Safe Packaging of 44,000 Water Bottles per Hour
ACMI, a manufacturer of high technology bottling and packaging lines, has been working in synergy with Pilz Italia on safety issues for years. The collaboration between the companies is mainly focused on risk assessment, which is fundamental to ensure safety in production. Several products supplied by Pilz Italia are present in ACMI machines: PSENcode sensors, PNOZ mB0 for safety logic and PNOZmulti configurator, just to name a few.
ACMI is an Italian producer of high technology bottling and packaging lines for the food & beverage sector. A globally well-known company, ACMI has obtained several patents and has developed important innovations in the packaging field over the years. Beside manufacturing end-of-line machines, ACMI is responsible for the engineering and automation of the entire line, acting as main contractor for entire projects.
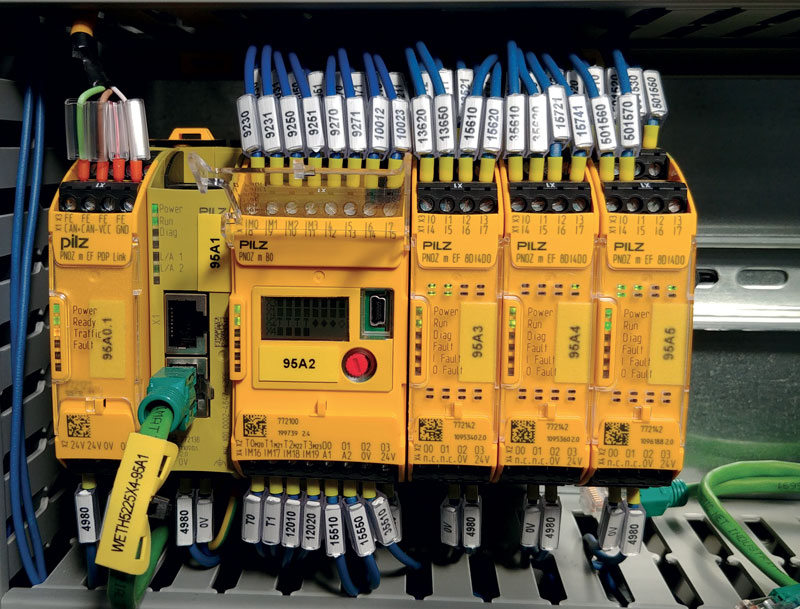
The layout of the bottling line
The Complete PET line for 44,000 bottles per hour installed at the site of a major Italian bottler of mineral water, produces 1.5 l square mono-format square water bottles. At the inlet there is the blowing-filling block where plastic preforms are blown, filled and capped. After a series of conformity checks (water level and correct application of the cap), bottles are conveyed inside a drying tunnel and then labelled and laser marked. A further quality control checks the correct application of the labels on the bottles, which then reach a Fenix shrinkwrapper. At the end of the line, a Viper handle applicator applies the handles to the individual packs, while a Thunder palletizer palletizes the packs both on a pallet and on half a pallet. The line ends with the wrapping of the pallets by means of an extensible film by the Vortex and Rocket fixed and rotating vane wrappers. ACMI took care of the design and installation of this high performance line, creating the layout of the plant and all the machines of the “dry” part of the line. In order to manage such high production speeds (consider that the square format presents a number of critical issues due to its specific conformation), the Fornovo-based company made use of the best technologies available on the market. The entire system was designed to operate automatically with only 3 operators who take care of the blowing-filling zone, the manual loading of the labels on the labelling machine and the end of the line respectively.
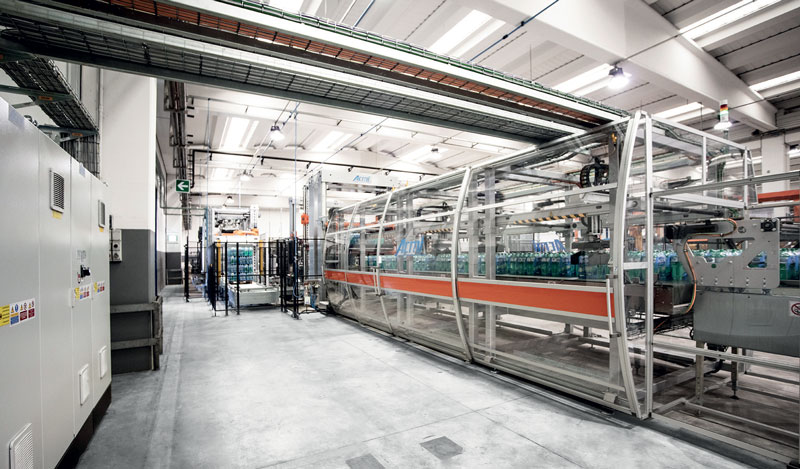
Manufacturer/supplier synergy focusing on risk assessment
First of all Pilz Italia carried out risk assessment on each ACMI machines (shrinkwrapper, handle applicator, palletizer, half-pallet wrappers, half-pallet stacker and whole pallet wrapper), and then proceeded with the risk assessment of the line. In particular, the interfaces between the various machines were analyzed and an evaluation of the non-conformities of the machines supplied by the co-partners in the project was carried out on a regulatory basis, identifying the risks and verifying the documentation provided by the partners.
The project managers of ACMI and Pilz carried out an initial inspection in order to identify any non-conformities of the machines involved in the project. The second inspection made it possible to verify the necessary measures to be implemented, so that the validation report of the Essential Health and Safety Requirements (E.H.S.R.) could be drawn up, in accordance with the requirements of the Machinery Directive 2006/42/EC. Finally, the Technical File and the Instruction and Maintenance Manual for the whole set of machinery was drawn up too.
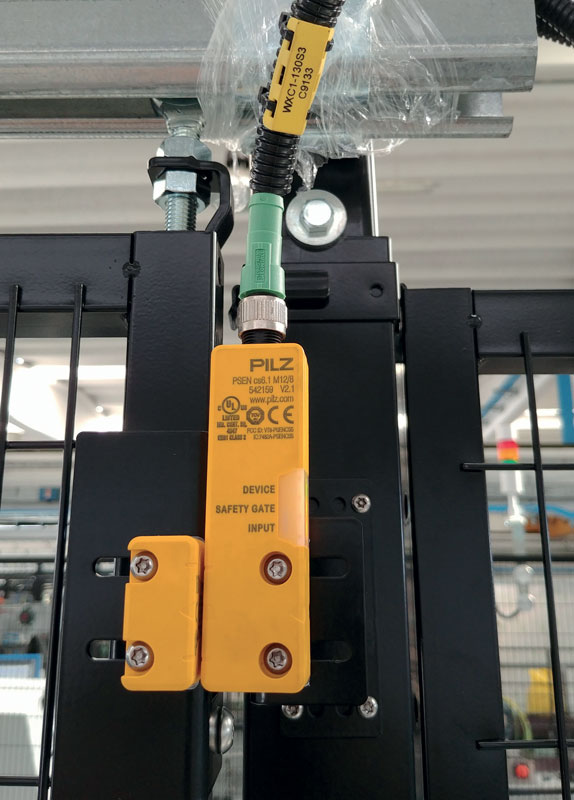
Pilz Risk Assessment included the following:
– identification of the standards and regulations in force;
– determination of machine limits;
– identification of the hazards at each stage of equipment life;
– risk analysis and assessment;
– identification of risk reduction strategies and measures.
Risk assessment is essential to ensure the safety of machinery and is the most effective and cost-effective way to reduce risks. Many activities carried out by both operators and machine maintainers involve a very high risk. The lack of a comprehensive analysis can often lead to accidents. During machine construction, modernization or inter-connection, the Risk Assessment is a fundamental factor in verifying the state of safety achieved and is also a valuable tool to identify any additional protective measures to be implemented.
PAScal software for the calculation of the Performance level allowed the performance level for every single safety function to be verified. Thanks to the simple graphical interface, PAScal allows safety functions to be configured thanks to pre-packaged libraries according to the VDMA 66413 library format, thus speeding up evaluation and verification of the Performance Level.
Configurable safety sensors and safety relays enhance flexibility
ACMI installed several products supplied by Pilz Italia in its machines. In particular it relied on PSEN code sensors conforming to the highest level of safety in accordance with EN ISO 13849-1 and EN IEC 62061. Thanks to RFID transponder technology, PSENcode safety switches combine maximum protection against manipulation with small footprint. In its version with fully unambiguous coding (high coding), PSENcode guarantees maximum flexibility and ease of use, while ensuring easy installation in accordance with EN ISO 14119:2013.
Safety logic was the task performed by programmable controller PNOZ mB0, of the PNOZ Multi2 range, guaranteeing maximum safety and, above all, maximum flexibility. The possibility to expand the safety logic and to manage advanced safety functions such as speed control make the Pilz solution a high performance solution and at the same time simple and flexible allowing ACMI machines high productivity. Thanks to the PNOZ mB0 module, ACMI was able to control emergency mushrooms, door sensors, modal selectors and enabling devices.
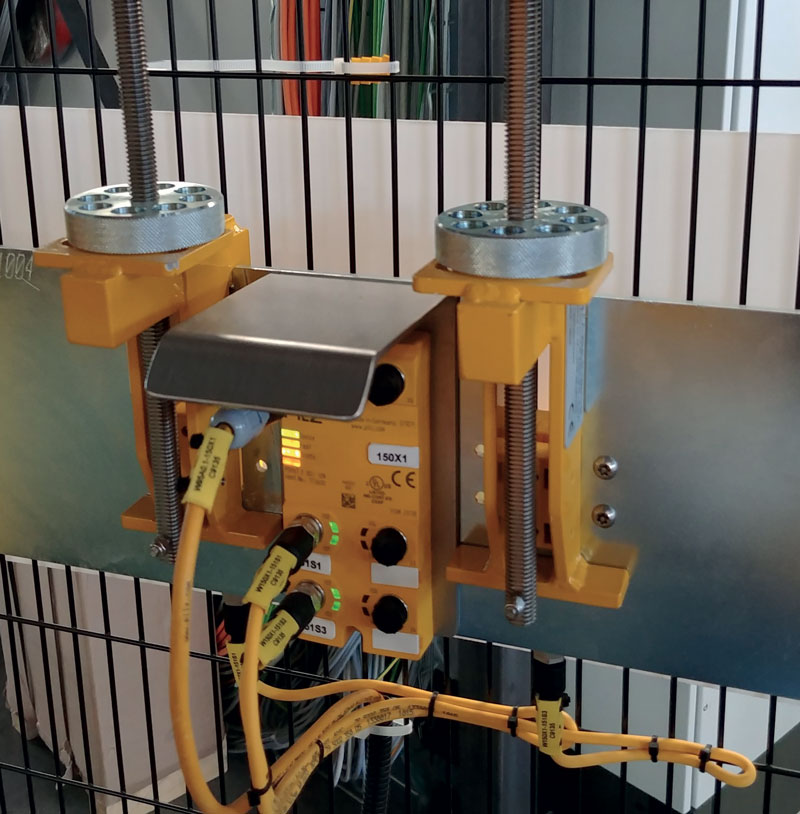
The system was configured by PNOZmulti configurator development software, which has simple and intuitive block programming. The PNOZ m EF PDPlink expansion module enabled the implementation of a secure network of PDP67 F 8DI ION cards (decentralized input modules with IP67 protection), with which it was possible to go into the field and collect the delocalized door sensors and various emergency mushrooms. In this way it was possible to optimize cabling and to make installation easier. Program’s CRC, which guarantees the uniqueness and integrity of the project, is stored in the technical file and can be viewed during the start-up phase of the PNOZ mB0 module together with the name of the project and the creation date. Online diagnostics through the PNOZmulti configurator allows operators to visualize the safety status in real time; thanks to the error stack and diagnostic words it is always possible to immediately identify any problem. The interfaceability of the PNOZmB0 system with the automation system of the machine was completed with the use of the PNOZ m ES Profinet fieldbus, which enables the communication of the status of the safety devices for a quick and easy identification of any problem.