Successful Partnership for a Full-electric Loader
The successful Moog-Dolomitech partnership is at the heart of a full-electric industrial loader. Moog proposed a complete state-of-the-art system to the Trento-based company: each loader was equipped with 3 Electrohydrostatic Pump Units (EPUs), 4 servomotors and 7 DR2020 servo drives. These highly customized components proved to be the right solution to meet the application requirements in terms of efficiency, high performance and low energy consumption.
Born in the automotive sector, e-mobility is progressively establishing itself also in the world of industrial vehicles: a vast segment that includes numerous types of vehicles dedicated to excavation, handling and transport of materials and where, increasingly often, the traditional combustion offer is flanked by electrically powered vehicles. An example of this trend is the electric industrial loader, created with the collaboration of Moog, which has contributed to the creation of a full electric machine with characteristics compatible with use in warehouses and industrial areas.
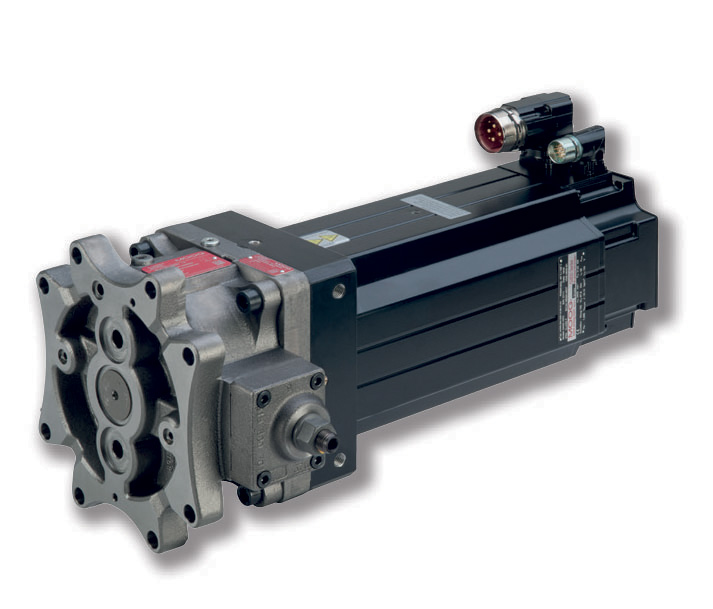
A complex project in terms of engineering and mechanics
The project, led by Dolomitech – an engineering company based in Trento and active in the research and development of propulsion systems for land, sea and air vehicles with high efficiency and low environmental impact – was complex from an engineering and mechanical point of view. The loader is, in fact, a “monster” machine in the category of industrial electric vehicles. Designed for short-range handling activities in steelmaking areas and plants, it weighs 50 tons, has a boom that reaches an extension of 18 meters and is able to lift 3 tons of material. These technical performances can be achieved only by choosing components that can effectively manage the mechanical, motion and electrical aspects.
In order to meet this challenge by adopting a full electric design, Dolomitech relied on Moog, which proposed a complete state-of-the-art system. In detail, each loader has been equipped with 3 Electrohydrostatic Pump Units (EPU), 4 servomotors and 7 DR2020 servo-drives. These components are highly customized and the project proved to be able to meet the application requirements in terms of efficiency, high performance and low energy consumption.
Battery power supply vs traditional power supply same performance
“The introduction of electric machines is increasingly considered as an investment with high added value, both in terms of environmental impact and operating costs. Limitations to the implementation of this technology, that were considered as impossible to overcome until a few years ago, are currently fading away. These solutions are becoming more and more popular, as they ensure reduced pollution, better working conditions and noise reduction” – explains Massimo Daziale, Key Account Manager at Moog Industrial. “Dolomitech was looking for a partner who could actively contribute to the success of the project – he continues -. Working in close contact with the client’s technical team, we developed an ad hoc system that stands out, for example, for motors with torque and speed performances perfectly aligned to the client’s requirements”.
The successful partnership with Dolomitech is a concrete demonstration of how Moog technology makes it possible to build
battery-powered machines with the same performance as traditional diesel-powered systems.
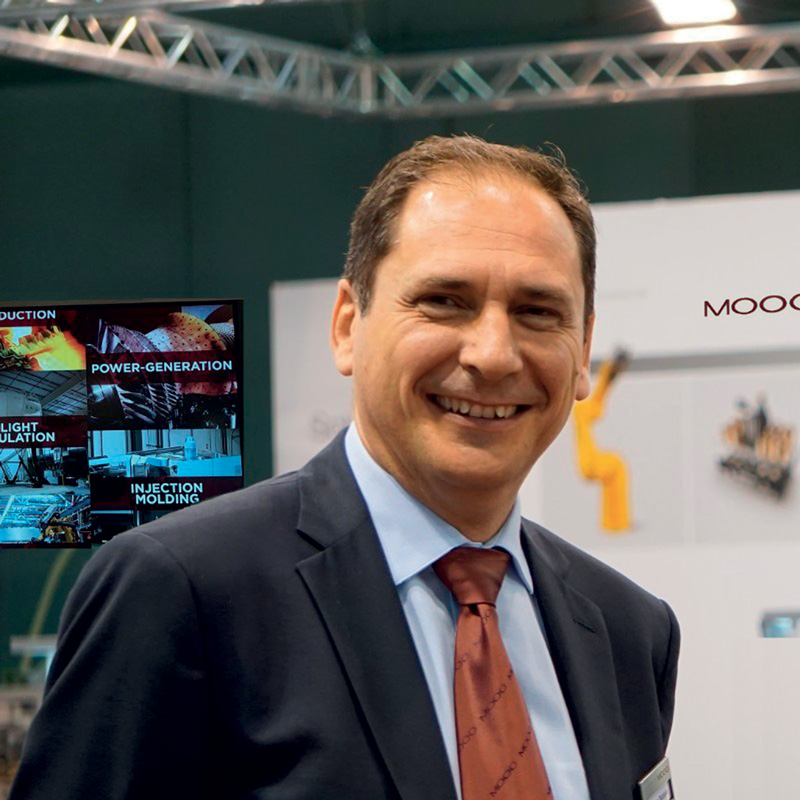
Hybrid/servodrives: the optimal combination technology
Finding the right balance of forces in an electric power system is crucial to increasing uptime. The combination of the EPU’s hybrid technology with customized energy-saving servo drives and servomotors, designed and engineered at Moog’s site in Casella, was able to meet the design requirements and to offer power and energy efficiency that contributed to functional autonomy and high load handling.
Moreover, Dolomitech particularly appreciated the ability of EPU to minimize the oil requirement, avoiding the need for dedicated tanks: this innovation, thanks to its oil-embedded characteristic, has now established itself as an enabling technology for increasingly eco-compatible and highly safe projects.