Muovere la robotica verso nuovi orizzonti
Le applicazioni in cui si muovono i robot KUKA sono quasi infinite, dall’automotive, all’assemblaggio, alla chirurgia. Recentemente, l’azienda sta esplorando il settore dei Consumer Goods, con soluzioni robotizzate per material handling e palletizzazione leggera, ma anche robotica mobile per l’intralogistica e robotica collaborativa. Alberto Pellero, Director Strategy and Marketing di KUKA Roboter Italia, durante il suo intervento ai Robotic Days del marzo scorso, ha parlato delle novità applicative e di prodotto che l’azienda sta portando avanti.
KUKA non ha certo bisogno di presentazioni; ciò nonostante, partirei con il chiederle di parlare del vostro approccio al mercato della robotica e di spiegarci qual è la vostra filosofia e quali sono i capisaldi tecnologici che portate avanti attraverso una gamma di prodotto che so essere completa
e piuttosto articolata?
Il nostro proposito è quello di fornire una scelta chiara per chi deve fare automazione intelligente, sempre vicina agli esseri umani e facile da usare; questo è molto importante, specialmente con i recenti sviluppi di robotica collaborativa e mobile. Come si sta muovendo KUKA nel mondo dell’automazione e dell’industria? Ci presentiamo con cinque divisioni: Systems, che fa impianti per il settore automotive, per operazioni di saldatura e incollaggio; Robotics, di cui KUKA Roboter Italia fa parte, che sviluppa robot e prodotti correlati, quali software e posizionatori; la ditta Swisslog, acquisita cinque anni fa, che rappresenta due divisioni all’interno gruppo, Swisslog e Swisslog Healthcare che si occupano rispettivamente di magazzini automatici e intralogistica, la prima, e di automazione negli ospedali e farmacie, la seconda; infine, la divisione Cina, non verticale per quanto riguarda i mercati applicativi ma lo è dal punto di vista geografico, che è molto importante perché il mercato cinese rappresenta circa il 60% dell’assorbimento dei robot. I focus applicativi di KUKA, invece, sono: automotive/Tier1, elettronica, general industry, e-commerce/retail, medicale e consumer goods. Dove ci concentriamo in particolare come divisione robotica? Fondamentalmente su quattro filoni: robot, quindi cerchiamo di avere un portafoglio prodotti il più vasto possibile e che abbracci qualsiasi settore; mobilità e intralogistica, che per noi è estremamente importante; la mobilità applicata alla produzione, quindi sistemistica e integrazione, utilizzando non più il concetto di linea tradizionale, ma quello di matrix manufacturing; infine, tutto il mondo dell’Industria 4.0 e ciò che noi chiamiamo digital service, quindi connettività, analisi dati e machine learning.

Stando ai dati elaborati dal Gruppo Statistiche di SIRI e dal Centro Studi UCIMU, nel nostro Paese la maggior parte dei robot è assorbita da applicazioni piuttosto “tradizionali” come il material handling e la palletizzazione, che rimandano al settore dei beni di consumo o Consumer Goods. È un ambito che vi ha visti particolarmente attivi nell’ultimo anno e dove, forse, la pandemia ha ulteriormente favorito gli investimenti in robotica. È così? Può raccontarci quali novità avete presentato per questo segmento?
Parlando di trend della robotica, c’è stata una discesa nel 2020 sugli investimenti. Nel 2021 vediamo invece fermento, almeno nel primo quarto dell’anno, anche in Italia, la quale ha tantissimi system integrator che installano i propri impianti prevalentemente all’estero. Il trend immaginato per i prossimi anni, fino al 2025, secondo l’IFR dovrebbe riportare il consumo di robot al valore pre-Covid, con un tasso aggregato di crescita del 10,4%. Sono certo che riusciremo a superare questo particolare momento industriale, e sicuramente nei prossimi anni vedremo una crescita molto forte per quanto riguarda il consumo di robot. Alcune statistiche parlano di un aumento dell’11% di consumo di robot in alcuni specifici settori industriali. Tra questi non è compreso l’automotive, anche se avrà ancora un grosso volume di business; invece, supereranno la soglia dell’11% i settori del Food & Beverage, del Metal & Machinery e del farmaceutico. Se si vanno a vedere i risultati dei primi tre quarter del 2020 in Cina, cioè il mercato più importante per la robotica come accennavo prima, l’automotive è sceso del 20%, mentre l’elettronica e l’elettrodomestico sono saliti del 17%. Per quanto riguarda il settore dei beni di consumo, invece, qual è il trend? Le statistiche parlano di una crescita positiva nei prossimi quattro anni, che si aggira in media al 5%. Possiamo affermare, quindi, che il volume di business sta aumentando: se la produzione è in salita, di conseguenza è necessaria più automazione, motivo per cui KUKA dall’anno scorso si sta interessando maggiormente a questo comparto. KUKA si occupa prevalentemente di robotica di processo, per esempio abbiamo installato robot in un impianto Nestlé in cui compiono diverse operazioni lungo la linea di produzione: ci sono quelli che spalmano le creme, in questo caso si tratta di un handling primario a contatto con il cibo; altri si occupano della parte di picking e inscatolamento, per la palletizzazione a strati o a scatole; infine è presente robotica per la logistica, cioè magazzini automatici, depalletizzazione e case picking, quindi la formatura di pallet diretti ai supermercati. La nostra offerta, per il settore del Consumer Goods, si è aperta anche a un’applicazione abbastanza nuova, quella della pallettizzazione leggera: un robot muove una scatola alla volta, cosa che fino a poco tempo fa era appannaggio di un operatore umano, in quelle linee di produzione dove non è richiesta una capacità produttiva molto alta. I robot KUKA, inoltre, sono anche in grado di eseguire una pallettizzazione mista, dove la macchina compone un bancale con prodotti molto diversi per forma e dimensione, grazie all’end effector modulare.
La robotica di servizio e la robotica mobile sono dei temi di grande attualità, che nell’epoca del digital manufacturing si stanno sempre più affermando nelle nostre fabbriche, soprattutto pensando all’intralogistica fra i reparti produttivi. Che tipo di soluzione proponete in questo segmento? Quali sono i vantaggi che si possono sperimentare, ma soprattutto qual è la realtà tipo che può trarre il massimo beneficio dall’adozione dei robot mobili? Può fare degli esempi?
La robotica mobile, come dicevo, è uno dei quattro pilastri fondanti dell’offerta KUKA. Abbiamo iniziato tanti anni fa con l’acquisizione di una ditta che si chiamava Omnimove, che sviluppava dei carrelli autonomi con una portata dalle 7 t in su, pensati per il settore ferroviario e aerospaziale. KUKA poi ha fatto sua questa tecnologia, realizzando degli AGV che vengono applicati sia per l’intralogistica sia per trasportare robot in un contesto produttivo. Ora abbiamo lanciato il nuovo piccolo AGV da 600 kg di portata estremamente compatto. La nostra offerta è molto ampia, partiamo da piccoli AGV da 200 kg su cui generalmente montiamo dei robot, ai classici AGV da 1,5 t che muovono i telai delle auto, fino ad arrivare a quelli fino a 100 t di portata. Quando vengono uniti AGV e cobot, si entra nel mondo della robotica vera e propria, che può essere utilizzata per molte applicazioni, quali la manipolazione di circuiti elettronici, forature, rivettature e tanto altro. Per esempio, abbiamo fornito a Lamborghini la nostra soluzione KMR, cioè KUKA Mobile Robot, per compiere avvitature sotto scocca di 230 bulloni di vario tipo: questo robot mobile sostituisce gli operatori in un lavoro faticoso e anti-ergonomico, mentre questi hanno più tempo per svolgere altre mansioni.
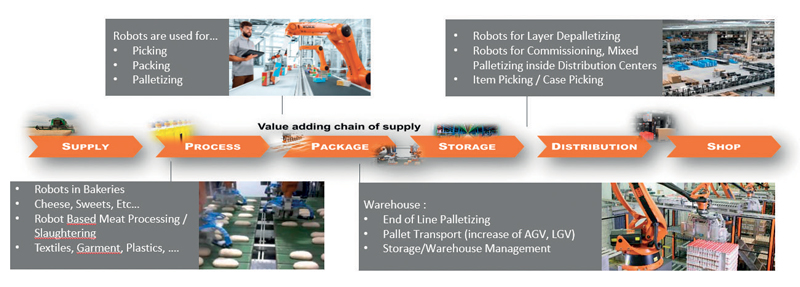
Un’ultima curiosità sempre sui robot mobili: sono di facile programmazione e implementazione? Esistono degli strumenti che ne facilitano l’integrazione all’interno dei contesti produttivi in cui sono inseriti?
Oggi si parla molto della facilità di programmazione dei robot, di conseguenza deve essere semplice anche il sistema di robotica mobile. Apparentemente potrebbe sembrare molto più complesso, pensando alla presenza del robot a bordo, ma in realtà non è così. La caratteristica peculiare dal punto di vista hardware nei nostri sistemi mobili sono le ruote con rulli folli, che permettono di spostarsi lateralmente o girare senza l’utilizzo di ruote sterzanti: in questo modo non vengono rovinati i pavimenti industriali, ed è possibile muoversi in spazi angusti senza una difficoltà di programmazione, poiché questo sistema possiede dei laser scanner a bordo che monitorano la presenza di persone e permettono di rimodulare la traiettoria. In termini di architettura software, se sono presenti più sistemi mobili all’interno di un contesto produttivo allora entra in gioco un fleet manager, che deve essere in grado di parlare con un ERP, un MES aziendale o HMI realizzati ad hoc, e, tramite collegamenti wireless, gestire una flotta di robot mobili per poi andare a realizzare quella che è la navigazione autonoma. Quindi, non è necessario spiegare al robot mobile la traiettoria che deve compiere, ma semplicemente dargli il punto di partenza e quello di arrivo. Questo permette anche una facile integrazione nei reparti produttivi, perché non è necessario un cambio di layout: l’AGV si auto-gestisce negli spostamenti.
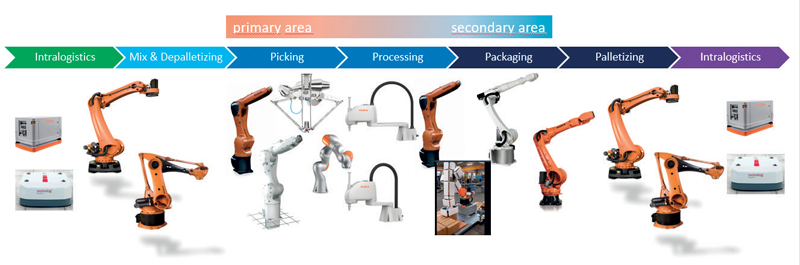
Un altro tema di attualità è la robotica collaborativa la cui potenzialità applicativa è fuori discussione. In passato KUKA ha fatto molto per lo sviluppo di questo segmento ma so che qualcos’altro bolle in pentola. Può darci qualche anticipazione e parlarci della filosofia che vi guida nello sviluppo di questa particolare gamma di robot? Quali saranno le peculiarità dei nuovi cobot Kuka?
Abbiamo consegnato il primo LWR nel 2008 all’Istituto Italiano di Tecnologia: ai tempi si poteva vendere solo ai centri di ricerca e università, perché non esistevano ancora delle normative chiare e nessuno si voleva prendere la responsabilità di far lavorare le persone affianco a un robot. Oggi i cobot si sono diffusi in molti settori, anche in quello del Consumer Goods. Quello che io sto notando è che la raffinata e avanzata tecnologia dei cobot è spesso “sprecata”, perché si ritrova a compiere operazioni che non la richiedono. I robot collaborativi sono erroneamente nominati quando bisogna realizzare una cella aperta: in quel caso c’è uno spazio di lavoro condiviso, dove basterebbe la presenza di sensori, laser scanner e software a bordo di un robot industriale, in modo tale che questo si fermi o rallenti nel momento in cui si avvicina l’operatore e riparti o acceleri quando va via. Quando c’è una vera e propria collaborazione tra robot e umano, quindi nel caso in cui sia necessario lavorare sullo stesso oggetto in contemporanea o fare un posizionamento, allora bisogna utilizzare un cobot; questa però è una piccolissima nicchia di mercato. L’ultimo cobot arrivato nella famiglia KUKA è LBR iisy, che abbiamo presentato ad Automatica del 2018 quando era ancora un concept. All’edizione virtuale di Hannover Messe 2021, presentiamo il nuovo controller iiQKA, un pacchetto di soluzioni digitali per i cobot. LBR iisy è da intendersi nell’accezione di robotica collaborativa di cui parlavo prima, cioè un utensile semplice da programmare e utilizzare; l’interfaccia teach pendant ha anche visualizzazioni in 3D, cosa che semplifica ulteriormente l’utilizzo. Ha sei assi, tutti dotati di torque sensor, quindi possiede tutte le opzioni di cedevolezza e sensibilità. Per quanto riguarda la velocità, il nostro LBR iiwa può arrivare fino a 2 m/s, che è la velocità massima anche per i tradizionali robot industriali. Ci andiamo a scontrare, a queste velocità, con la normativa che impone un movimento non in prossimità, ma con una coesistenza di un operatore all’interno di una cella di 650 mm/s per arrivare fino a 250 mm/s nell’applicazione effettivamente collaborativa dove ci possono essere dei rischi. Potenzialmente, quindi, il cobot può andare molto veloce, ma non lo può fare durante un’applicazione collaborativa. In ogni caso, io non farei lavorare un robot collaborativo, anche se protetto da recinzioni, al massimo della sua velocità, perché non è nato per quello: per operazioni ad alta velocità, vanno bene i robot industriali tradizionali, decisamente più solidi ed eventualmente sensorizzabili.
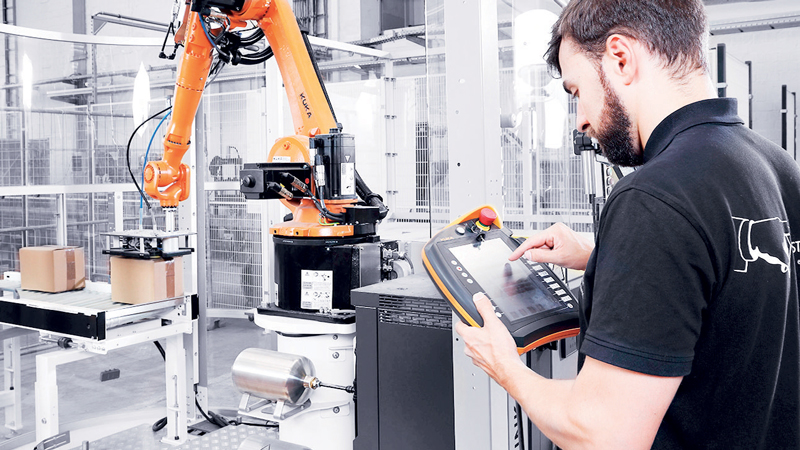
Quali vantaggi e quali svantaggi avete sulla concorrenza rispetto ai robot collaborativi attualmente? E quali sono le applicazioni nel settore medicale, come per esempio nella chirurgia? Nell’ambito della piegatura robotizzata, invece, avrebbe senso sostituire le rotaie fisse a pavimento con degli AGV o robot mobili, ed eventualmente fino a che carico al polso?
Quello della robotica collaborativa è un panorama estremamente popolato da molti marchi validi e affidabili, che hanno riempito un mercato che prima non esisteva. Se vogliamo parlare di svantaggi, posso dire che uno di questi è che al momento non abbiamo un robot low-cost, ma lo avremo con l’uscita ufficiale sul mercato di LBR iisy. Avere una proposta low-cost, infatti, è importante: se un’azienda ha intenzione di inserire un robot affiancato a un operatore, deve poter avere un ritorno dell’investimento il più veloce possibile. Il nostro LBR iiwa è performante, sensibile, con sette gradi di libertà, sette giunti e torque sensor, ma a volte è troppo: in alcuni casi basterebbe un controllo dell’impedenza dei motori all’interno del controller per evitare una collisione. Questo svantaggio, però, può diventare anche un vantaggio: è il robot più sensibile del mercato al momento, ed è ideale per applicazioni delicate come il sensitive assembly. Per l’ambito medicale, altro settore delicato, abbiamo una vasta gamma di soluzioni, da un sistema di movimentazione con un grosso robot da 150 kg dotato di sorgente per fare terapie radio (l’ospedale Fatebenefratelli ne possiede un esemplare), fino ad arrivare ai robot per la riabilitazione e a quelli chirurgici, per esempio il nostro LBR Med è utilizzato anche nella riduzione osteoarticolare per tagliare tessuti con il laser. Per quanto riguarda la sostituzione di rotaie fisse con un AGV, mi sento di sconsigliarlo: queste rotaie, essendo fissate a terra, garantiscono una precisione, una compattezza e una ripetibilità non eguagliabili da un AGV.