Vi spiego come migliorare il processo di saldatura con la giusta miscela di gas
I Robotic Days hanno visto una giornata interamente dedicata al tema della saldatura robotizzata, era quindi naturale parlare dei gas e delle miscele utilizzati in questo processo. È stata SIAD, main sponsor dell’evento, dalla voce del Project Manager Nicola Sala, a raccontarci quale ruolo hanno
i gas industriali e come possono migliorare, in termini sia di ottimizzazione della produzione che di costi, i processi di saldatura.
Quando vi abbiamo proposto di sponsorizzare la giornata dedicata alla saldatura robotizzata, avete accettato subito con entusiasmo per parlare di gas e miscele per la saldatura. Direi, quindi, di partire parlando del ruolo e dell’importanza che i gas e le miscele di gas hanno per un processo di saldatura robotizzato. Abbiamo scelto di sponsorizzare questa giornata dei Robotic Days per rimarcare il ruolo dei gas nella saldatura, e per condividere degli spunti sul loro utilizzo e sui vantaggi ottenibili grazie all’uso di una miscela piuttosto che un’altra. Ma prima di parlare delle possibilità di implementazione grazie al ruolo attivo dei gas nel processo, iniziamo dalla base: a cosa serve il gas in saldatura? Si dice che si utilizzi per proteggere la saldatura, ma cosa significa veramente? Proteggiamo la saldatura dall’aria, o meglio da ciò che è contenuto nell’aria, ed è quindi opportuno identificare quali sono quelli che chiamo i tre “nemici” dell’acciaio: acqua (umidità nell’aria), ossigeno, e il terzo è “un gruppo”, ovvero gli inquinanti (per esempio zolfo e idrocarburi). Questi tre nemici sono poi i valori che vengono monitorati, secondo la norma 14175 che fornisce la classificazione dei gas di protezione.
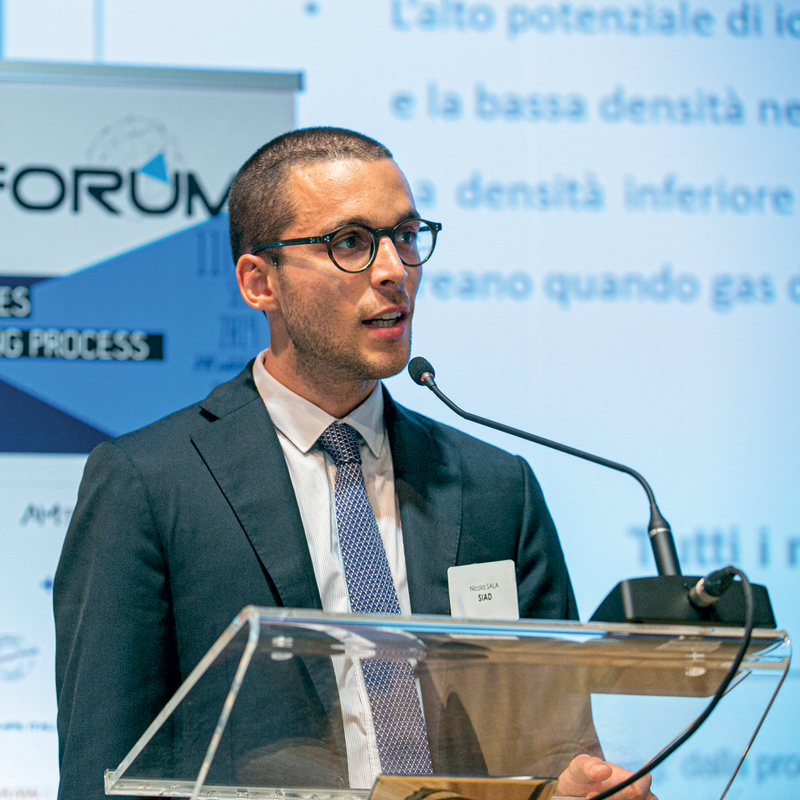
Abbiamo detto che, oltre a proteggere il processo di saldatura, gas e miscele svolgono un ruolo attivo. Può parlarcene?
Entrando più nel dettaglio, scopriamo che in realtà il gas di protezione non è solo uno, ma ci sono ben sei gas che possono essere impiegati in miscela nei processi di saldatura: argon, azoto, anidride carbonica, ossigeno, elio e idrogeno. La scelta di quali utilizzare e delle rispettive percentuali dipende dalle proprietà chimiche e fisiche di quest’ultimi in relazione al materiale, al processo e al tipo di lavorazione. Per quanto riguarda la protezione, si possono utilizzare sia argon che azoto, entrambi gas inerti. Ma perché si utilizza il primo rispetto al secondo (se non in particolari lavorazioni)? Perché l’azoto non conserva la proprietà di gas inerte alle alte temperature, causando nitrurazioni. Per questo motivo si utilizza l’argon come base di tutte le miscele di saldatura per processi MIG/MAG, o come unico gas nel caso di processi TIG. La penetrazione è un altro fattore fortemente influenzato dal gas; in questo caso entrano in gioco quelli che vengono definiti gas attivi, come ossigeno e anidride carbonica. Questi, nella saldatura MIG/MAG, vengono addizionati all’argon in percentuali variabili, solitamente incrementate in relazione allo spessore e alla penetrazione richiesta. Perché usiamo questi gas? Essendo appunto “attivi”, all’interno dell’arco elettrico, le molecole si dissociano e riassociano grazie alle alte temperature: questo processo genera energia addizionale che favorisce una penetrazione maggiore, e soprattutto fa in modo che la penetrazione non sia concentrata nel centro del cordone di saldatura, andando a creare il cosiddetto cordone a “testa di chiodo”.
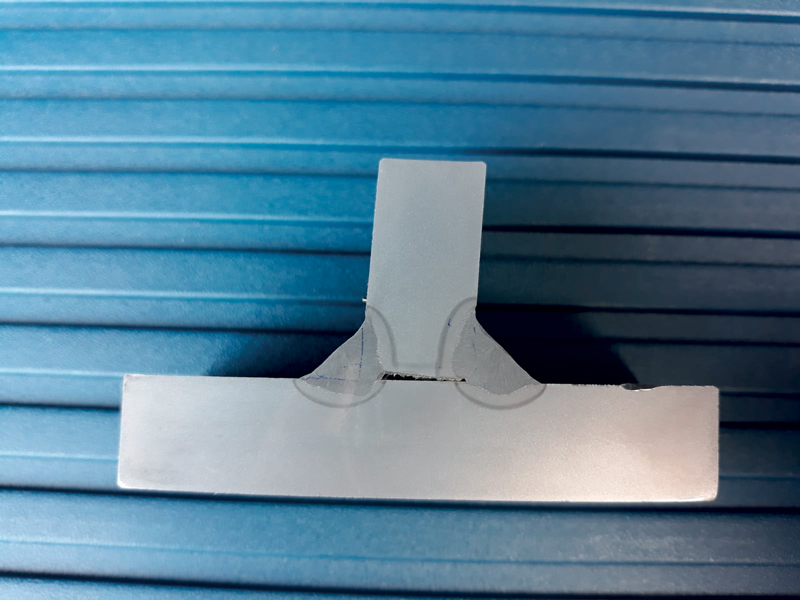
In che modo gas e miscele possono “implementare” o “migliorare” un processo di saldatura robotizzato?
Introduciamo due ulteriori gas che svolgono un ruolo fondamentale quando andiamo a parlare di implementazione delle performance: elio e idrogeno. Entrambi possiedono un’elevata conducibilità termica. Questo significa permettere che l’energia trasmessa dall’arco elettrico arrivi, attraverso il gas di protezione, al bagno di saldatura in maniera più fluida e diretta. Ciò permette di evitare di dover “inviare” eccessiva energia e che questa energia si disperda lateralmente andando a incrementare la zona termicamente alterata e i colori di rinvenimento. La trasmissione più diretta e uniforme dell’energia comporta anche una maggiore e più uniforme penetrazione all’interno del cordone di saldatura. Ma qual è la differenza sostanziale tra questi due gas? Se pensiamo all’idrogeno ci viene subito in mente la sua caratteristica principale: l’infiammabilità. Per questo motivo, in saldatura, non viene mai utilizzato in addizione all’argon in percentuali maggiori del 5-7%. Questo significa che beneficiamo dell’implementazione del processo dovuto alla conducibilità termica non tanto dall’idrogeno, ma soprattutto dall’elio. L’idrogeno, però, ha il vantaggio di possedere la proprietà cosiddetta riducente, ovvero la capacità di legarsi alle particelle di ossigeno presenti nel bagno di saldatura e, anche grazie alla propria leggerezza, trasportarle al di fuori del bagno di saldatura. Come risultato, si avranno quindi dei cordoni di saldatura completamente disossidati e più lucenti.
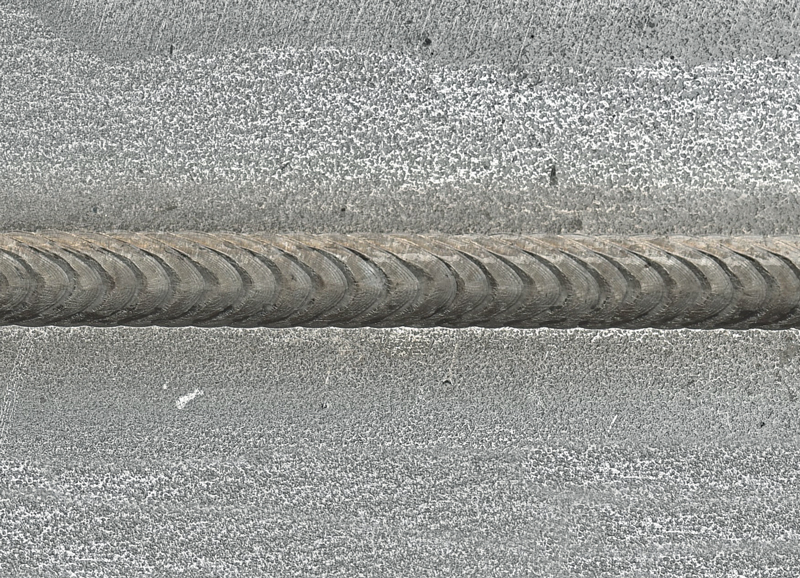
Come si concretizzano poi queste proprietà dei gas nella vostra gamma di prodotto che proponete al mercato?
Finora abbiamo fantasticato molto sulle infinite possibilità di utilizzo dei gas, anche se noi produttori abbiamo standardizzato le miscele. Ne abbiamo create 30-40, ognuna delle quali dà il miglior risultato per un determinato processo e/o uno specifico prodotto. Per esempio, abbiamo confrontato una saldatura che utilizza la miscela standard di 97,5% di argon e 2,5% di anidride carbonica con una composta da 82% di argon, 3% di anidride carbonica e 15% di elio. Abbiamo notato che con la seconda, grazie al minor apporto termico complessivo e alla minore porosità derivata dall’elevata conducibilità termica dell’elio, è possibile completare la saldatura in due passate anziché tre, e che l’aspetto del cordone è più piacevole esteticamente.
Rimanendo in tema saldatura a filo, pensiamo invece a cosa potrebbe accadere se non utilizziamo un gas attivo insieme all’argon. Se viene effettuata una saldatura su acciaio con argon 100%, risulterà difettosa. L’unico caso in cui si può utilizzare argon schietto è con gli allumini, mentre con gli acciai vediamo la formazione di cordoni a testa di chiodo, cioè un difetto di saldatura; la corrente elettrica non basta per fare una penetrazione adeguata, poiché si focalizza al centro del cordone. Se all’argon, invece, vengono aggiunti anidride carbonica o ossigeno anche se in piccole percentuali, si ha una penetrazione più uniforme del cordone di saldatura. Nella saldatura TIG, è invece l’Idrogeno il gas più interessante, per esempio la miscela di argon 95% e idrogeno 5% permette un miglioramento della profondità e dell’ampiezza di penetrazione. La scelta del gas, quindi, può avere degli effetti positivi o negativi sulla produzione. Non dovrebbe mai essere considerato un elemento secondario o di poco conto.
È possibile dimostrare che l’uso delle miscele che proponete abbia un vantaggio economico, non solo metallurgico?
Per farlo torno all’esempio della miscela di argon ed elio, dove siamo riusciti a utilizzare due passate di saldatura invece che tre, portando quindi un risparmio in termini di costi, nonostante il prezzo più elevato per l’acquisto dell’elio. Il gas, in realtà, è uno dei costi più bassi all’interno del processo di saldatura, anche quando sono rari o difficili da estrarre, come l’elio appunto: mediamente, il gas rappresenta il 4% delle spese. La manodopera o i sistemi di gestione saldatura, nel caso di robot e automatismi, rappresentano invece l’85% dei costi di saldatura. Se riusciamo a ridurre quest’ultima percentuale, pur aumentando il costo del gas, alla fine la spesa totale dell’intero processo è inferiore rispetto all’utilizzo di una miscela senza l’elio.
Ecco perché è importante scegliere la miscela migliore per le proprie esigenze, e perché si tratta di un elemento da considerare a monte.
In chiusura, avrei due curiosità.
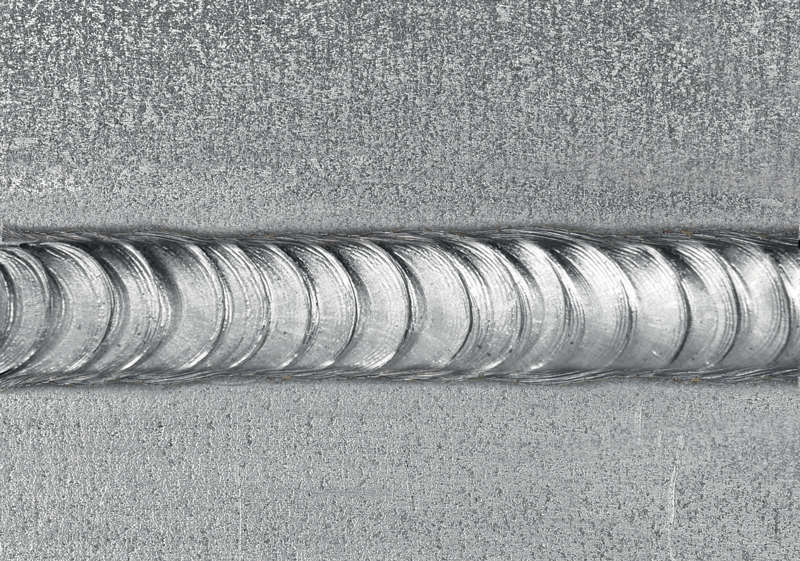
La prima molto banale: come vengono prodotti i gas? La seconda riguarda invece le miscele che, da quanto ho capito, nascono per dare delle risposte concrete a un’esigenza applicativa ben precisa; è corretto?
Ogni gas ha la sua storia e viene prodotto in modo diverso. Partiamo dai tre gas principali che produciamo, cioè ossigeno, argon e azoto. Questi vengono estratti dall’aria attraverso un processo che si chiama frazionamento molto simile alla distillazione: il frazionamento dell’aria viene effettuato sfruttando i diversi gradi di evaporazione dei gas. Noi liquefiamo l’aria, poi, grazie al riscaldamento di questa, riusciamo a estrarre i gas, sapendo che questi evaporano a una temperatura diversa. L’anidride carbonica è la protagonista dei processi di saldatura, e deriva da impianti di recupero o da sintesi, come rifiuti organici o acciaierie. L’elemento più costoso è, come già detto, l’elio che, essendo un elemento molto volatile, non può essere estratto dall’aria, ma da giacimenti. Questi si trovano in diverse parti del mondo, e il suo prezzo si comporta in modo simile a quello del petrolio, quindi è soggetto al mercato e alla situazione geopolitica. L’idrogeno, cioè il gas più “chiacchierato” del momento, è diviso in diversi “colori”. L’idrogeno “grigio” è quello che crea più inquinamento perché deriva da processi di sintesi come lo steam reforming dove viene estratto dal metano sintetizzandolo, formando anche anidride carbonica che non viene recuperata. Se, invece, si riesce a recuperare l’anidride carbonica, come succede nei nostri impianti, l’idrogeno viene definito “blu”. Esiste poi un’altra tipologia di idrogeno, che viene chiamato “verde”, il quale deriva completamente energie rinnovabili. Viene ricavato da elettrolisi, quindi dalla sintetizzazione dell’acqua tramite energia elettrica; la fonte di energia elettrica dev’essere rinnovabile, ovviamente. Le nostre miscele rispondono tutte a richieste applicative precise. La domanda che ci facciamo, e che ci viene spesso fatta, è come supportare l’avanzamento tecnologico con un elemento che esiste da migliaia di anni e che viene utilizzato nel campo della saldatura da secoli. La nostra risposta è rappresentata dall’ampia offerta di miscele di gas SIAD, unita ad un supporto consulenziale ed operativo costante a tutte le aziende che adottano le nostre soluzioni ed innovazioni.