La saldatura robotizzata? Ve la spiego io!
A tu per tu con Maurizio Ravelli, Presidente di Tiesse Robot che in occasione della giornata dedicata alla saldatura robotizzata dei Robotic Days ci ha raccontato la filosofia costruttiva e lo stato dell’arte Kawasaki Robotics in questo particolare segmento della robotica industriale, dall’alto di chi, dal 1980 a oggi, ha sviluppato e innovato questo processo e può vantare oltre 1.300 le isole realizzate e consegnate in Italia e nel mondo.
Parlando di saldatura robotizzata, qual è il vostro approccio al mercato e quali sono gli ambiti manifatturieri cui vi rivolgete? Può parlarci della filosofia costruttiva che vi guida in termini di sviluppo prodotto e quali sono i capisaldi tecnologici che portate avanti. Pensando alle celle, è ancora possibile parlare di gamma di prodotto standard o parliamo, per lo più, di soluzioni customizzate sulle specifiche esigenze del cliente?
Vorrei spendere qualche minuto per una breve introduzione della Tiesse Robot che rappresenta dal 1976 una realtà nel panorama della automazione Italiana e oggi un leader sul mercato nei processi robotizzati. Per Tiesse Robot parlare di approccio è un po’ limitativo. La saldatura ad arco è nel nostro DNA aziendale dato che le prime applicazioni risalgono al 1977 con soluzioni dedicate per poi intuire nel 1980 con la prima applicazione di un robot idraulico Unimation che il mercato si sarebbe spostato verso i sistemi robotizzati. A oggi, dal 1980 sono oltre 1.300 le isole realizzate e consegnate in Italia e nel mondo. Già prima della fine degli anni 80 era stata messa a catalogo una serie di posizionatori standard e quindi di soluzioni per portate fino ai 500 – 700 kg; oggi arriviamo a considerare isole standard soluzioni con posizionatori fino a 2.000 kg. La nostra filosofia costruttiva, basata su un background consolidato e unico, è quella di garantire un prodotto durevole nel tempo e con caratteristiche meccaniche e tecnologiche che garantiscano le performance promesse al cliente. Le celle standard sono oggi ancora una base consolidata del mercato ma è pur vero che ora le soluzioni richieste si sono spostate verso impianti medio – grandi (nel senso di dimensioni e pesi dei pezzi da processare) la cui personalizzazione è sempre più spinta.
Come esempio posso dire che per un cliente che produce pianali ferroviari in Alluminio, è stata affiancata alla saldatura robotizzata una stazione sempre robotizzata con sorgente laser di pulizia dei giunti da saldare per rimuovere gli ossidi in modo da garantire una saldatura ottimale. Stiamo affrontando una richiesta di un importante gruppo che richiede un processo tecnologico di saldatura e lavorazione meccanica nella stessa cella o richieste di celle con posizionatori aventi portate da 25 a 40 Tons. Sono sempre più richieste anche celle miste di manipolazione pezzi e saldatura Jigless) che permettono di comporre e saldare pezzi senza mascheraggi.
Qual è il vostro concetto di cella di saldatura? Penso per esempio al concetto di cella plug & play che sta prendendo sempre più piede sul mercato. Esiste una configurazione ottimale? Se si, quali sono le caratteristiche che deve avere?
Il sistema plug & play è giocoforza applicabile a soluzioni compatte ove sia possibile pre-allestire robot, posizionatore, saldatrice, talvolta gruppo aspirazione e filtrazione e apparecchiatura elettrica in una base unica e quindi interconnessa e dotata anche di telecamera di visione area di saldatura che richiede quindi solo l’allacciamento elettrico, gas e aria. Stante che anche i robot più piccoli oggi sono dotati di software di saldatura stiamo progettando mini celle che devono coprire quei processi di saldatura di piccoli particolari.
Prendiamo in considerazione il robot; quali peculiarità deve avere dal punto di vista meccanico ed elettronico per essere sincronizzato al meglio con tutte le periferiche della cella ed essere aperto verso il generatore con cui, a prescindere dalla tecnologia, deve avere un’integrazione profonda per essere affidabili e produttivi?
Oggi ormai qualsiasi sia il generatore è collegato al controllore del robot tramite dei bus di campo e con possibilità di una interfaccia diretta visibile sulla tastiera di programmazione dello stesso che evidenzia i parametri principali del processo. Devo anche dire che è sempre più frequente utilizzare tabelle “Job” dove si posso raggruppare le WPS e richiamare le singole posizioni da programma robot con una facile gestione. Questo, in particolare, è funzionale quando si usano sensori laser di inseguimento e misurazione geometria del giunto di saldatura che può quindi accedere a delle posizioni della tabella in modo semplice. Naturalmente gli assi dei posizionatori sono gestiti come assi robot e spesso gli stessi controllori anche nelle versioni supercompatte sono già predisposti per potere gestire e ricevere 2- 3 assi esterni per arrivare a 16 assi con appositi cabinet di contenimento azionamenti.
Dal punto della configurazione meccanica la concezione del robot di saldatura ha conosciuto qualche anno fa l’introduzione del robot dotato di polso cavo che permette quindi un passaggio interno e coassiale del fascio cavi facilitando accessibilità in spazi ristretti ma anche introducendo qualche limite dovuto all’allestimento del gruppo trascina filo a bordo robot nella libertà di movimento degli assi 2 e 3.
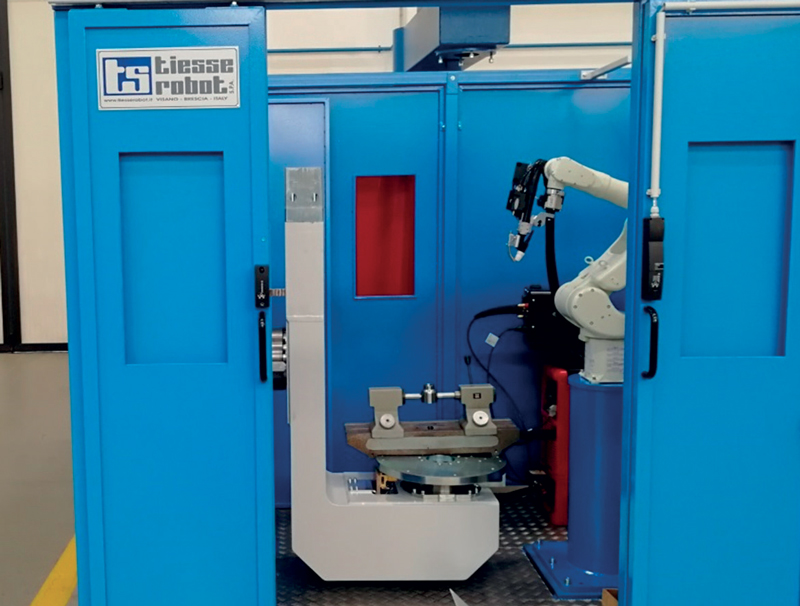
Pensando alla qualità del giunto di saldatura, in quali termini contribuisce e influisce il robot al raggiungimento di un risultato ottimale? In base a quali parametri applicativi viene scelta la tecnologia di saldatura più adatta?
La scelta del processo di saldatura è parte dell’analisi del problema che il cliente ci sottopone; ci sono casi in cui il tutto è definito dalle specifiche della richiesta. Ci sono casi border line (esempio Tig- Plasma) dove la richiesta di finitura del giunto può essere eseguita e ottenuta con diversi processi. Ci sono casi in cui il fornitore suggerisce al cliente possibili alternative in funzione della produzione richiesta, deformazioni termiche da limitare e via dicendo come nel caso della saldatura laser che a velocità di processo maggiori comporta però un investimento sul processo e sulla preparazione e mascheraggi superiore e quindi non sempre giustificato dalla maggiore produttività. La combinazione di parametri quali apporto termico, produttività, preparazione dei pezzi permette di adottare o sconsigliare determinati processi.
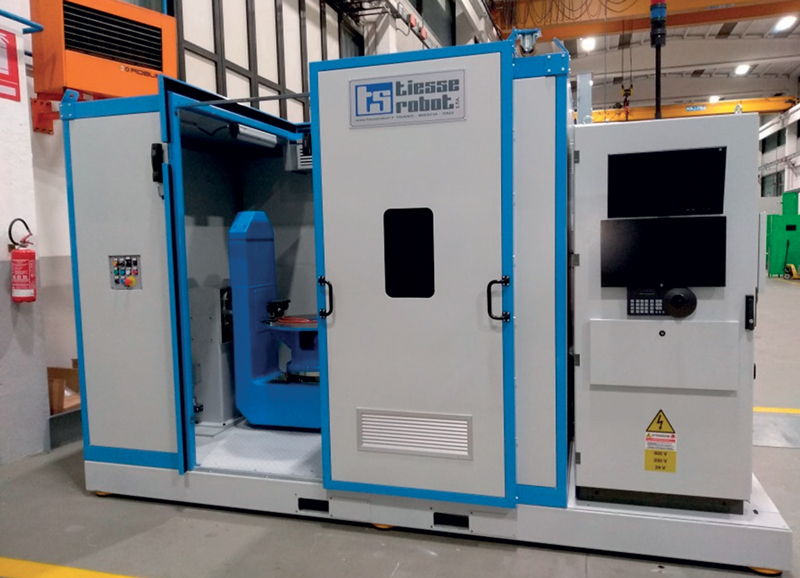
Focalizziamoci sull’operatore di una cella di saldatura robotizzata, quali competenze deve avere? Deve essere un saldatore skillato o al giorno d’oggi è “sufficiente” essere dei buoni programmatori? Lo stato dell’arte della tecnologia sopperisce alla mancanza cronica di saldatori provetti? E soprattutto, quando conviene prendere in considerazione di investire in una cella robotizzata da inserire nel proprio contesto produttivo?
L’operatività di un’isola robotizzata, in particolare, di saldatura, è diversa dalle isole di manipolazione. Esiste una parte di processo e una parte di gestione dell’isola. La prima penso sia demandata a chi deve eseguire la programmazione dell’isola che include anche la scelta dei parametri di processo, quindi ci deve essere da parte dell’addetto una conoscenza dello stesso. La gestione operativa non richiede questo skill e deve essere facilitata dal fornitore dell’isola con soluzioni adeguate a semplificare le operazioni di start up, ripristino ciclo e riallineamento automatico della torcia in caso di urto etc.
Non dimentichiamoci che l’uso di determinati sensori di ricerca e inseguimento del giunto (laser etc.) richiedono per la programmazione una conoscenza un po’ più strutturata di come il sensore stesso interagisce con la logica del movimento del robot. Sono sempre più usati anche pacchetti software di programmazione Off Line che per mettono una programmazione separata dall’uso della cella di saldatura. Anche qui l’integrazione con i sensori laser di ricerca e inseguimento del giunto potenziano e semplificano l’esecuzione dei programmi.
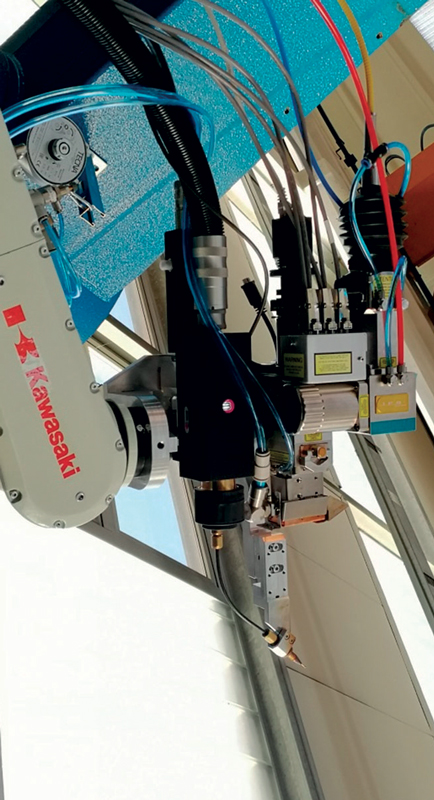
Questa mattina si è parlato dei gas, delle loro proprietà e dei vantaggi nell’utilizzo ottimale. Può raccontarci un caso in cui siete riusciti a implementare il processo grazie al gas o in alternative in quali processi credete che il gas potrebbe essere veramente determinante nell’appoggiare la transizione in corso verso efficienza e automazione?
Naturalmente la scelta di un gas è parte del processo per potere garantire dei risultati ottimali anche in termini di presentazione del cordone di saldatura oltre che di penetrazione quindi la scelta da parte del cliente o del fornitore dell’impianto di un fornitore qualificato è indispensabile.
Per esempio in un’applicazione fatta in Sud Africa abbiamo raggiunto sulla saldatura di steam channels su un serbatoio in acciaio inox una velocità di circa 1.800 mm/min su cordone da 3 mm anche grazie al gas scelto dal cliente col proprio fornitore qualificato.
La saldatura robotizzata è un’applicazione adatta alle caratteristiche di un cobot?
Personalmente sono estremamente cauto sull’uso dei robot collaborativi nelle celle di saldatura per ragioni di adeguatezza delle norme di sicurezza, e a oggi per quanto ne sia a conoscenza tutte le funzioni specifiche dei robot di saldatura non sono implementate sui robot collaborativi che vediamo proposti in isole molto semplici ma che alla fine dovranno essere configurate come isole tradizionali e quindi non ne capisco l’utilità.