State-of-the-art Motion Systems Speed up Commissioning
Festo electrical systems and digitisation help minimise commissioning time of a complex machine developed by Rem Automation. The automation inside the machine is for the most part controlled by Festo Motion systems; the entire series of new CMMT-AS and CMMT-ST drives are integrated into the machine.
Rem Automation deals with automation in various sectors including: automotive, electrical equipment, hydraulic pumps, gearboxes and car locks.
The collaboration with Festo, initially chosen as a supplier of pneumatic components and then extended to the electrical part, was established in 2007. It brought advantages both in terms of design and performance. “We decided to take advantage of Festo’s technologies because their solutions allow us to save time in the application, with optimal performance for what we use – says Massimo Marconcini, co-owner of Rem Automation -. There is no doubt about the quality of their products; moreover having a single supplier allows us to reduce the system commissioning time”.
The relationship of trust that has been established is underlined by the primary role of consultancy, which starts with the choice of solutions during the mechanical design phase. Marco Dottore, Application Sales Engineer – Electronic Light Assembly of Festo, followed Rem Automation in all phases of product selection, right up to the actuators: “It was a 360-degree service that began with the design – in September 2019 – and reached commissioning at the beginning of 2020”.
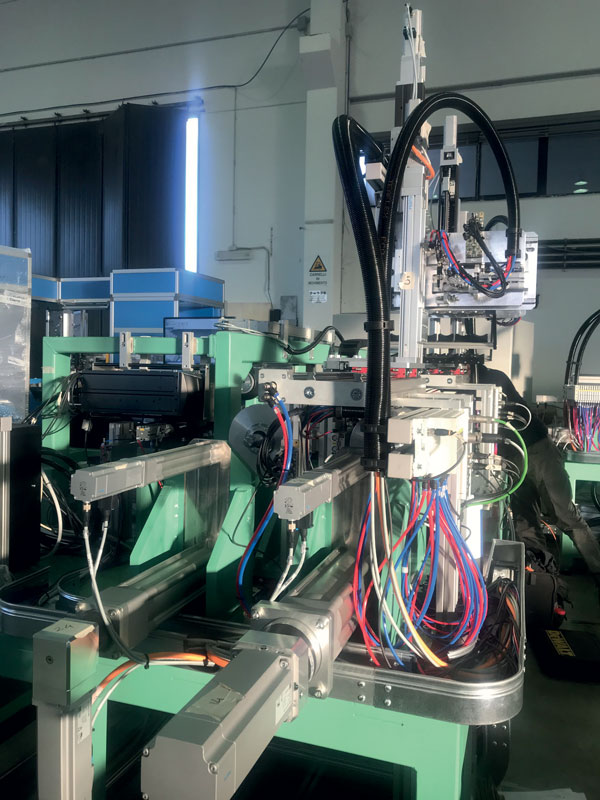
The result of the synergy with a foreign customer
Rem Automation’s market is purely Italian, even if they are entering foreign markets, although driven by Italian clients: “In this specific case we are working for a new customer, an Australian company operating in the mining sector – says Maroncini -. When we received the order there were no specifications, so we turned directly to Festo. At project level, the practical return was immediately recognised, especially in terms of commissioning, as all it takes is for the software to reintroduce the purchased codes and the system is configured”.
We are talking about a fairly complex machine which is capable of processing products of various sizes and shapes.
This is the reason why a technology that could adapt to different lengths and diameters was required. Rem Automation decided to opt for electrical systems in order to reduce the machine set-up times”.
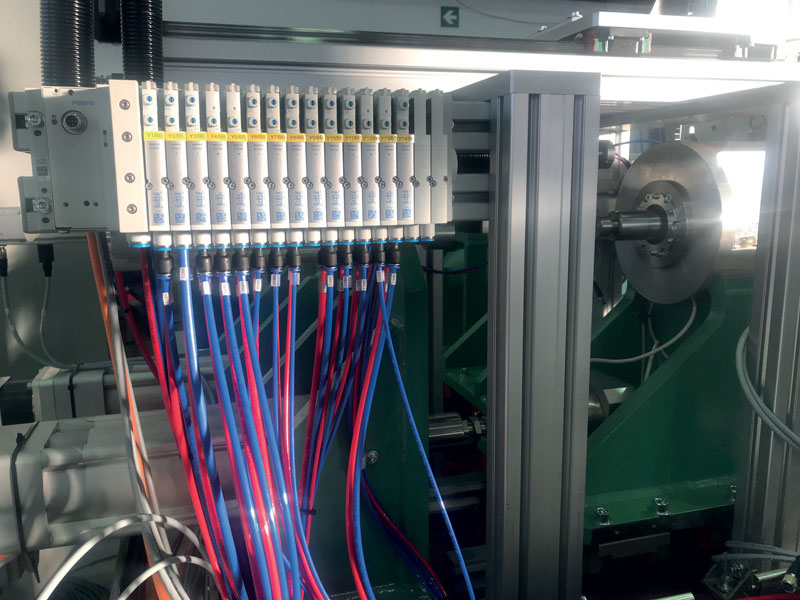
Electrical systems for the control of the automation inside the machine
The machine was also digitised from a Motion point of view. The automation inside the machine is for the most part controlled by electrical systems.
It was a great deal of co-engineering between Rem Automation, Festo and the client’s external designer. This led to the correct sizing of the axes, motors and Festo’s drives needed for the various applications. Everything happened without losing sight of the need to exploit products’ details suited to the technical and physical characteristics required for the machine, i.e. dimensions and performance. The entire series of new CMMT-AS and CMMT-ST drives are also integrated in the machine, with a considerable advantage in terms of commissioning thanks to the new Automation Suite configuration platform, which makes it possible to use Profidrive. The latter, in fact, standardizes PLC code, allowing the user to choose whether to use Sinapos or Technological Object for axis configuration. “We are also working on the integration of the CPX-AP-I module starting from the robotized island, and we hope to extend it to the rest of the line as well – says Marconcini referring to the island on which a central anthropomorphic robot operates by moving several pieces”. In addition to this there are two main special “twin” benches, in order to reduce working times and doubling production. On both benches, the first steps are carried out, planting, which, having to work over several lengths, involves format changes.
While in the following steps there is also a marking laser and a rotation test: “The island produces belt rollers for the mining sector, so it is essential to carry out the necessary tests – concludes Marconcini -; if one of these two rollers were to stop, it would create considerable damage. That’s why Festo’s Motion systems were chosen, to allow maximum flexibility and operational safety”.
More details 👇🏻