Una saldatrice robotizzata, non un robot di saldatura!
Forte della partnership strategica con Panasonic, Roboteco Italargon costituisce l’anello di giunzione tra il costruttore nipponico e il cliente, occupandosi di tutte le fasi di studio e implementazione relative al processo di saldatura di un manufatto. In occasione delle giornata dedicata alla saldatura robotizzata dei Robotic Days, Tommaso Lanza, Responsabile Innovazione Meccatronica di Roboteco Italargon, ci ha accompagnato alla scoperta della filosofia All In One e della saldatrice robotizzata Panasonic.
Parlando di saldatura robotizzata, qual è il vostro approccio al mercato e quali sono gli ambiti manifatturieri cui vi rivolgete? Può parlarci della filosofia costruttiva che vi guida in termini di sviluppo prodotto e quali sono i capisaldi tecnologici che portate avanti. Pensando alle celle, è ancora possibile parlare di gamma di prodotto standard o parliamo, per lo più, di soluzioni customizzate sulle specifiche esigenze del cliente?
Quella tra Roboteco e Panasonic è una sinergia che si sviluppa ormai da diversi anni. Roboteco nasce nel 1988 con l’obiettivo di integrare l’esperienza già presente sul campo della saldatura con la robotica e l’automazione e nel 1991 inizia la partnership strategica tra Roboteco e Panasonic. Nel 2017 è avvenuta la fusione con Italargon, altra azienda storica del settore. Oggi siamo un’azienda che continua a unire l’istinto all’innovazione con l’inossidabile esperienza nel settore della saldatura robotizzata e automatica. I 30 anni di stretta collaborazione con Panasonic sono sicuramente l’aspetto più importante della nostra realtà. Partendo dal know how specifico di costruttore di saldatrici manuali, Panasonic ha creato una vera e propria saldatrice robotizzata, secondo il concetto dell’All In One. Tawers (per la saldatura ad arco) e LAPRISS (per la saldatura laser) non sono semplici prodotti ma piattaforme tecnologiche che costituiscono una vera fusione tra il manipolatore e il generatore di saldatura. Il concetto di fusione ha portato a strumenti sofisticati, affidabili e incentrati sui processi che permettono di raggiungere risultati sorprendenti. Noi come Roboteco-Italargon costituiamo l’anello di giunzione tra il costruttore e il cliente, occupandoci di tutte le fasi di studio e implementazione relative al processo di saldatura di un manufatto. Grazie ai nostri specialisti della saldatura e all’esperienza costruita riusciamo a spaziare su svariati campi della saldatura ad arco e laser su svariati tipi di materiali e accoppiamenti. Oltre all’attenzione che mettiamo nella messa a punto dei processi, cerchiamo di ottimizzare la macchina o l’impianto per la tipologia produttiva del cliente, riuscendo quindi a supportare sia la piccola e variegata produzione artigianale, sia la produzione a elevata produttività del settore automotive. Per quel che riguarda le celle pensiamo che le nostre soluzioni debbano quindi partire dall’ascolto del cliente; sta a noi poi capire se una configurazione “standard” può garantire la produttività richiesta o se invece ci sia bisogno di qualcosa di studiato ad hoc.
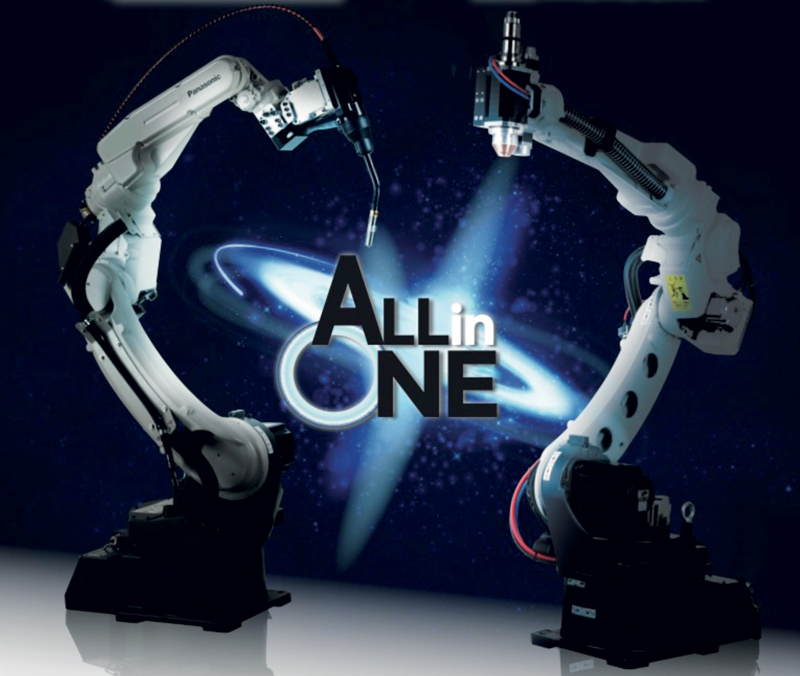
Qual è il vostro concetto di cella di saldatura? Penso per esempio al concetto di cella plug & play che sta prendendo sempre più piede sul mercato. Esiste una configurazione ottimale? Se si, quali sono le caratteristiche che deve avere?
Come già introdotto il fulcro del nostro lavoro è capire le esigenze produttive del cliente. L’aspetto che curiamo principalmente è la scelta e la messa a punto del miglior processo possibile di saldatura. Un altro aspetto che riteniamo importante è il concetto di “One Responsibility” secondo il quale ci poniamo di fronte al cliente come unici fornitori dell’intera cella. Questo comporta un grande impegno e un forte senso di responsabilità da parte nostra, ma trasferisce al cliente grandi vantaggi sia in termini efficienza, formazione, affidabilità del servizio e aggiornamento tecnico durante tutta la lunga vita dell’impianto. Seguendo questo approccio abbiamo sviluppato negli anni svariate soluzioni anche molto differenti. Alcuni esempi sono: la cella compatta con tavola rotante rivolta a lotti produttivi variegati e spazi di lavoro limitati; oppure, celle con elevata flessibilità in grado di riconoscere il pezzo da saldare, monitorare i parametri di saldatura durante il processo e decidere, in base a essi, se scartare o scaricare il particolare lavorato; fino a macchine dedicate completamente automatizzate, completamente ottimizzate per raggiungere la produttività richiesta con la massima efficienza dell’impianto.
Prendiamo in considerazione il robot; quali peculiarità deve avere dal punto di vista meccanico ed elettronico per essere sincronizzato al meglio con tutte le periferiche della cella ed essere aperto verso il generatore con cui, a prescindere dalla tecnologia, deve avere un’integrazione profonda per essere affidabili e produttivi?
Questa più che un assist è una provocazione, come già accennato Panasonic porta avanti nei propri prodotti il concetto di All In One. Sia il Tawers sia il LAPRISS fondono il controllo delle cinematiche del manipolatore e il controllo del generatore sulla medesima CPU. Mi piace ribadire la grande differenza tra il concetto di fusione di Panasonic e quello di integrazione di tutti gli altri costruttori di robot e saldatrici. In pratica ancora adesso, a distanza di molti anni dalla nascita del primo robot Tawers, Panasonic è l’unico robot sul mercato a non disporre di una saldatrice di terze parti. In pratica una saldatrice robotizzata e non un robot di saldatura Per quanto riguarda la meccanica e l’elettronica dei robot abbiamo invece bisogno di agilità, velocità e precisione. I nostri robot di saldatura hanno aree di lavoro che arrivano fino a un raggio di 2 m; questa che sembrerebbe una limitazione è in realtà un grande pregio, in quanto la taglia ridotta consente elevate rigidezze e miglior precisione. Tipicamente per applicazioni estese creiamo periferiche in grado di cooperare con il robot per poter ottenere la miglior posizione di saldatura possibile. Proprio sulle periferiche riusciamo a dare un forte contributo a quelli che sono i prodotti Panasonic. Sviluppiamo diverse macchine e siamo sempre aperti a nuove customizzazioni. Lavorando per ottenere prodotti che possano integrarsi nella sinergia del robot e del suo generatore per ottimizzare il processo.
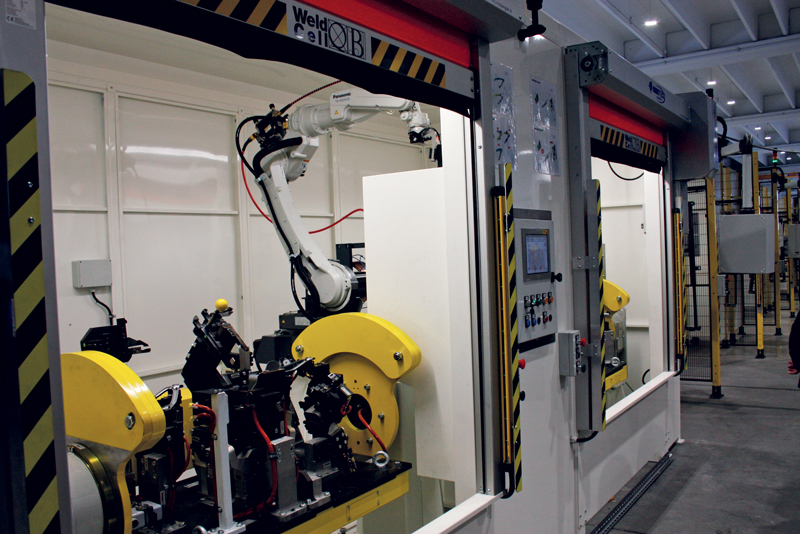
Pensando alla qualità del giunto di saldatura, in quali termini contribuisce e influisce il robot al raggiungimento di un risultato ottimale? In base a quali parametri applicativi viene scelta la tecnologia di saldatura più adatta?
Pensando al processo di saldatura, anche manuale, sappiamo che se un 60% della bontà del risultato è dato dalla scelta del processo di saldatura, un buon 40% è sicuramente nelle mani di chi salda o di chi programma il robot. Nel secondo caso a tenere in mano la torcia di saldatura è un robot. I vantaggi più evidenti sono sicuramente la precisione, la ripetibilità e la velocità, mentre tra gli svantaggi abbiamo un’evidente cecità del robot a ciò che succede durante il processo. Con la tecnologia Panasonic il manipolatore è invece in grado di reagire alle variabili del processo di saldatura riuscendo a comportarsi come farebbe un saldatore esperto. La tecnologia Tawers si differenzia su molti. Il traino del filo, per esempio, è gestito, grazie a un motore servo controllato, in base alla posizione del robot. L’apporto di filo è così molto costante anche nelle posizioni in cui il fascio cavi è particolarmente sollecitato. Le funzioni di Lift-Start e Lift-End consentono di innescare e terminare il bagno di saldatura evitando difetti e spruzzi. La funzione Auto-Extension è in grado di mantenere costante la distanza tra la torcia e il pezzo anche a fronte di deformazioni importanti.
Focalizziamoci sull’operatore di una cella di saldatura robotizzata, quali competenze deve avere? Deve essere un saldatore skillato o al giorno d’oggi è “sufficiente” essere dei buoni programmatori? Lo stato dell’arte della tecnologia sopperisce alla mancanza cronica di saldatori provetti? E soprattutto, quando conviene prendere in considerazione di investire in una cella robotizzata da inserire nel proprio contesto produttivo?
Le nostre macchine sono molto flessibili, consentono di ottenere buoni risultati anche per utenti inesperti e possono appagare i saldatori più specializzati. In particolare, una funzione interessante per saldatori entry-level è il Welding-Navigation, che consente di ottenere i parametri di saldatura inserendo il materiale, il tipo di giunto e gli spessori in gioco. Per quel che riguarda i saldatori esperti, invece, abbiamo la possibilità di partire da diversi software di saldatura in base al tipo di processo e ai materiali, è possibile andare a lavorare sui parametri di questi software per affinare il risultato o addirittura è possibile creare dei parametri di saldatura completamente personalizzati e svincolati da ogni impostazione. Un nuovo tipo di “operatore” che stiamo riscontrando sempre più è l’operatore off-line, ovvero colui che lavora sulle nostre celle mediante il proprio PC usando il software DTPS, proprietario Panasonic e completamente compatibile con i nostri robot. Questo approccio consente di ottimizzare la produttività riducendo i tempi di programmazione, permette di verificare immediatamente l’accessibilità di un mascheraggio e consente ovviamente di calcolare con precisione i tempi ciclo per formulare offerte calibrate, esigenza molto sentita presso molti conto terzisti.
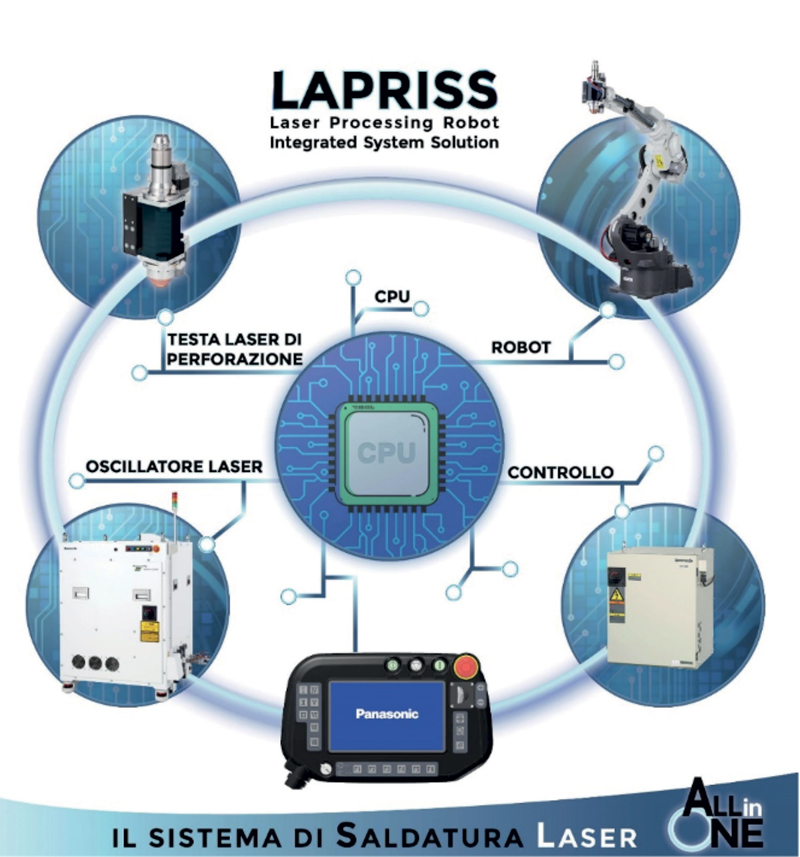
Questa mattina si è parlato dei gas, delle loro proprietà e dei vantaggi nell’utilizzo ottimale. Può raccontarci un caso in cui siete riusciti a implementare il processo grazie al gas o in alternative in quali processi credete che il gas potrebbe essere veramente determinante nell’appoggiare la transizione in corso verso efficienza e automazione?
Per quel che riguarda il gas siamo consapevoli delle possibilità offerte da miscele sempre più evolute e sofisticate. Detto ciò, un’applicazione molto particolare che porterei come esempio è quello della saldatura MAG di acciaio zincato. In questo caso, il gas utilizzato è la semplice ed economica CO2 pura in combinazione con la nostra soluzione di torcia e processo attivo chiamata SAWP (Super Active Welding Process).
Il SAWP consente di agire attivamente sul filo di saldatura con un movimento alternato di arretramento e avanzamento fino a 150 volte/sec, creando un arco alternativamente caldo e freddo molto concentrato. Il movimento del filo di saldatura accoppiato con le proprietà di diffusione del calore della CO2 consentono di ottenere l’evaporazione e l’espulsione dei vapori di zinco ottenendo un cordone con ottima penetrazione, assenza di porosità ed estetica appagante. Essendo un processo molto controllato risultano minime o assenti le proiezioni tipiche dei vecchi processi di saldatura a filo con CO2. Applicazioni dove invece il gas e la sua purezza sono fondamentali sono quelle di saldatura laser. Sul nostro LAPRISS utilizziamo argon molto puro per proteggere la saldatura nella maniera più opportuna.
La saldatura robotizzata è un’applicazione adatta alle caratteristiche di un cobot?
I cobot sono una delle grandi novità di questi ultimi anni e grazie anche ad azioni marketing molto efficaci tutti ne siamo venuti a conoscenza. Questi robot hanno l’enorme potenzialità di poter lavorare fianco a fianco con le persone senza costituire rischi. Purtroppo penso che associare a questo prodotto il processo di saldatura sia contradditorio se non addirittura controproducente. Come si può garantire la sicurezza di un operatore attrezzando un cobot con una torcia di saldatura? Ebbene per garantire la sicurezza dovrei costruire una cella esattamente identica a quella di un robot di saldatura, ma a questo punto perché costruire una cella complessa per inserirvi uno strumento con produttività inferiore? In conclusione, penso che i cobot siano veramente un’innovazione interessante, ma ritengo al contempo che l’ambito della saldatura robotizzata non sia indicato per questo prodotto.