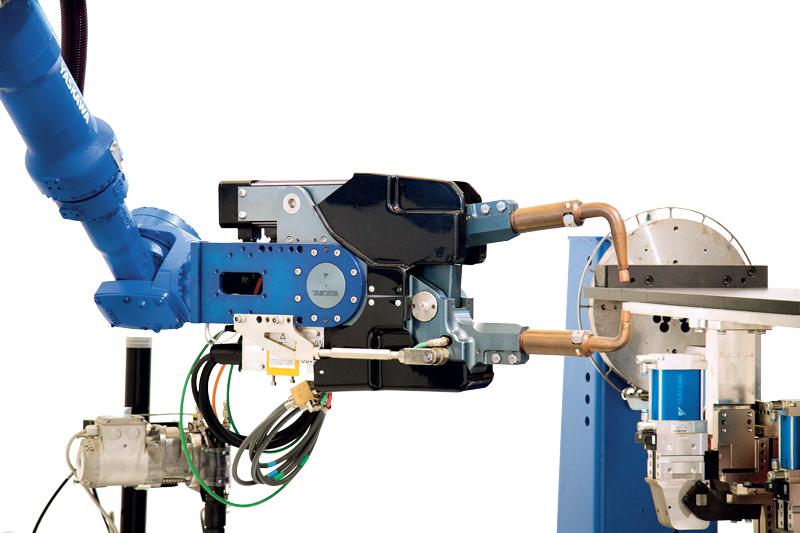
Pensando alla qualità del giunto di saldatura, in quali termini contribuisce e influisce il robot al raggiungimento di un risultato ottimale? In base a quali parametri applicativi viene scelta la tecnologia di saldatura più adatta?
Le caratteristiche di precisione e ripetibilità delle operazioni sono senza dubbio un fattore fondamentale per permettere al robot di offrire una costanza di qualità di saldatura superiore a quella manuale: abbattono, infatti, in modo totale il rischio di imprecisioni dovute generalmente all’elemento umano. Ma questo non è tutto. Ad avere un ruolo primario per garantire la qualità della saldatura sono anche tutte le soluzioni in grado di rilevare eventuali anomalie nei giunti di saldatura e adeguare in automatico i parametri di lavorazione. Si tratta di un elemento importante per perseguire l’efficientamento delle lavorazioni anche dal punto di vista economico: la capacità di rispondere dinamicamente alle piccole anomalie abbatte infatti il numero di rilavorazioni necessarie e accresce significativamente la qualità dell’output. Le soluzioni utili a questo scopo sono diverse e si basano su tecnologie di diversa natura: ad esempio, Yaskawa propone due diverse tecniche per ottenere lo stesso obiettivo, destinate a contesti operativi distinti. La prima è COMARC Arc Sensor, un sistema di tracciatura del giunto di saldatura basato sull’impiego di un deviatore di corrente e capace di verificare il reale andamento dei giunti mediante la misurazione delle variazioni d’intensità di corrente rilevate mentre il robot sta pendolando. Il robot può così seguire il percorso corretto del giunto, adeguando in modo dinamico il percorso programmato alle eventuali piccole difformità dei componenti o alle distorsioni provocate dal calore stesso impiegato durante la saldatura. Non richiedendo l’impiego di alcun dispositivo esterno ingombrante, questo dispositivo non interferisce con il design della torcia e la capacità di inserimento del robot in spazi ridotti. Tuttavia, questa soluzione presenta il limite di richiedere spalle di saldatura non inferiori ai 4 mm di spessore e materiali idonei dal punto di vista del loro comportamento in presenza di corrente elettrica. Per tutte le situazioni che non ricadono in questa descrizione un’alternativa altrettanto valida è rappresentata dal sistema segui giunto laser, basato su un sistema di visione abbinato alla torcia di saldatura. L’aspetto che accomuna entrambi i sistemi è la gestione tramite software, fondamentale per garantire l’integrazione funzionale della soluzione di saldatura nei sistemi di gestione dell’impianto complessivo.
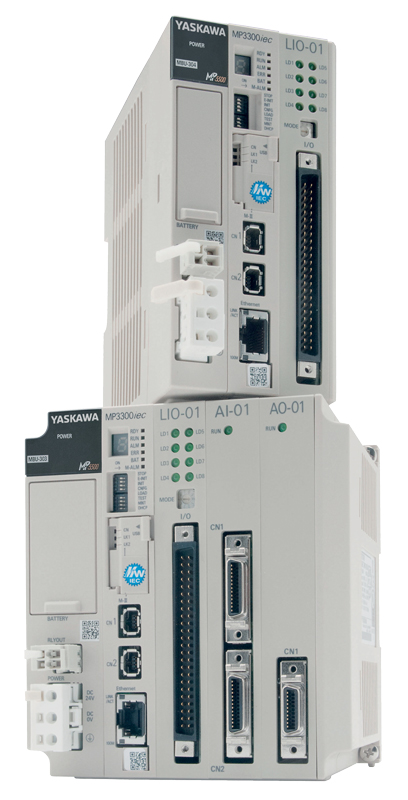
Focalizziamoci sull’operatore di una cella di saldatura robotizzata, quali competenze deve avere? Deve essere un saldatore skillato o al giorno d’oggi è “sufficiente” essere dei buoni programmatori? Lo stato dell’arte della tecnologia sopperisce alla mancanza cronica di saldatori provetti? E soprattutto, quando conviene prendere in considerazione di investire in una cella robotizzata da inserire nel proprio contesto produttivo?
Indubbiamente l’uso di una cella di saldatura robotizzata favorisce la semplificazione delle attività, ma non può sopperire in toto agli skill di saldatura dell’operatore. Sono questi infatti a far la differenza, risultando indispensabili per prendere alcune decisioni non delegabili al sistema robotizzato, quali per esempio la scelta dei gas più adatti o l’identificazione di eventuali procedure particolari da seguire. Per questo, all’interno dei nostri corsi di formazione non ci limitiamo a erogare formazione solamente sui sistemi tecnologici da noi prodotti, ma includiamo anche dei focus sul processo di saldatura nei suoi aspetti più tradizionali. Resta comunque innegabile la capacità delle celle robotiche di ridurre la complessità dei processi. Non a caso, in passato la scelta di implementare in azienda un sistema di saldatura robotizzato era vincolata principalmente alla dimensione dei lotti da lavorare, mentre ora a far la differenza sono altre logiche. Sono infatti sempre più diffusi sistemi di saldatura anche per quelle realtà che si trovano a gestire lotti piccoli ed estrema variabilità tra gli stessi. Gli elementi differenzianti che fanno propendere per l’adozione di una soluzione robotica sono piuttosto la qualità della lavorazione, la sua velocità, aspetti ergonomici di gestione di pezzi particolarmente pesanti o ingombranti e tutto ciò che può essere ricondotto a una più efficiente gestione dei processi.
Questa mattina si è parlato dei gas, delle loro proprietà e dei vantaggi nell’utilizzo ottimale. Può raccontarci un caso in cui siete riusciti a implementare il processo grazie al gas o in alternative in quali processi credete che il gas potrebbe essere veramente determinante nell’appoggiare la transizione in corso verso efficienza e automazione?
Indubbiamente l’impiego del gas corretto è fondamentale per un processo di saldatura efficace e qualitativo. Come è ben noto, i gas per la saldatura si raggruppano in due grandi famiglie: i gas inerti, particolarmente indicati per i processi MIG, e i gas attivi, più idonei ai processi MAG.
Alla base della saldatura vi sono due elementi fondamentali: gas e filo, ovvero tipo di lega. È quindi sicuramente importante usare il gas giusto in funzione del materiale e del processo. Ad esempio, per saldare oggetti in alluminio serve un processo MIG e, dunque, un gas inerte, mentre i migliori risultati di saldatura di parti in ferro (acciaio al carbonio) si ottengono con una miscela attiva, fatta di Argon e CO2.
La scelta del giusto gas è particolarmente significativa in relazione ad alcuni materiali, particolarmente difficili da saldare, come i metalli zincati. Come è noto, infatti, lo zinco tende a evaporare in modo significativo e questo crea una turbolenza che origina pallini di saldatura. Il risultato è dunque una saldatura poco pulita. Per ovviare al problema si può usare CO2 pura, che richiede un minore calore e, dunque, riduce l’evaporazione dello zinco.
La saldatura robotizzata è un’applicazione adatta alle caratteristiche di un cobot?
Capiamo le perplessità, ma ci sono alcuni aspetti tipici dei cobot che spiegano probabilmente in modo molto chiaro l’interesse che queste soluzioni stanno riscuotendo anche nel mondo della saldatura, nonostante le prestazioni di un cobot siano innegabilmente diverse da quelle di un robot industriale e l’applicazione di saldatura nel suo complesso sia tra le più difficili da gestire in modo totalmente collaborativo. Rispetto ad un grande robot tradizionale, infatti, un cobot assicura maggior versatilità, minore ingombro e un investimento economico più contenuto. Il tutto combinato a una modalità di programmazione e gestione sempre più intuitiva. Risultano quindi particolarmente interessanti per chi si approccia per la prima volta all’impiego di un robot. Se poi il robot non è un collaborativo puro, ma piuttosto un ibrido cooperativo come quelli della nostra famiglia HC, capaci di offrire performance da industriale e di regolare la sua operatività in funzione della reale presenza dell’operatore, a questi plus si aggiunge anche quello dei tempi ciclo estremamente ridotti. Questa è la filosofia alla base della nostra cella di saldatura cooperativa Weld4Me.