Interessati a tutto ciò che è nuovo
Specializzata nel campo dei connettori e bobine per elettrovalvole, ATAM porta avanti da mezzo secolo un percorso improntato all’innovazione. La società fa della customizzazione di prodotto uno dei suoi punti di forza, rivolgendosi anche a mercati di nicchia come il mondo ATEX e IECEx e prodotti con certificazioni VDE e UL. Andrea Ciceri, COO della società, ci parla degli ultimi investimenti, di applicazioni innovative e molto altro…
Il percorso compiuto da ATAM nei suoi primi 50 anni di vita è all’insegna dell’innovazione. Mezzo secolo di storia in cui l’azienda si è evoluta grazie ai continui investimenti nell’automatizzazione e interconnessione delle sue strutture, nella R&D e nella formazione del personale.
Parliamo di innovazione a 360 gradi: innovazione di prodotto, di processo, di gestione e di controllo di gestione. InMotion ha intervistato Andrea Ciceri, Direttore Operazioni, per parlare di questo e di molto altro.
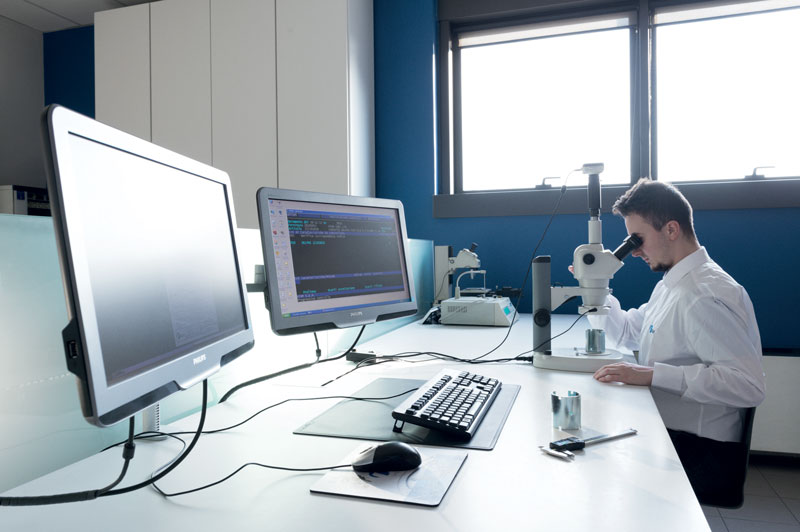
InMotion: ATAM mette l’innovazione al centro della propria attività. Ci può parlare dei recenti investimenti in questa direzione?
Andrea Ciceri: La propensione agli investimenti di ATAM è decisamente molto forte. Partiamo dallo sviluppo dei nuovi prodotti e, in particolare, di tre novità di spicco. La prima è un contatto innovativo per i nostri connettori. Da anni utilizziamo un contatto molto evoluto basato su un sistema di connessione dei cavetti a vite; ora, partendo da questo contatto, abbiamo inserito un dispositivo di connessione elastico. Abbiamo quindi investito in attrezzature per eseguire una campionatura di questo contatto che potrebbe portare a una piccola rivoluzione nel mondo dei connettori elettrici per elettrovalvole, riducendo drasticamente i tempi e i costi di cablaggio. Altri progetti hanno riguardato la miniaturizzazione delle elettrovalvole che vengono applicate al mondo dell’oleodinamica, il principale settore di sbocco dei nostri prodotti. Anni fa siamo stati precursori di questo tipo di prodotto, che prevede l’integrazione tra la bobina e la valvola, ma recentemente, in co-design, con il cliente siamo riusciti a realizzarne uno ancora più piccolo, rivolto alle macchine movimento terra e ai trattori. Questo progetto ha fatto scuola e oggi è diventato uno standard nel mondo dell’oleodinamica a basso costo. La miniaturizzazione, in ambito oleodinamico, pneumatico e in quello delle automazioni, è uno dei campi dove intravediamo le maggiori possibilità di sviluppo. Penso, per esempio, al mondo della frenatura pneumatica dei grandi veicoli (il trasporto autoferrotranviario, per esempio).
Un altro nuovo progetto sul quale abbiamo investito è lo sviluppo di una serie di bobine con circuito magnetico esterno: queste bobine vengono utilizzate, sempre in ambito oleodinamico, sui carrelli elevatori, un’applicazione sfidante in termini di rapporto prestazioni/consumo energetico. Su un carrello elevatore sono le batterie stesse che provvedono a tutti i movimenti, quindi l’autonomia del veicolo è della massima importanza.
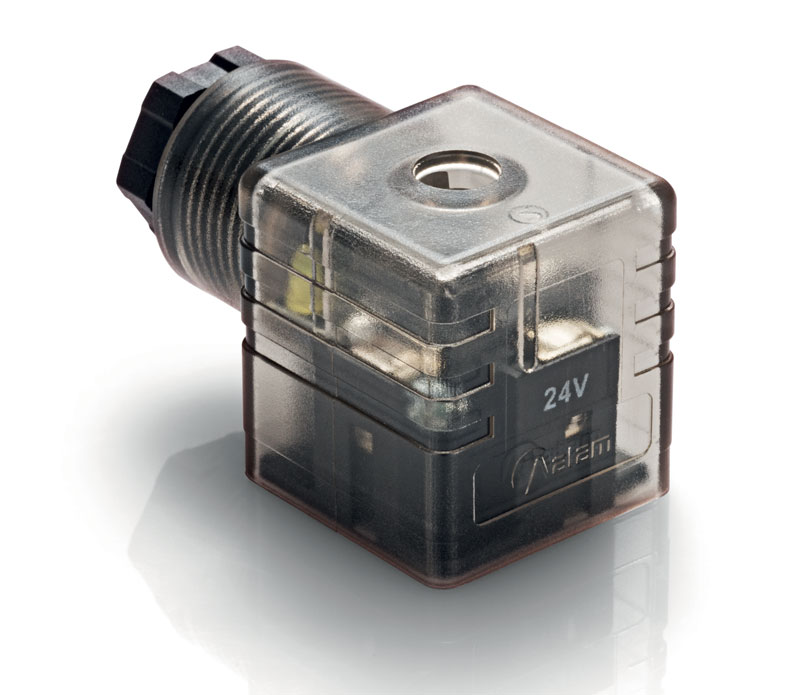
In questa applicazione le nostre bobine ad altissime prestazioni, con un assorbimento di corrente ridotto, hanno rappresentato un grande passo in avanti; sono state offerte ai due maggiori player del settore e hanno avuto un grande successo. Un altro campo in cui investiamo da sempre è la ricerca sui materiali. Da qualche anno abbiamo sviluppato un nuovo materiale che permette di omologare il nostro prodotto secondo la classe di isolamento termico H, che corrisponde a 180° C continuativi; oggi lo stiamo adottando in mass production con i maggiori player del settore dell’oleodinamica dove sono richieste prestazioni che raggiungano classi termiche elevatissime. Questo materiale, innovativo e competitivo, è in grado di offrire prestazioni superiori rispetto alle massime raggiungibili fino a qualche anno fa, non era mai stato impiegato sulle bobine. Il nostro impegno nella ricerca di nuovi materiali non ha mai conosciuto sosta. Utilizziamo al nostro interno almeno dieci famiglie di materiali diversi suddivisi tra termoplastici e termoindurenti, declinati in 25 sottotipi, per l’incapsulamento dell’avvolgimento, un’operazione apparentemente semplice, ma con tanto know-how e tecnologia realizzativa alle spalle. Stiamo investendo risorse anche nell’automazione industriale con un programma di rinnovamento del nostro parco macchine, dalle presse a iniezione per il sovrastampaggio di materie plastiche sui nostri prodotti, alle macchine per il collaudo finale che, nel nostro caso, è particolarmente severo. Si tratta di macchine automatizzate che richiedono un intervento minimo da parte dell’operatore. Inoltre è in fase di realizzazione un’attrezzatura specifica per la verifica della qualità dei componenti elettronici in ingresso, che analizzerà le reali prestazioni in funzionamento, rispetto alle specifiche dichiarate dai costruttori. Un tipo di verifica difficilmente realizzabile, se non dai costruttori stessi, che rende ATAM l’unico produttore di solenoidi in grado di garantire la piena conformità dell’elettronica a bordo bobina. Altre novità riguardano la gestione del prodotto. Abbiamo realizzato un sistema gestionale personalizzato che contiene al suo interno la funzione di PLM, grazie al quale riusciamo a tracciare ogni singola fase della vita del prodotto, dal recepimento della richiesta di offerta fino alla sua spedizione, attraverso la realizzazione dei singoli componenti, l’assemblaggio, il sovrastampaggio e il collaudo. Abbiamo così a disposizione lo “storico” di ogni prodotto, comprensivo dei report di laboratorio e delle decisioni prese in ogni singola scelta. Il passo successivo sarà la divulgazione dei punti salienti di questo storico presso i clienti, con modalità di tracciabilità ormai internamente consolidate, onde permettere loro di avere tutte le informazioni su ogni singolo prodotto o lotto di produzione. Implementato da gennaio 2020, il nostro PLM è in fase di continuo perfezionamento e adattamento alle nostre esigenze e a quelle del cliente. Concludo con la progettazione: recentemente abbiamo adottato un nuovo modulo CAE FEM: un sistema di analisi multifisica che analizza il campo magnetico generato dal nostro prodotto, l’incidenza dei flussi magnetici all’interno dei circuiti magnetici, la forza dell’attuatore montato sulla bobina e la temperatura sviluppata dal prodotto e la sua dissipazione; abbiamo così un’analisi completa di tutto ciò che è inerente alla sua applicazione.
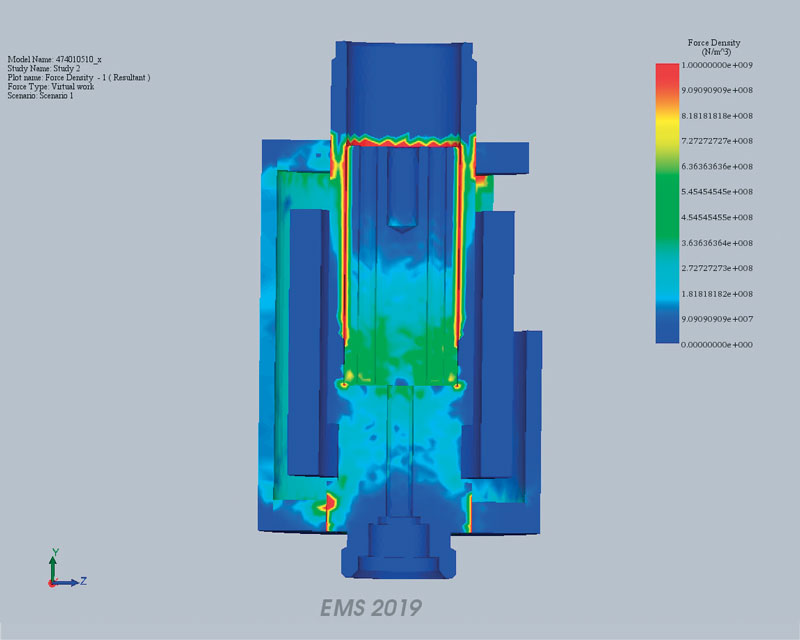
IM: La customizzazione di prodotto caratterizza l’attività di ATAM. La progettazione viene portata avanti in co-design con i clienti. Quanto è importante questo lavoro sinergico per la vostra attività?
AC: La capacità di customizzazione, per le sole bobine elettriche, rappresenta il 70% di quanto produciamo. La personalizzazione è possibile grazie al forte know-how del reparto R&D, in grado di offrire una consulenza specializzata che si spinge oltre lo sviluppo del prodotto, coinvolgendo l’intero gruppo solenoide elettrovalvola o connessione elettrica. La nostra filosofia è basata sull’ascolto del cliente; il confronto con l’ufficio tecnico del cliente è quindi costante; lavoriamo in sinergia già dalla fase del concepimento del prodotto fino alla sua commercializzazione assistendolo anche nell’ottenimento di certificazioni specifiche. La nostra strategia è quella di indirizzare il cliente verso tecnologie a noi accessibili offrendogli in tempi rapidi un prodotto inedito customizzato in termini di prestazioni, ingombri, condizioni ambientali, imballi, consegne… tenendo conto anche delle metodologie e dei processi di fabbricazione in atto nella sua azienda. Il tutto con la massima trasparenza.
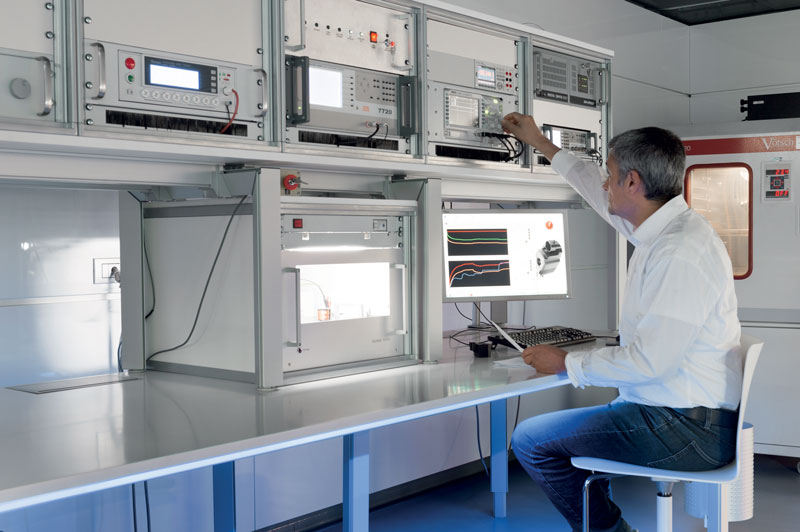
IM: Le vostre capacità in termini di personalizzazione di prodotto e il costante lavoro di ricerca vi portano a sviluppare prodotti innovativi, non ancora presenti sul mercato.
AC: È così. Il continuo impegno nella ricerca ci porta spesso ad agire come pionieri sul mercato nell’ambito delle costruzioni pneumatiche e delle automazioni. Spesso il cliente si rivolge a noi perché necessita di qualcosa di realmente innovativo, non presente sul mercato.
Cito qualche esempio, partendo dalla ricerca sui materiali di isolamento per il sovrastampaggio dei nostri prodotti, a seconda dell’ambiente in cui si trovano ad operare. Siamo stati i primi, nel mondo della pneumatica a integrare l’operatore all’interno della bobina, una configurazione che consente un risparmio di costi. Siamo stati i primi a includere l’elettronica all’interno del sovrastampaggio. Siamo stati pionieri nella climatizzazione delle celle a batteria per i veicoli ibridi ed elettrici. Siamo stati pionieri nell’ambito della miniaturizzazione in campo oleodinamico, pneumatico e dell’automazione, uno degli ambiti dove intravediamo le maggiori possibilità di sviluppo. Siamo entrati nel settore delle applicazioni medicali, fondendo tutto quello che era il nostro know-how… Essere pionieri in queste applicazioni particolari è per noi motivo di vanto.
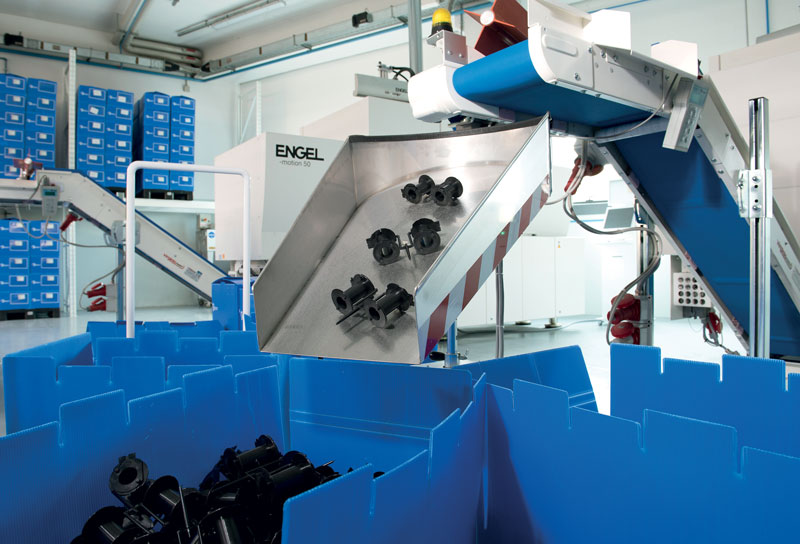
IM: Nella sua attività ATAM pone particolare attenzione alle certificazioni. Le applicazioni ATEX sono un ambito nel quale siete particolarmente specializzati
AC: Seguiamo svariate norme internazionali, e applichiamo il meglio di questi standard ai nostri prodotti in modo da mantenere una grande flessibilità produttiva. La normativa Atex, in particolare, ci tocca da vicino. Il nostro Direttore tecnico, che proviene da quel mondo, ha portato con sé tutta la sua esperienza in un campo dove la normativa è in continua evoluzione. Non solo… il nostro incaricato Atex vanta una lunga collaborazione con uno dei principali istituti italiani di omologazione in questo ambito. Ci occupiamo delle applicazioni Atex con due nostre gamme di prodotto, una rivolta al mondo dell’automazione pneumatica e l’altra al mondo dell’oleodinamica.
IM: Per portare avanti un’attività di questo tipo è fondamentale possedere un forte know-how e competenze specifiche, quindi figure professionali dedicate. Quando è importante investire nella formazione delle risorse?
AC: Nella nostra azienda il processo di formazione è continuo. Tendiamo costantemente a trasformare le competenze reali nelle competenze ideali per coprire le posizioni all’interno dell’azienda, attraverso corsi specifici. Per fare un altro esempio di Training on the job… tutti i giorni, alle 8.30, nel nostro Daily Scrum Meeting scambiamo informazioni con tutte le funzioni dell’organizzazione in modo che tutti possano essere a conoscenza di quello che verrà svolto in giornata. È un momento in cui viene spalmato il know-how su tutte le funzioni, vengono condivisi problemi, informazioni, in modo che anche chi non è coinvolto direttamente, sia messo al corrente. In un’ottica di scambio e Continuous improvement, una volta al mese, in una riunione più strutturata e allargata chiamata “comitato di miglioramento” vengono analizzati tutti gli indicatori principali della società (produzione, acquisti, vendite, rendimento e così via), in modo da informare tutti sull’andamento generale e i punti di attenzione principali. Una gestione di questo tipo è essenziale per un’azienda che produce e gestisce 5000 codici, con volumi produttivi di 7/8 milioni di bobine all’anno e altrettanti connettori.