Automatizzare la piegatura per rendere tutta l’azienda efficiente
Con Davide Gastaldi di Bruno Perano e Paolo Mason di TRUMPF scopriamo come l’automazione della fase di piegatura, oltre a importanti vantaggi in termini di sicurezza e continuità della produzione, garantisca efficienza e qualità anche nei processi a valle come, ad esempio, la saldatura.
A valle della fase di taglio, il ruolo delle piegatrici è sempre più strategico, oltre che vero ago della bilancia parlando di efficienza di processo. In particolare, il tema della piegatura automatizzata è argomento di strettissima attualità. Come approccia questo tema TRUMPF e come lo declina all’interno della sua gamma di prodotto?
Paolo Mason: “TRUMPF propone due tipologie di celle allestibili con caratteristiche personalizzabili di automazione: la TruBend Cell 5000 e la TruBend Cell 7000. Concepita per essere modulare, la TruBend Cell 5000 può essere realizzata con una misura diversa a seconda delle necessità del cliente: possiamo realizzare impianti che arrivano a 16 metri di binario con piegatrici fino a 320 t con peso massimo movimentabile pari a 150kg compreso di pinze. La TruBend Cell 5000 può essere inoltre dotata dell’impianto cambio utensili automatico e di due diversi sistemi per la correzione dell’angolo di piega: ACB Wireless, che misura e corregge gli angoli attraverso utensili con dischi tastatori, e con il sistema ottico ACB Laser. Massima flessibilità anche nei sistemi di presa pezzo con soluzioni a ventosa, con magnete e con pinza. Importante sottolineare come la macchina possa essere utilizzata facilmente anche in modalità completamente manuale se i nostri clienti ne hanno l’esigenza. Molto veloce e produttiva, TruBend Cell 7000 occupa un’area di 21 m2 ed è una soluzione ideale per piccoli lotti e pezzi di dimensioni ridotte (500×380 mm). Questa cella è dotata anche di LoadMaster Bend, un sistema che carica i fogli di lamiera sulle piegatrici durante il tempo mascherato utilizzando un sensore lamiera integrato che ne garantisce il posizionamento ottimale. Parlando di automazione è importante sottolineare come TRUMPF, grazie alla partnership con STARMATIK, può offrire anche soluzioni completamente customizzate sulle esigenze del cliente”.
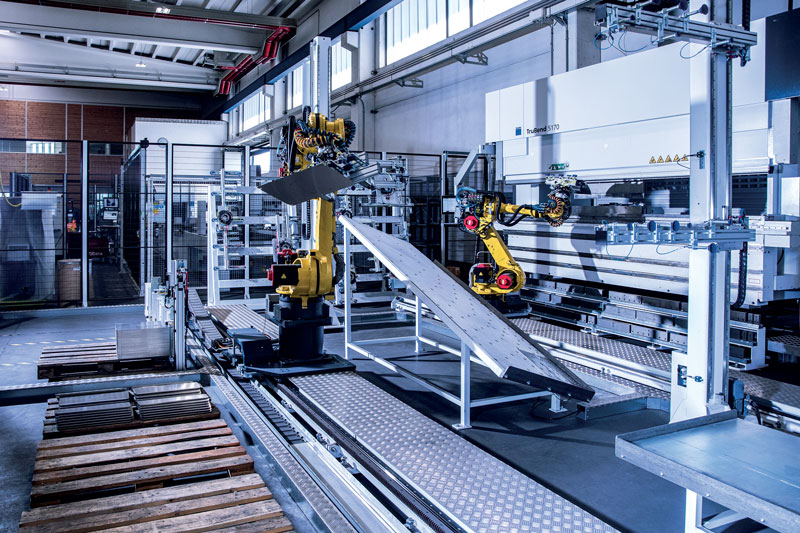
Parlando di automazione nella piegatura, una testimonianza autorevole è certamente Bruno Perano di Peveragno in provincia di Cuneo, realtà che da tempo ha scelto TRUMPF e le sue soluzioni. Con Davide Gastaldi, membro della famiglia Perano, a cui chiedo di parlarci dell’attività dell’azienda e di raccontarci le esigenze produttive per cui si sono rivolti a TRUMPF approfondendo proprio il tema della piegatura.
Davide Gastaldi “L’azienda Bruno Perano è nata negli anni Novanta come una piccola carpenteria a produzione familiare, attiva come contoterzista in vari settori. Nel primo periodo, quando sono arrivato io in azienda, eravamo in pochi e la lavorazione della lamiera veniva effettuata con cesoie, scantonatrici e piegatrici assolutamente manuali, come anche l’assemblaggio e la saldatura. Nel 2000 Bruno Perano ha deciso di puntare sulla saldatura robotizzata e ci siamo accorti che, per non avere difficoltà sulle linee automatizzate, dovevamo garantire pezzi sempre precisi e conformi. Servivano quindi attrezzature affidabili e performanti, esigenza che ci ha portato ad acquistare la nostra prima piegatrice TRUMPF che, a conferma della qualità, è ancora impegnata nella realizzazione di particolari in officina. La piegatrice è stata successivamente affiancata da una macchina laser. TRUMPF, proprio per potere gestire in automatico le saldature e gli assemblaggi di pezzi mantenendo così al massimo la conformità delle sagome. Da quel momento è iniziata una collaborazione che si è sviluppata in tutti questi anni di sviluppo industriale: oggi abbiamo 4 celle di piegatura con Bend Master, una TruBend Cell 7000, un impianto customizzato realizzato con STARMATIK, e da un anno e mezzo, abbiamo inserito una pannellatrice TruBend Center 7030.
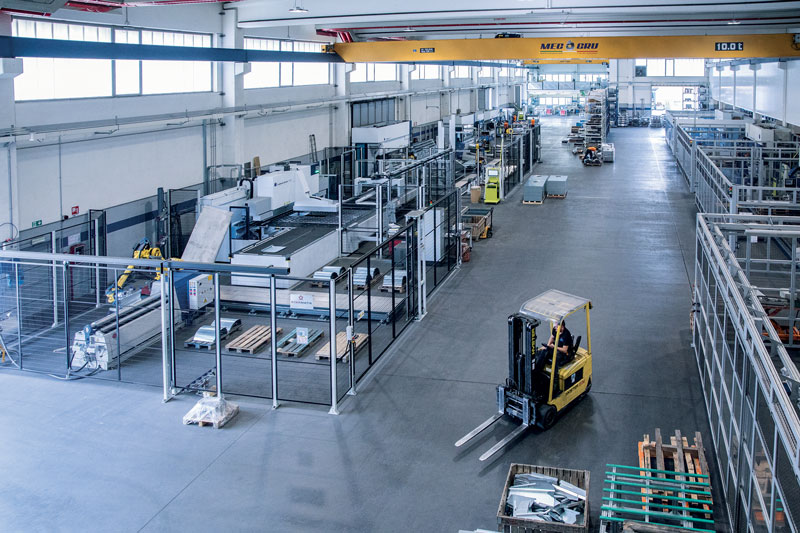
Scendendo più nel dettaglio vorrei capire quali sono state le esigenze di piegatura sottoposte a TRUMPF e con quali soluzioni il costruttore ha risposto in virtù del fatto che in officina sono state installate più celle robotizzate differenti fra loro. Penso ad esempio alla diversa dimensione dei pezzi.
Davide Gastaldi “La dimensione dei pezzi da lavorare è stato il tema principale intorno a cui abbiamo sviluppato il nostro parco macchine. Quando abbiamo deciso di investire nella prima cella robotizzata era il 2007 e, con la collaborazione di TRUMPF, abbiamo cercato di analizzare quali pezzi gestivamo in quel periodo. Sulla base di quello studio, la soluzione più indicata era BendMaster 60 perché ci permetteva gestire tutti pezzi, sia medio-piccoli che medio-grandi. Col passare degli anni e con l’aumentare della produzione c’è stata l’esigenza di integrare gli impianti e siamo passati a un impianto con BendMaster 150, quindi in grado di lavorare pezzi più pesanti, fino a 150 kg, e dimensioni sicuramente maggiori (ad esempio abbiamo lavorato fogli di lamiera da 3 m per 1,5 m). In un secondo tempo ci siamo resi conto di quanti pezzi piccoli gestivamo e che dovevamo piegare ancora manualmente, perché non adatti a questi impianti. Abbiamo quindi installato la cella TruBend Cell 7000, una macchina veloce e sicura che permette di gestire pezzi anche molto piccoli (arriviamo a pezzi di qualche centimetro di grandezza). È una macchina completamente autonoma, l’attrezzaggio è infatti automatico, così come il cambio pinza, e la programmazione si realizza totalmente offline in ufficio. L’operatore non deve fare altro che caricare il programma e osservare il primo pezzo.
Oltre a essere molto precise, queste macchine TRUMPF sono molto sicure: utilizzando questi impianti automatizzati garantiamo anche maggiore sicurezza per gli operatori, perché evitiamo sia di far movimentare grandi lastre manualmente, sia di dover avvicinare troppo le mani agli utensili di piega come avviene quando si lavora pezzi molto piccoli.
Infine, da un anno e mezzo a questa parte abbiamo inserito anche la pannellatrice TruBend Center 7030: per noi è stata una novità perché ha una tecnologia completamente diversa da quella che eravamo abituati a gestire anche a livello di programmazione e gestione. Vediamo questa tecnologia come una soluzione che si abbina alla piegatura: realizziamo su questa macchina sia pieghe standard, in base alla disponibilità delle macchine, ma anche abbiamo sviluppato pezzi specifici per essere gestiti sulla pannellatrice. La macchina è stata installata con carico e scarico robotizzato, poi integrato con un impianto STARMATIK che consente di portare i pezzi anche alla fase di calandratura, rendendo l’impianto automatizzato, dal quale escono pezzi finiti”.
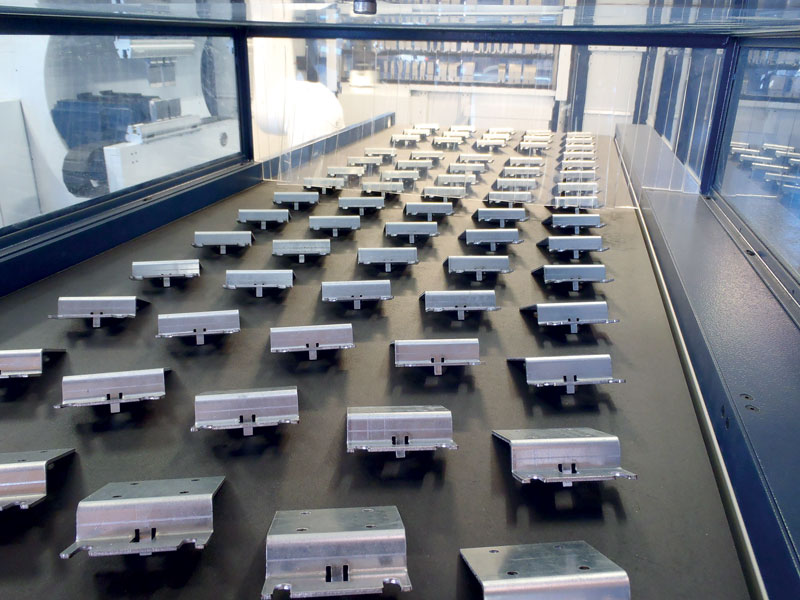
L’efficienza della piegatura, in un mercato fatto di piccoli lotti e di campionature, passa ormai necessariamente dall’abbattimento dei tempi morti e, di conseguenza, dal riattrezzaggio automatico della piegatrice. Come si coniuga questo tipo di necessità con il concetto di cella robotizzata che nell’immaginario, invece, rimanda soprattutto a una produttività piuttosto spinta di particolari ripetitivi?
Davide Gastaldi “Inizialmente anche noi avevamo questo approccio: quando nel 2007 abbiamo investito in automazione era perché avevamo la necessità di gestire lotti con numeri importanti. Va detto che è normale che l’automazione spaventi un po’ quando si è abituati a fare lavorazioni in modo manuale, però oggi i software per la programmazione della piegatura fanno la differenza: sono tutti gestiti da ufficio e permettono di lavorare completamente offline. Questo è un grande vantaggio, perché hai uno strumento che ti permette di programmare mentre la macchina produce e che è stato reso molto semplice e intuitivo: sono utilizzabili, infatti, anche da chi non ha una grande esperienza di piegatura. Il software è in grado di proporre la sequenza ottimale di piega utilizzando l’attrezzatura disponibile in quel momento. In questo modo, la gestione del piccolo lotto è più semplice, anche grazie ai sistemi di cambio pinza e cambio utensili automatici”.
Paolo Mason “Quando si parla di automazione, lo scoglio principale da superare è il timore della complessità della programmazione di questi impianti. Invece, come spiegava Davide, oggi parliamo di programmi molto semplici e intuitivi da utilizzare. Per questo diciamo che è possibile utilizzare in maniera più proficua le competenze dei propri operatori grazie alla maggiore sicurezza di processo e alla possibilità di lavorare in turno non presidiato.
Tante aziende pensano anche che l’automazione abbia senso solo con grandi lotti, invece non è così, come è evidente visitando la Bruno Perano. Infine, le soluzioni TRUMPF in uso qui evidenziano anche la nostra capacità di fornire non solo soluzioni standard ma, anche grazie alla collaborazione di STARMATIK, impianti customizzati a 360° intorno alle esigenze del cliente”.
Parlando sempre di piegatura robotizzata: quali vantaggi ha portato all’attività quotidiana di Bruno Perano? Penso per esempio alla precisone di piega che si ripercuote positivamente sulla saldatura robotizzata posta a valle della piega?
Davide Gastaldi “Oggi abbiamo sette robot di saldatura ed è fondamentale che siano alimentati sempre con pezzi conformi, altrimenti si fermerebbe la linea. La piegatura automatizzata ci dà questa garanzia, mentre è normale che un operatore, magari dopo ore che sta piegando lo stesso pezzo, possa perdere concentrazione e mettere in linea pezzi non conformi. Lo stesso discorso vale anche, se non di più, per la saldatura tradizionale: in questo caso un pezzo non conforme è molto pericoloso perché la mano umana riesce a combinare lo stesso gli accoppiamenti, ma, invece di scartare il singolo pezzo, si finisce per dover scartare tutto il saldato con oneri maggiori. Un altro vantaggio è sicuramente la continuità di produzione che garantisce l’automazione: su questo tipo di linee con grandi numeri è un elemento molto importante”.
Paolo Mason “Tutti gli impianti in uso in Bruno Perano sono dotati di sensore dell’angolo di piega, dalla pannellatrice alla piegatrice robotizzata, fino alle due celle. In questo modo, si riesce a garantire un processo che, fin dal pezzo 1, sia preciso e controllato”.