The new smart actuator helps reduce costs
Ewellix introduces the smart linear actuator CAHB-2xS with extended functionality for use in demanding applications such as agricultural and construction machinery. Thanks to its innovative features, this actuator helps to reduce development, material and maintenance costs.
Compared with earlier models, the smart actuator CAHB-2xS offers four new or enhanced features: in control, accurate position sensors, built-in monitoring/diagnostics and communication; typical MTTF of 75 years (calculated on 8 hours/day; 240 days/year). Patented non-contact sensors provide a true absolute position of movement that never require calibration, while motion is constantly monitored with the option to synchronise multiple actuators to offer parallel motion even at full speed. In addition, the CAHB-2xS monitors its own condition and can transmit an error code if it operates outside specifications. The actuators have a wide range of potential applications. These include agricultural equipment, construction machinery and materials handling equipment. They can also be used in work platforms and scissor lifts, and in electric vehicles such as utility task vehicles (UTV), road-sweepers and buses. One example is an autonomous mobile robot (AMR), which could use four actuators to lift heavy loads in a horizontal plane. Alternatively, a combine harvester might use dozens of actuators – connected to an electronic control unit (ECU) to ensure correct process control, information feedback, and onboard diagnostic function.
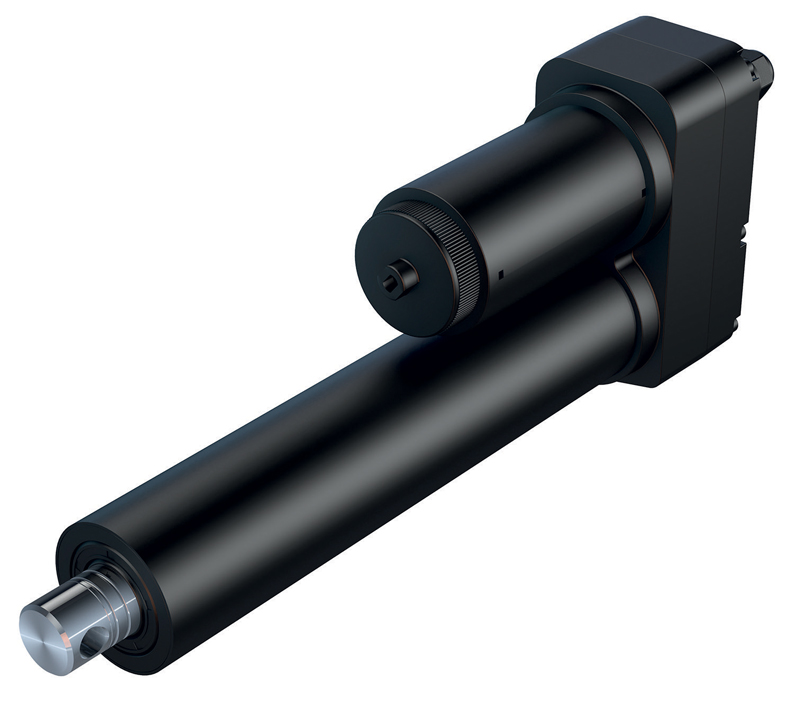
Thanks to the CAN bus device wiring is easier
Together, these new features deliver several customer benefits, including lower costs, faster time to market and higher productivity. In terms of cost saving, the actuator can be connected to a simple switch or a relatively inexpensive electronic control unit without the need for a high-current controller. When the equipment CAN bus is used, then the actuator wiring can also be simplified. In addition, multiple actuators with parallel motion can be controlled without the need for an extra electronic box or CAN bus on the equipment – further pushing down material and development costs. Machine developers can also design new products – or perform upgrades – more easily and quickly using the new actuator, with its plug and play functionality. For example, the firmware can be loaded to the actuator, allowing features such as the end stop to be adjusted from the equipment. Additionally, the CAN bus command allows users to specify an exact actuator position that is reached at a defined speed and with a maximum force, while the intelligent firmware eliminates the need for calibration or actuator testing.
With the SmartX platform loads in push and pull up to 10,000 N
End users find that the actuator’s smooth, powerful motion with soft stop/start – even when handling large loads – helps them work more productively. In addition, onboard diagnostics help identify any problems early, allowing them to be resolved before they become a serious concern. Minimising unscheduled shutdowns help reduce maintenance costs. The actuator does not require regular overhaul and maintenance, as would be needed in a hydraulic system. During development, the actuators passed the environmental test plan to satisfy OEM requirements when used in harsh mechanical, electrical and climatic conditions.
The new SmartX digital platform associated with the most powerful actuator of the CAHB-2xS series, the CAHB-22S – equipped with a ballscrew, is capable of delivering a push and pull load of up to 10,000 N. This arrangement offers high levels of efficiency, reducing energy consumption and making it ideal for applications such as battery-operated vehicles, where it can help to increase the range and reduce recharge times.