Una macchina per il packaging 4.0 Ready
Un incontro riuscito tra mondo reale e mondo virtuale: la creazione del “Digital Twin” per una macchina da packaging automatica ad alta tecnologia ha consentito di ridurre tempi e rischi in fase di commissioning. Per lo sviluppo di questa macchina, Siemens ha supportato Easysnap con una piattaforma hardware/software unica e integrata.
di Silvia Crespi
All’ultima edizione del Forum Meccatronica “Le tecnologie abilitanti per la digitalizzazione 4.0 dell’industria” presso la Mole Vanvitelliana di Ancona, Siemens ha illustrato le potenzialità dell’integrazione delle tecnologie hardware e software in grado di soddisfare le esigenze di un mondo sempre più interconnesso e veloce, sul quale si basano i nuovi modelli di business.
Nel suo intervento all’interno della sessione convegnistica “Progettazione”, Siemens ha presentato un case study reale focalizzato sulla digitalizzazione e l’automazione industriale verso l’Industria 4.0 nei processi produttivi dell’industria del packaging.
In apertura della presentazione, Tommaso Valle, Pack Team Manager di Siemens Italia, ha illustrato, in sintesi, i driver tecnologici che stanno trasformando l’industria. Assistiamo, infatti, a un’evoluzione sia del modo in cui il prodotto prende vita, sia del modo in cui viene realizzato e si modifica nel tempo.
La via che i costruttori di macchine devono seguire è quella di abbracciare le tecnologie abilitanti per trasformare l’organizzazione in cui operano in un’impresa digitale. Per ottenere il massimo beneficio, il processo di trasformazione dovrebbe essere applicato all’intera value chain: dall’ideazione del prodotto (fasi di Product design e di Production Planning), alla sua realizzazione (fasi di Production Engineering e Production Execution) fino alla vita in esercizio del prodotto (Servizio).
Tutte queste fasi devono avere un “filo digitale” comune che permetta di accorciare il ciclo di vita dell’innovazione e consentire una continua trasformazione dell’impresa.
La soluzione Siemens è quella del prototipo digitale, o “Digital Twin”, che consente di simulare la costruzione e il funzionamento della macchina prima della sua effettiva realizzazione: un approccio che prevede il cambiamento culturale del modo di lavorare.
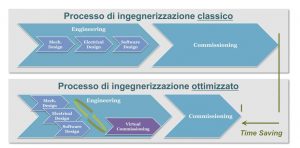
Virtual commissioning di una macchina per il packaging
Il case study presentato riguarda il Virtual Commissioning di una macchina da packaging, dove la creazione del “gemello digitale” ha permesso un notevole risparmio nei tempi di sviluppo.
Il processo di ingegnerizzazione classico prevede di arrivare al Commissioning attraverso le fasi di progettazione meccanica, progettazione elettrica e progettazione software, spesso sviluppate in modo separato e susseguente (non integrato e in parallelo). Il processo di ingegnerizzazione ottimizzato sfrutta i vantaggi del modello digitale, per ottenere una progettazione ottimizzata (sviluppo virtuale della macchina con cicli di feedback corti). Grazie allo sviluppo e simulazione ottimizzati, il risparmio di tempo nella fase di commissioning è notevole. Il prototipo digitale della macchina consente, infatti, di eseguire facili test di modifiche, azzerando il rischio di danni fisici alla macchina.
Tale processo è stato applicato alla macchina da packaging automatica Pulsar 351 di Easysnap Technology, azienda emiliana specializzata nel campo delle macchine da packaging certificate per le industrie del food, farmaceutiche, cosmetiche e medicali, e proprietaria di Easysnap®, una tecnologia brevettata che consente di aprire con una mano sola confezioni per prodotti liquidi e semi-liquidi.
La Pulsar 351, un’applicazione innovativa in termini di performance e flessibilità, è stata realizzata seguendo un workflow altrettanto innovativo: un percorso 4.0 completo che prende avvio dalla realizzazione di un gemello virtuale, un vero e proprio digital twin.
Un nuovo approccio alla gestione temporale della commessa
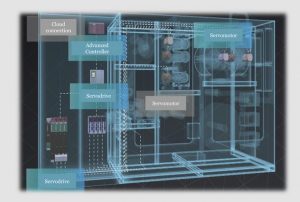
La macchina è particolarmente sofisticata e flessibile, dotata di 12 assi, sincronismi, cambi formato e diverse opzioni di prelievo robotizzato.
Per il suo sviluppo è stata prevista una piattaforma HW/SW unica e integrata. La creazione del digital twin ha consentito di chiudere il gap tra sviluppo meccanico e sviluppo software e di eseguire un test virtuale prima di quello reale. I software sono stati testati senza macchina fisica, così come i test di collisione (il che ha evitato il rischio di guasti alla meccanica). I test delle modifiche alla macchina hardware e software sono stati eseguiti prima dell’installazione.
In sintesi, si è trattato di mettere in campo un approccio totalmente nuovo alla gestione temporale della commessa. Un approccio che ha riguardato anche gli aspetti della manutenzione predittiva, grazie al condition monitoring system. Infine l’utilizzo del cloud ha creato valore aggiunto sia per l’OEM che per gli end-user.