Macchine e automazione: alleati nella riaffilatura degli utensili
Schunk Präzisionswerkzeuge, realtà tedesca specializzata nella produzione di utensili, ha recentemente investito su un’affilatrice MX7 Linear (la seconda installata in azienda) e sul sistema RFID, entrambi sviluppati da ANCA. Obiettivo: ottimizzare le operazioni di riaffilatura automatizzata di lotti misti di utensili.
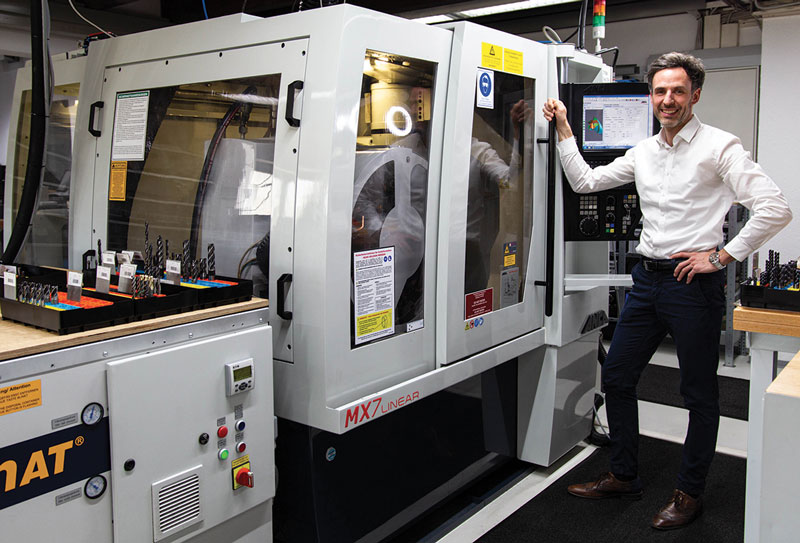
Schunk Präzisionswerkzeuge, fondata nel 1979 da Siegfried Schunk, inizia la propria attività in un garage di Coburgo, in Germania. Da fornitore di servizi di riaffilatura nel corso degli anni l’azienda è diventata fornitore di soluzioni, in grado di produrre la propria gamma di utensili da taglio di precisione oltre che utensili personalizzati per applicazioni speciali. Nata come ditta individuale, Schunk Präzisionswerkzeuge ha conosciuto un’evoluzione costante, e a oggi conta un organico di quindici dipendenti altamente qualificati. Nel 2010 l’amministratore delegato, Christian Schunk, decide di iniziare la produzione di utensili da taglio conquistando una fetta di mercato in continua crescita. Oggi il fatturato relativo ai nuovi utensili rappresenta circa il 60% del fatturato dell’azienda, con prodotti destinati a settori come l’industria automobilistica, aerospaziale, medica e degli stampi. Tutt’oggi Schunk continua ad offrire un servizio di riaffilatura professionale, che comprende la preparazione di bordi e il rivestimento presso la propria struttura dedicata, la Schunk Pro Finish (il servizio di rivestimento è stato introdotto da Christian Schunk nel 2009). Chi si rivolge a Schunk Präzisionswerkzeuge lo fa sia per l’acquisto di utensili sia per avere una gestione completa degli stessi, da ogni punto di vista: riaffilatura, preparazione dei bordi, trattamento superficiale.
Caricare lotti con utensili misti
Già nel 1998, Schunk Präzisionswerkzeuge ha indirizzato i propri investimenti in una rettificatrice a CNC a 5 assi, sviluppando un proprio sistema di caricamento “caotico” per lotti misti. A quell’epoca il fondatore Siegfried Schunk stava implementando, in modo non ordinato, un sistema di riaffilatura per lotti misti di clienti, utilizzando i robot Manutec Siemens su tre diverse rettificatrici. In Schunk, la rettifica con lotti misti di utensili è stata utilizzata con successo per oltre 20 anni. Oltre alla flessibilità garantita da un sistema di questo tipo, il suo impiego assicura una maggiore produttività perché in grado di eseguire la rettifica su un gruppo misto di utensili in assenza di personale. Questa mentalità di tipo “industriale” ha portato l’azienda a investire nel 2017 nella sua prima affilatrice MX7 di ANCA, azienda australiana con uffici dislocati in tutto il mondo e con una rete piuttosto estesa di rappresentanti e agenti (anche in Italia). Davvero ampio è il range di soluzioni offerto: si va dalle macchine utensili ai software fino all’automazione.
Gli utensili realizzati da Schunk Präzisionswerkzeuge sono destinati a diversi settori come l’industria automobilistica, aerospaziale, medica e degli stampi. Visto il successo riscosso con il primo modello MX7 Linear, Schunk Präzisionswerkzeuge ha investito in un secondo modello – un’altra MX7 – di ANCA.
Una coppia costante su tutta la gamma di giri
La gamma MX Linear è particolarmente adatta a soddisfare le esigenze di chi produce utensili alla ricerca della massima resa pur rimanendo flessibili in linea con le esigenze del cliente. La serie è dotata di motori lineari di nuova tecnologia che consentono di raggiungere livelli di precisione e prestazioni particolarmente elevati. MX7 Linear è un’affilatrice CNC potente e versatile progettata per la rettifica di produzione. Questo tipo di macchine è equipaggiato con un mandrino a magneti permanenti da 38 kW che fornisce una coppia elevata a un numero di giri inferiore, ideale per la rettifica di metallo duro e una vasta gamma di altre applicazioni. Il vantaggio principale di impiegare un mandrino a magneti permanenti è la sua capacità di fornire una coppia costante su tutta la gamma di giri. Tale mandrino presenta infatti una coppia maggiore a bassi regimi di rotazione, ideale per applicazioni come la rettifica del metallo duro. Tipico di un mandrino con motore a induzione, la potenza raggiungerà la sua coppia massima a un certo numero di giri. Ciò consente di mantenere costante la coppia per il resto della gamma di rotazione. La macchina ha un ingombro ridotto ma lo spazio di lavoro è particolarmente ampio. La corsa X è pari a 540 mm, Y 510 mm e Z 217 mm. I movimenti minimi degli assi durante le operazioni di rettifica riducono di fatto i tempi ciclo. Per quanto riguarda l’automazione, l’affilatrice MX7 Linear di ANCA può essere integrata con il sistema RoboMate, per la produzione di utensili ad alto volume o FastLoad-MX, per la produzione di volumi ridotti di utensili. Visto il successo riscosso con il primo modello MX7 Linear, Schunk Präzisionswerkzeuge ha investito in un secondo modello – un’altra MX7 – di ANCA espandendo al tempo stesso il flusso di lavoro RFID esistente. Per Christian Schunk infatti era importante mantenere la capacità di carico in maniera non ordinata e allo stesso tempo poter beneficiare di una maggiore precisione dovuta al cambio della pinza portapezzo.
Un flusso di lavoro digitale
Per dare una struttura ai lotti di utensili misti e con lavorazioni multiple, Christian Schunk ha sviluppato un proprio sistema di archiviazione che permette di ordinare tutti gli utensili di un ordine cliente su un pannello portautensili comune. Il pannello riporta un’etichetta e un codice a barre che contiene tutte le informazioni rilevanti sul lavoro da svolgere, come il tipo e il numero di utensili, la data di scadenza e altri dati di rilievo. Questo tipo di informazioni è utile inoltre per la raccolta degli utensili dopo che avviene la rettifica di ogni ordine. Schunk non ha solo implementato il flusso di lavoro RFID di ANCA per la riaffilatura non ordinata, ma utilizza anche i dati di produzione in una scheda di programmazione digitale che mostra lo stato di ciascuna lavorazione.
Visto il successo riscosso con il primo modello MX7 Linear, Schunk Präzisionswerkzeuge ha investito in un secondo modello – un’altra MX7 – di ANCA. La linea di affilatrici MX Linear di ANCA comprende i modelli MX5 e MX7.
Meno costi e più efficienza
Grazie alla tecnologia RFID di ANCA, Schunk Präzisionswerkzeuge è riuscita a ridurre i costi e ad aumentare l’efficienza operativa. Questo sistema consente inoltre di ordinare gli utensili come richiesto al tipo di produzione anziché secondo l’ordine cliente. Qualsiasi numero e combinazione di utensili di diversi clienti possono essere preparati per la riaffilatura in una stazione di programmazione dedicata. Ogni utensile viene valutato presso la postazione e operatori qualificati selezionano e modificano il programma di rettifica richiesto. Il singolo programma viene quindi codificato su un portautensile RFID e successivamente il portautensile e l’utensile stesso verranno posizionati in un pallet per la rettificatrice. A ogni portautensile RFID viene assegnato il nome cliente e il numero di lavorazione, così da rendere piuttosto semplice identificare l’ordine cliente originale dopo la rettifica.
Al termine della riaffilatura degli utensili, le informazioni RFID vengono lette e l’utensile viene restituito all’ordinativo originale del cliente. Il portautensili RFID ritorna in magazzino e può quindi essere utilizzato per un’altra commessa. In produzione, le informazioni RFID vengono scansionate e viene caricato il file di rettifica dell’utensile; tutti i parametri di rettifica, le modifiche richieste al pacco mola o le modifiche alle dimensioni della pinza portapezzo vengono eseguite automaticamente. Come ha spiegato Christian Schunk: “Ha senso ridurre al minimo i cambi delle pinze portapezzo, il che significa che gli utensili vengono solitamente ordinati per diametro e per tipo di utensile. In questo modo non solo si ottimizzano i tempi ciclo, ma si prolunga anche la durata delle pinze portapezzo, preservando al tempo stesso il portapinze. Ma, soprattutto, ciò permette di ottimizzare l’utilizzo delle scorte”. Christian Schunk si assicura anche che le macchine siano utilizzate al loro massimo. In quest’ottica, i dipendenti dell’azienda iniziano il giovedì a preparare gli utensili per la riaffilatura automatizzata senza personale che avviene durante il fine settimana. I pallet degli utensili vengono caricati per adattarsi ai processi di produzione ottimali; l’utilizzo di un sistema di carico non ordinato aumenta la produttività e riduce al minimo i tempi ciclo. Il caricamento non ordinato è una formula collaudata per l’efficienza. Se in precedenza Schunk ha lavorato per ordine cliente (caricando pertanto tutti i diametri di un cliente insieme), adesso l’azienda è passata a un sistema di caricamento completamente disordinato, indipendente quindi dall’ordine reale del cliente. Per l’utilizzazione della seconda MX7 ANCA, Schunk e ANCA hanno collaborato in modo da garantire un flusso di lavoro RFID ampliato in modo da poter ospitare un utensile con un diametro superiore, pari a 25 mm.
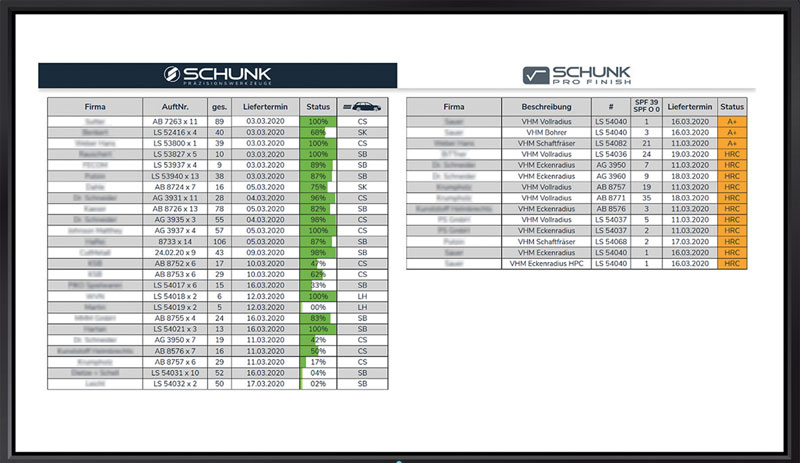
Diverse soluzioni per la riaffilatura
Per la riaffilatura di lotti misti di utensili, ANCA propone diverse soluzioni automatiche come spiega Andreas Sommer, Product Manager di Anca: “ANCA fornisce, ad esempio, un sistema di caricamento delle pinze portapezzo con pinze Nikken che consente all’utensile e alla pinza di essere cambiati insieme, come avviene ad esempio sulla macchina ANCA FX5 equipaggiata con il robot AR300. L’utilizzo del software Loadermate garantisce inoltre la riaffilatura non presidiata di un gruppo misto di utensili”. In alternativa, ANCA propone il cambio pinza portapezzo e il sistema RFID in presenza delle macchine MX. “Il software Dynamic Tool Group Manager di ANCA è al centro del flusso di lavoro RFID ed è in grado di raggruppare gli utensili in base alla tipologia, richiedere operazioni di riaffilatura e di avanzamento in base al fattore di usura o assegnare un singolo file utensile a un unico utensile.
Con RFID le informazioni richieste vengono registrate nella postazione di programmazione e l’utensile viene accoppiato al tag RFID. La macchina raccoglie l’utensile insieme al portautensile RFID, scansiona l’RFID e richiama automaticamente il programma di rettifica, imposta tutti i parametri di rettifica e carica il pacco mole corretto. Se è necessaria una modifica della pinza portapezzo, la macchina eseguirà tale operazione automaticamente. L’RFID viene collocato in una posizione di interscambio mentre l’utensile viene caricato e ricondizionato. La soluzione RFID di ANCA consente agli utenti di caricare in modo non ordinato gli utensili in un pallet caricatore, creando così un programma singolo per ogni utensile. La posizione dell’utensile all’interno del pallet può essere scambiata con un altro utensile in qualsiasi momento qualora fosse necessario riaffilare un utensile con urgenza. La rettificatrice e l’utensile possono eseguire l’operazione di riaffilatura singolarmente e senza operatore (la durata dell’utilizzo non presidiato della macchina dipende dal tipo di caricatore e dalla capacità dei pallet)”.