Significativa riduzione di tempi e costi d’installazione
La tendenza attuale del montaggio di moduli I/O direttamente sul campo senza quadro elettrico offre tutta una serie di vantaggi, come la riduzione dei tempi e dei costi d’installazione. Per questo motivo, Phoenix Contact ha aggiunto un box I/O sicuro al suo collaudato sistema I/O Axioline E con grado di protezione IP67. Ora, anche i segnali di sicurezza fino a SIL 3 e PL e possono essere acquisiti ed emessi.
Nello sviluppo di nuove applicazioni, molti costruttori di macchinari e impianti si trovano spesso a confrontarsi con l’interrogativo se i sensori e gli attuatori installati sul campo debbano essere collegati alla tecnica di controllo in modo classico tramite moduli I/O installati nella morsettiera. Un’alternativa è costituita dal collegamento tramite moduli I/O con grado di protezione IP65/67 montati direttamente sul campo. Su questo punto si incontrano opinioni diverse, perché ogni approccio presenta vantaggi e svantaggi. Mentre la variante con morsettiera apre a un alto livello di granularità, la soluzione IP65/67 riduce notevolmente dei tempi e dei costi di montaggio e di installazione.
Quali sono dunque i requisiti essenziali che i costruttori di macchine e sistemi di automazione pongono all’integrazione del livello sensore/attuatore? Da un lato, è necessaria una grande flessibilità per poter reagire rapidamente alle esigenze specifiche del cliente, perché di norma non esistono due macchine di serie identiche. Anche questo aspetto è quindi un problema importante in questo segmento dell’ingegneria meccanica. D’altro canto, vale il detto “il tempo è denaro”, motivo per cui i produttori di macchinari e impianti si aspettano un’installazione semplice ed esente da errori. È a questo punto che i dispositivi di campo con elevato grado di protezione mostrano i loro punti di forza. Poiché possono essere installati direttamente in loco nella macchina o nell’impianto, si creano brevi percorsi di cavi e la posa dei cablaggi necessari diventa facilmente comprensibile. Inoltre, i cavi M12 preassemblati contribuiscono a ridurre il tempo necessario. In caso di necessità di sostituzione dei moduli a sistema avviato, l’utente richiede una diagnosi esatta con l’ubicazione e la causa dell’errore, in modo da garantire la disponibilità dell’applicazione (figura 1).
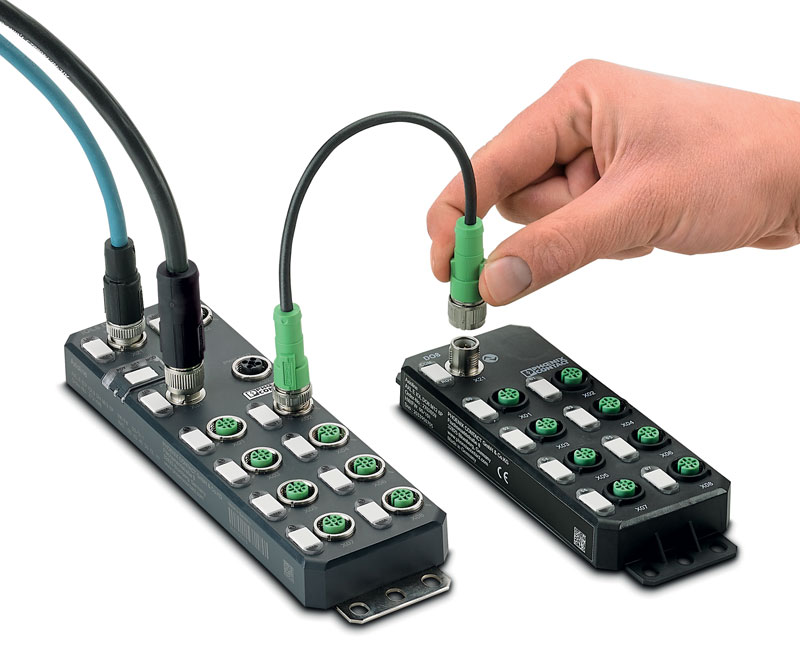
Sicuro fino a SIL 3, SIL CL 3 e PL e
Gli argomenti elencati sono la ragione per cui il numero di utenti di moduli I/O decentralizzati con elevato grado di protezione è in costante crescita da anni. Con i dispositivi della consolidata serie Axioline E, Phoenix Contact copre un’ampia gamma di tipi di segnale e di reti richiesti. I moduli Axioline E si sono dimostrati specialisti Ethernet per l’installazione sul campo. Ciò è dovuto al fatto che il sistema di I/O nel formato monoblocco, collegabile direttamente alla macchina senza quadro elettrico, supporta tutti i protocolli di comunicazione basati su Ethernet, consentendo un elevato grado di flessibilità. I suoi ingressi e uscite digitali consentono l’implementazione della maggior parte dei requisiti. Altri tipi di segnale vengono accoppiati tramite il master IO-Link integrato (figura 2). Fino a poco tempo fa, gli utenti si trovavano di fronte alla sfida che i segnali relativi alla sicurezza non potevano essere acquisiti ed emessi con il sistema. Pertanto, per garantire la sicurezza funzionale era necessaria una soluzione parallela la cui realizzazione avveniva o tramite moduli di sicurezza separati in un quadro elettrico centrale o tramite un controllore di sicurezza aggiuntivo, dove entrambe le alternative richiedono un dispendioso cablaggio in parallelo.

Questo non è più necessario perché la gamma di prodotti Axioline E è stata ampliata per includere il box I/O sicuro Axioline E Safe con grado di protezione IP67. Il modulo può ricevere e trasmettere segnali relativi alla sicurezza, come l’arresto di emergenza o la barriera fotoelettrica. A seconda della parametrizzazione e del cablaggio, si può raggiungere un livello di sicurezza fino a SIL 3, SIL CL3 o PL e (figura 3). Oltre agli otto ingressi e quattro uscite sicure e all’interfaccia IO-Link, il box I/O include altre caratteristiche speciali. Ad esempio, è stato eliminato l’interruttore per l’impostazione dell’indirizzo di sicurezza che viene ora assegnato tramite il rispettivo tool di progettazione o tramite il controllore. Per una rapida sostituzione del dispositivo è disponibile opzionalmente un memory stick separato per l’indirizzo di sicurezza. Il box I/O si caratterizza anche per la sua natura multilingue: da un lato supporta il protocollo Profisafe e può essere utilizzato insieme ai controllori di sicurezza compatibili con Profisafe, dall’altro la tecnologia integrata SafetyBridge Technology (SBT) consente l’interconnessione in quasi tutte le reti di automazione (figura 4).
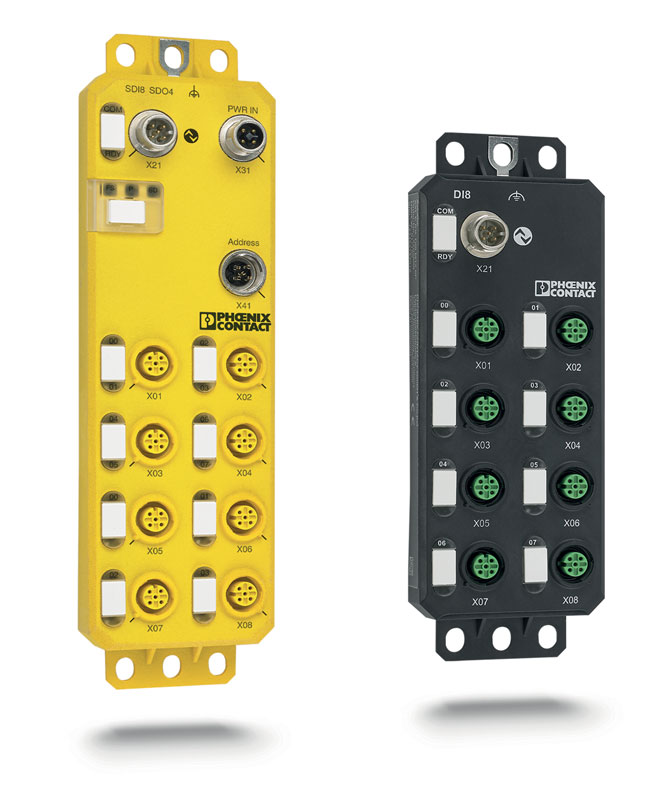
Implementazione indipendente dalla rete e dal controllore
Considerando il PLC della macchina come elemento centrale, una soluzione con un controllore sicuro offre un vantaggio decisivo: sul PLC è disponibile lo stato di tutti i moduli di ingresso e di uscita sicuri. Lo stesso vale per tutte le informazioni diagnostiche dei moduli sicuri. Se, ad esempio, si verifica un cortocircuito su un’uscita o una violazione dell’equivalenza su una coppia di ingressi, l’errore viene visualizzato all’operatore semplicemente tramite il controllore ed il sistema di visualizzazione associato e gli vengono suggerite misure per la sua risoluzione. Se queste non portano all’eliminazione del guasto, le informazioni sono accessibili anche tramite soluzioni di manutenzione remota. Il costruttore della macchina può quindi aiutare l’operatore a distanza, riducendo i tempi di fermo macchina ed aumentando la disponibilità dell’applicazione.
I vantaggi derivanti dalla combinazione di moduli I/O sicuri e controllori sicuri installati in modo decentralizzato sono quindi evidenti. Tuttavia, numerosi utenti devono affrontare la sfida che non tutti i produttori di controlli offrono un PLC di sicurezza, o del maggior costo per un controllore sicuro. Molti costruttori di macchinari sviluppano il proprio PLC, ma non hanno le competenze per implementare un controllore sicuro, costringendo i propri clienti, di conseguenza, ad utilizzare concetti obsoleti. Gli utenti devono quindi accettare gli svantaggi della soluzione classica oppure, ad esempio, utilizzare un bus separato per il trasferimento dei dati di sicurezza, che deve essere accoppiato al PLC standard. Ciò avviene tramite il cablaggio in parallelo agli ingressi standard o il collegamento tramite gateway bus. Entrambe le soluzioni si rivelano complesse e comportano costi aggiuntivi.
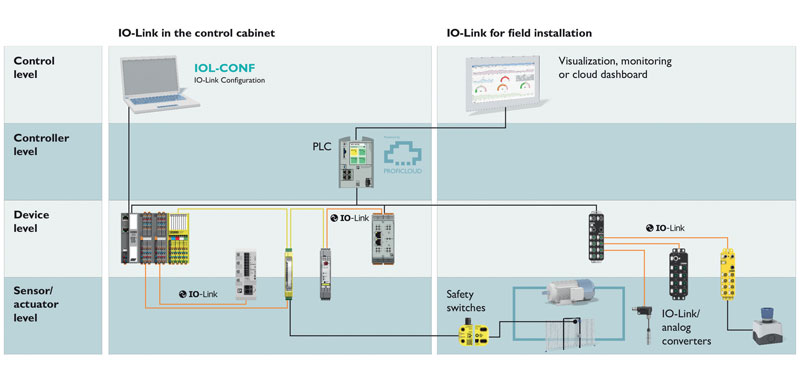
Diagnostica completa senza ulteriori aggravi
In questo contesto, il box I/O Axioline E Safe supporta il protocollo SafetyBridge. Un sistema SBT operativo è costituito da moduli di ingresso e di uscita sicuri e dai cosiddetti moduli logici. I moduli I/O acquisiscono i segnali di sicurezza o li emettono. Inoltre, essi eseguono costantemente la diagnostica controllando il dispositivo per verificare la presenza di cortocircuiti e allacciamenti incrociati nonché di violazioni antivalenti ed equivalenti, ad esempio. Il modulo logico rappresenta l’elemento centrale dell’installazione SafetyBridge, genera e controlla il protocollo di comunicazione SBT relativo alla sicurezza ed elabora i collegamenti logici della logica di sicurezza parametrizzata. Non è necessario un controllore sicuro.
I segnali di sicurezza ricevuti o emessi con i moduli I/O SafetyBridge possono essere inoltrati tramite quasi tutte le reti di automazione, come Profibus, Profinet, Ethernet/IP, Ethercat, Ethercat, CANopen, Sercos III o Modbus TCP, così come i comuni tipi di controllori. Come il box I/O Axioline E Safe, per l’accoppiamento del modulo SBT alla rispettiva rete, il modulo è dotato di interfaccia IO-Link per lo scambio di dati. L’integrazione nella rete utilizzata avviene tramite il rispettivo master IO-Link. Il controllore standard gestisce il trasporto dei dati tra i moduli. Il programmatore PLC ha accesso allo stato di tutti gli ingressi ed uscite sicuri. Senza necessità di ulteriori hardware, cablaggi o programmazioni, ha accesso alle informazioni su quale porta di sicurezza sia stata aperta o quale arresto di emergenza sia stato azionato. In combinazione con un sistema di visualizzazione, l’operatore riceve informazioni su come eliminare un eventuale guasto, riducendo notevolmente i tempi di fermo macchina causati dalla sicurezza funzionale. l
Nota sull’autore: l’ing. Lutz Rahlves è Product Manager Safety, Divisione Automation Infrastructure, Phoenix Contact.