Smart Couplings or Industry 4.0
R+W presents the AIC coupling: a smart component with integrated sensors able to measure, collect and transmit data during its operation, in full harmony with the principles of Industry 4.0. The AIC coupling provides an important example of technological and conceptual advancement not only for the transmission components sector but also for the drives sector.
In response to market needs in terms of digitization, R+W has developed the AIC coupling, a smart component that lends itself optimally to integration into digital ecosystems. Ecosystems contribute to the end-to-end digitization of production processes, which involves all partners in the relevant value chains. The choice of a smart component within a driveline stems from the need to collect as much data as possible of the operating conditions of a powertrain, obtaining as accurate an estimate as possible of the actual state of the machine/plant, in order to carry out the appropriate maintenance program.
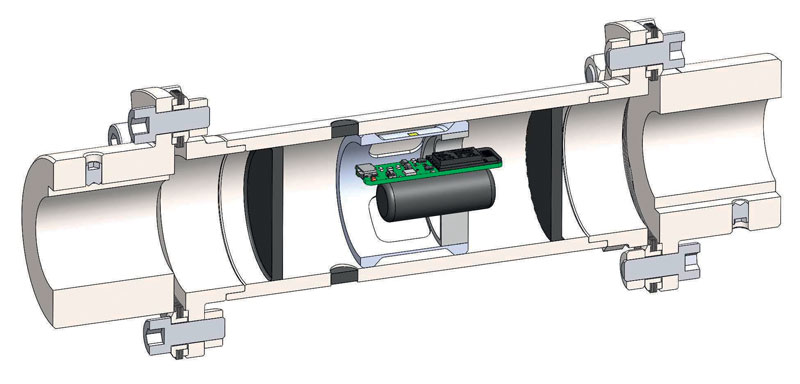
Structure and mechanical features of smart couplings
Figure 1 shows a simplified section of the AIC coupling, with the main electronic components. The structural choices made by R+W, for the realization of the housings of all the direct measurement systems of the operating data and of the other ICT components (used for connectivity and necessary for the transmission of the collected data), started from a series of considerations related to the standard measuring instruments available. The use of these instruments within a transmission, through the construction of the appropriate housings, would have increased the overall dimensions of the transmission. The containment of inertia and encumbrances is the main constraint to be respected during the design activities of a transmission, so the integration of standard measuring instruments into it is not always feasible, given the unavailability of miniaturized versions for all types of instruments required. Furthermore, the housings must be such as to allow the execution of the measurement itself, which is a further lower limit to the reduction of the overall dimensions. The integration of standard measuring instruments within a transmission is not feasible in most cases; this happens not only for the reasons indicated but also because it is impossible to implement a data transmission system using standard wiring. Any possible solution to the problem, however limited in terms of functionality and achievable performance, would lead not only to an increase in the moment of inertia (which is an additional criticality if the transmission functions at variable regimes) but also to a (considerable) increase in production costs.
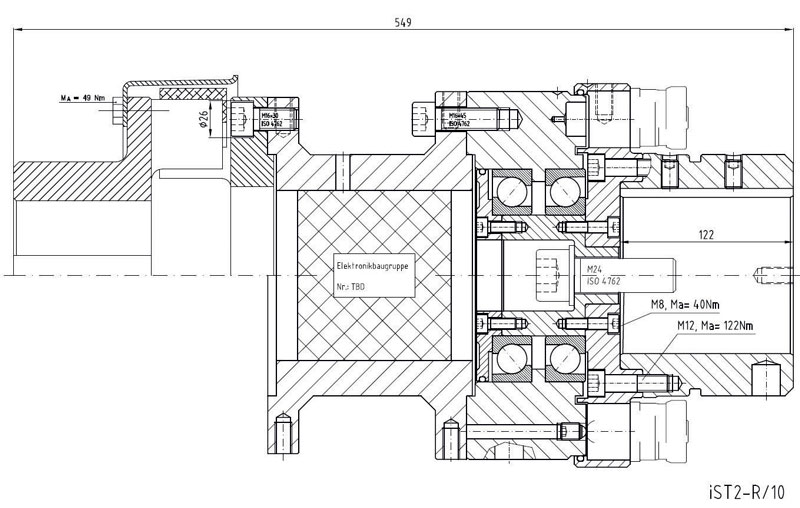
The AIC coupling not only has unique characteristics in terms of IoT-related advantages (as will be explained below), but also provides structural solutions that allow its integration with other existing R+W products. In fact, it can be used with all couplings with an intermediate spacer of the LP2, LP3, LPA series of disc pack couplings, ZA, ZAE and EZ2 series of line shafts; as a next development there is the integration with the STF flanged units, while the integration with the other types of couplings (EK, ST, SK, BK and ES) is currently under development. These integration features are enabled by the special modular structure which can be easily integrated into the spacers as shown in Figure 2. These structural choices allow the use of the AIC joint also in heavy duty applications, as shown in Figure 3. Further advantages, also at structural level, are given by the simplicity of installation, thanks to the absence of additional flanges. The choices indicated have also made it possible to achieve both high levels of sensor protection (which is enclosed in a special seal) and economic production.
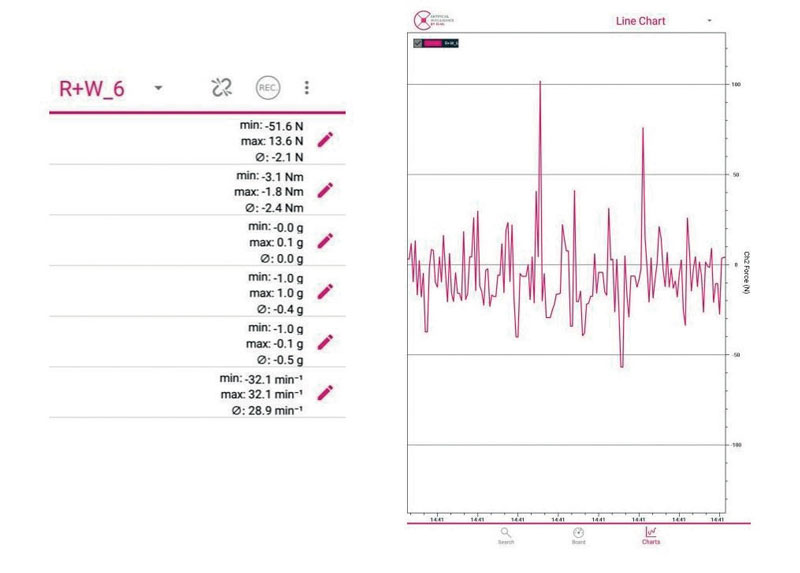
Functions and connectivity of the AIC coupling
R+W started from the design of these components to integrate, in the new AIC coupling, state-of-the-art sensors and solutions for signal processing.
The heart of the system is thus given by the electronic components, which integrate different types of sensors such as strain gauges, accelerometers and gyroscopes. It is interesting to highlight how the choices made by R+W on the type of sensors integrated in the AIC coupling is optimal with respect to the possible needs of use:
- strain gauges extend the functionality provided by the first torsional couplings, providing a measurement of localized torsional strain
(or overall torsional deflection) starting from that of mechanical stress;
- accelerometers detect and measure structural oscillations and vibrations, referring to the entire kinematic chain;
- the gyroscopes used are of the type dedicated to the measurement of angular velocity, generally consisting of a 3-axis accelerometer or a series of uniaxial accelerometers arranged in a radial direction, in a number suitable to provide a reading extracted from the average of the readings of the individual component accelerometers.
- In addition to the integrated sensors, there is an electronic board that mounts a microcontroller, a Bluetooth radio module and a signal amplifier.
The electronic board thus designed provides the connectivity functions that make the AIC coupling, in fact, a smart component.
It is powered by a lithium-ion battery; the charging system used has extremely interesting aspects, which are described below.
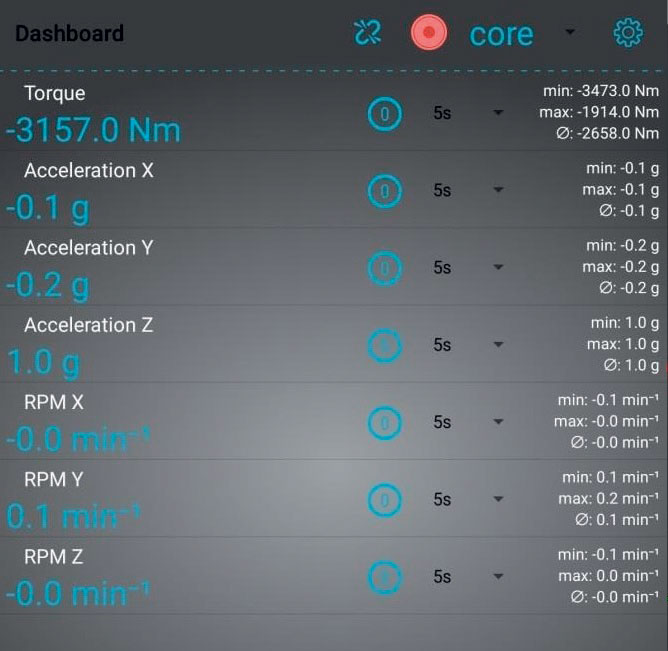
The wireless charging system exploits the phenomenon of electromagnetic induction
With the AIC coupling R+W has succeeded in achieving a unique example of extension of the transducer concept, intended as a union between sensor and signal processing devices. The latest updates concern both the improvement of the coupling-control system communication (obtained by using an external gateway configured to optimize data collection and processing activities) and the wireless charging system (consisting of a device which exploits the phenomenon of electromagnetic induction previously mentioned, generated by wireless data transmission systems). These solutions allow the AIC coupling to operate and transmit data continuously, without having the limit of a certain measurement time related to the charge of the battery, occurring during normal operating conditions. By exploiting the phenomenon of electromagnetic induction, R+W has succeeded in creating an efficient battery charging system without the use of any additional device, with further economic advantages. Moreover, the insertion of these devices
has been realized in such a way that they do not constitute a structural criticality in terms of increasing the moment of inertia, thus keeping the mechanical properties unchanged.
Application fields and advantages
The AIC coupling, with its ability to perceive, interact and interconnect, is an element of deep change in terms of achievable performance and the creation of dedicated cinematic chains, especially when destined to those machines designed to be used in production lines operating in an automatic and adaptive way. On the basis of these aspects, the system is designed to interact optimally with the operator during data collection and processing, in order to achieve an adequate use in all contexts of IoT Assisted Production, intended as a key concept of Industry 4.0. In relation to this activity, data collection covers the following physical quantities: torque (with an error of <1%); speed (with an error of <3%); vibration (with an error of <3%) compression / rebound (with an error of <3% for calibrated LP combinations up to 1000 Nm). The representation of the measured data, related to these quantities, is realized through a special app for Android mobile devices, as shown in Figure 4; the same measured data can be recorded and exported in csv format, as shown in Figure 5. The app’s dashboard provides a complete overview of the measured quantities, including maximum and minimum values and their average, as shown in Figure 6.
The graph display modes are shown in Figure 7; the app provides the ability to superimpose multiple different curves into a single graph and display data measured from multiple AIC couplings operating simultaneously. Other display functions concern the charge level of the lithium batteries, described above, and the display of the wireless signal strength, as well as buttons to enable screenshot capture and the export as files in csv format. These measurement modes can also be extended to fixed and pre-existing systems; this extension is still under development. The measurement aggregation modes also allow an improved evaluation and understanding of the behaviour of the rotating bodies which make up the transmission. On the basis of the characteristics and functionalities described, the fields of application envisaged by R+W, for the AIC coupling, can be referred to those fundamental for Intelligent Manufacturing, that is: predictive maintenance activities; test setups; verification of theoretical design data; real time control of parameters such as vibrations, temperatures and recall forces. These features achieve the main functionality of Intelligent Manufacturing: to support the updating and management of the production, together with the research and development path for a given type of product.
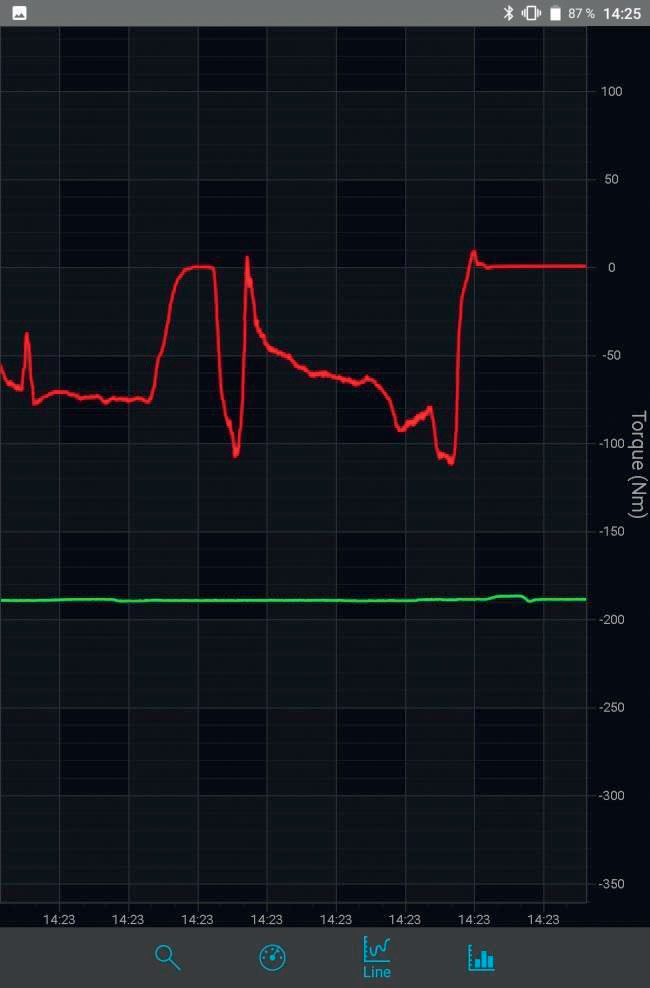
On the basis of these premises, the advantages that can be achieved with the use of the AIC coupling can be summarized as follows: continuous monitoring of use in real time; application-based predictive maintenance; quality monitoring through end-of-line control; validation of design data with actual data collected under operating conditions. But that’s not all. The results achieved with the AIC coupling make it a reference component also in cyberphysical systems technology, for which physical objects and software platforms are integrated to exchange information in an optimal way.