Successful Partnership for the Construction of the Test Bench
Moog and Agrati Group have merged their know-how to create an advanced dynamic test bench, with an integrated safety system. The shared design process allowed the application requirements to be satisfied in terms of safety and product customization.
The partnership between Moog and Agrati Group has led to the creation of a next-generation dynamic test bench. This is an advanced solution which includes an integrated safety system. Headquartered in the Monza and Brianza area, Agrati Group is a world-renowned name in the field of Fastener Solutions and complex fastening components for the European, North American and Chinese automotive markets. A technology partner capable of ensuring high levels of quality and service, thanks to the consolidated know-how developed during intense Co-Design activity with its customers. There are four Agrati Tech Centers created during the past few years to support the design and validation of its solutions.
The development of the new test bench stems from the need to have more information and data for the design of complex components and product development. With Moog Agrati Group shares principles focused on value innovation and maximum customization, realized synergistically with the order.
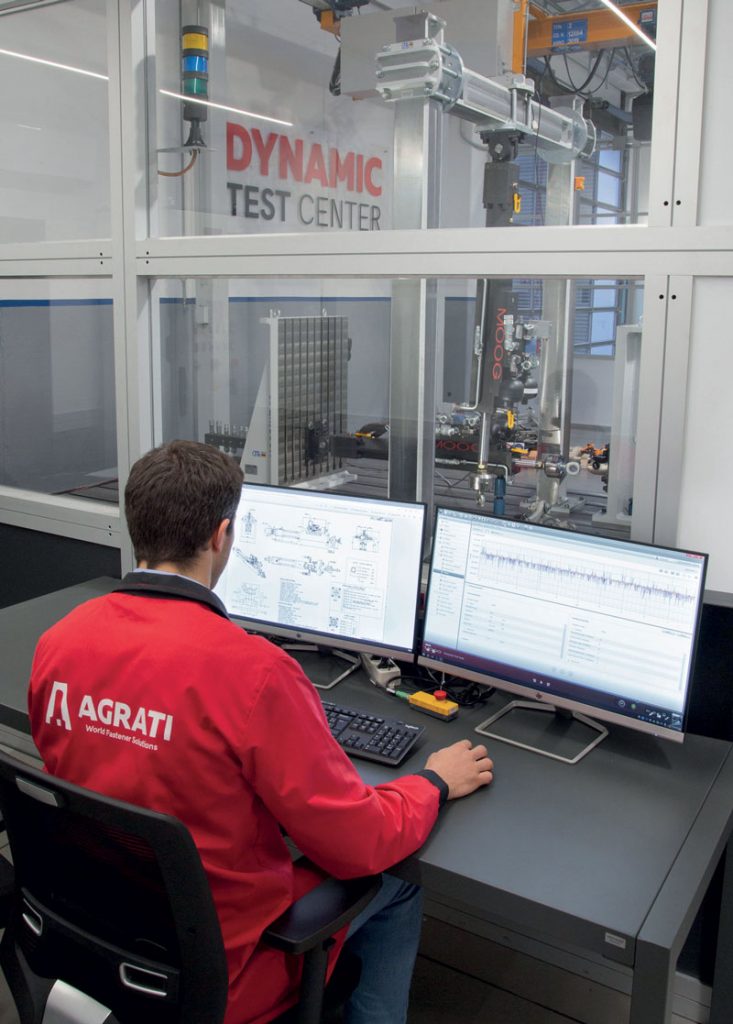
A shared design path focused on safety
The two companies have engaged in a shared design process, which began with the analysis of the design requirements immediately handled by Moog’s technical team. Two requirements in particular have been met with this ambitious project: first of all, meeting Agrati’s primary need to equip the bench with a safety system, whose parameters have been defined by the customer through an in-depth risk assessment.
To this end, the Moog team worked on the integration of a specific safety PLC into the test control system, using monitored valves to increase the reliability of the system and inserting hydraulic chokes to limit the maximum speed of movement of the actuator, with the aim of safeguarding the worker during both the set up and reconfiguration of the bench and the processing phases. Secondly, Moog has developed highly customised hydrodynamic actuators so that they could be perfectly compatible with Agrati’s proprietary mechanical interface. A crucial aspect which allowed to demonstrate, directly in the field, the ability to study customized components, able to ensure, with precision, the levels of force and speed required by the application. The supply is completed by a hydraulic power unit with an output of 100 l/min at 210 bar maximum pressure, a hydraulic power unit control panel, a safety management and control panel for the various work stages of set-up and testing, a two-channel controller and, consequently, two actuators.
Qualified technical support from design to testing
Throughout the entire process Moog has provided constant qualified technical support: from the design phase to the installation and testing of every single part of the subsystem. On its part, the Agrati Group appreciated Moog’s ability to work together, constantly adapting the solutions to the requirements arising during the process, in full respect of the shared time frames. All of this, in a climate of active dialogue which, through continuous fine-tuning, made it possible to overcome all the critical issues which emerged and to consolidate, over time, a relationship of great trust.