Monitoraggio della produzione a tutto campo
L’introduzione di quattro serie di dispositivi di monitoraggio rientra negli sforzi profusi da Omron per il raggiungimento delle 100.000 unità di componenti IoT. I dispositivi di monitoraggio verificano costantemente le condizioni degli impianti e delle apparecchiature e rilevano in anticipo gli errori di stato degli impianti.
di Andrea Baty
Omron tra lanciando quattro serie di dispositivi per il monitoraggio delle condizioni e verifica dello stato operativo degli impianti produttivi: dispositivi per il monitoraggio delle condizioni dei motori, che consentono di prevedere i guasti ai motori a induzione trifase; alimentatori con collegamento in rete, in grado di prevedere la vita utile e i guasti degli alimentatori installati nei quadri di controllo; sensori di flusso e sensori di pressione, in grado di monitorare il fluido idraulico e l’acqua di raffreddamento utilizzati nelle pressatrici e nelle macchine di stampaggio; un amplificatore intelligente per il monitoraggio delle condizioni, in grado di accelerare l’applicazione di Internet of Things (IoT) nei sensori analogici già installati negli impianti o nelle macchine.
I dispositivi di monitoraggio controllano in tempo reale le modifiche ai sistemi di alimentazione degli impianti produttivi, comunicando i tempi di sostituzione delle parti nelle reti di comunicazione prima che si verifichino guasti, contribuendo a prevenire le interruzioni impreviste degli impianti e i problemi di qualità dei prodotti.
L’uso di questi dispositivi permetterà di ridurre le perdite di produzione associate alle interruzioni impreviste degli impianti, migliorando la precisione dei piani di manutenzione.
Dispositivi di monitoraggio dello stato dei motori
I dispositivi di monitoraggio dello stato dei motori rilevano gli errori provocati dal deterioramento dei motori a induzione trifase utilizzati in numerosi impianti produttivi, ad esempio trasportatori, sollevatori e pompe.
I dispositivi di monitoraggio rilevano gli errori e le variazioni di stato relativi a vibrazioni, temperatura, corrente e resistori di isolamento, mostrando i dati sull’unità principale o in remoto tramite comunicazioni Ethernet/IP™ e offrendo i seguenti vantaggi: abbattimento delle perdite di produzione provocate dalle interruzioni impreviste degli impianti; digitalizzazione delle conoscenze dei manutentori qualificati; passaggio da una procedura d’ispezione periodica a quella preventiva, riducendo considerevolmente le attività di ispezione.
Collegamento in rete per gli alimentatori
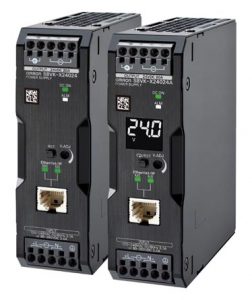
Gli alimentatori con collegamento in rete, oltre a garantire la funzione di base di erogazione della c.c. ai dispositivi degli impianti, mostrano i dati necessari per monitorare e provvedere alla manutenzione dell’alimentazione elettrica. Ad esempio, possono indicare quando devono essere sostituiti, mostrare informazioni sulla tensione/corrente di uscita e aumentare la corrente da remoto ricorrendo alla comunicazione Ethernet/IP e al monitoraggio dell’unità principale, offrendo i seguenti vantaggi: comunicazione anticipata dei tempi per la sostituzione di un alimentatore, riducendo le interruzioni impreviste degli impianti provocate dai problemi di alimentazione; monitoraggio da remoto dei tempi di sostituzione, esecuzione totale, tensione e corrente, riducendo gli interventi di manutenzione in loco; utilizzo in combinazione con il software dedicato per il monitoraggio dell’alimentazione per visualizzare le condizioni dell’alimentazione sulla curva declassamento.
Per prolungare la durata dei dispositivi, è possibile adottare facilmente misure atte a migliorare gli ambienti di installazione e modificare la capacità degli alimentatori.
Sensori di flusso e sensori di pressione per centri di lavoro e presse
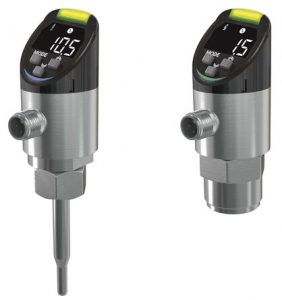
Un unico sensore di flusso può misurare sia la portata, sia la temperatura dell’acqua di raffreddamento utilizzata nelle macchine di saldatura o stampaggio. Il monitoraggio degli errori provocati dalla temperatura e dalla portata dell’acqua di raffreddamento consente di rilevare i segnali delle interruzioni impreviste causate dal surriscaldamento dei trasformatori di corrente, aumentando la qualità e la stabilità della saldatura e prevenendo gli errori di stampaggio.
I sensori di pressione mostrano simultaneamente la pressione e la temperatura del fluido idraulico nei centri di lavorazione e nelle presse. Questi dispositivi rilevano i segnali del deterioramento delle guarnizioni dovuto all’aumento della temperatura e alle successive perdite di fluido idraulico. Inoltre, rilevano le variazioni di temperatura dovute al deterioramento della viscosità del fluido idraulico, garantendo una qualità di elaborazione costante.
Il fatto di non dovere installare un sensore di pressione e un sensore di temperatura sulle tubazioni dimezza i lavori di installazione.
Rilevando svariate tipologie di dati di misurazione, ad esempio “portata e temperatura” e “pressione e temperatura”, questi sensori sono in grado di visualizzare le condizioni degli impianti risparmiando denaro, spazio e ore di lavoro.
Amplificatore intelligente di ultima generazione per il monitoraggio
L’amplificatore intelligente per il monitoraggio si collega a sensori di uscita analogici generici.
Omron offre la serie di amplificatori N-Smart di ultima generazione che si collegano ai sensori in fibra ottica e ai sensori laser. L’aggiunta dell’amplificatore intelligente per il monitoraggio, in grado di collegarsi a sensori di uscita analogici generici, permette di creare facilmente una rete economica composta da più sensori al fine di tenere sotto controllo le condizioni di un impianto.
In precedenza, per ottenere i dati dai sensori con uscita analogica, era necessario disporre di onerosi data logger e dispositivi di misurazione. Il sensore può sincronizzare fino a 30 unità a velocità elevate di 1 ms, raccogliendo i dati durante le operazioni di produzione, rilevando le modifiche minime agli impianti e l’affidabilità dei segnali, consentendo quindi un controllo ottimale delle macchine basato sui cambiamenti di stato dell’impianto.